Quality, health at work
.webp)
- 1- Implement your quality of life approach at work
- 2- Dealing with the risk of employee burnout
- 3- Ergonomics for non-specialists
- 4- Stress and health at work: finding your balance
- 5- Facilitator, Health-Safety-Environment Prevention Officer
- 6- Lead minute meetings or Quick Meetings
- 7- Driving Quality on a daily basis
- 8- Ensuring the security of your establishment
- 9- QSSE* auditor: knowing how to observe and analyze
- 10- CHSCT of SEVESO establishments
- 11- Quality Correspondent / Facilitator
- 12- Complete training for the Quality Manager
- 13- Practical training in FMEA* product and process
- 14- Practical training on the cause tree
- 15- Practical training for Quality controllers
- 16- Crisis management
- 17- Practical guide to the ISO 14001 version 2015 standard
- 18- Practical guide to ISO 45001
- 19- Practical guide to ISO 9001 - Special industry
- 20- Practical guide to ISO 9001 - Special services
- 21- ISO 9001 V2015: managing risks and opportunities
- 22- Quality at the service of the customer experience
- 23- The quality assistant
- 24- The prevention plan
- 25- The Quality dashboard
- 26- Human and Organizational Factors (HOF) in QSSE
- 27- Health and safety risk assessment and the single document
- 28- Manage by processes
- 29- Measure your customer satisfaction, exploit their complaints
- 30- Measure your non-quality costs
- 31- Advanced statistical methods
- 32- MSP/SPC (Statistical Process Control): aiming for six sigma
- 33- Process driver
- 34- Perform system and/or process quality audit
- 35- Sustainably reduce its environmental impacts
- 36- Environmental regulations - Level 1
- 37- Environmental regulations - Level 2
- 38- Solve problems in the field
- 39- Responsible for continuous improvement
- 40- Environment Manager
- 41- Responsable QSSE
- 42- Quality Manager
- 43- Quality Manager: 4 attitudes for success
- 44- Purchasing Quality Manager
- 45- Health and Safety Manager
- 46- Monitor and improve the quality of your suppliers and subcontractors
- 47- ISO 20000, Foundation, certification (understanding the Service Management System)
- 48- ISO 20000 Lead Auditor ''Service Management System''
- 49- CGEIT®, IT governance, preparation for Certified in the Governance of Enterprise IT certification
- 50- Lean Six Sigma®, Green Belt, certification
- 51-
- 52- CRISC®, IS risk management, preparation for certification (Certified in Risk and Information Systems Control)
- 53- M_o_R®, Risk Management, Practitioner, certification
- 54- Generation Y: good managerial practices
- 55- Integrate and manage generation Z how to bet on the new generation
- 56- CSR communication: enhancing the image of your company responsibility for the message, support and dissemination
- 57- Managing through quality processes
- 58- ISO 9001, quality, Foundation, certification
- 59- ISO 9001 Lead Implementer, ''QUALITY MANAGEMENT''
- 60- Build and manage an integrated QSE system
- 61- Managing good communication practices in the health and medico-social sector
- 62- HACCP method in health establishments food hygiene
- 63- Quality and safety of care preparation for V 2014 certification
- 64- Improving hygiene in health establishments risk prevention
- 65- ISO 13485 Lead Auditor "Quality management - Medical devices"
- 66- ISO/IEC 17025 Lead Implementer "Quality Management – Laboratory Management System"
- 67- ISO 45001 Foundation “Health and safety at work”
- 68- ISO 45001 Lead Auditor "Health and safety at work"
- 69- ISO 45001 Transition “Health and safety at work”
- 70- ISO 45001 Lead Implementer “Health and safety at work”
- 71-
- 72- ISO 13485 Lead Implementer "Quality management - Medical devices"
- 73-
- 74- ISO/IEC 17025 Lead Assessor "Quality Management – Laboratory Management System"
- 75- fire safety in business
- 76- Concepts of risk management and site security
- 77- ISO 55001 Lead Implementer
- 78- Electrical authorization
- 79- Work at Height
- 80- Electrical safety
- 81- Lean Six Sigma®, Black Belt, certification
- 82- Lean Six Sigma®, Yellow Belt, certification
- 83- First aid training
- 84-
- 85-
- 86-
- 87- Safety and Risk Management
- 88- Fire Prevention and Firefighting
- 89- QHSE / ISPS Standards
- 90-
- 91- Risk Analysis – FMEA Method
Implement your quality of life approach at work
★★★★★
- QST-1
- 2 Days (14 Hours)
Description
Living conditions at work are an issue for companies and employees. Companies can make quality of life at work an element of enhancing their employer brand and their attractiveness. For employees, feeling good in their professional environment appears to be a motivating factor, and the deterioration of living conditions at work, a reason for dissatisfaction. The ANI on the policy for improving the quality of life at work indicates areas for reflection, the objective of this training is to enable you to translate them into concrete actions.
Who is this training for ?
For whom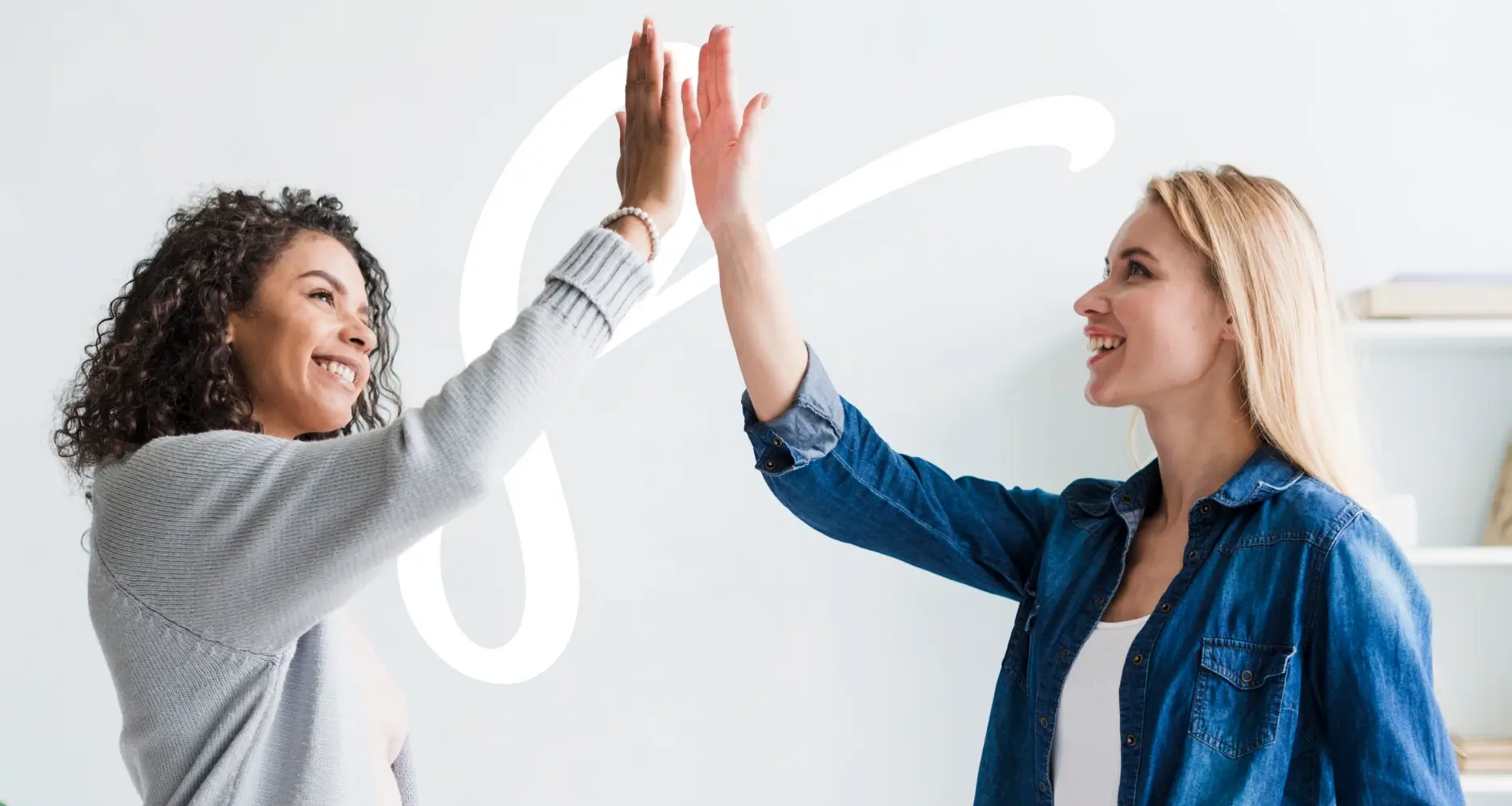
None.
Training objectives
Develop and implement a Quality of life at work approach in harmony with its corporate culture.
Follow the action plan and measure its effects.
Know the CE/CSE's room for maneuver in the event of a change in the economic situation of the company.
9Training program
Define the elements of your quality of life at work project
- Take into account the issues: sociological perspective; impacts on the company's image and HR policy; induced economic effects.
- Select the elements of your QVT policy: conditions work; employee services; arrangement of work spaces.
Implement your quality of life at work charter
- Define the key points: layout of work spaces; work-life balance; organization of working times and arrangements.
- Constitute the steering committee: HR, managers, members of the staff representative institutions, occupational health stakeholders.
Bringing the QVT approach to life
- Define the action plan: organize actions over time; select internal and external stakeholders; encourage employee expression on the project; monitor impacts on an organizational, relational and economic level.
Integrate the QVT approach into a global approach
- Impacts on managerial practices and manager involvement.
- Harmonization with agreements on professional equality and health issues at work.
Dealing with the risk of employee burnout
★★★★★
- QST-2
- 2 Days (14 Hours)
Description
In new work contexts: reorganizations, restructuring, uncertainties, management solely through processes, work in a company can be exhausting, or even make you sick. This is why it is important to detect the symptoms of burnout and analyze the causes in order to act without delay. Support for the employee is essential, this is the objective of this training.
Who is this training for ?
For whom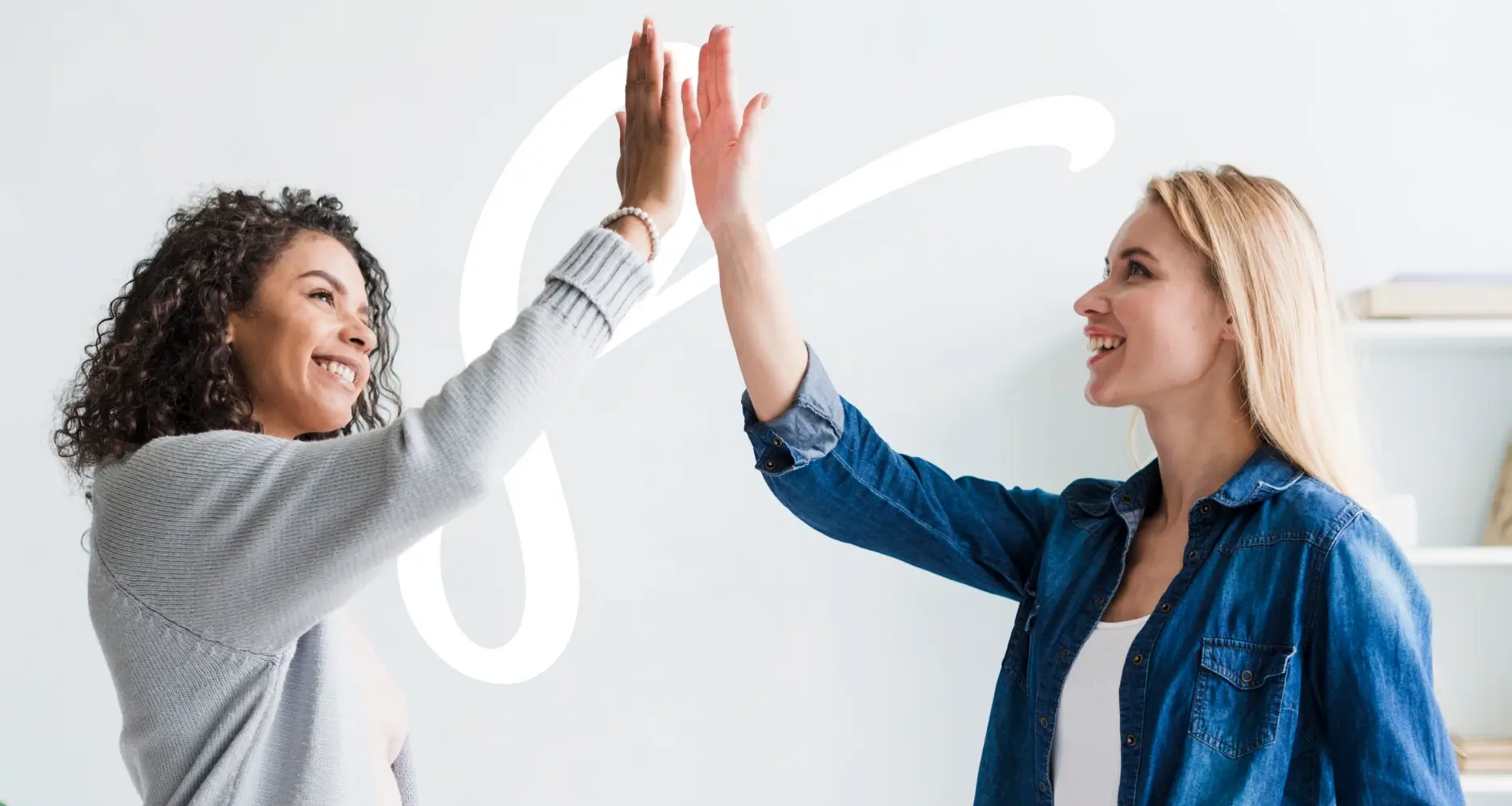
None.
Training objectives
Understand the triggers for burn-out.
Detect symptoms and identify changes in behavior.
Support employees who are suffering.
Define prevention and action plans.
12Training program
Take into account the complexity of burnout factors
- Manifestations of professional burnout syndrome: the link between burn-out and other professional risk factors; professional contexts which induce burn-out risks.
- Populations sensitive: professional history, age category, socio-professional categories...
Identifying the manifestations of professional burnout
- Identify the first signs to act preventively.
- Evaluate an employee's stress factors at work.
- Detect the stages and manifestations of a risk of burn out.
- Measure the impacts on the employee's physical and psychological health.
Supporting employees suffering at work
- Measure the level of burn-out of the employees concerned.
- Set up support by setting the framework: confidentiality, duty to alert, need for support.
- Create discussion and steering groups on the subject.
- Call in external professionals (psychologists).
- Alert institutional actors: HR, occupational physicians, services social.
13Define prevention and action plans
- Consequences of burnout: costs and the employer's obligation to perform.
- Identify all the indicators and measure their severity.
- Conduct an employee interview support.
- Inform to facilitate prevention.
- Making managers aware of their role in dealing with suffering at work.
- Dealing with risky situations.
- Build a prevention plan.
Ergonomics for non-specialists
★★★★★
- QST-3
- 2 Days (14 Hours)
Description
Ergonomics is an approach that makes it possible to develop working conditions conducive to the well-being and quality of life at work of employees. This training allows you to discover the fundamentals of ergonomics to improve productivity and well-being at all workstations.
Who is this training for ?
For whom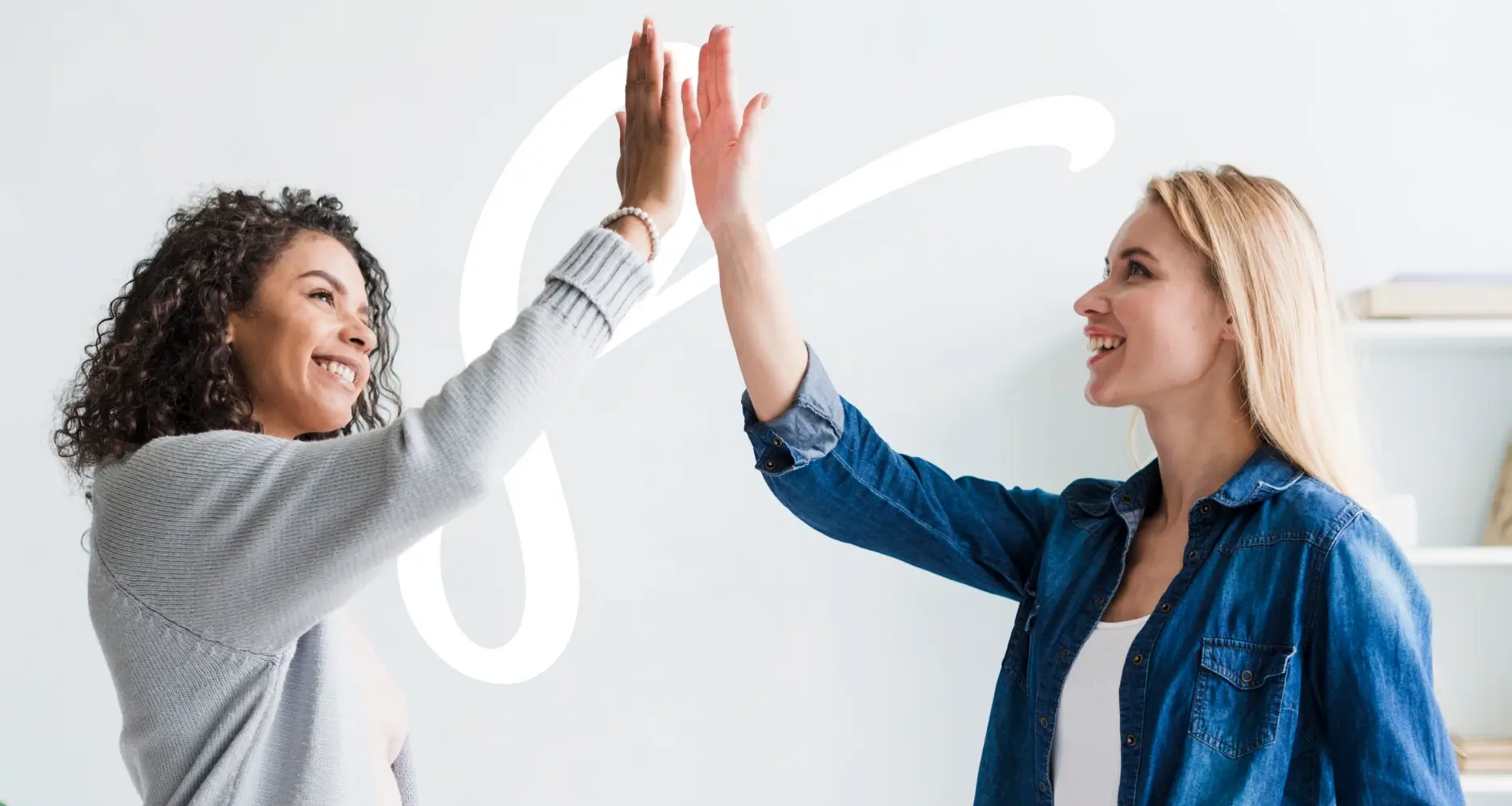
None.
Training objectives
Learn the basic notions of ergonomics.
Identify the contribution of ergonomics to work.
Integrate the notions of pace and mental load.
Improve the layout of work spaces.
16Training program
Master the basic notions of ergonomics
- Improving the workstation: why, how? interest of ergonomics for efficiency and productivity at work; legal obligations; involving competent stakeholders in the analysis and design of workstations .
- Fundamental knowledge of ergonomics: postures, frequencies, efforts, risks of Musculoskeletal Disorders.
Work on the layout of workspaces
- Prolonged sitting or standing positions.
- Computer workstations: seated posture, computer screen, keyboard.
- The layout of offices and meeting rooms meeting.
- Orientation in relation to lighting points: case of open space offices.
Practice the ergonomic analysis of a workstation
- The particular case of seated workstations.
- The specificity linked to standing workstations.
- Analyze a situation, a workstation and propose improvements .
- Be attentive to the physical layout: furniture, work accessories.
Moving from ergonomics to developing well-being at work
- Measure and act on mental workload.
- Anticipate mental workload factors: measurement tool.
- Integrate the impact of work rhythms.
- Carry out an ergonomic diagnosis.
- Involve all stakeholders: HR, CHSCT/CSSCT occupational physicians.
Stress and health at work: finding your balance
★★★★★
- QST-4
- 2 Days (14 Hours)
Description
The notion of well-being at work covers multidimensional aspects. Depending on your work environment, the culture and managerial methods of your organization and your own expectations, the criteria are different. In this 'Stress and Health at Work' training, we offer you an individualized approach which will allow you to identify your own stress signals, which can lead to communication difficulties. You will thus be able to act in anticipation independently.
Who is this training for ?
For whom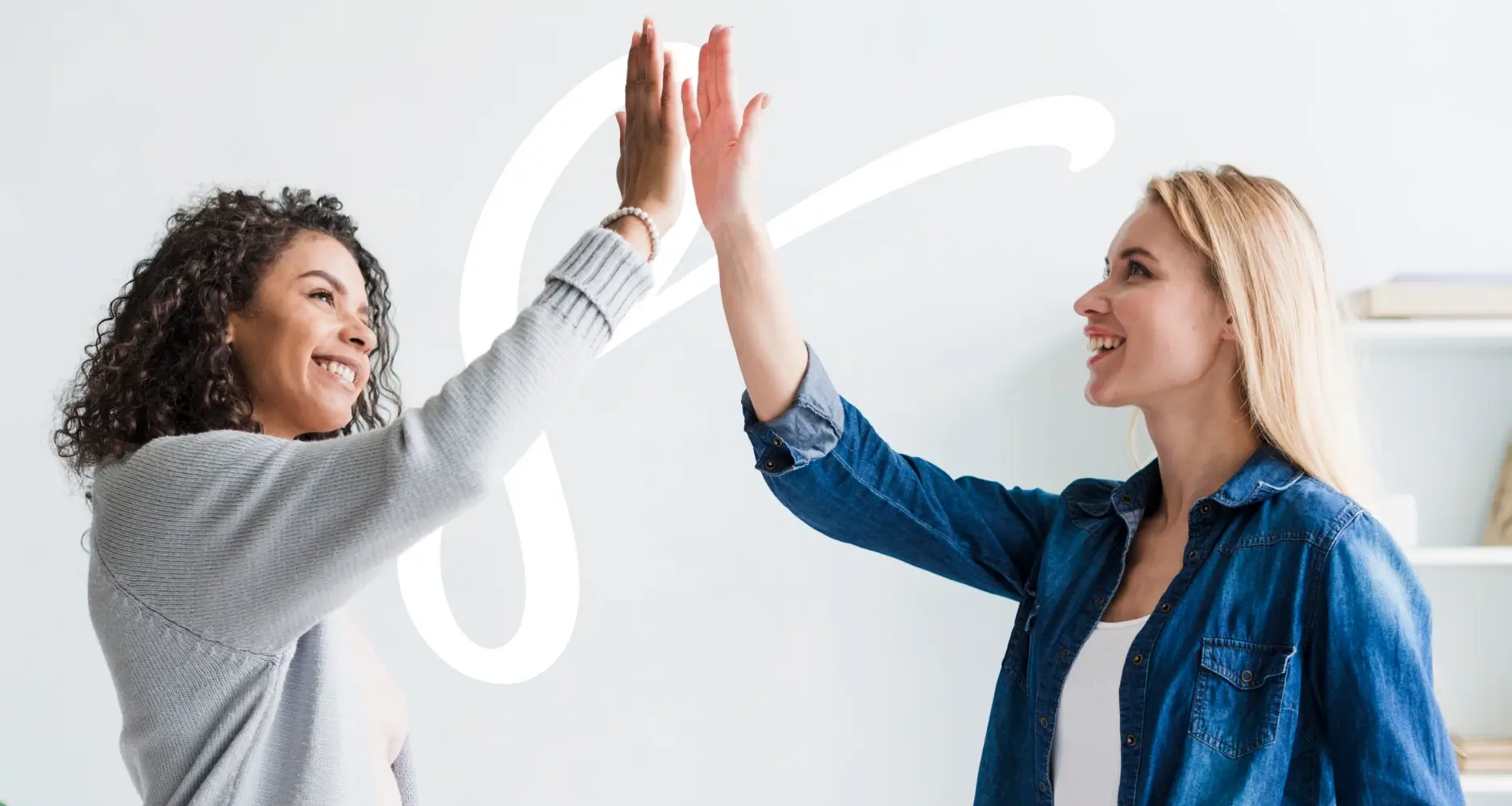
None.
Training objectives
Understand the mechanisms of stress that can affect your health at work.
Take action on stress factors using appropriate techniques.
19Training program
Preserve your health capital in your professional environment
- Identify your stress factors: work rhythms, objective levels, loss of connections; multiplicity of demands; changing and uncertain environments.
- Become aware of risk factors: life balance professional and personal life; mental load; impact on self-confidence; difficulties in asserting oneself and expressing one's feelings.
Identify stress warning signs
- Physiological signals: impacts on sleep, health.
- Signals linked to hyper adaptability: feeling of permanent vigilance, incompetence.
Observe the impact of different signals on yourself
- Understand the mechanisms of stress and identify them for yourself: relational difficulties; sudden changes in mood; repetitive feelings of fatigue; musculoskeletal disorders; difficulty relaxing.
Implement an action plan to act as quickly as possible
- Accept the diagnosis of professional overwork.
- Act on your personal stressors: health support: sleep, nutrition, relaxation, breathing; coaching type support.
- Act to communicate with management and explain their difficulties.
Facilitator, Health-Safety-Environment Prevention Officer
★★★★★
- QST-5
- 3 Days (21 Hours)
Description
The role of the facilitators, Health/Safety-Environment (SSE) relays, is decisive. Relays between those responsible for the HSE function and operational staff, they bring the approach to life in their activity on a daily basis. This training provides them with the skills necessary to fully carry out their mission.
Who is this training for ?
For whom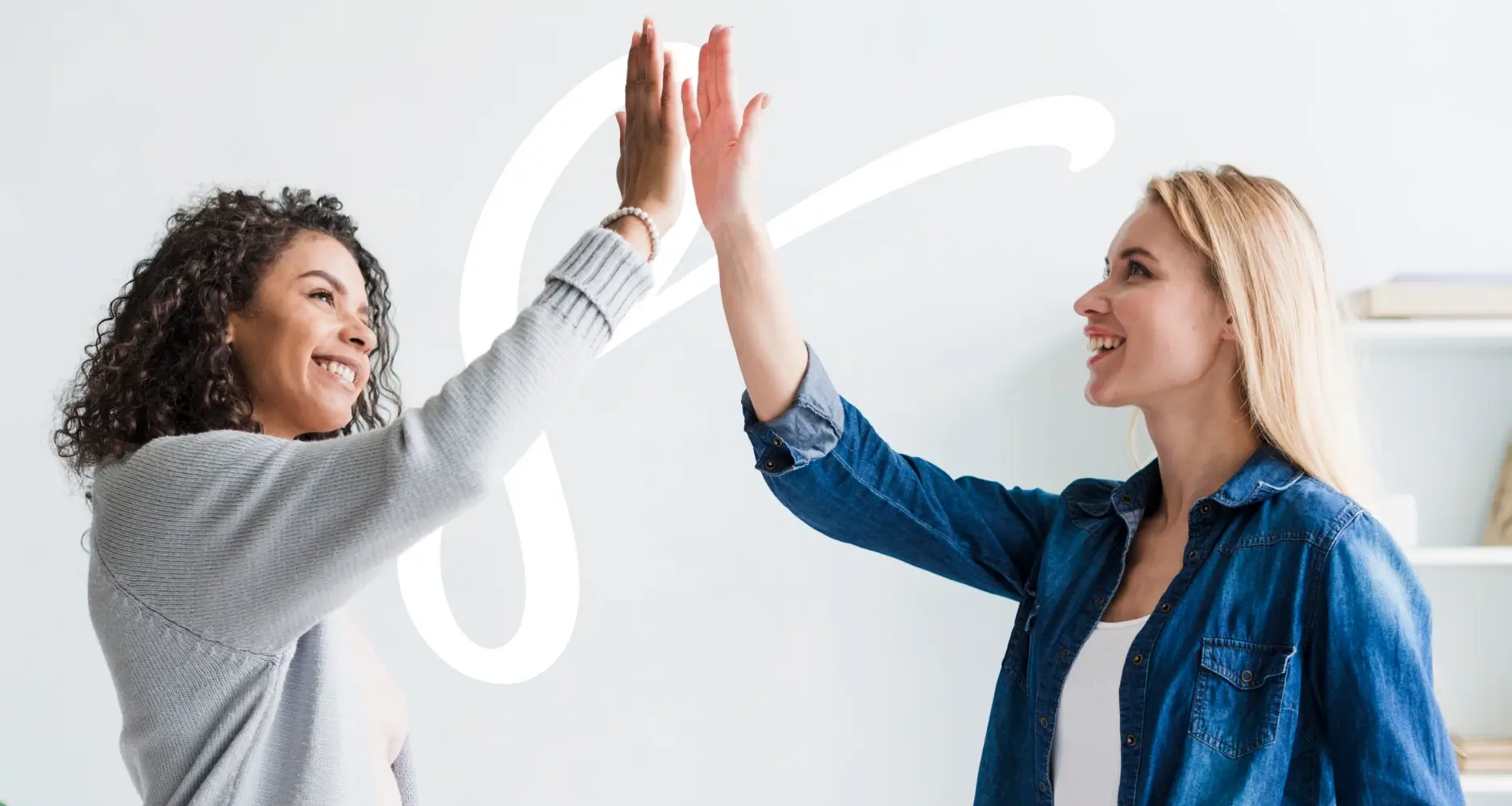
None.
Training objectives
Acquire the methods and tools to be an effective relay within the company as part of its Environment and Safety approach
22Training program
Understanding the challenges of HSE systems
- Objectives of Health, Safety, Environment (HSE) management systems.
- Key points of HSE regulations.
- Summary presentation of the ISO 14001 and 45001 standards.
- Logic of the PDCA.
- Missions of an SSE facilitator.
Identify the risks to control
- The principle of HSE risk analysis, the notions of prevention and protection.
- The implementation of preventive actions (operational control actions).
- Monitoring actions on the ground.
- Managing emergency situations.
Engage in continuous improvement (PDCA)
- Carry out assessments, lead field meetings.
- The HSE action plan: implementation and monitoring.
- Updating documents.
- Following a deviation, what corrective actions should be taken? Address the root causes.
- Job audits to make progress.
Measure, communicate HSE results
- The SSE indicators to follow.
- Turn your dashboard into the PDCA application tool.
- The communication plan.
23Measure, communicate HSE results
- The SSE indicators to follow.
- Make your dashboard the PDCA application tool.
- The communication plan.
Make everyone an actor
- Clarify everyone's responsibilities.
- Take action and prevention.
Remote activities
- An
- expert "Leading the HSE (health, safety, environment) approach on a daily basis" and a video "Tutorial: HSE audits".
Lead minute meetings or Quick Meetings
★★★★★
- QST-6
- 1 Days (7 Hours)
Description
Minute meetings (5 minutes flat!) help drive the continuous improvement process in the field. Our training gives you the keys to effectively prepare and lead these meetings. Active teaching based on simulations ensures the success of this day.
Who is this training for ?
For whom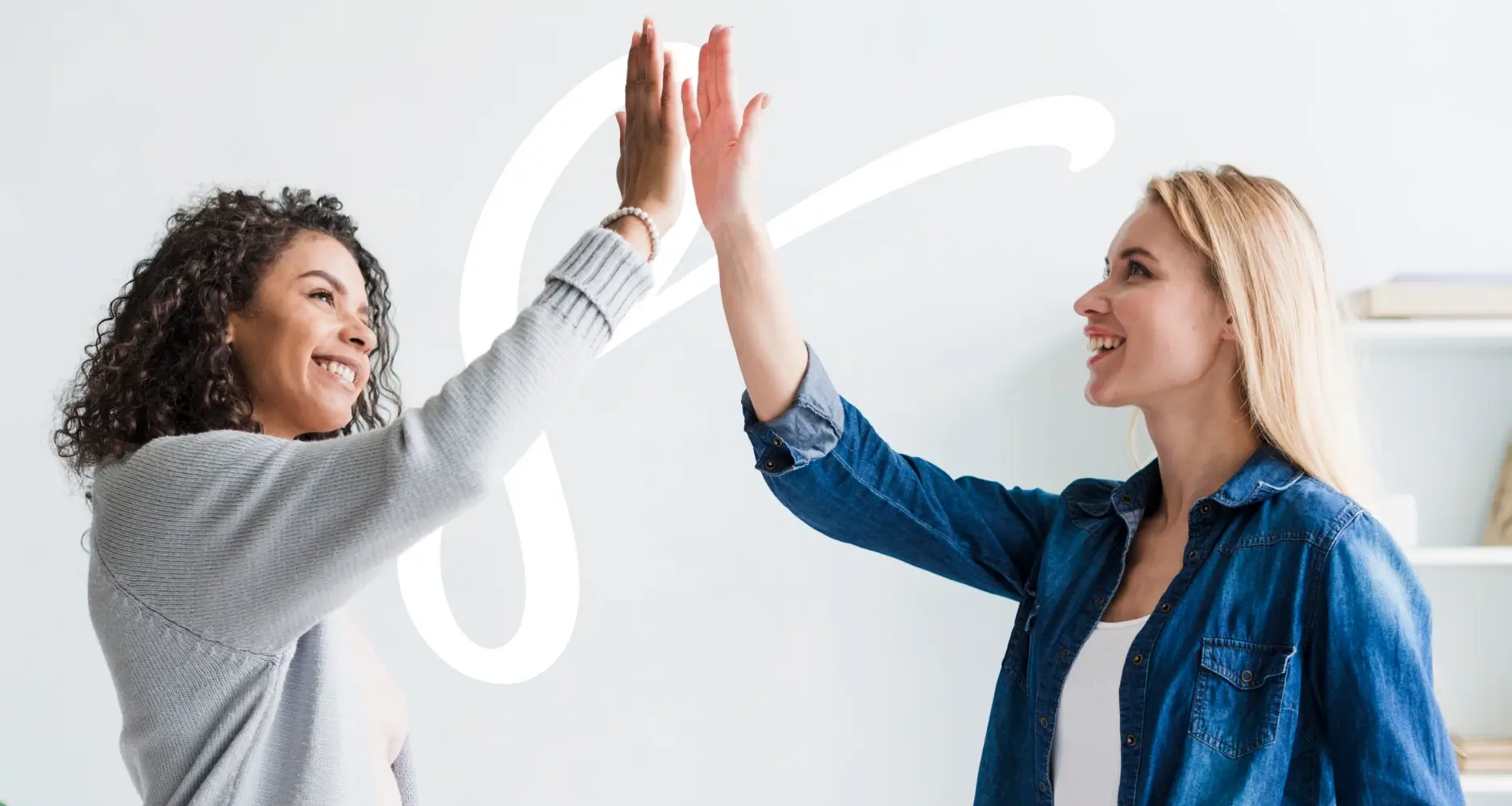
None.
Training objectives
Acquire the principles of preparing and leading minute meetings in the field
26Training program
Understand the characteristics of minute or 5 minute meetings
- Identify the issues of each minute meeting: information, problem resolution stage, communication, data collection, etc.
- Establish a precise and realistic objective: the ideal place to be in action; the material necessary to facilitate in the field.
- Understand the causes of meeting failures and exploit them.
Prepare the meeting to ensure its success
- Choose your participants, inform them in advance of the subject and their role.
- Structure the progress of the brief: identify the key stages; formalize the progress in a simple but structured way; check the timing.
- Rely on the right animation tools, including digital tools.
- Organize a hot and cold assessment.
Succeed in your animation: practice
- Acquire the techniques to quickly transmit information and encourage participation.
- Know how to apply the principles of animation to produce and regulate information in the context of quick meetings.
- Simulate: prepare an intervention based on a case study or professional context.
- Identify your strengths and areas for improvement.
Driving Quality on a daily basis
★★★★★
- QST-81
- 2 Days (14 Hours)
Description
Well beyond quality methods and tools, our surveys carried out with Quality managers show that one of the most important difficulties of a Quality approach remains the daily adherence of everyone, the animation of quality in the field... It therefore seemed essential to us to provide Quality project managers with a practical response to this particular dimension of their profession during this training.
Who is this training for ?
For whomQuality Manager, correspondent, Quality facilitator. Anyone who has to manage and implement a Quality approach.
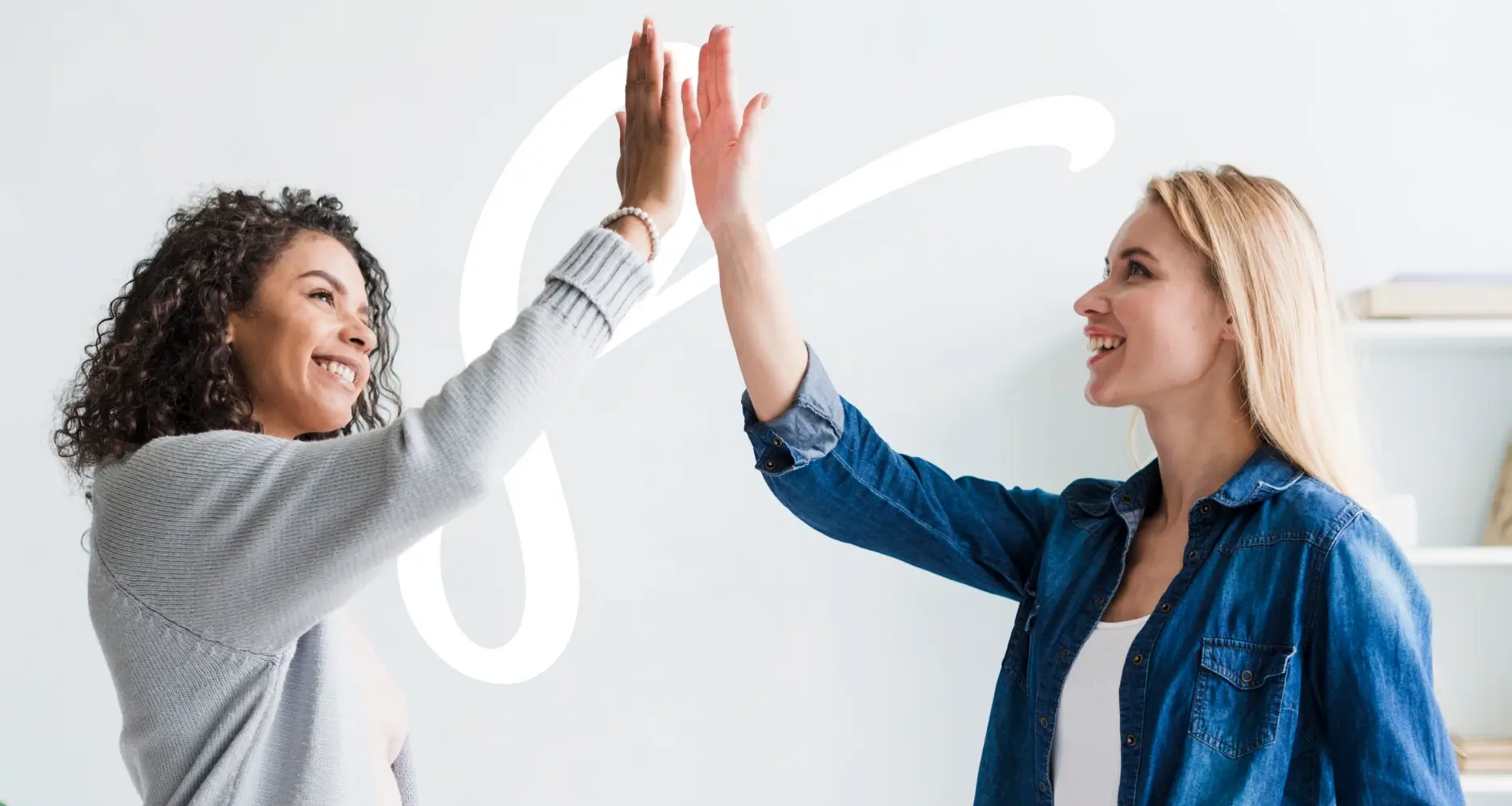
- Basic quality knowledge must be known.
Training objectives
Animate your Quality project and maintain enthusiasm on a daily basis.
Mobilize everyone to the challenges of a Quality approach.
29Training program
Carry out an inventory of the Quality dynamics of your company (sequence 1)
- Self-diagnosis of your practices.
- Establish the typology of actors.
- Give meaning to the word 'Quality' in your company.
“Sell” Quality internally (sequence 2)
- Above all, seek agreement on the issues.
- Prepare your argument according to the interlocutor.
- Assert yourself without aggression, feel legitimate.
Communicate effectively (sequence 3)
- Improve the display, Create a Quality
- Your communication plan to be defined: who communicates what, to whom, how often and how?
Organize Quality events (sequence 4)
- Avoid routine, 'pre-audit' wake-ups by bringing quality to life on a daily basis, solving problems on the ground in quick meetings.
- Organize games to interest and promote skills.
- Imagine 'a day of quality' to mobilize, generate surprise and interest.
- Use digital tools: videos, interactive quizzes, etc. .
Create an awareness module (sequence 5)
- Design quality awareness workshops: what messages? audience? how?
- Use the game as an educational tool.
Build your animation plan (individual sequence)
- Choose from the tools presented those that are best suited to the current context of your company.
- Initiate your quality animation plan.
Ensuring the security of your establishment
★★★★★
- QST-8
- 2 Days (14 Hours)
Description
Malicious acts which lead to damage to material goods, people and intellectual property are today a real risk for many companies and organizations. Taking this vulnerability into account leads them to initiate a real security policy. This new training allows you to identify your key risks and possible operational solutions to deal with potential malicious acts.
Who is this training for ?
For whom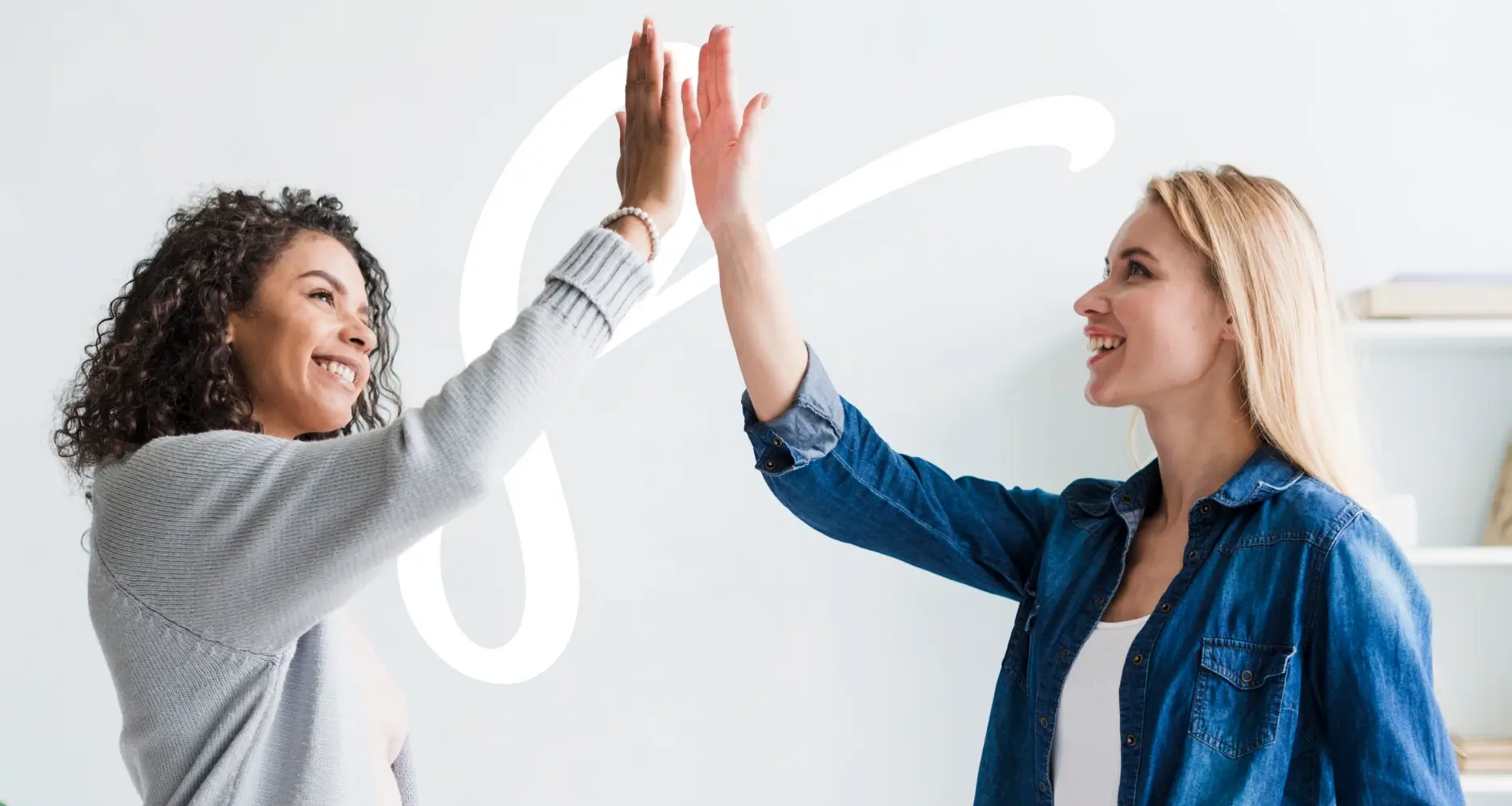
None
Training objectives
Know how to assess your vulnerabilities and define your priorities in terms of establishment security.
Establish a security and organizational inventory based on the threats that may weigh on your site.
Identify the most suitable means of protection.
32Training program
Identify and assess the risks of malicious intent for your establishment
- Identify the risks taking into account your context: Theft, damage to equipment.
- Economic and industrial espionage.
- Possible aggression against people reception and other collaborators.
- Hacking of the information system.
- Economic fraud.
- Knowing how to detect them in the field.
- Know how to prioritize risks: assess their severity and probability of occurrence taking into account your activity and the specificities of your environment.
- Scenario Specific case of an ERP (establishment open to the public) / Self-diagnosis.
Implement actions to respond to identified security needs. Rely on key players internally and, if necessary, specialized companies.
- Reasoning elimination / reduction of risk, protection system but also transfer of responsibilities.
- Technical solutions to protect against intrusions.
- Job creation security, security service, rounds...
- Identify your rules regarding internal and external communication.
- Know how to manage visitors, fixed-term contracts, interns, external companies.
- Establish internal procedures.
- Take regulations into account: obligations regarding employee health and safety and security of establishments.
- Criminal law, responsibilities associated.
33Evaluate your safety system Know how to test the system: internal audits, unannounced checks.
- Emergency situation scenario testing and feedback.
- Engage in a process of continuous improvement using key indicators.
QSSE* auditor: knowing how to observe and analyze
★★★★★
- QST-9
- 2 Days (14 Hours)
Description
To measure the conformity of the QSSE management system with the chosen standards and evaluate its effectiveness, the QSSE audit is extremely relevant. This training focuses on the specificities of QSSE audits, the key points to verify in the field. Through photos, the trainees are in an audit situation from the first day!
Who is this training for ?
For whom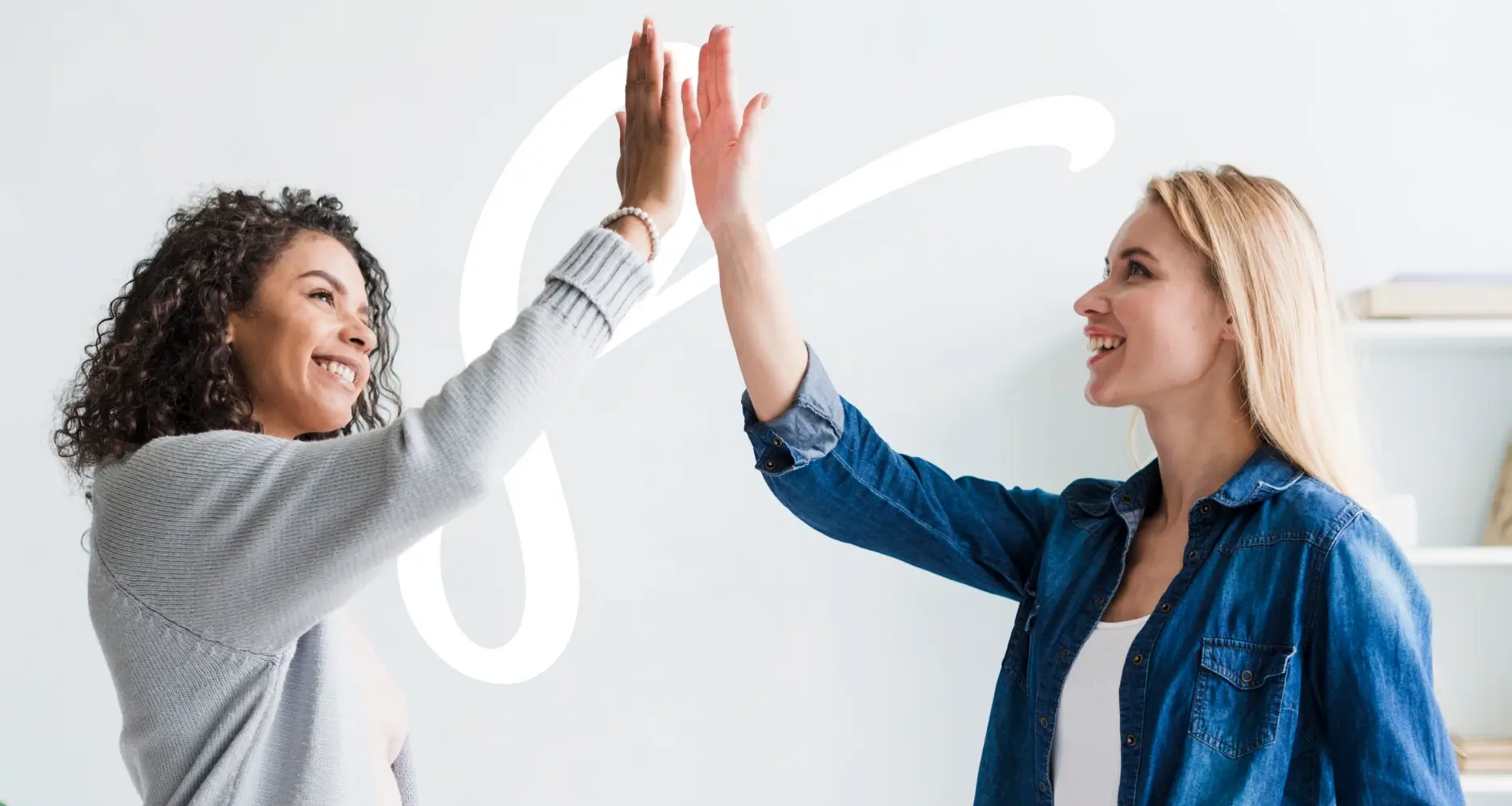
None
Training objectives
Identify and implement the conditions for the success of a QSSE * Quality - Health/Safety - Environment audit.
Learn to observe effectively and ask the right questions.
36Training program
Understanding the challenges of QSSE audits
- Reminder of key references, similarities and particularities.
- QHSE audits: particularities, purposes, goals and types.
- Qualities of the QHSE auditor.
Preparing for your QSSE audit: specifics
- Gather the regulations in force.
- Gather the QSSE system documents associated with the audited processes: standards, documented information, procedures...
- Develop your questionnaire 'QSSE audit, list the key points to check: case of system audits, processes.
- Prepare your interview guide by integrating the observations to be made in the field, in the company and outside .
Carry out the audit visit: specifics of the QHSE audit The opening meeting: introduce a QHSE audit.
- The field visit: alternate between documentary analysis and observations to collect evidence and identify QHSE risks; know how to look, feel, evaluate; check the consistency of the documents presented.
- S 'adapt to the auditee.
- Identify the auditor's good attitudes.
- Know how to take notes.
- Prepare your closing meeting.
- Present your conclusions: formalize the findings in a factual manner, prioritize the QSSE gaps observed.
Manage the post-visit
- Give meaning to your QHSE audits: establish substantiated, relevant and attractive reports.
- Obtain an action plan from the auditees.
- Monitor and measure it the effectiveness of actions.
CHSCT of SEVESO establishments
★★★★★
- QST-10
- 2 Days (14 Hours)
Description
The mission of the CHSCT is to contribute to the prevention and protection of the health of its employees, such as those made available by an external company, and to the improvement of working conditions in the company. The safety issues inherent to SEVESO classified establishments require knowledge of specific prerogatives for the prevention of major accidents, whether this involves issuing a relevant opinion on prevention documents (hazard study, POI, SGS, etc.). ), to identify the signals linked to the deterioration of the control of major accident risks or to encourage the involvement of personnel in accident prevention. This training, developed specifically for SEVESO establishments, is aimed at staff representatives at the CHSCT (in addition to the training provided for in art. L. 4614-14 of the Labor Code for the exercise of their missions) as well as at managers responsible for health, safety and risk management issues.
Who is this training for ?
For whom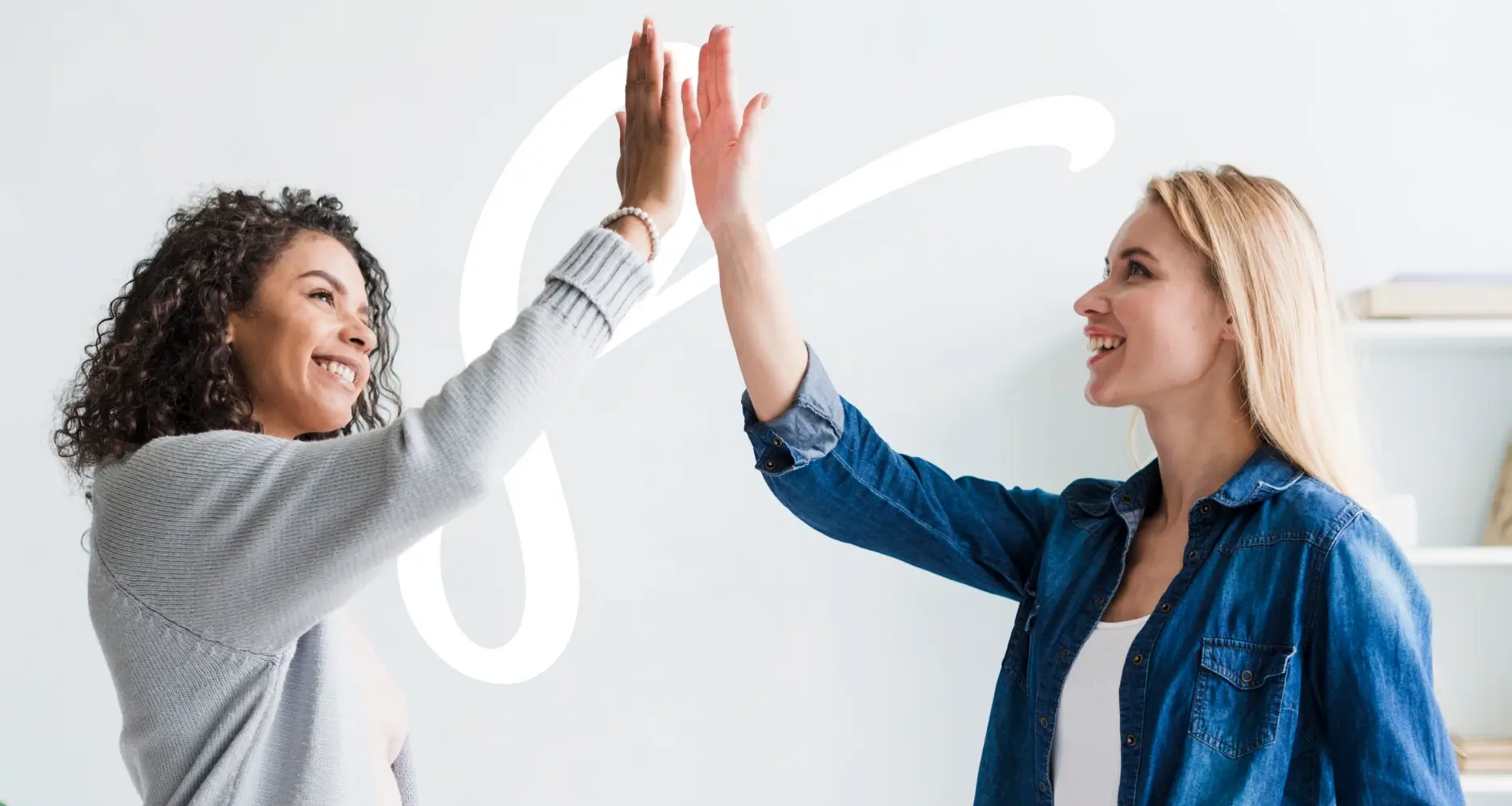
- This training is complementary to the legal training necessary for the exercise of the general missions of a staff representative at any CHSCT, provided for in Article L. 4614-14 of the Labor Code.
Training objectives
Issue a relevant opinion during the consultation of the CSE on major accident prevention documents.
Identify a deterioration in risk control.
39Training program
Why involve staff representatives at the CHSCT in the prevention of major accidents?
- Complementarity of regulations relating to work and Classified Facilities (IC).
- Attributions and roles of those involved in technological risk management.
- Positioning of the CHSCT.
- Case study based on a film relating the course of a major accident.
- Approach to controlling the risks of a major accident.
- L 'hazard study.
- Assessment of risk control.
- The Technological Risk Prevention Plan (PPRT).
Missions and means of action of staff representatives at the CHSCT
- Regulatory developments relating to the labor code in Classified Facilities (IC): law of July 30, 2003 relating to the prevention of technological and natural risks, the repair of damage and its implementing texts.
- Regulatory tools available to the CHSCT: advisory opinion, recourse to the technological risk expert, strengthening of the right to alert…
- The intervention of External Companies in SEVESO establishments.
- Bodies open to staff representatives: the extended CHSCT (to external companies), the CISST (Inter-company committee for health and safety at work), and the Site Monitoring Commission (CSS).
Quality Correspondent / Facilitator
★★★★★
- QST-11
- 2 Days (14 Hours)
Description
As true relays for Quality managers, Quality correspondents/facilitators must energize the Quality approach within their department or entity. This mission requires a good knowledge of Quality principles, as well as the associated key tools (Quality indicators, action plan, problem resolution, documentation, etc.). Discover these fundamentals in this 'Quality Correspondent / Facilitator' training which focuses above all on practice.
Who is this training for ?
For whom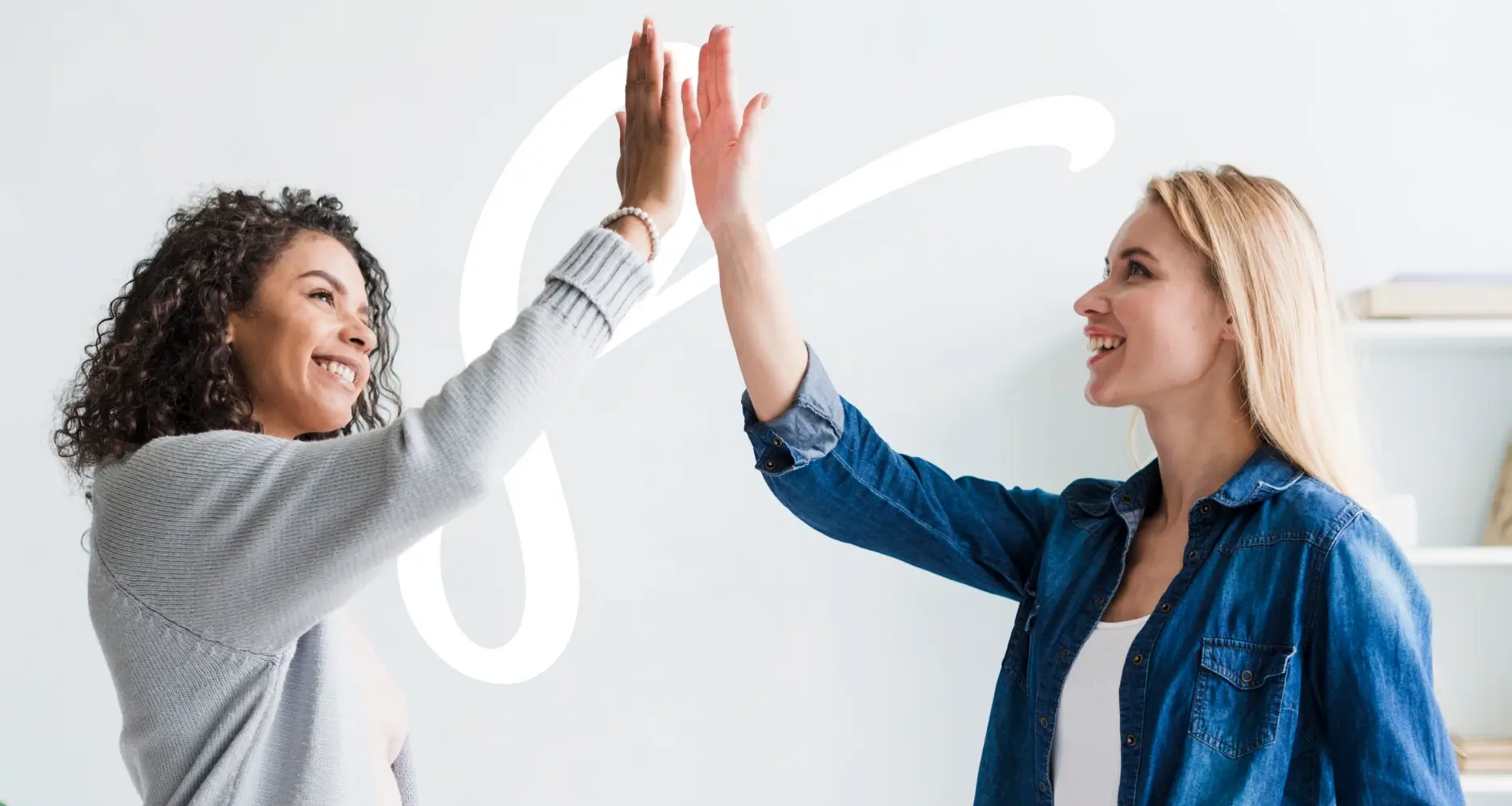
None.
Training objectives
Understand the principles of the ISO 9001 V2015 standard to relay to the quality manager and/or process managers
42Training program
The principles and challenges of a Quality approach
- The scope of a Quality approach, the vocabulary.
- Quality management and the PDCA cycle.
- The customer at the heart of the action.
Understanding the main points of ISO 9001 V2015
- The ISO 9001 V2015 standard: requirements by chapter.
- Key points of the process approach.
- The architecture and control of a document system: Quality manual, process sheets, procedures…
Bring improvement to life with the right Quality tools
- Identify areas for progress within its scope of action.
- Build your Quality action plan in line with the company's quality policy.
- Make Quality objectives concrete with operational staff.
- Trigger corrective actions using a problem-solving method.
- Help prepare for an audit.
- Ensure monitoring actions in its entity.
Measuring progress
- Manage using Quality indicators and dashboard: define them for your activity.
- Creation and communication of a Quality dashboard.
- Provide information to managers and Quality managers.
The mission of the Quality correspondent
- Relay between the Quality manager, managers and employees.
- Train, communicate, lead, be proactive.
43Remote activities
- An expert "ISO 9001 standard: knowing the key points of implementation" and a video "Formatting a quality indicator".
Complete training for the Quality Manager
★★★★★
- QST-85
- 10 Days (60 Hours)
Description
This cycle spread over several months constitutes the reference training for Quality managers who take up their duties, because it covers all the challenges that a Quality Manager must respond to.
In the first part, the issues and principles of a quality approach are explained, then the PDCA implementation tools.
The second session is reserved for the explanation of ISO 9001 V2015, then in the third part the key prevention and control tools are developed in addition.
Finally, the last part, in summary, gives the keys to carrying out audits to evaluate and manage your quality approach.
This professional course allows you to effectively and credibly take charge of your position as Quality Manager, by gradually building your company's Quality project from the intersessional periods.
This permanent practical application allows you to anchor your learning in a real situation or as close as possible to the field.
Who is this training for ?
For whom- Newly appointed Quality Manager within industrial or service companies.
- Engineer
- Project manager for a Quality function.
- Quality manager in position wishing to consolidate his practices.
- Future pilot or coordinator of the Quality approach (ISO 9001 certification or others).
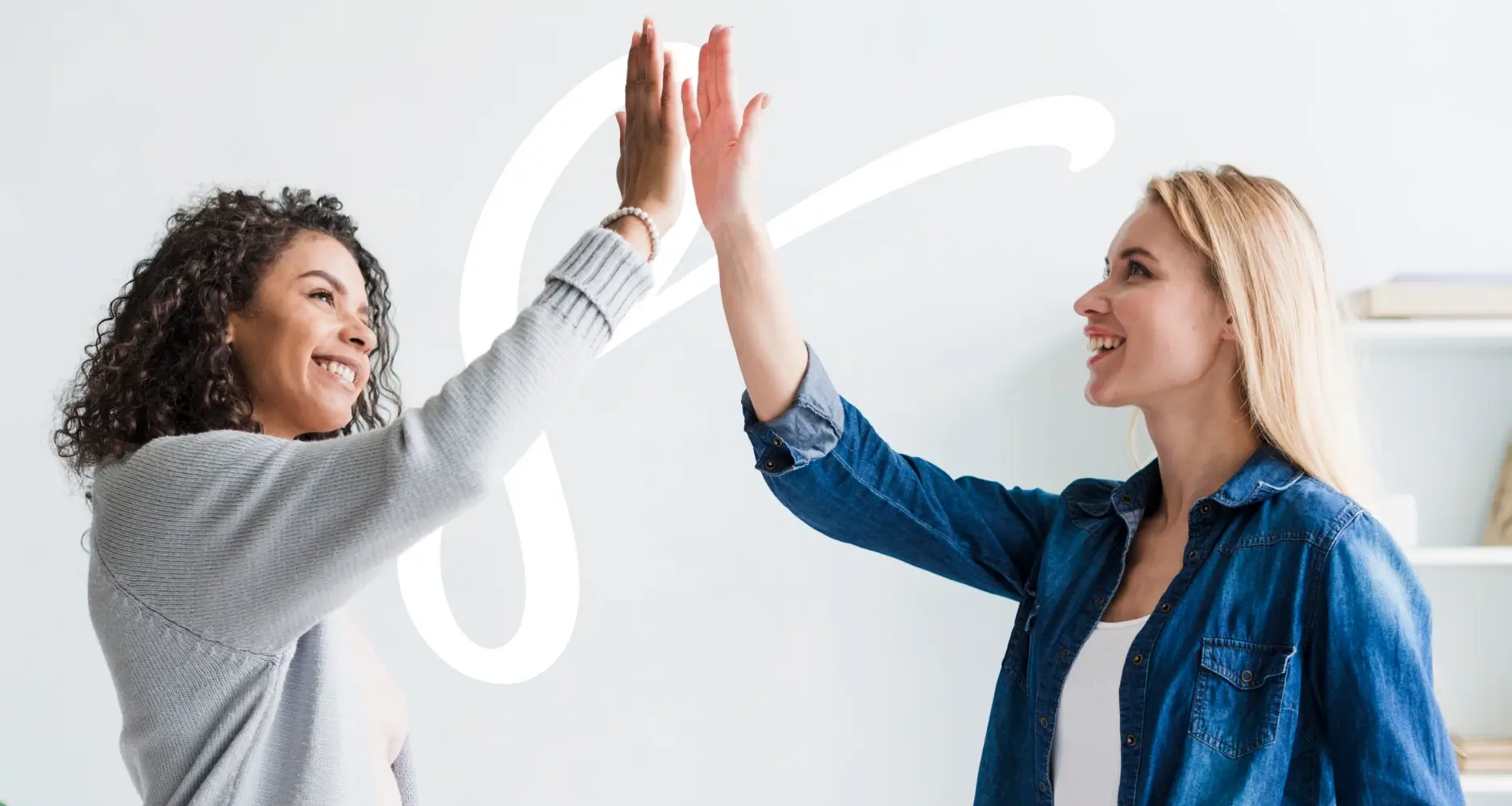
Know how the company works.
Training objectives
- Acquire a global and complete vision of the quality function
- Appropriate the essential quality methods and tools
- Build a quality project, bring it to life, make everyone involved in the process
- Identify the key points for successful ISO 9001 certification
46Training program
Before the face-to-face
- A self-diagnosis.
Quality: issues, approaches
- Quality at the heart of the company's competitiveness and performance. Putting the customer at the heart of the action.
- Understand the sequence: quality, quality management, quality assurance, control...
Implement a Quality approach
- Start with a relevant diagnosis (identification of non-quality costs, quality perceived by customers, dysfunctions, process assessment).
- Organize quality structures.
- Formalize the PAQ (action plan).
- Scenario Practical group case study.
Build the Quality dashboard
- Indicators to measure perceived and achieved quality.
- Use the quality dashboard as a management tool.
- Scenario exercises and self-diagnosis.
Define each person’s contribution
- Role, functions and missions of a Quality department.
- Find the motivating factors, the key players.
- Practical application: Before part 2 , participants analyze the context of their company and identify avenues for progress.
Understanding the logic of ISO 9001 V2015
- The logic of the ISO 9001 standard, the 10 chapters.
47Meeting the requirements of Standard 9001: key tools
- Analysis of the internal and external context of the organization: listening to interested parties, the process approach, risk analysis, data study.
- Management responsibility: the driving role of management and management; Responsibilities and quality authorities; formulation of the quality policy.
- Planning the QMS: formulating an action plan within a logic of prevention and improvement.
- Support processes: document control; key procedures, quality records to be created... management of skills and knowledge; 4
- Evaluation of quality and improvement performances.
- Scenario Exercises for translating the chapters of the ISO 9001. Presentation of concrete examples of meeting the requirements.
Establish your action plan
- The stages of certification. The pitfalls to avoid.
Remote activities
- To appropriate the contributions of an expert on a theoretical or practical point two
- experts "4 key tools of industrial quality" and "4 essential tools of quality of service".
- Practical application: Before session 3, implementation of ISO 9001 tools
Corrective actions to progress
- Solve problems with the CARREDAS approach and associated tools (Pareto, 5M, decision matrix, etc.).
- Corrective and preventive action sheets, monitoring of actions.
- Scenario Case study in sub-group.
FMEA to prevent failures
- Practice FMECA (Analysis of Failure Modes, Their Effects and Their Criticality) process and product.
- Take preventive and/or monitoring actions.
- Scenario Practical exercises.
48Key statistical methods
- Reception control.
- Statistical quality control: concept of centering and dispersion.
- Final control of the product or service.
Remote activity
- To illustrate the contribution of knowledge, a video "Succeeding in audit interviews".
- Practical application: Study of the opportunity to implement the tools seen in session 3
The challenges of quality audit
- System audit and process audit.
- Organize internal and external audits.
Prepare for the audit visit
- Determine the area to be audited.
- Constitute the audit team. Develop the schedule.
- Gather and study the reference documents.
- Develop an audit questionnaire and an interview guide.
- Scenario Application to a case study.
Practice the audit visit
- Lead the kick-off meeting.
- Master questioning and note-taking. Obtain concrete answers.
- Communicate initial conclusions. Simulation of interviews.
49Manage the post-visit
- Write a simple and useful report.
- Follow the auditees' action plan.
- Scenario Application to the case study.
After face-to-face - Implementation in a work situation
- A reinforcement program by email.
Practical training in FMEA* product and process
★★★★★
- QST-82
- 2 Days (14 Hours)
Description
Increasingly complex and efficient products and systems lead companies to implement rigorous prevention methods both in terms of product design and the implementation of new processes. Product and process FMEA* allow you to identify, evaluate and control quality risks when there is still time to act! Optimizing validation and monitoring plans, reducing non-quality costs, preventing failures are all objectives during this training that FMEA pilots aim for. *Analysis of Failure Modes, Their Effects and Their Criticality.
Who is this training for ?
For whomEngineers and technicians from methods, industrialization, manufacturing, quality and maintenance departments and anyone who must lead or participate in Process FMEAs.
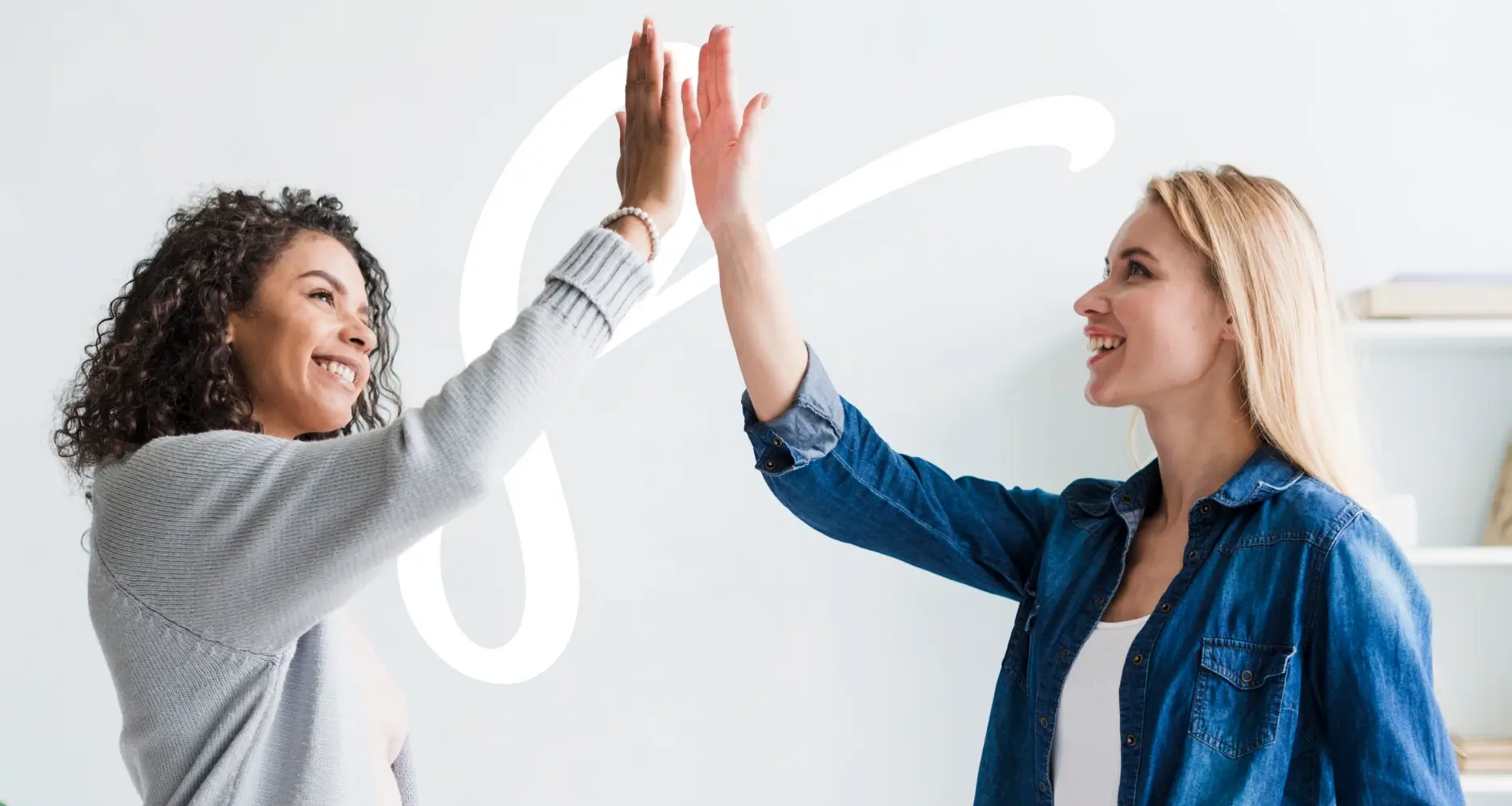
This training does not require any prerequisites.
Training objectives
Know the objective and scope of a Process FMEA.
Identify the way of analyzing the product risks potentially generated by the implementation of the production process.
Understand the rules for running this tool for efficient work.
Effectively practice the product and process FMEA method (*Analysis of Failure Modes, their Effects and their Criticality).
52Training program
Situate the principles of FMEA
- Factors triggering an FMEA: prevention logic, risk management; contractual aspects with the customer; ISO 00 V0 certification.
- Define the goal and principles of the FMEA applied to the product or business processes.
Practicing product FMEA
- Define the study: objectives, limits, working group.
- Prepare the study, use the functional analysis of the product.
- Identify and evaluate the potential product failures.
- Calculate the criticality of failures, reason risks.
- Find corrective actions to reduce identified priority risks, plan and implement them.
- Reassess potential failures.
Manage process FMEA
- Select the priorities.
- Prepare the study: build a synoptic overview of the process.
- At each stage of the process, analyze and evaluate potential failures (risks of product non-conformity) linked to the production or support process.
- Calculate the criticality of failures.
- Find corrective actions to reduce the criticality of process failures.
- Reassess potential non-conformities.
- Plan, implement corrective actions.
53Manage and lead an FMEA
- The role of the facilitator: ask the right questions.
- Create a relevant and creative FMEA group.
- Succeed in your FMEA.
- Know how to present conclusions internally and to the client.
Practical training on the cause tree
★★★★★
- QST-14
- 1 Days (7 Hours)
Description
Despite all the prevention measures put in place, sometimes accidents occur. It is then important to understand why this event appeared, what is the chain of causes that led to it and above all how to act to definitively avoid its recurrence. This practical training in the tree of causes will be a source of progress on the subject.
Who is this training for ?
For whom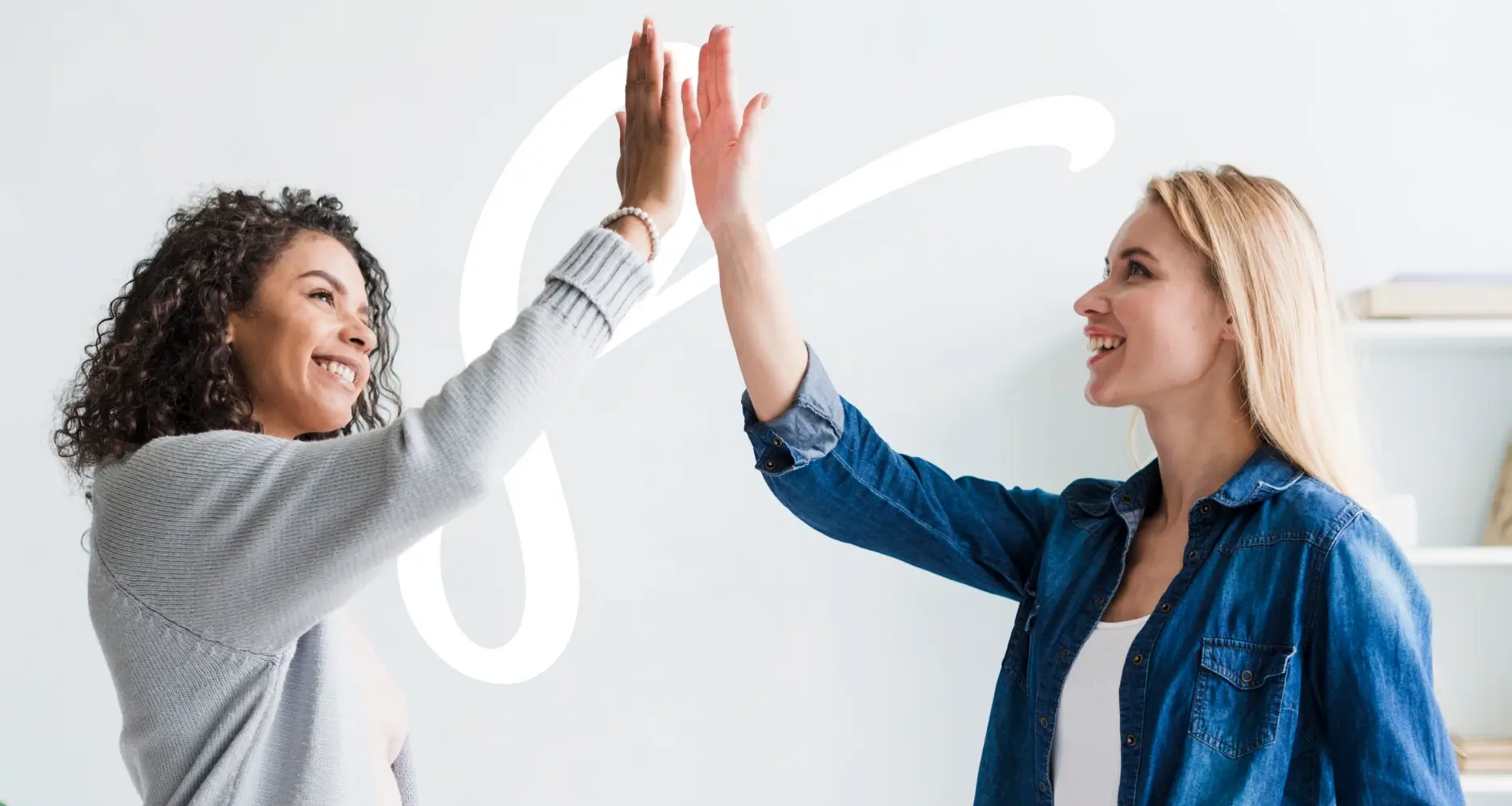
None.
Training objectives
Discover and practice the cause tree to find the root cause of a problem or accident and take effective corrective actions
56Training program
Before the face-to-face
- A self-diagnosis.
Objectives and purposes of the cause tree
- The purpose, interests and limits of the tree of causes.
- Place of the tree of causes in problem resolution and more generally in the Health and Safety approach of the company.
- The accident mechanism: understanding it to better anticipate it.
Understand the associated methodology
- Create a working group.
- Collect facts and data on the accident or problem to be treated: associated tools to be effective.
- Search for the 'sequence of causes at the origin of the event: ask yourself the key questions.
- Construct the tree of causes respecting logic: sequence connection.
- ; Verify the elements in the field before concluding.
- Produce usable accident reports.
- Deduce key corrective and preventive actions.
Practice the tree of causes
- Moving from theory to practice: essential advice for collecting data and building the tree.
- Organize the development of the tree collectively.
- Produce a clear and relevant report.
After face-to-face, implementation in a work situation
- A reinforcement program by email to help put it into practice.
Practical training for Quality controllers
★★★★★
- QST-15
- 3 Days (21 Hours)
Description
The guarantee of quality delivered to the customer cannot be debated: whether in industrial or service companies, quality control guarantees the conformity of products and supplies. To be even more effective, control must be more than an observation and provide real avenues for improvement for operational staff. This training helps controllers to take a step back, to be more relevant in their findings and their actions, but also to work in synergy with other operational sectors.
Who is this training for ?
For whom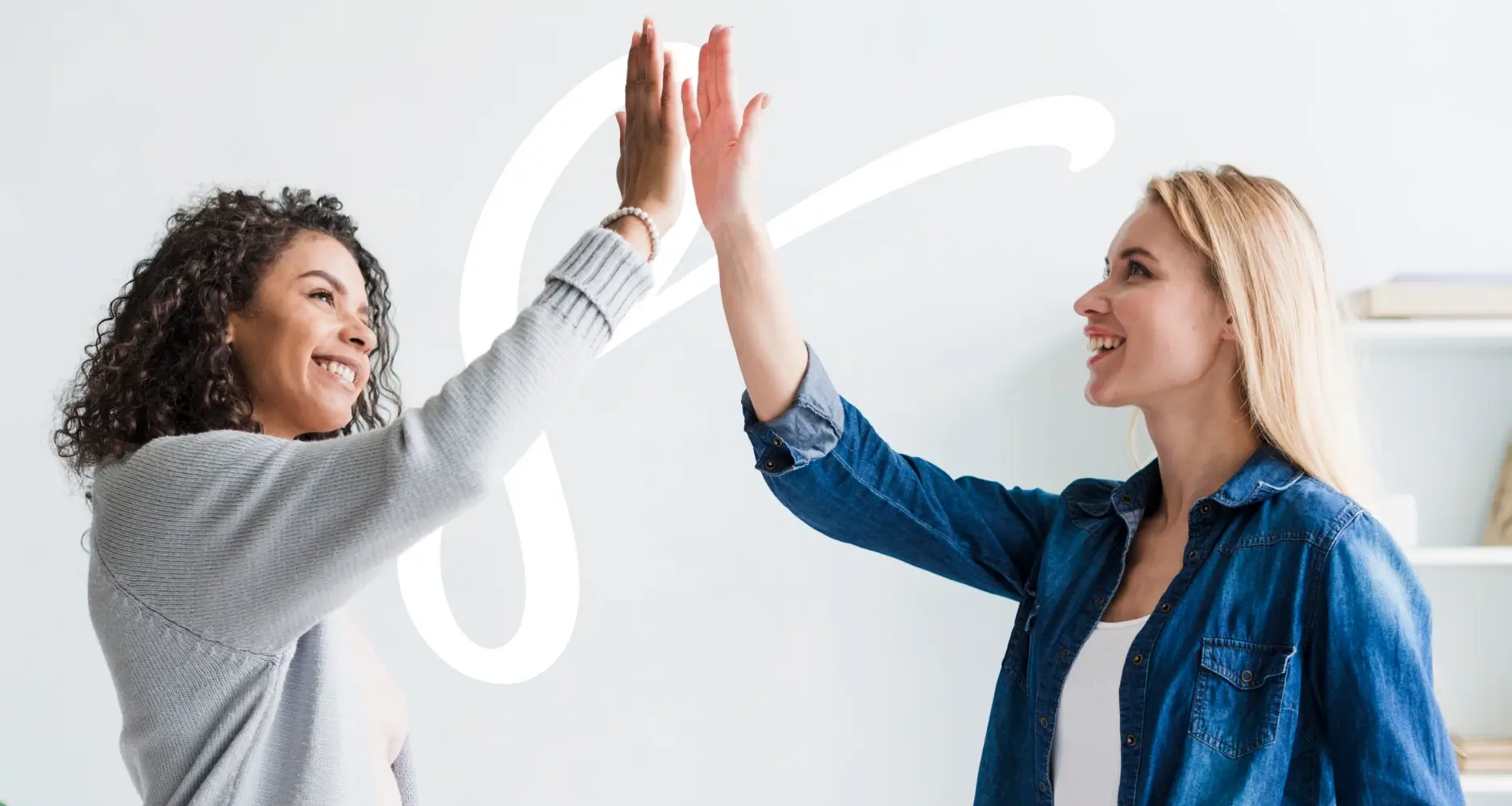
None.
Training objectives
Have the essential tools to make controls more effective and initiate continuous improvement.
Adopt the right attitudes to create positive relationships with operational entities.
59Training program
Discover quality in the company.
- Quality concepts and compliance.
- The importance of the continuous improvement cycle (PDCA).
- Main requirements of ISO 9001.
Control production
- Types, methods and control plan.
- The challenges of metrology: concept of repeatability and reproducibility.
- The concept of monitoring plan: product control process control.
Practice reception control
- Acceptance control by attribute: use of MIL STD 0 standards, associated risks.
Practice in-process control (SPC)
- Check the 'capability' of the machine and process.
- Principle of control cards and associated management rules: anticipate the appearance of non-conformities.
Perform the final check
- The Demerits method to verify the overall conformity of the product or service delivered.
From control to continuous progress
- Statistically exploit the control results (graphs, PARETO, centering values and dispersion).
- In the event of detection of non-compliance: control the non-compliant product. Find solutions "poka yoké"
- Manage the implementation of corrective actions with operational staff. Validate their effectiveness.
Acquire the Quality reflex in the workshops
- Responsibilities for self-control.
- Responsibilities of the controller: attitudes to create positive relationships.
Build your progress plan
Crisis management
★★★★★
- QST-16
- 2 Days (17 Hours)
Description
In the event of an accident on an industrial site, the internal operation plan aims to protect the personnel, property and environment of the establishment. A structured operating PC, reflex action sheets, tools to anticipate developments in the accident and its potential consequences are the key to an effective emergency management organization.
Who is this training for ?
For whom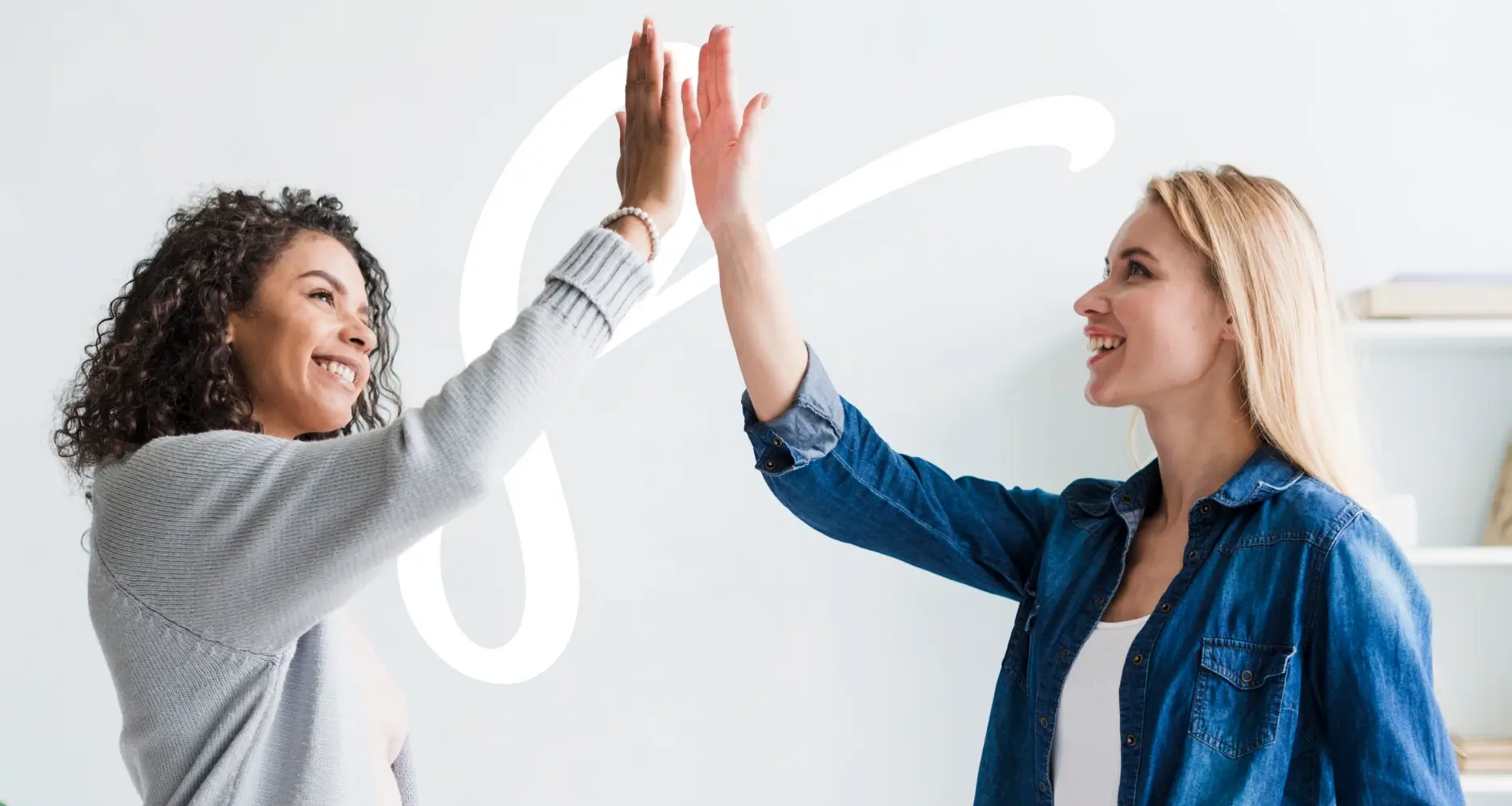
- Know your company’s POI.
Training objectives
Manage a crisis in the event of an industrial accident, using crisis management tools, including the Internal Operation Plan (POI) and working effectively within an Operator PC
62Training program
Hazard Study (EDD) and POI
- The links between the EDD and the POI.
- The expectations of a POI in relation to the EDD: from a regulatory point of view; from a point of view operational.
- The regulatory context: POI / Special Intervention Plan (PPI).
Crisis organization
- Strategic locations, crisis room equipment.
- The different functions of crisis management: Operator and field PC.
- Roles and missions of each actor.
- The organization before and after the arrival of external assistance.
- Tools to help with crisis management.
Practical guide to the ISO 14001 version 2015 standard
★★★★★
- QST-17
- 2 Days (14 Hours)
Description
This training offers all the tools to understand and meet the requirements of the ISO 14001 version 2015 standard and improve the company's environmental performance. During the training, participants build their specific action plan helped by the advice and experience of our consultant-trainer.
Who is this training for ?
For whom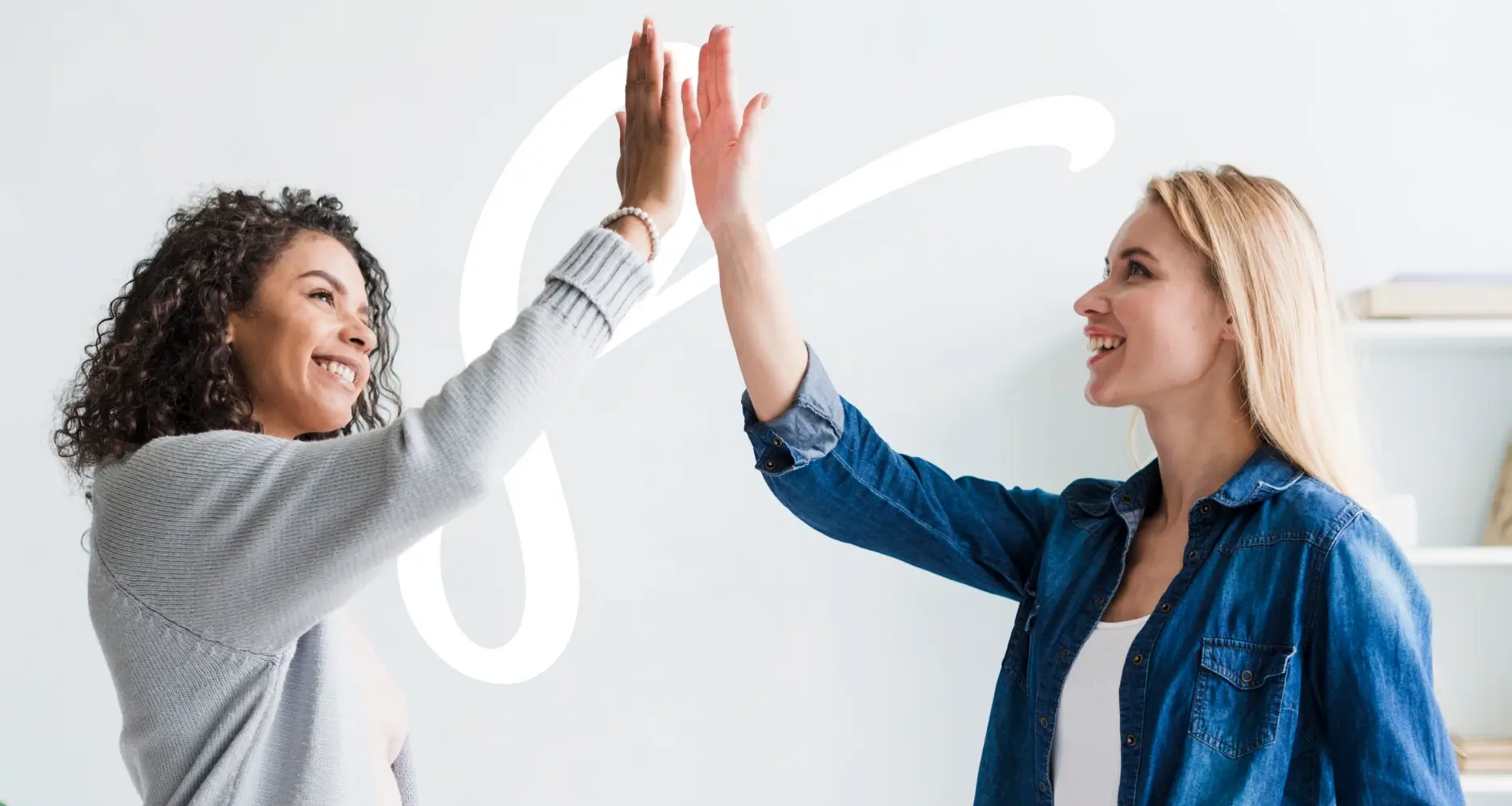
Training objectives
Know how to interpret the requirements of the ISO 14001 V 2015 standard.
Identify the concrete means to respond to them within the framework of your activity.
65Training program
Challenges of ISO 14001V2015
- The objectives sought, concept of environmental performance.
- Vocabulary and key concepts.
- Reminders on environmental regulations.
Context analysis (Chap 4)
- Understanding the internal and external context of the company.
- Identify, listen to interested parties.
- Reason risks/opportunities.
- Define the scope of application.
Leadership and planning (Chapters 5 and 6)
- The driving role of management.
- Clarify roles, responsibilities. Involvement of managers.
- Carry out an initial impact analysis based on the product life cycle.
- Identify priorities, formulate an environmental policy.
- Formalize an action program (objectives, targets, resources, monitoring, etc.).
- Compliance obligations.
66Support and control of operational activities (Chap 7 and 8)
- Adapt material and intangible resources.
- Build an adapted documentation system (notion of documented information, procedures, records).
- Ensure competence, awareness personnel.
- The communication plan.
- Operational control: good field practices (in normal and emergency situations).
Performance evaluation and improvement (Chap 9 and 10)
- Implement controls and key indicators.
- React to non-compliance.
- Trigger corrective actions.
- Organize management reviews
Pass your ISO 14001 V2015 certification
Practical guide to ISO 45001
★★★★★
- QST-87
- 3 Days (21 Hours)
Description
The ISO 45001 standard (International Standard Organizations) is the new international reference text which specifies the requirements for a health and safety management system as well as the guidelines for their use. It thus helps to develop and implement a prevention and continuous improvement approach aimed at reducing and/or eliminating professional risks and providing employees with safe working conditions. Discover in this new training how to concretely meet the requirements of this new ISO 45001 standard with a view to certification or not.
Who is this training for ?
For whom- Director.
- Manager.
- Health and Safety Facilitator.
- Team manager.
- Safety representative.
- ISO 45001 certification project manager.
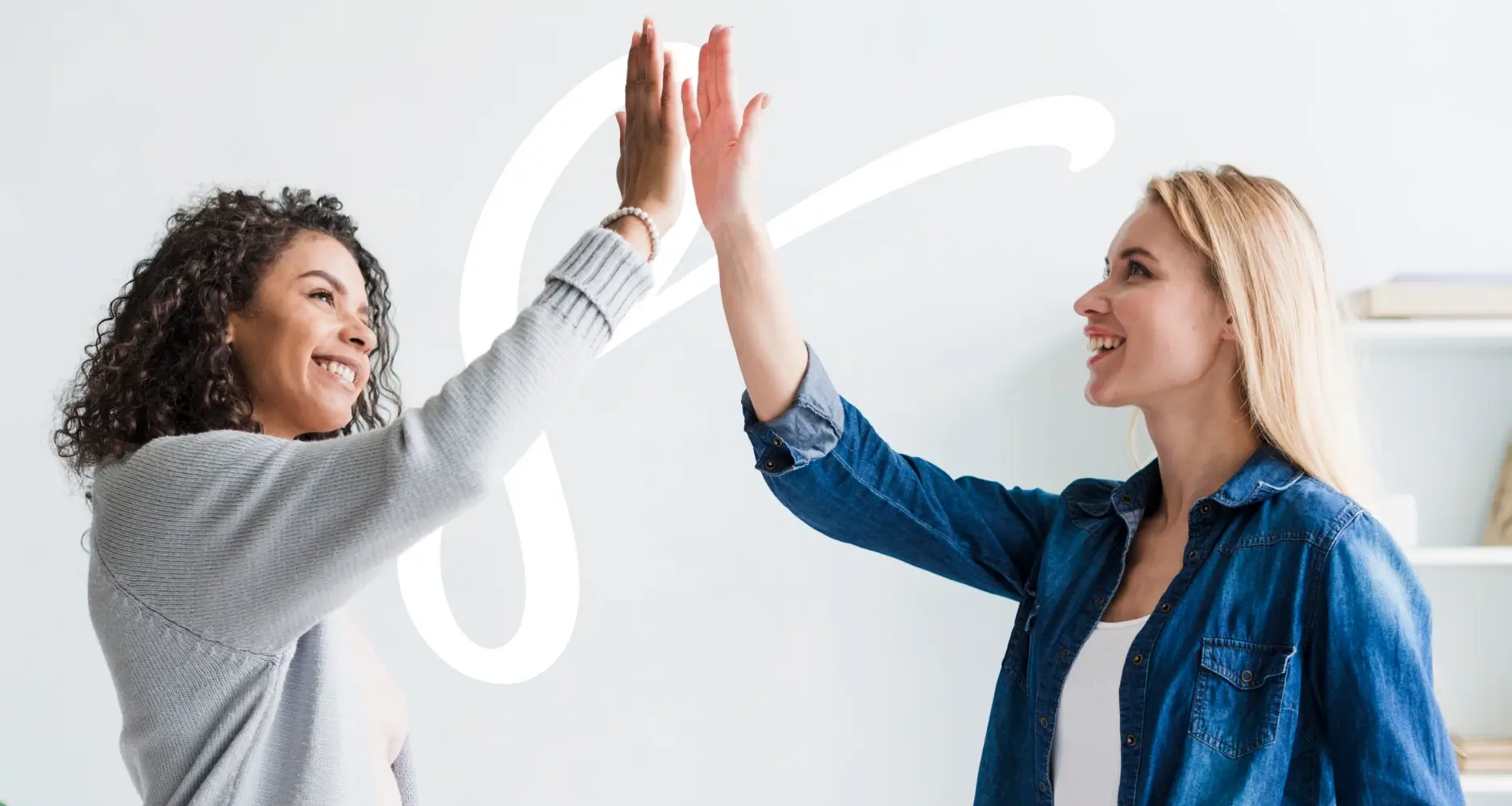
None
Training objectives
- Understand the issues and vocabulary of an Occupational Health and Safety (OHS) management system
- Analyze the requirements of ISO 45001, identify their logic and key points
- Identify the concrete means to be implemented in the company to answer them
69Training program
Before the face-to-face
- A self-diagnosis.
Chapter. 4: Context of the organization
- Analyze the internal/external context of the company.
- Field of application.
- Concept of interested parties.
- The key elements of the system.
Ch 5 and 6: leadership participation, planning Key role of general management, formulation of OHS policy. Define responsibilities. Consultation and participation. OSH risk assessment.
- Key points of the regulation.
- From policy to OHS objectives, action planning.
Chap. 7 and 8: support and implementation of operational activities Provide appropriate resources.
- Raise awareness, communicate.
- Ensure staff competence.
- Mastery of documented information.
- Planning and operational control.
- Case of outsourcing and purchasing.
- Emergency situations.
Chap. 9 and 10: evaluation and improvement of OHS performance Create a monitoring plan.
- Internal OHS audits.
- Regulatory compliance assessment.
- Management review.
Successfully complete your certification After face-to-face training, implementation in a work situation
- A reinforcement program to help you implement your training.
70Certification Assessment of skills to be certified via an online questionnaire incorporating role-playing scenarios (40 minutes).
- To find out more about remote activities To support you in your implementation: an
- expert 'Organize QHSE regulatory monitoring'; a video 'Tutorial: Formatting SSE indicators'.
Practical guide to ISO 9001 - Special industry
★★★★★
- QST-82
- 3 Days (21 Hours)
Description
Discover in this very operational training, the principles and requirements of the ISO 9001 V2015 standard, its application in the context of your industrial activity. Back in the company, rely on the action plan developed during training to build and/or develop your management system in compliance with the requirements of ISO 9001 V20015, with a logic of risk management and continuous progress. /p>
Who is this training for ?
For whomQuality manager, quality correspondent. Quality Insurance Manager. Responsible for the industrial company certification project.
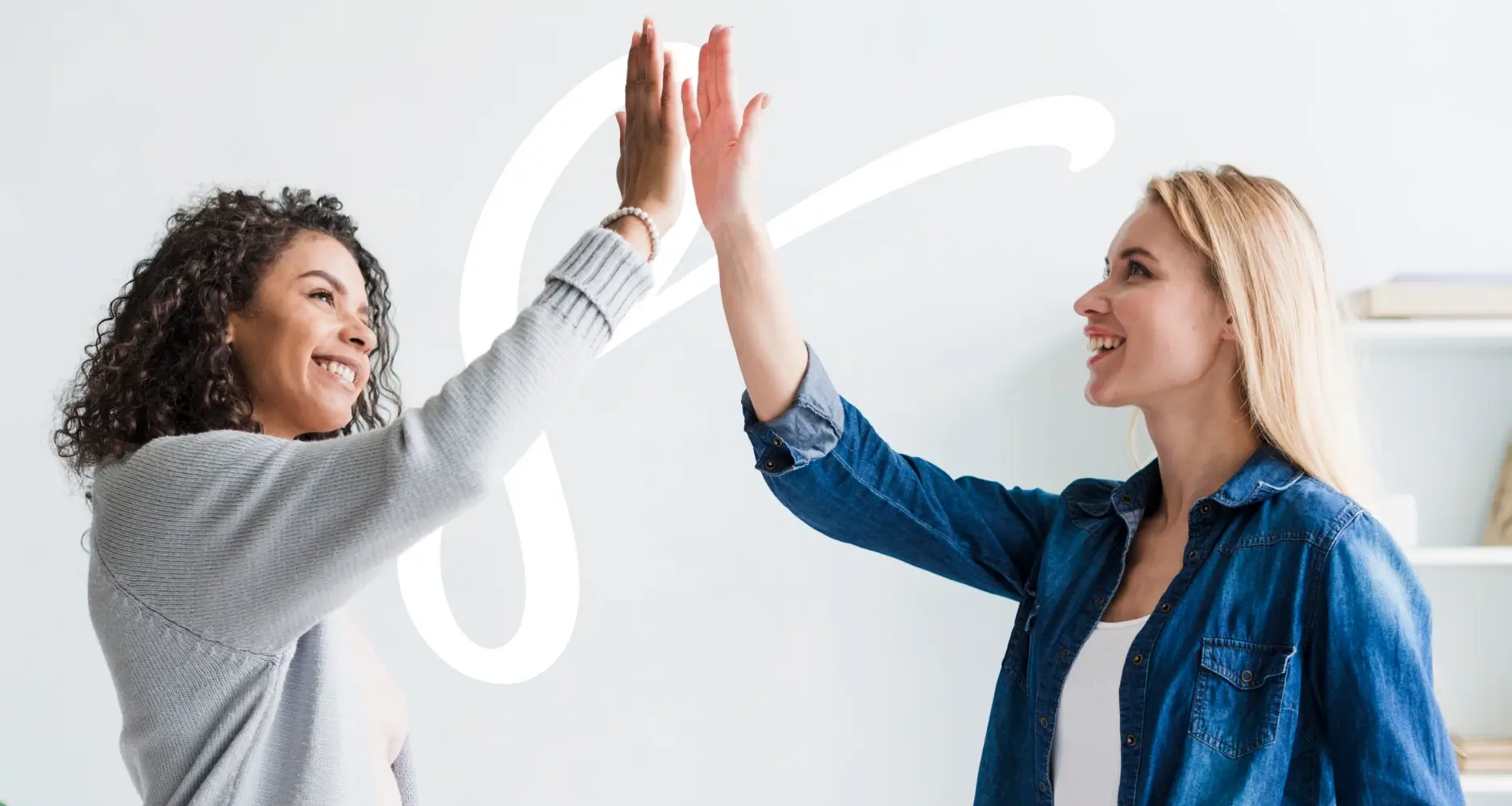
None
Training objectives
Identify how to respond in a simple and concrete way to the requirements of the ISO 9001 V2015 standard by bringing real added value to your company.
Identify the steps to progress to obtain and maintain certification.
Build your individual action plan .
73Training program
ISO 9001 V2015 Vocabulary, principles and issues. 10 chapters of ISO 9001. Context analysis (Ch 4) Understanding the internal and external context of the organization, identifying risks/opportunities.
- Identify your interested parties.
- The process approach: identify, describe, manage processes.
Leadership (Chapter 5) Build on management commitment and strategy. Customer listening to start. Formalize the quality policy.
- Clarify everyone's role.
Planning (Chapter 6) Translate policy into measurable quality objectives.
- Formalize your action plan.
Supports (Chapter 7) Build and master a relevant documentary system.
- Adapt infrastructures.
- The communication plan.
- Integrate the notion of metrology.
- Human resources management: evaluate, provide skills, raise awareness.
- Manage knowledge.
Carrying out operational activities (Ch 8) Improve your purchasing, sales, production, design, delivery processes, etc. Manage non-compliant product. Performance evaluation and improvement (Ch 9 and 10) Key quality indicators.
- Measuring customer satisfaction, process and management reviews, internal audits.
- Carry out corrective actions.
Pass your Remote Activities certification
- In addition to the training, an e-learning module 'Problem solving tools and methods' and a tutorial 'Describing a quality process'.
Practical guide to ISO 9001 - Special services
★★★★★
- QST-20
- 1 Days (7 Hours)
Description
Favoring the practice and specificities of service companies, this training helps you understand the requirements of ISO 9001 V2015 and how to respond to them within your company. It provides you with the assets to successfully complete ISO 9001 V2015 certification.
Who is this training for ?
For whom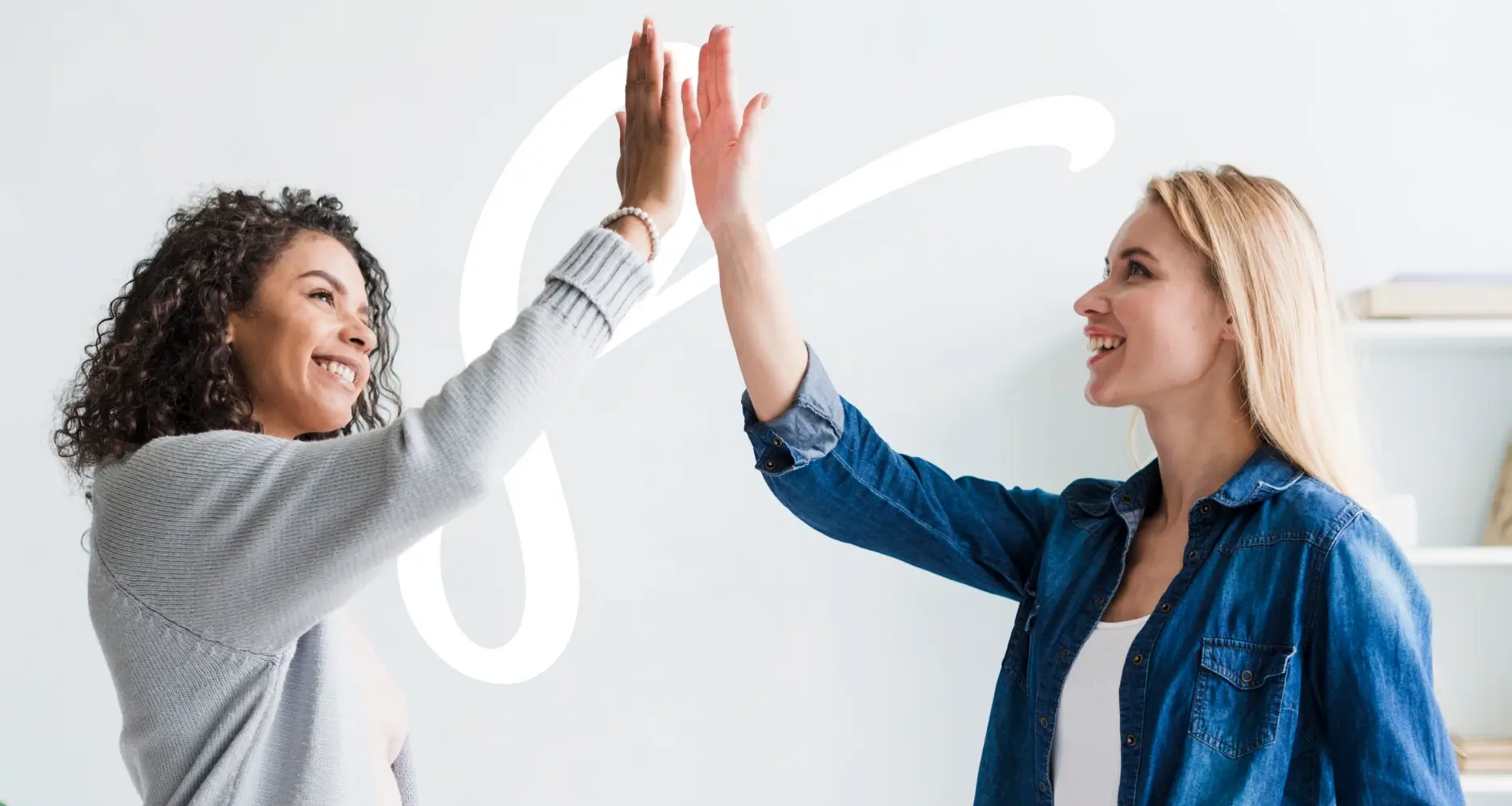
None.
Training objectives
Identify the means to meet the requirements of the ISO 9001 V2015 standard within a company.
Locate the steps to successfully complete certification.
76Training program
The ISO 9001 V2015 standard: Vocabulary, principles, issues.
Context analysis (Chapter 4)
- Understand the internal and external context of the organization. Identify risks/opportunities.
- Notion of customers and interested parties.
- The process approach: identify, describe, manage processes.
Leadership (Chapter 5)
- Formalize the quality policy.
- Clarify everyone's role.
QMS Planning (Ch 6)
- From policy to quality objectives.
- Formalize your action plan.
Supports (Ch 7)
- Build a relevant documentation system, (documented information).
- HR management: evaluate, provide skills, raise awareness.
- Manage knowledge.
- Adapt infrastructure.
- The communication plan.
Carrying out operational activities (Ch 8)
- Analyze and improve key purchasing, sales, production, design, post-delivery activities.
- Control of non-compliant product.
Performance evaluation and improvement (Ch 9 and 10)
- Key quality indicators.
- Measuring customer satisfaction, process reviews, internal audits. Corrective actions.
- Management review.
Passing certification: key points
77Remote activities
- Two e-learning modules "Problem solving tools and methods. Go. A","Problem solving tools and methods. Go. B" and a tutorial: "Describing a quality process".
ISO 9001 V2015: managing risks and opportunities
★★★★★
- QST-21
- 2 Days (14 Hours)
Description
The international ISO 9001 V2015 standard requires companies to take a risks and opportunities approach. Companies must, in this new framework, identify the risks and opportunities that must be taken into account to ensure the effectiveness and continuous improvement of the Quality Management System. This new training gives you the operational tools to anchor this logic in your quality approach.
Who is this training for ?
For whom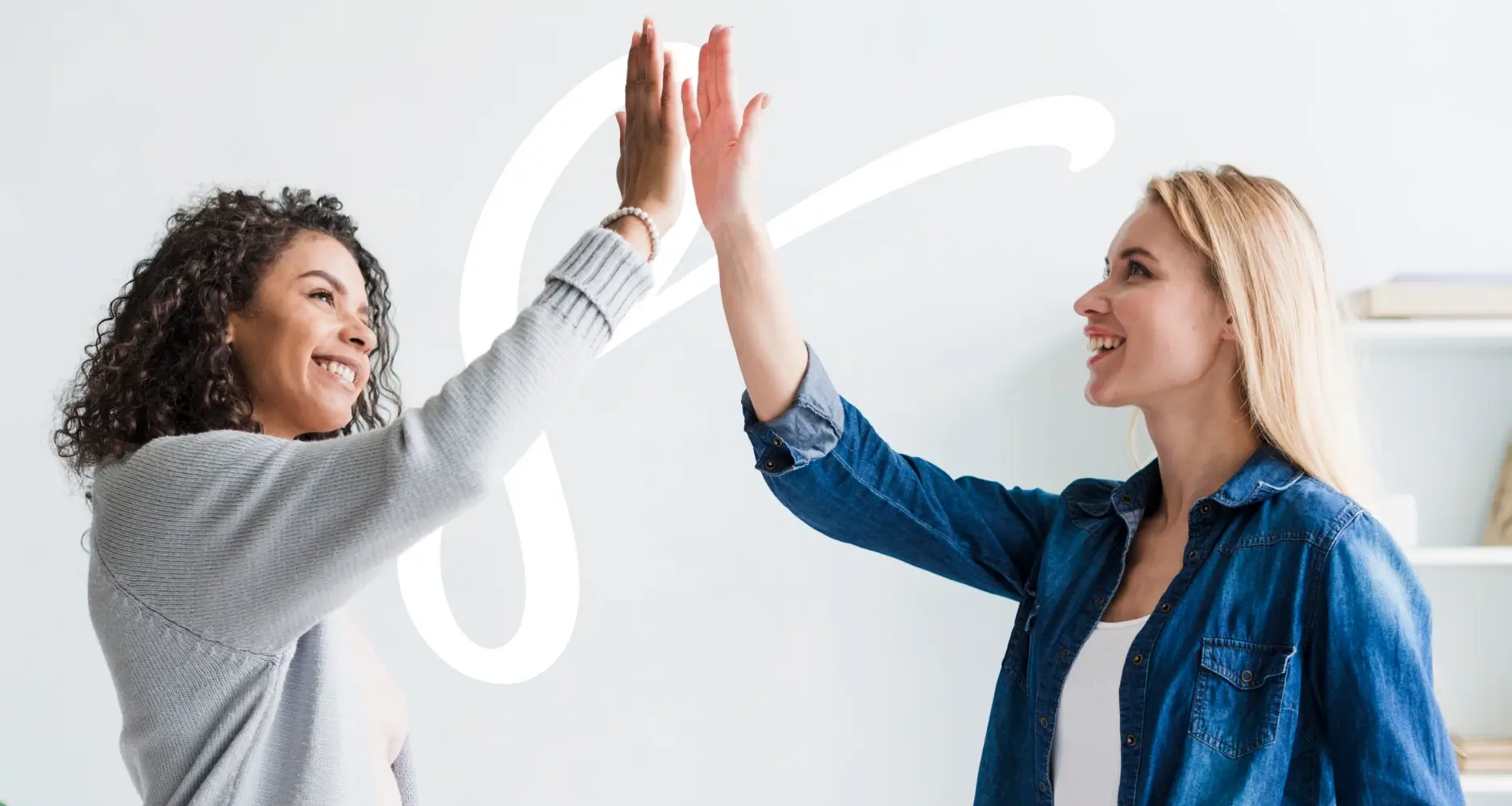
None
Training objectives
Understand the challenges of a risks and opportunities approach
Discover the operational tools to implement this approach
80Training program
Before the face-to-face
- A self-diagnosis.
The challenges of the approach
- Risks and Opportunities Concept of risks and opportunities within a QMS (Quality Management System): what the ISO 00 V0 standard says, the vocabulary; benefits of a logic of prevention, improvement and anticipation; anchor this logic in the analysis and understanding of the context.
- SWOT: synthesis tool.
91215Implement a risk-based prevention approach
- Identify risks at different levels: strategic, processes, products and services.
- Know how to simply identify and evaluate real quality risks on processes, taking into account the severity and occurrence .
- Commit to risk management: establish your prevention and/or protection plan, implement it and check its effectiveness.
- Bring the risk approach: update the analysis; organize audits.
- Prepare an assessment during management and process reviews.
Knowing how to seize opportunities
- Exploit external opportunities.
- Use team meetings, customer listening, process reviews, audits, surprise reports...
- to create internal momentum.
- Select an opportunity based on objective criteria, transform it into action, measure its effectiveness.
- Use digital.
After face-to-face, implementation in a work situation
- An Excel file helps you put your risk analysis into practice.
Quality at the service of the customer experience
★★★★★
- QST-22
- 2 Days (14 Hours)
Description
Improving perceived quality and working on the customer experience is one of the new projects for the Quality Manager. Beyond product compliance, beyond the process approach, this work orients the quality system on what experiences, on what the customer really perceives through these interactions with your company. These two days of training allow you to build an action plan resolutely aimed at enthusing your customers throughout their journey.
Who is this training for ?
For whom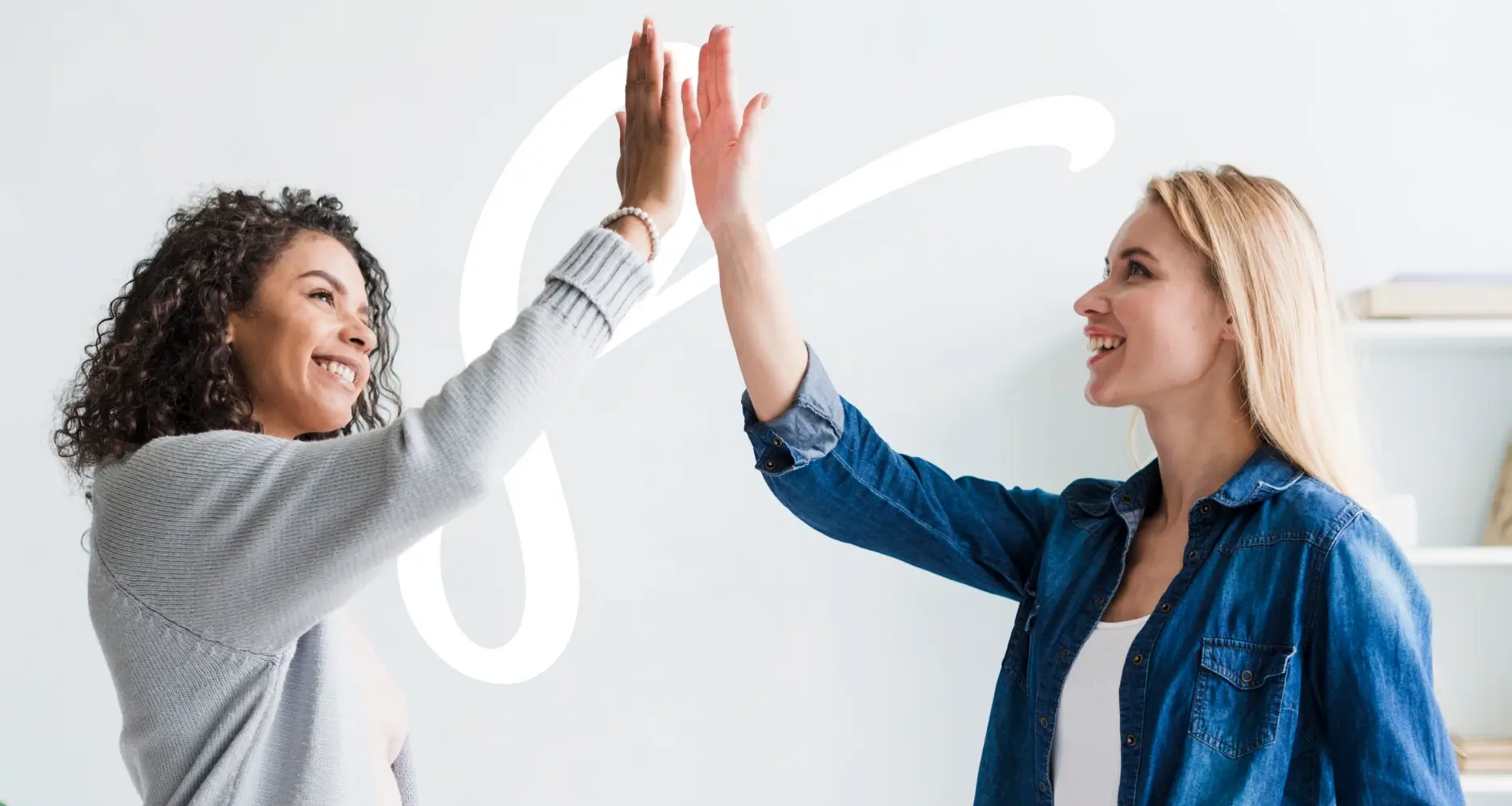
- This training requires knowledge of the principles of quality management systems.
Training objectives
Build your customer journey and associate it with a continuous improvement plan to strengthen the customer experience.
Apply operational tools.
83Training program
Before the face-to-face
- A self-diagnosis.
The challenges of perceived quality and customer experience
- The scope of the customer experience on the customer journey.
- From expected quality to perceived quality: aiming for customer enthusiasm.
Describe the customer journey
- Link the customer journey to company processes.
- Reason multichannel and personae.
- Associate customer expectations and their expectations at each key stage. emotions" .
- Secure the route, establish the prevention plan, check its effectiveness.
Improve customer satisfaction along the way
- Measure perceived quality: surveys, NPS, CES, audits and mystery shoppers.
- Define progress objectives, formalize your action plan.
- Optimize relationships with the customer along the way: best front office practices.
- Dealing with dissatisfied customers, managing social networks.
- Identifying seduction expectations: aiming for "wow!" effect. Create a competitive advantage.
After face-to-face - Implementation in a work situation
- Available online: a tool to build your customer journey and after face-to-face, a personalized activity that will allow you to translate it into a work situation.
The quality assistant
★★★★★
- QST-81
- 2 Days (14 Hours)
Description
Placing the customer at the heart of the processes implies the mobilization of everyone, in the service of quality. At the heart of the action, the Quality Assistant anticipates, alerts, organizes, communicates and contributes to energizing the daily approach by supporting the Quality manager. This training provides the essential tools and methods for the quality assistant to strengthen their added value within the Quality structure.
Who is this training for ?
For whomQuality Assistant.
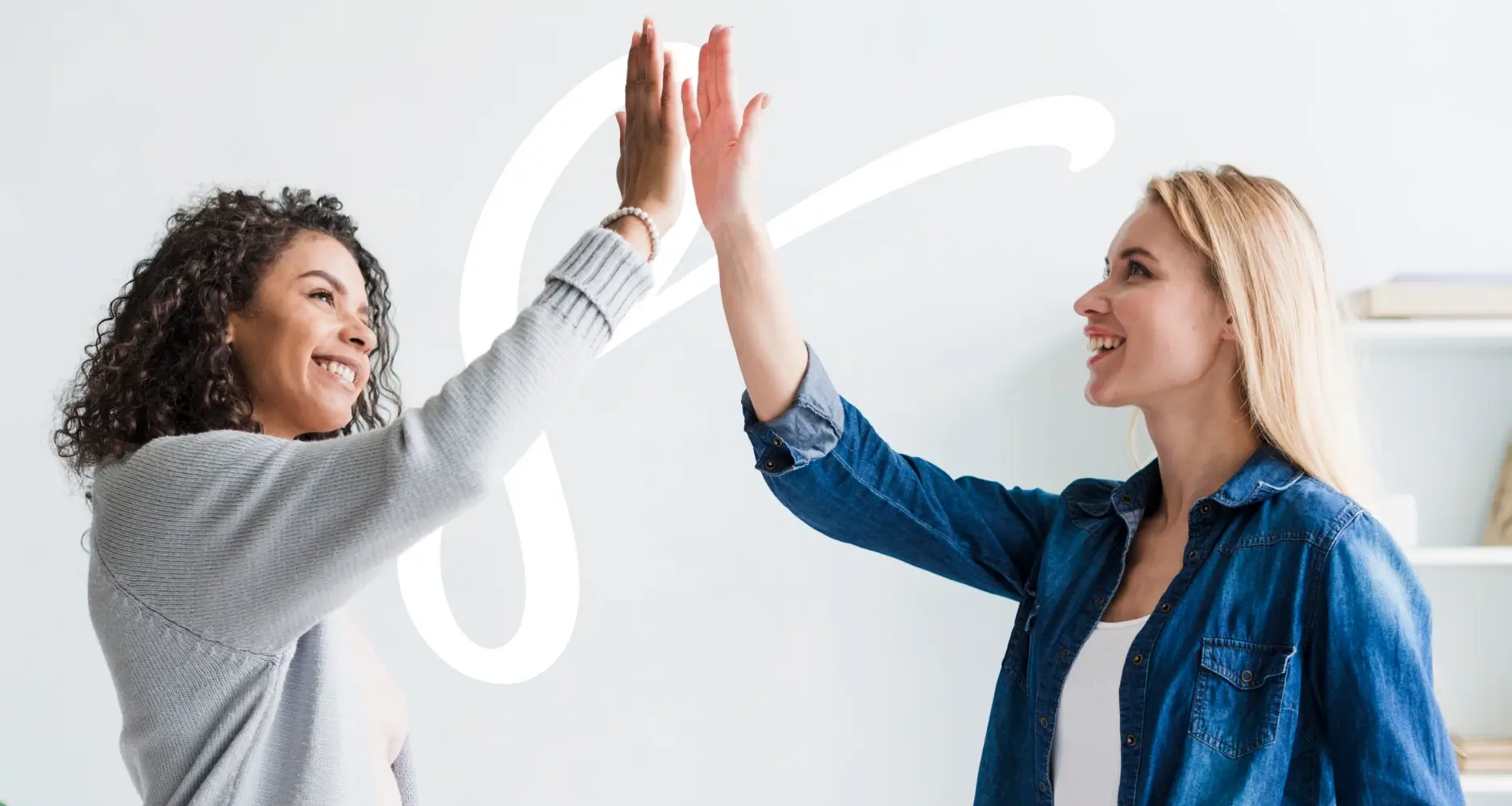
None.
Training objectives
Use the main tools to carry out your mission.
Identify the key points of the ISO 9001 V2015 standard.
86Training program
Finding your way through vocabulary and standards
- Understand the principles of quality management, the vocabulary.
- Specify the requirements of ISO 9001 v2015: the process approach, the risk approach…
- Identify key quality events: management review, process review, internal and external audits...
Participate in the management of the quality documentary system
- Know the architecture of the documentary system.
- The requirements of the ISO 00V0 standard in terms of documented information: distribution, updates; archiving, classification.
- Adapt the documentation to needs, make it simple and effective.
Assist the quality manager in deployment
- Formalize the mission of the quality assistant.
- Assist in the implementation of the quality management system: manage schedules (audits, reviews, work plan quality actions...), ensure the progress of progress actions: corrective actions, processing of complaints, help auditors prepare their internal and external quality audits.
- Ensure measurement and quality monitoring: format dashboards, communicate results effectively.
Effectively promote the Quality approach
- Prepare and participate effectively in quality meetings, know how to follow up, diplomatically receive and process a customer complaint, be a source of proposals.
Remote activity
- To support you in your implementation: a video 'Tutorial: Formatting a quality indicator'.
The prevention plan
★★★★★
- QST-24
- 1 Days (7 Hours)
Description
Before any intervention by an external company on your site, it is obligatory to organize a joint inspection visit in order to analyze the risks of interference. A written prevention plan must then be formalized if the total number of working hours planned is at least 400 hours over 12 months, or if the work appears on the list of dangerous work. Beyond meeting this obligation, the implementation of a prevention plan guarantees you the anticipation and control of the risks of interference or coactivity linked to the performance of operations (provision of services, works. ..). This training gives you the keys to writing and implementing a relevant prevention plan.
Who is this training for ?
For whom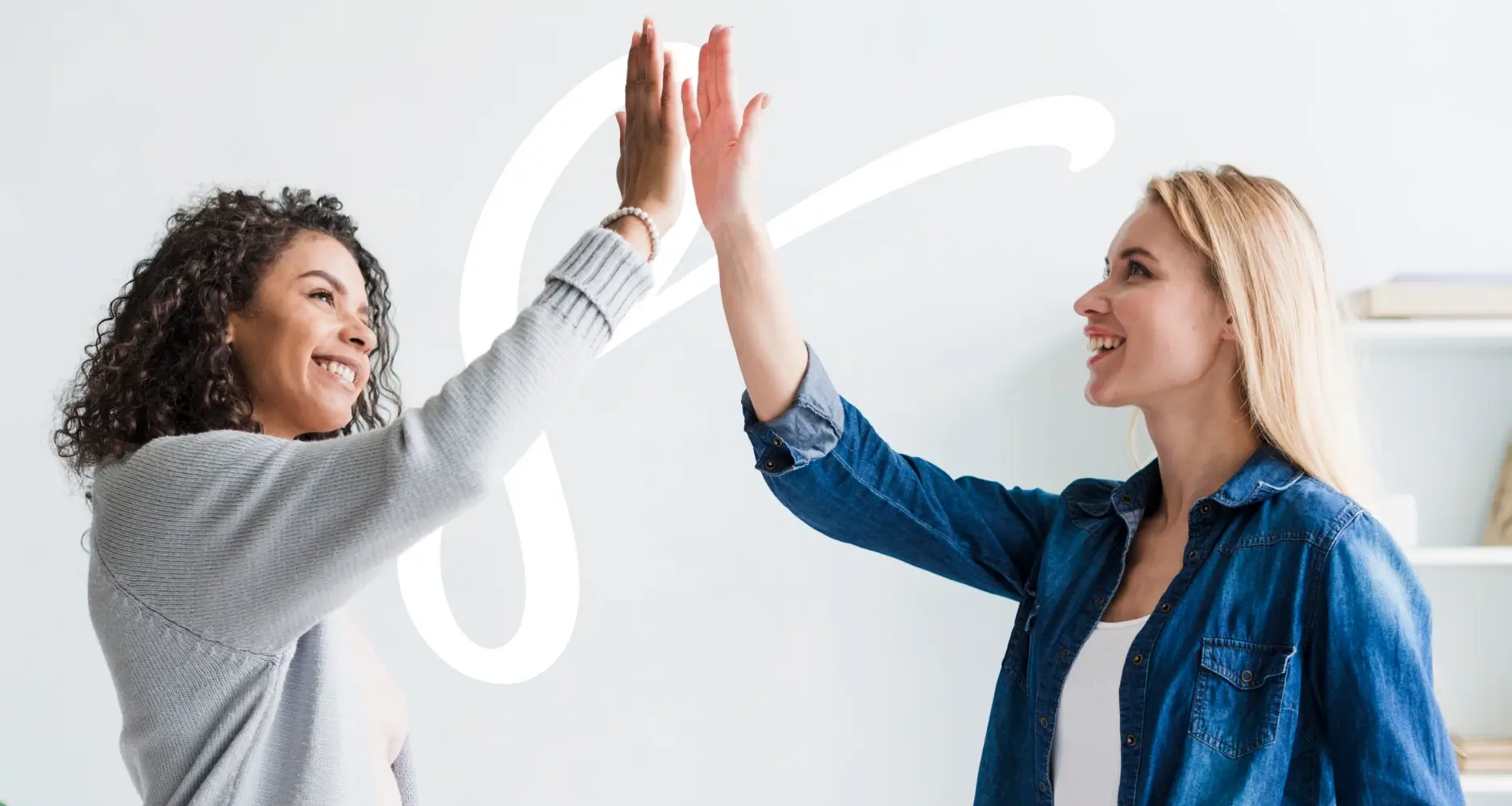
None.
Training objectives
Identify the legal obligations associated with the prevention plan.
Know how to develop and implement a prevention plan to guarantee control of risks linked to external companies.
89Training program
Before the face-to-face
- A self-diagnosis.
The regulatory dimension
- The scope associated with the prevention plan: in what specific cases should it be initiated?
- The obligations of companies: those carrying out the work, those hosting the work.
- What should a prevention plan contain; what are the essential sections and associated documents?
- Criminal and administrative responsibilities.
Write your prevention plan
- Communicate your prevention plan.
- Carry out the preliminary inspection in the field: the essential elements to collect and verify.
- Carry out the joint risk analysis , identify the risks associated with co-activities and those linked to the execution of the work.
- Formalize your risk analysis, associate the mandatory documents.
Ensure control of identified risks
- Implement and follow a relevant prevention plan to control risks.
- Drafting the safety protocol, loading and unloading of goods: order of 26/04/96.
- Control during the intervention of the external company.
- Obligations linked to employees of external companies.
- Update the risk analysis .
After face-to-face, implementation in a work situation
- A reinforcement program by email.
The Quality dashboard
★★★★★
- QST-25
- 2 Days (14 Hours)
Description
The implementation of quality indicators is one of the most important missions of the Quality function, because it allows the objective measurement of the effectiveness of the Quality management system and ensures the steering of the approach. This training day gives you the essential keys to designing and implementing the quality dashboard. It puts participants in a situation of creating and presenting indicators.
Who is this training for ?
For whom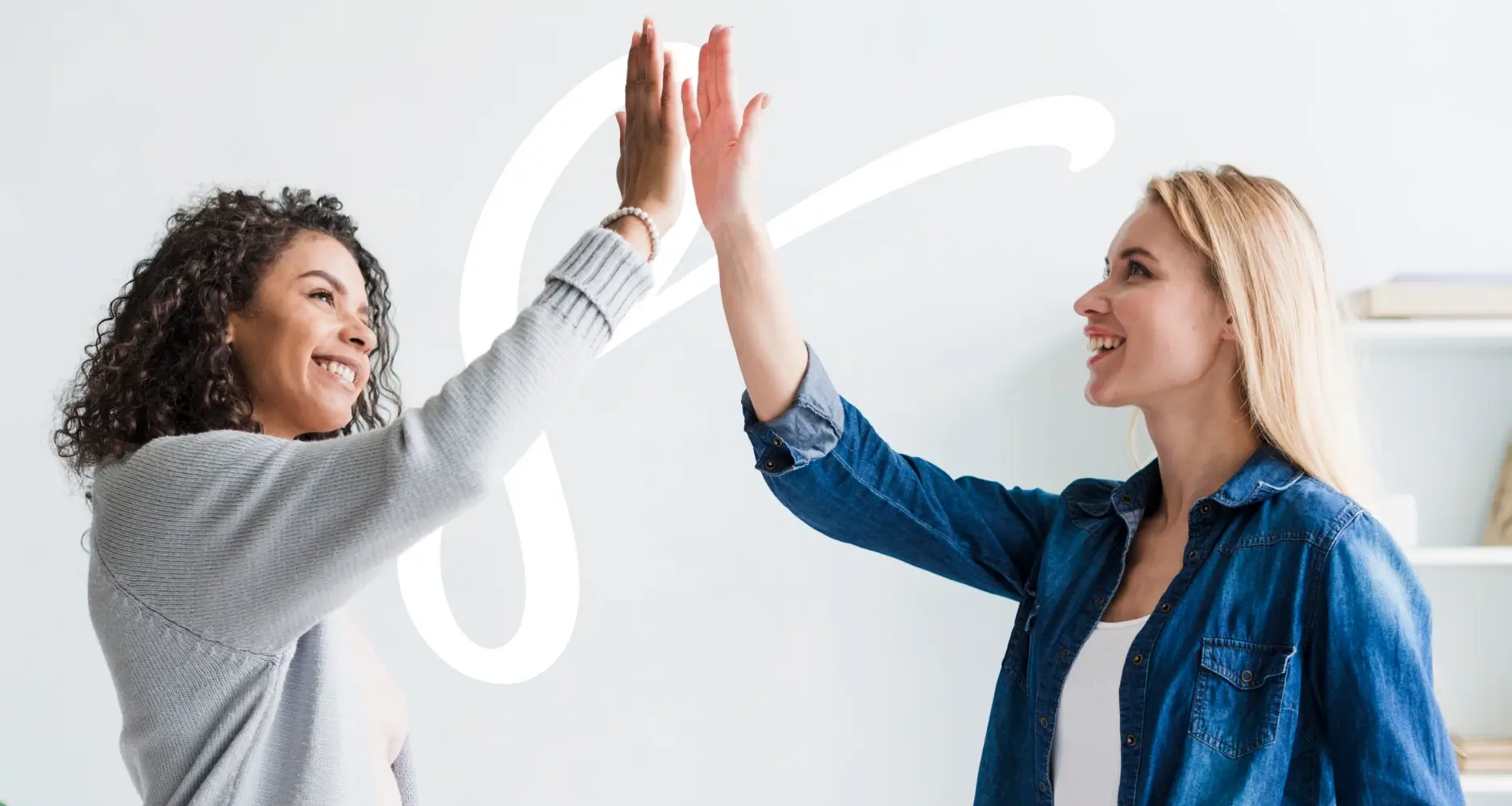
None
Training objectives
Identify the keys to choosing the right quality indicators.
Know how to format the indicators in a PDCA logic.
Use dashboards as a real management and animation tool.
92Training program
Before the face-to-face
- A self-diagnosis.
Understand the dashboard objectives
- Quality Why a measurement system? Elements and objectives of the quality dashboard: management, measurement, dialogue, delegation tool.
- PDCA demonstration.
Defining relevant quality indicators The characteristics of the 'good' indicator
- Quality.
- Distinguish between performance and management indicators.
- Choose your quality indicators on key axes: expected quality, achieved quality, perceived quality by customers, the axes of the quality policy.
- Define your indicator precisely (indicator grid).
4Identify the key indicators of quality approaches Evaluate the product or service: product demerit indicators, process indicators.
- Customer satisfaction indicators, the concept of NPS.
- Indicators linked to your quality policy.
- Indicators associated with non-quality costs.
Construct and format the indicators
- Go from global to specific.
- The graphic representations to use to demonstrate the implementation of PDCA (Plan, Do, Check, Act) in the company.
- The minimum information to be associated with indicators beyond the numbers.
Practice commenting on your quality dashboards Comment on an indicator: 3 minutes to take action or congratulate the results. Communicate your dashboards, periodically evaluate their relevance. After face-to-face, implementation in
- A tutorial to help you put the learnings of the training into practice.
- To find out more about remote activities To support you in your implementation: a 'Tutorial' video : Format a quality indicator.
Human and Organizational Factors (HOF) in QSSE
★★★★★
- QST-26
- 1 Days (7 Hours)
Description
Sometimes despite significant means to make activities more reliable (written and explained procedures, modification of processes, etc.), errors and accidents are repeated. We see this in the field: the organization designed to reduce the risk of work accidents, product or environmental non-conformities must integrate the human factor upstream, both individually and collectively. This training gives you the keys to strengthening the reliability of your Quality-Health/Safety-Environment management systems by deploying a real operational culture focused on prevention and continuous improvement.
Who is this training for ?
For whom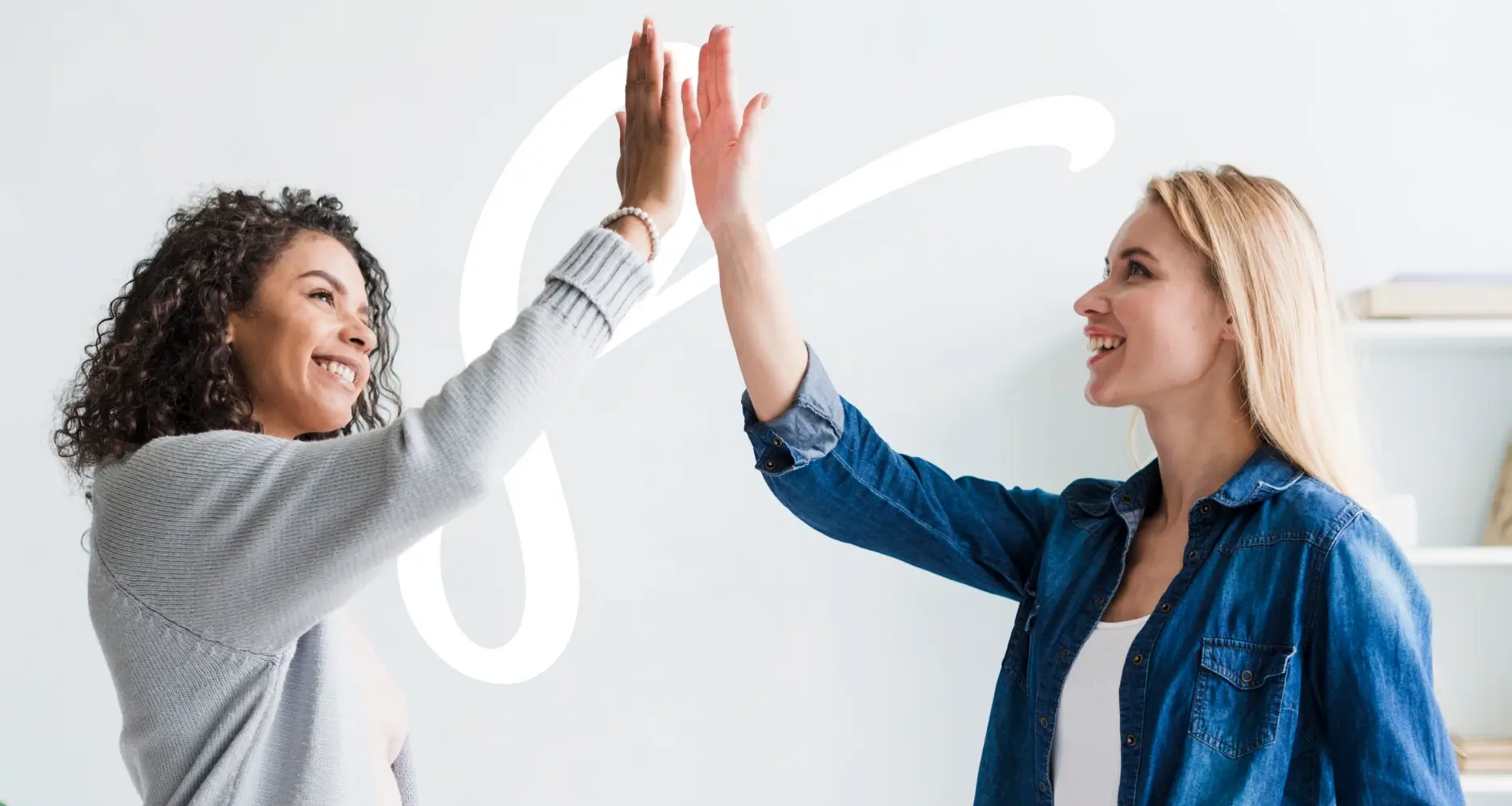
None
Training objectives
Understand the issues related to the behavior of individuals and teams.
Identify influential management methods.
Locate the keys to success to deploy a real QHSE culture in the field.
95Training program
Understand individual and collective modes of operation
- From beliefs to risk perceptions.
- Relations between identity, attitude and individual behavior.
- The modes of operation of the human brain (SRK, Rasmussen model) .
- Human capacities and limits.
- The operating modes of an organization: the production/prevention compromise.
- Impact of the type of management: autonomy and accountability.
3Dissecting the phenomenon of human error The human factor in accidents: cause or consequence?
- Key lessons linked to major past industrial and technological accidents.
- Are humans reliable? Where do our errors come from? Concept of active error, latent error.
- Stress and human reliability.
- Problems of coactivity.
- The Reason Model.
Organize and make QSSE activities reliable Evaluate and make real activity reliable: the difference between compliance with the prescribed and reality; accept the limitation of rules and procedures.
- Bird's pyramid.
- Manage by taking into account FOH: know how to observe: distinguish between field approaches (visit, audit, control), know how to react to findings of discrepancies, the QSSE equation: between compliance and proactivity; convincing: the ABC model.
- The key attitudes of the manager.
96Establish an operational QHSE culture
- Types of QHSE culture.
- Evaluate the reliability of the real QHSE management system.
- Know how to test the system in place.
- Engage in continuous improvement: indicators and feedback.
Health and safety risk assessment and the single document
★★★★★
- QST-28
- 2 Days (14 Hours)
Description
The occupational risk assessment (EvRP) makes it possible to identify the critical risks to which employees may be exposed at work. This is the basis of any prevention approach. This training allows you to evaluate and prioritize occupational health and safety (OHS) risks, including psycho-social risks, within your company. And beyond the observation and drafting of a single relevant document, it helps you structure your prevention program in a logic of continuous risk management.
Who is this training for ?
For whom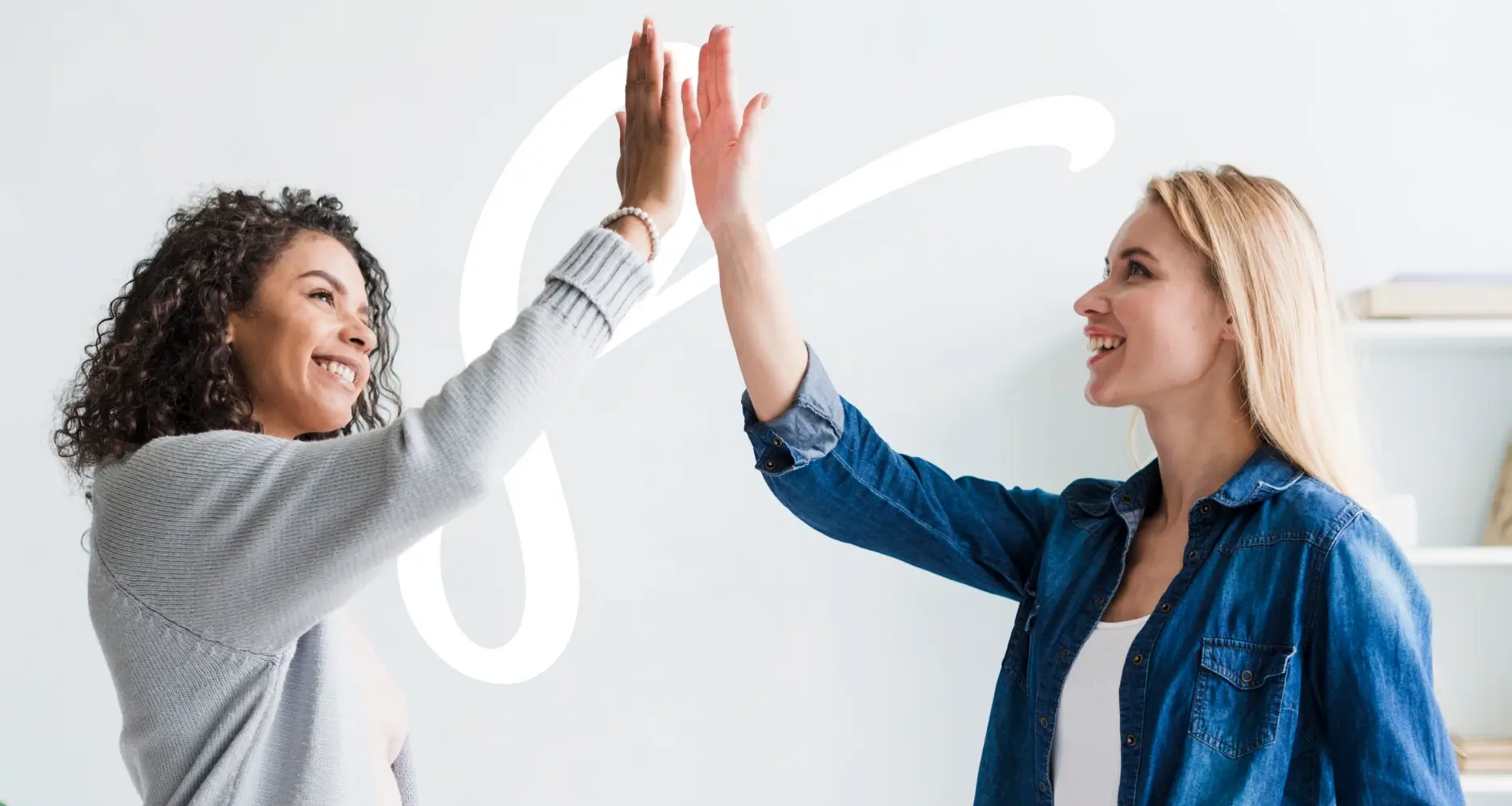
Training objectives
Construct your health and safety risk analysis and update your document
99Training program
Why an occupational risk assessment?
- Internal/external issues.
- The legal and regulatory context.
- Vocabulary: danger, risk, dangerous event, damage, notion of arduousness at work , the positions concerned.
Implement risk assessment
- Choose the scope of the study.
- Prepare the analysis upstream: collection of key data.
- Organize the working groups and the analysis /field observations.
- Identify the different dangers and risks.
- Estimate and prioritize gross risks: evaluation of the severity, frequency and/or probability of occurrence of the danger.
- Take into account the means of controlling existing risks.
- Carry out a summary map: classify the risks.
- Focus on particular cases: psychosocial risks, ATEX, assessment of arduousness, CP, co-activity...
Write your D.U and your prevention program
- Reduce the severity through protective actions.
- Reduce the probability of occurrence by acting on the root causes.
- Formalize the risk control plan: plan actions, clarify responsibilities.
- Write your single document (DU).
100Make the Single Document a management tool
- Monitor the decided actions and the results.
- Update the risk assessment through audits, safety visits, accidents and changes in activities.
- Share information with teams; lead prevention in the field.
Remote activities
- Three experts: ""Addictions" ; "Road risks" and "Psychosocial risks".
Manage by processes
★★★★★
- QST-29
- 2 Days (14 Hours)
Description
More and more companies are committing to process management. Promoting transversality and listening to the customer, this new approach will induce profound changes in terms of management and sharing of responsibilities. This training gives you the keys to starting this challenge by identifying the keys to building your process map.
Who is this training for ?
For whom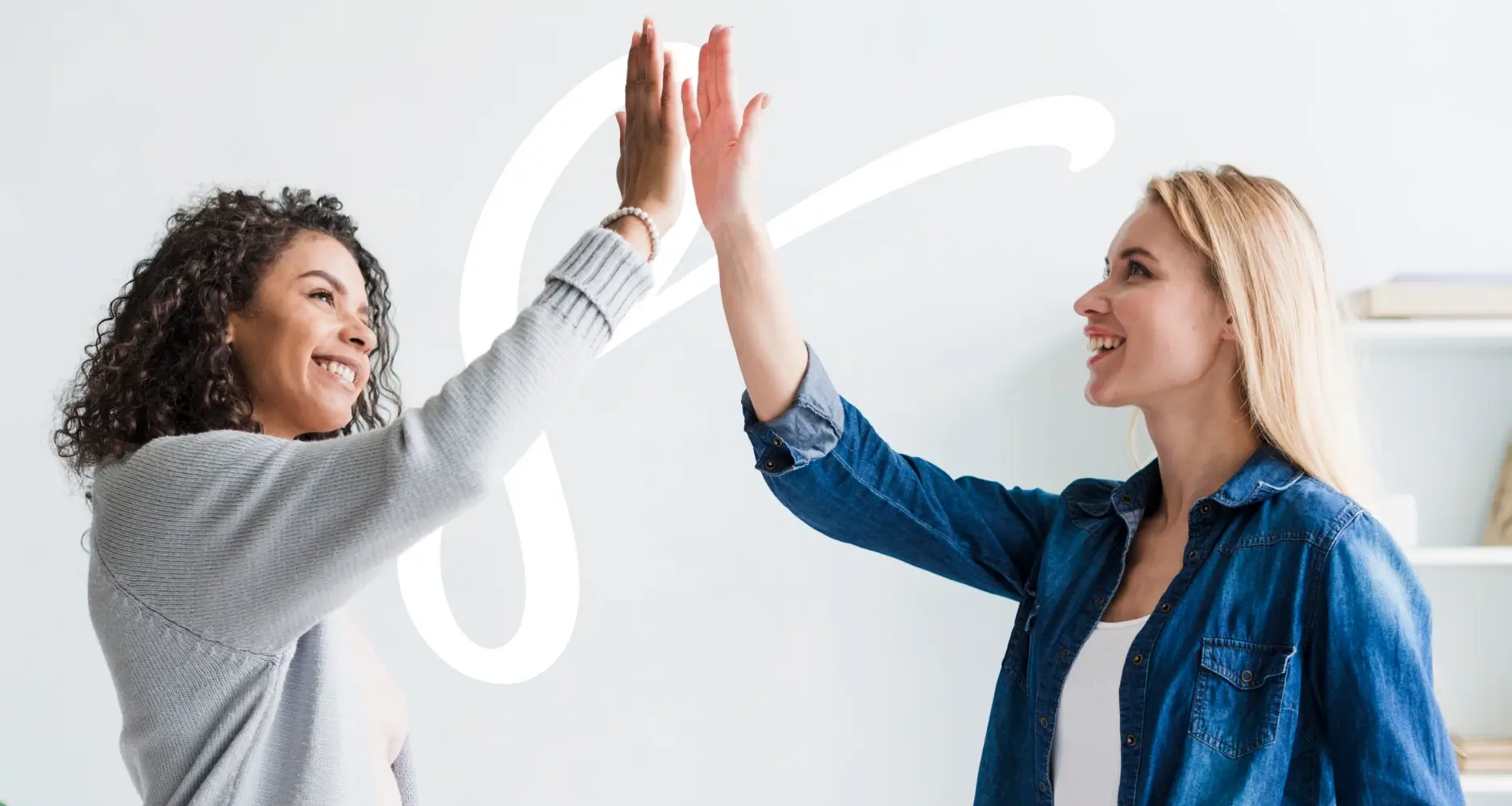
None
Training objectives
Understand the issues and principles of management through processes.
Acquire the method to identify the macro-processes of your company and construct the process map.
Identify the principles and conditions for success of transversal management.
103Training program
The essentials of the process approach The concept of process, the challenges of management by processes, its benefits, its limits.
- The choice of pilots and the notion of associated transversal management.
- From the identification of processes to management: the key stages, what this really changes in terms of management.
Build a business process map
- Understand the objective.
- Apply a structured method to identify business, support and managerial processes.
- Visually represent all processes: concept of mapping .
- FSA matrices (functions-strategy and expectations) to validate the mapping and identify strategic processes.
- Pitfalls to avoid.
- Presentation of business process mapping examples.
Managing through processes: the keys Describe the process, write process identity sheets. based on the purpose of the process, formulate the performance indicators. Evaluate and reduce risks associated with processes.
- Take stock of the process, initiate a logic of continuous quality improvement (PDCA: Plan-Do-Check-Act).
- Describe the strategic objectives by process using the contribution matrix.
- The process review; a formal assessment of the process activities.
- A measure of maturity in levels.
Measure your customer satisfaction, exploit their complaints
★★★★★
- QST-30
- 3 Days (21 Hours)
Description
To evaluate their quality performance, companies turn to their customers, the sole judges of the quality of their products or services. Thus, understanding customer expectations, measuring customer satisfaction, and dealing with their dissatisfaction, becomes an imperative for quality managers and customer service managers. Discover simple tools in this training that will help you revitalize your action around the voice of the customer, increase their loyalty rate and innovate intelligently!
Who is this training for ?
For whom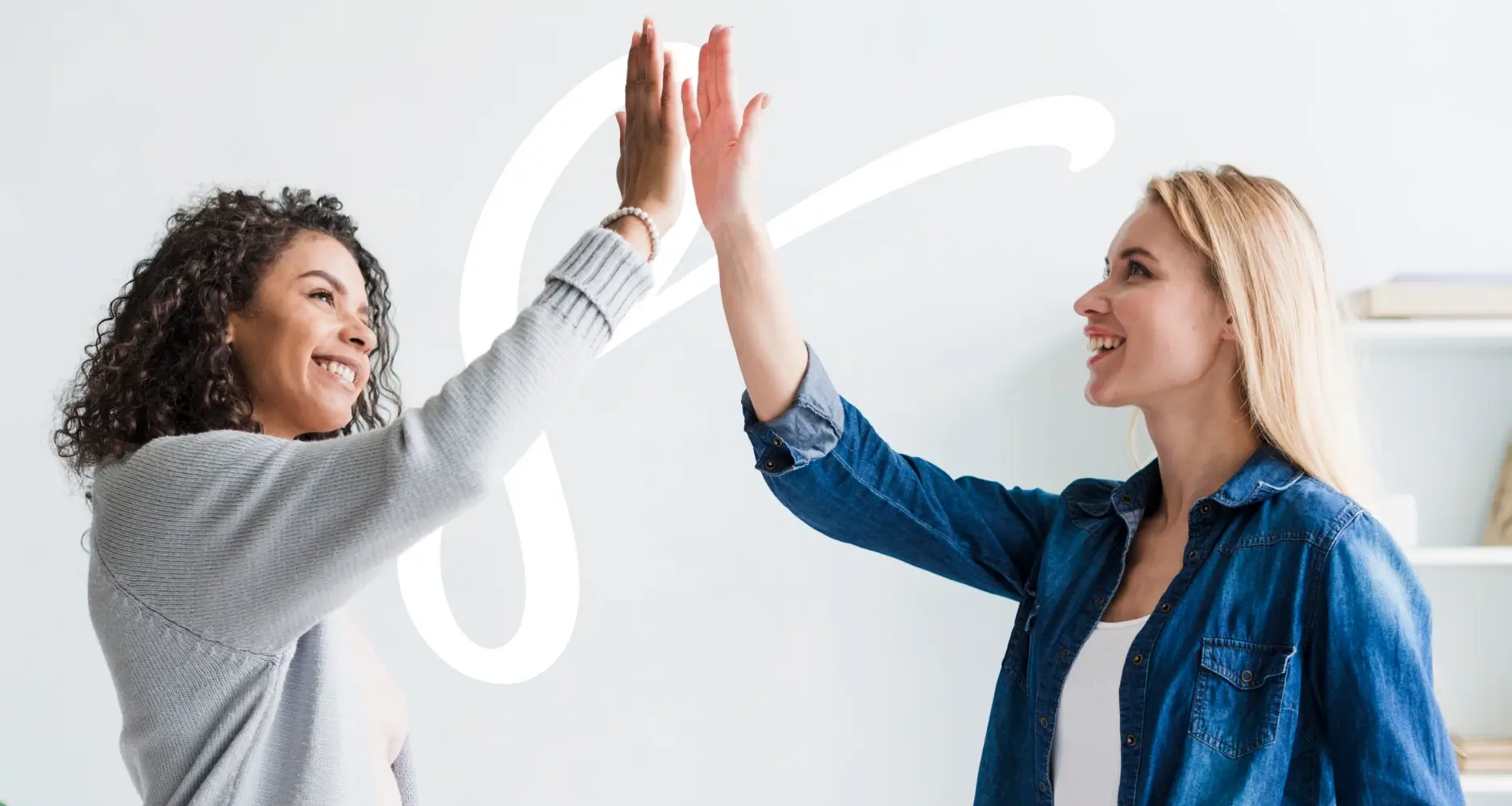
None.
Training objectives
Acquire tools to establish a diagram of customer needs and construct and use a satisfaction survey.
Process customer complaints effectively.
106Training program
To know how to listen...
- The role of the customer in the quality process.
- Listening to the customer upstream and downstream of the services.
Build a satisfaction survey
- Organize a qualitative study of customer needs face-to-face or in a focus group.
- Construct the customer expectations diagram.
- Qualify expectations by the Kano questionnaire.
- Build a satisfaction survey.
- Designing the questionnaire: measuring perceived quality.
- Working in relation to the competition.
- Digital solutions.
Use a satisfaction survey
- Format the results of the survey: construction of the company's performance grid (mapping). Identify priority areas for progress.
- Calculate the NPS (Net Promoter Score) and the CES (Customer Effort Service).
- Know how to evaluate the statistical precision of the results.
Implement complaints processing
- Define what a complaint is.
- Ensure and centralize complaints, encourage your customers to express them. React urgently: security actions.
- The two degrees of response to customers: curative action to ensure a return to customer satisfaction and corrective action to avoid renewal a posteriori.
- The formalization of the treatment.
Remote activities
- Three e-learning modules "Problem-solving tools and methods. Go. A","Problem solving tools and methods. Go. B" and "You and your client: objective listening".
Measure your non-quality costs
★★★★★
- QST-31
- 2 Days (14 Hours)
Description
Beyond ISO 9001 certification, the quality approach can contribute in a very concrete way to the profitability of the company. Measuring and reducing non-quality costs and reducing production costs become real levers for action. How to demonstrate the profitability of a quality management system? How to convince management of the financial performance of a quality department? How to think about numbers beyond quality indicators? This training gives you the keys...
Who is this training for ?
For whom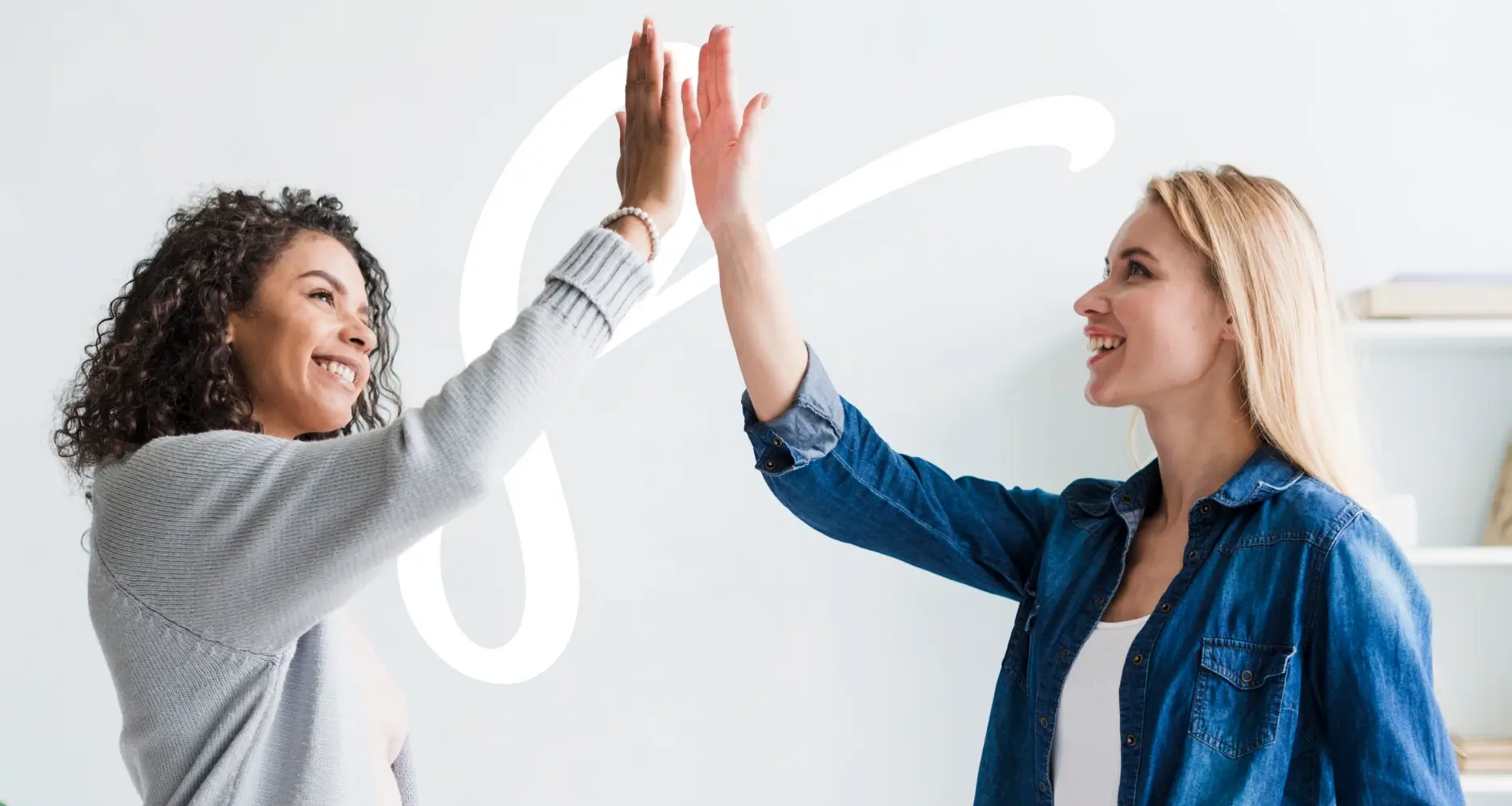
- This training requires knowledge of the principles of a quality management system.
Training objectives
Understand the economic dimension of quality.
Identify non-quality cost measures.
Adapt measurement and action methods to influence the profitability of the company.
109Training program
Before the face-to-face
- A self-diagnosis.
Quality economic levers
- Know the financial vocabulary of management.
- Adopt its language to be more credible.
- The economic challenges in which quality participates.
- Action levers to reduce production costs.
The cost of obtaining quality (C.O.Q)
- Calculate internal and external non-quality costs (CNQ).
- Calculate control and prevention costs (Quality costs: QC).
- Evaluate the COQ . Its 4 sections.
- Reduce COQ while guaranteeing customer safety.
- Identify courses of action to optimize the company's margin, measure efficiency.
Reason return on investment
- Adopt an investment logic when developing action plans, calculate the cost of the proposed solution, deduce the potential gains.
- Develop your information sheet corrective action to adhere to this logic.
Go further
- Reason the costs of acquiring and retaining customers.
- Know how to argue your selling price.
After face-to-face, implementation in a work situation
- A reinforcement program by email.
Advanced statistical methods
★★★★★
- QST-32
- 2 Days (14 Hours)
Description
Statistics are essential tools in many sectors of the company to exploit numerical data and compare results. They are used to model a phenomenon, validate the relevance of differences in results between them, predict, make estimates in the future, understand the relationships between factors. This training gives you the keys and statistical tools to know how to process data by assessing the associated risks of errors.
Who is this training for ?
For whom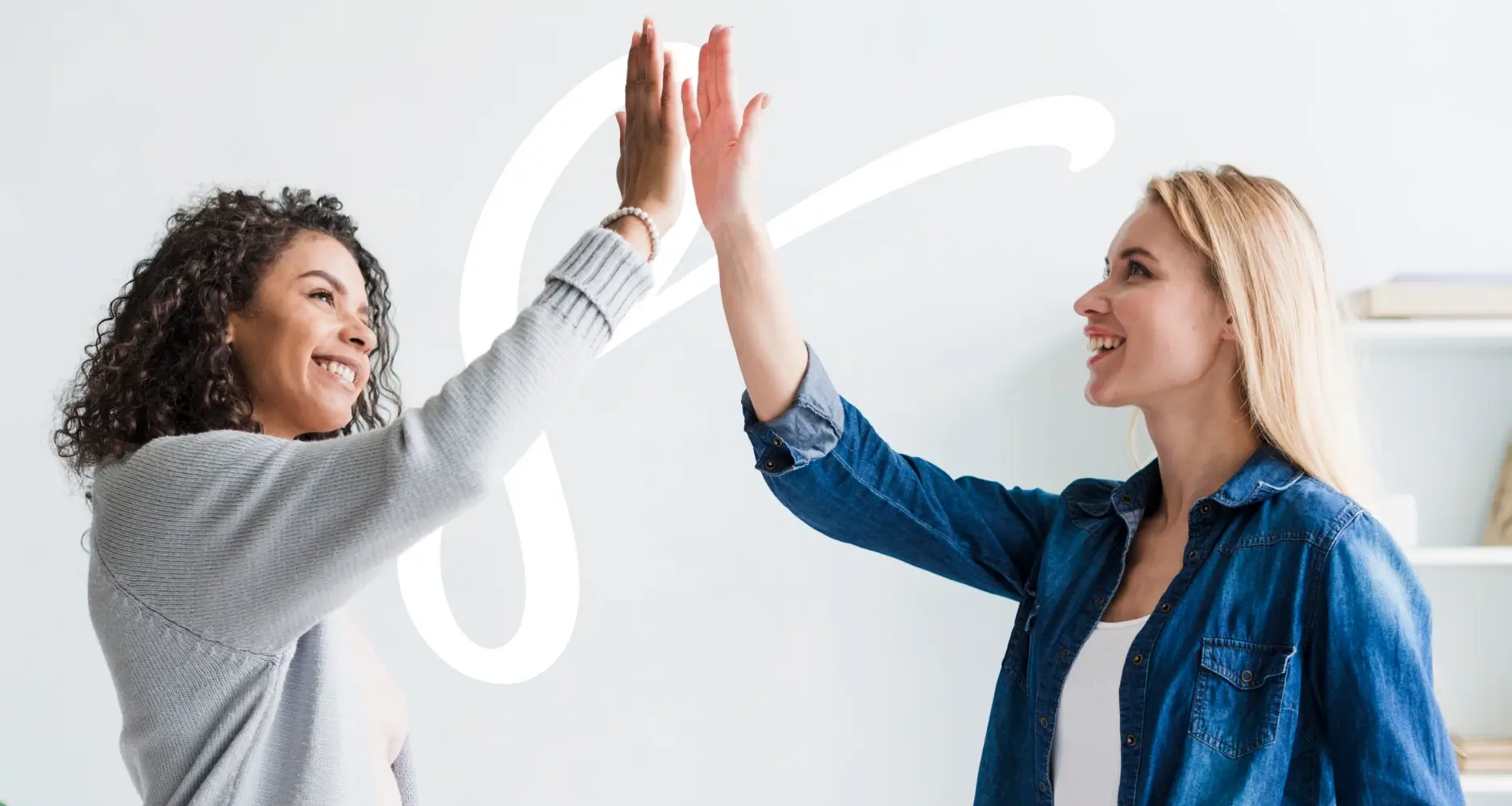
None
Training objectives
Identify and practice statistical tools allowing estimates and comparisons of numerical data to be made.
Identify the relationships between two factors. Understand the principle of forecasting.
112Training program
Lay the foundations for statistical analysis
- Collect and prepare statistical data.
- Choose the right statistical method based on the nature of the data and the desired result.
- Install the statistical data utility analysis in Excel or the XLTSTAT free add-in.
Estimate results and know how to evaluate the associated precision
- Estimate a mean or proportion by the confidence interval.
- Evaluate the precision of the result, define the minimum sample size.
- Define a representative sample and apply an adjustment.
Compare numerical results with each other
- Comparison of means and proportions.
- Use hypothesis tests (Chi Square, Student, Fisher).
- Detect influential factors through analysis of vairiance (ANOVA with one or more factors).
- The risks to avoid.
Look for the relationship between several factors
- Measure the relationship between several variables.
- Calculate the correlation matrix and plot the correlogram.
- Model a numerical variable by multiple regression.
Forecast data into the future Detect and extend a trend over time. Identify seasonal phenomena.
- Predict exponential smoothing and interpret the prediction interval.
MSP/SPC (Statistical Process Control): aiming for six sigma
★★★★★
- QST-33
- 3 Days (21 Hours)
Description
MSP or SPC is nowadays a proven preventive method which makes it possible to anticipate the appearance of non-compliant products in production for large series. This method, widely used within the framework of 'six sigma', is based on 2 fundamental approaches developed in this training: the calculation of the capabilities of the means of production; monitoring and controlling industrial processes using control cards which detect process deviations.
Who is this training for ?
For whom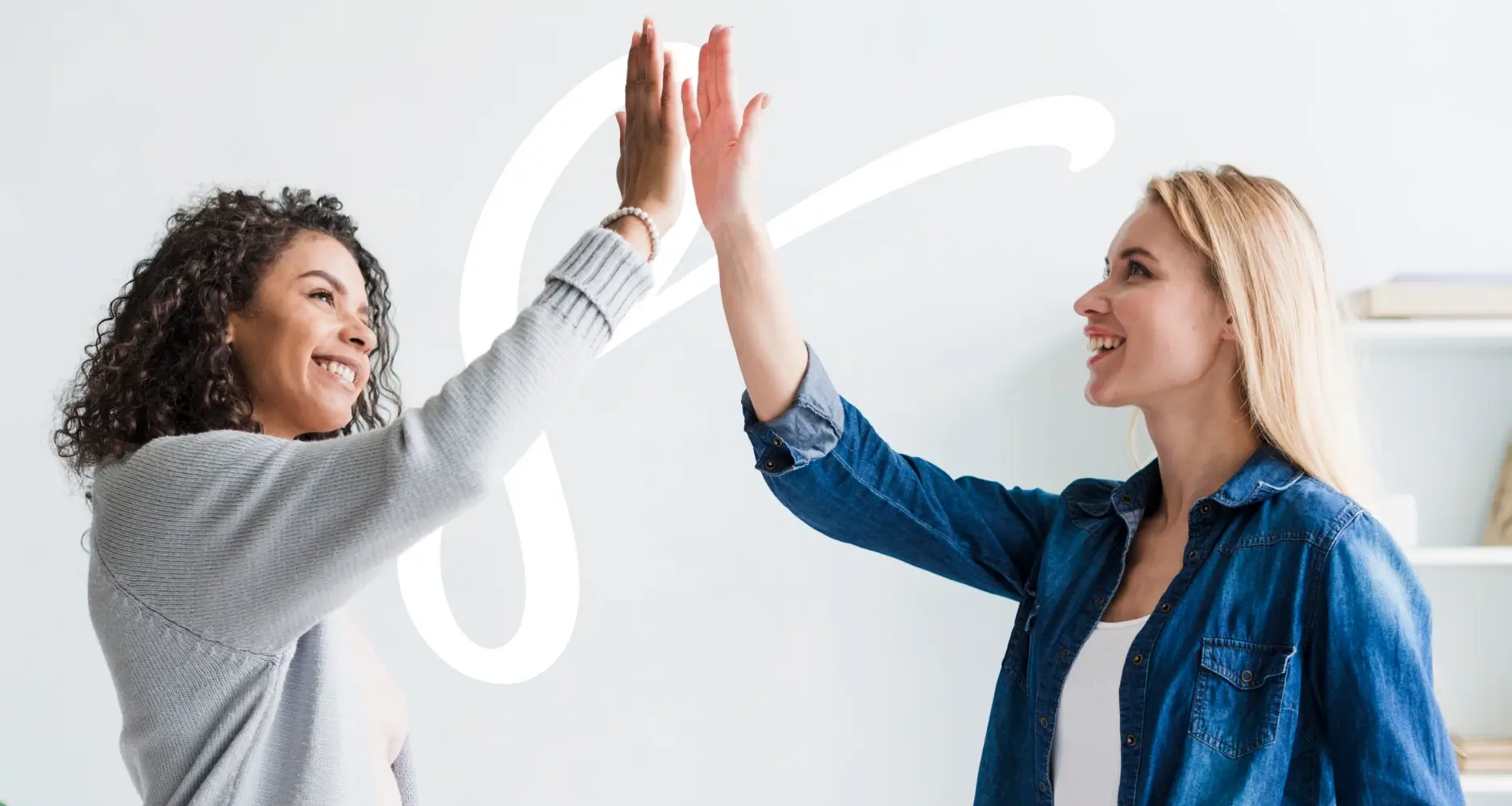
- It is recommended to have knowledge of statistical basics or to have followed training Training objectives
Implement the different stages of an MSP approach.
114
Build control charts and know how to use them.
115Training program
MSP in an improvement process
- Culture changes at the origin of MSP: transition from % to ppm; the logic of prevention; link with six sigma.
- Principles of MSP.
- Associated statistical concepts: the normal law, centering and dispersion.
Step 1: Organize your MSP project
- Choose the process, the product and the parameters to follow.
- Identify the phases of the process, the conditions for success, create your project team.
Step 2: Measure the performance of your process
- Check the normality of production.
- Calculate the machine and process "capabilities": Cp, Cpk, Cm, Cmk.
Step 3: Set up a management system
- Build your control charts: Calculation of control and monitoring limits: control charts (average/standard deviation).
- Case of small series.
- Management using control cards: read the cards, spot trends, identify random and assignable causes; define management rules, use a logbook, trigger improvement actions.
- Control charts with attributes (p, np, c, u) and individual values.
- Rely on self-control.
Step 4: Improve the MSP approach
- Audit the system, make assessments, monitor improvements. Lead and communicate.
- Recalculate the control limits if necessary.
Process driver
★★★★★
- QST-34
- 2 Days (14 Hours)
Description
The process approach developed in the ISO 9001 standard promotes the decompartmentalization of the company and the deployment of the Quality strategy. This approach leads to an increased role and responsibilities for 'process pilot' managers. In this training, they will discover how to become real contributors to the Quality system and the performance of their company by effectively managing their process in a logic of risk management and continuous improvement.
Who is this training for ?
For whom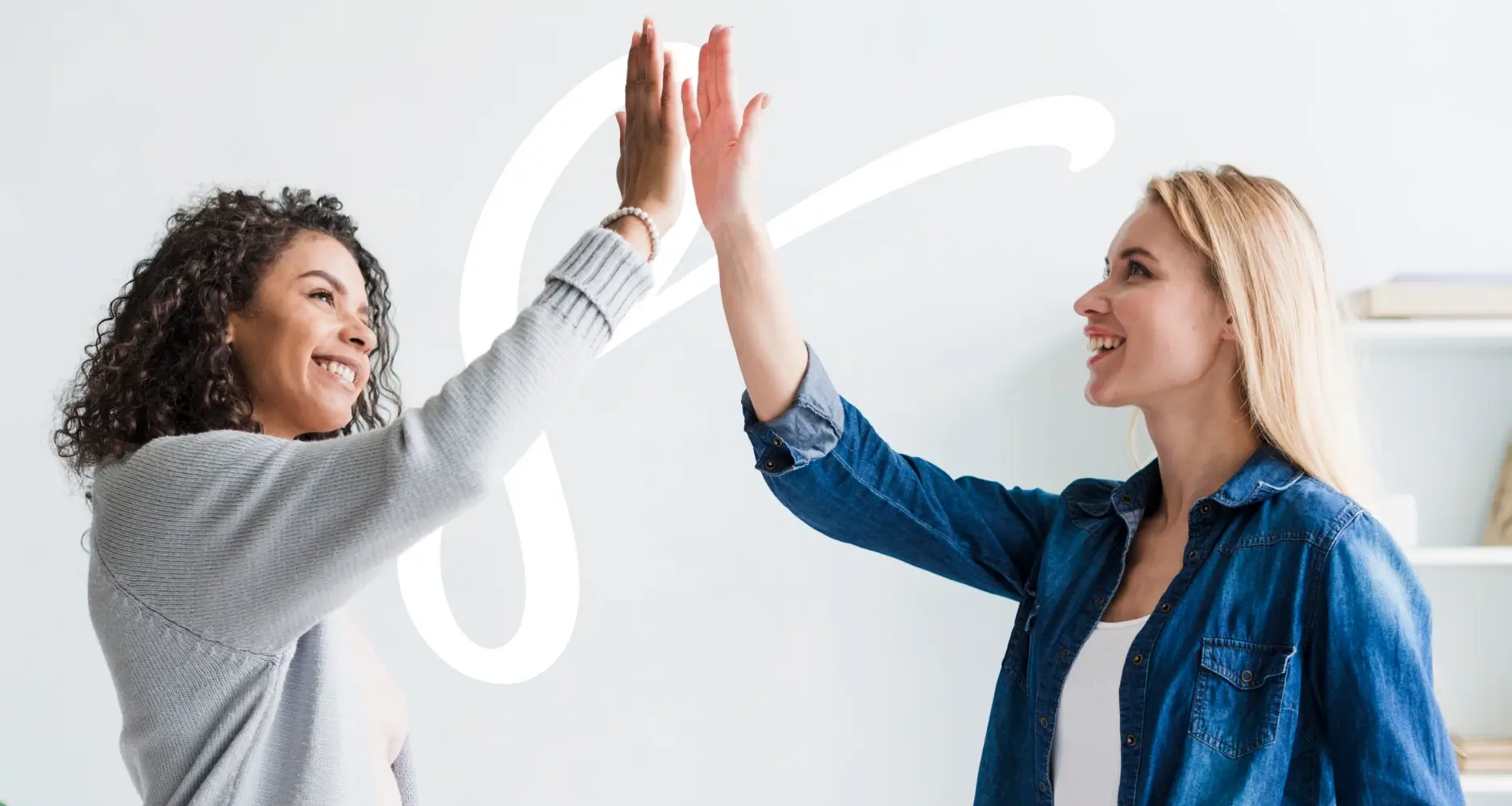
None.
Training objectives
Identify the missions and roles of the process manager. Understand the process approach, principles and interests.
Acquire the tools to effectively describe and manage a process.
118Training program
The process approach to decompartmentalize the company
- The principles of the process approach.
- The requirements of the ISO 00 V0 standard.
- Process mapping.
Describe and control the progress of a process by reasoning about risk
- Describe a process: aim for what is necessary, identify the characteristics of a process, make links with existing procedures and operating methods, represent processes graphically.
- The information sheet process identity: what sections it must contain.
- Identify and reduce the related risks.
- Implement appropriate monitoring actions to control non-compliance. conformities.
Manage and improve a process
- Measure the performance of the process from a 'quality-cost-time' perspective.
- Differentiate between performance and monitoring indicators.
- Take stock of the process, set progress objectives, formalize your action plan.
- Prepare and organize process reviews.
- Know how to identify opportunities.
Responsibilities of the process manager
- Example of mission sheet.
- Define the pilot's contributions and the expected results.
- Know how to communicate, lead, inspire people to act.
Remote activities
- Two videos "Tutorial: Describing a quality process" ; "Tutorial: Building support for your process review".
Perform system and/or process quality audit
★★★★★
- QST-36
- 3 Days (21 Hours)
Description
Quality audit is an essential tool for maintaining quality within companies. Internally, it is a source of progress and guarantor of the effectiveness of the Quality system. Externally, it allows you to evaluate, select your suppliers and create a lasting and effective relationship with them. During these 3 days of training, discover and practice the quality audit method, simple and rigorous, as well as all the attitudes that make 'a good auditor', listening to those audited and initiating progress actions. You are therefore truly operational when you return to work.
Who is this training for ?
For whom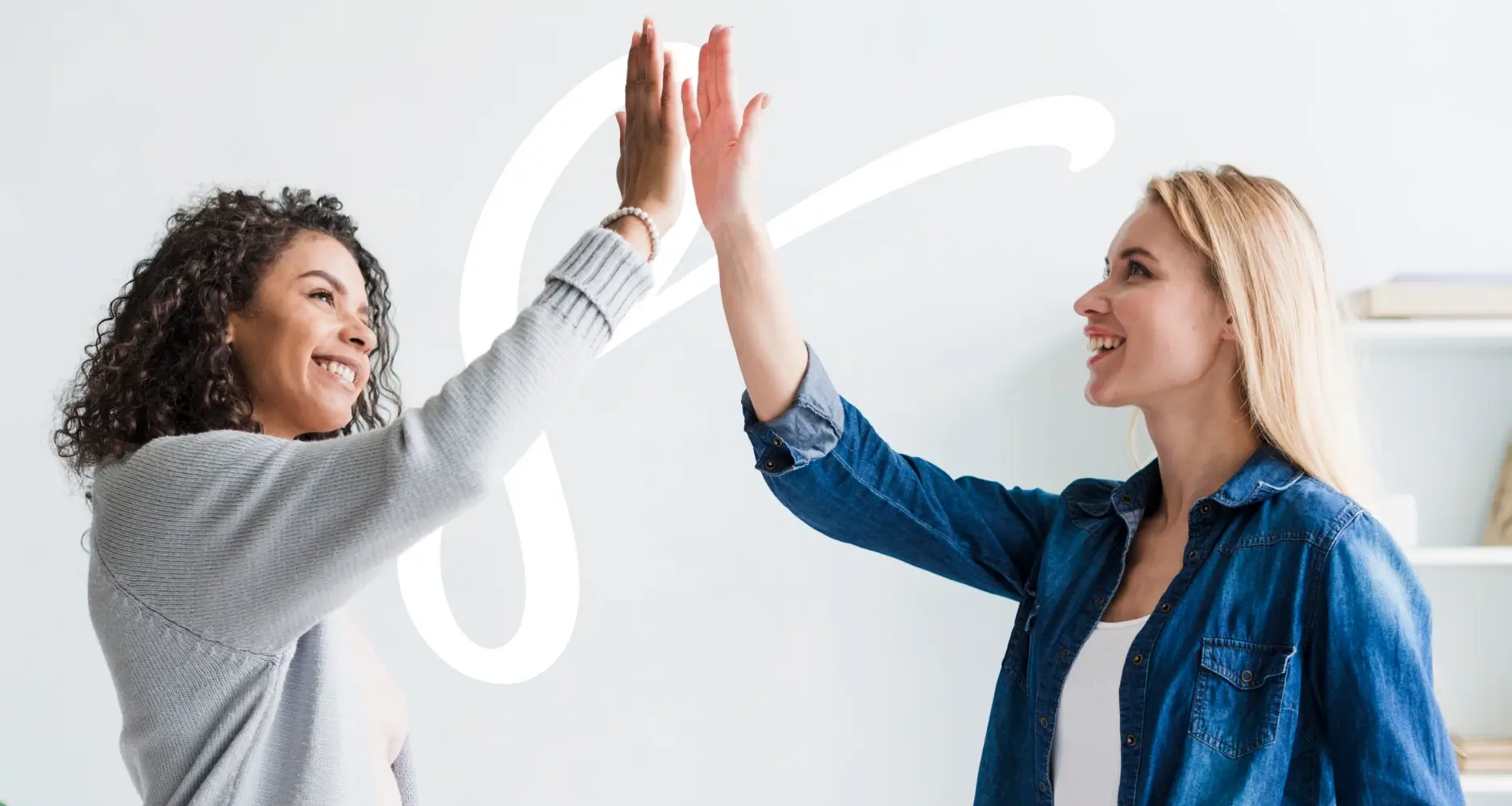
- Knowledge of the principles of quality and the reference system used (ISO 9001 or other), on the basis of which the audit will be carried out, is recommended. You can follow the day in advance: "The fundamentals of quality and ISO 9001" (ref. 8262).
Training objectives
Acquire the method and tools to effectively carry out Quality audits (system and processes), internal or external.
Assimilate the behavioral attitudes which promote the success of the audit.
121Training program
Before the face-to-face
- A self-diagnosis.
Principles and issues of quality audit
- Reminder of the principles of management and quality assurance.
- Standardized definition of audit. The issues: findings and progress.
- The different types of 'audit: system and process. The specificities of the process audit.
- The internal audit program, the audit procedure.
Preparing for the audit visit: practical case
- Build your audit plan.
- Build the team of quality auditors.
- Gather and study the reference documents (ISO 9001 standard or other framework and the documents of the auditees: quality manual, process descriptive sheets, procedures, etc.).
- Develop an audit questionnaire based on the ISO 9001 standard (or other standard): checklist of points to check.
- Prepare your interview guide (open questions).
- List the evidence to collect and observations to make.
- Scenario Practical exercise of audit preparation based on a case study (analysis and study of documents, construction of audit questionnaire)
122Practice the quality audit visit (simulation)
- Structure a positive relationship with the auditees: make them want to collaborate; be neutral; listen without interpreting; know how to avoid conflicts.
- Lead the opening meeting.
- Master the questioning, follow up, adapt to the auditees, facilitate exchanges with open questions, reformulate to ensure understanding.
- Obtain concrete answers: collect and analyze documents from the audited, observe in the field.
- Take notes as necessary.
- Prepare the audit summary, communicate the first conclusions during the closing meeting: note the points strong, prioritize and formulate the deviations observed (non-conformities or remarks); validate the conclusions with the auditees.
- Scenario Simulation of audit interviews in a case study: observation of techniques and attitudes of the listener.
Manage the post-audit visit (simulation)
- Write the audit report by taking up the conclusions of the closing meeting. Reason added value for the company and its customers.
- Engage the auditees: convince, obtain an audit plan 'action schedule, immediate curative reasoning then medium-term corrective Measure progress.
- Scenario Simulation of audit closing meeting. Writing an audit report.
After face-to-face - Implementation in a work situation
- Available online: reusable documents for your next audits (process and system audit questionnaire: reports, guide, blank schedule, etc.).
- Support program by email: "one challenge per week for 7 weeks".
- Videos to rediscover the auditor's good reflexes: "Succeed in your audit interviews"; by adopting the right attitudes" and "Formulating a deviation at the end of the audit".
- A training module: "Practice active listening".
Sustainably reduce its environmental impacts
★★★★★
- QST-37
- 2 Days (14 Hours)
Description
As part of their commitment to sustainable development, responsible companies have chosen to reduce their environmental impacts by working on ambitious challenges such as biodiversity, energy efficiency, eco-design, and the circular economy. Discover in this new training the issues and principles of these methods which will effectively complement your ISO 14001 environmental management system.
Who is this training for ?
For whom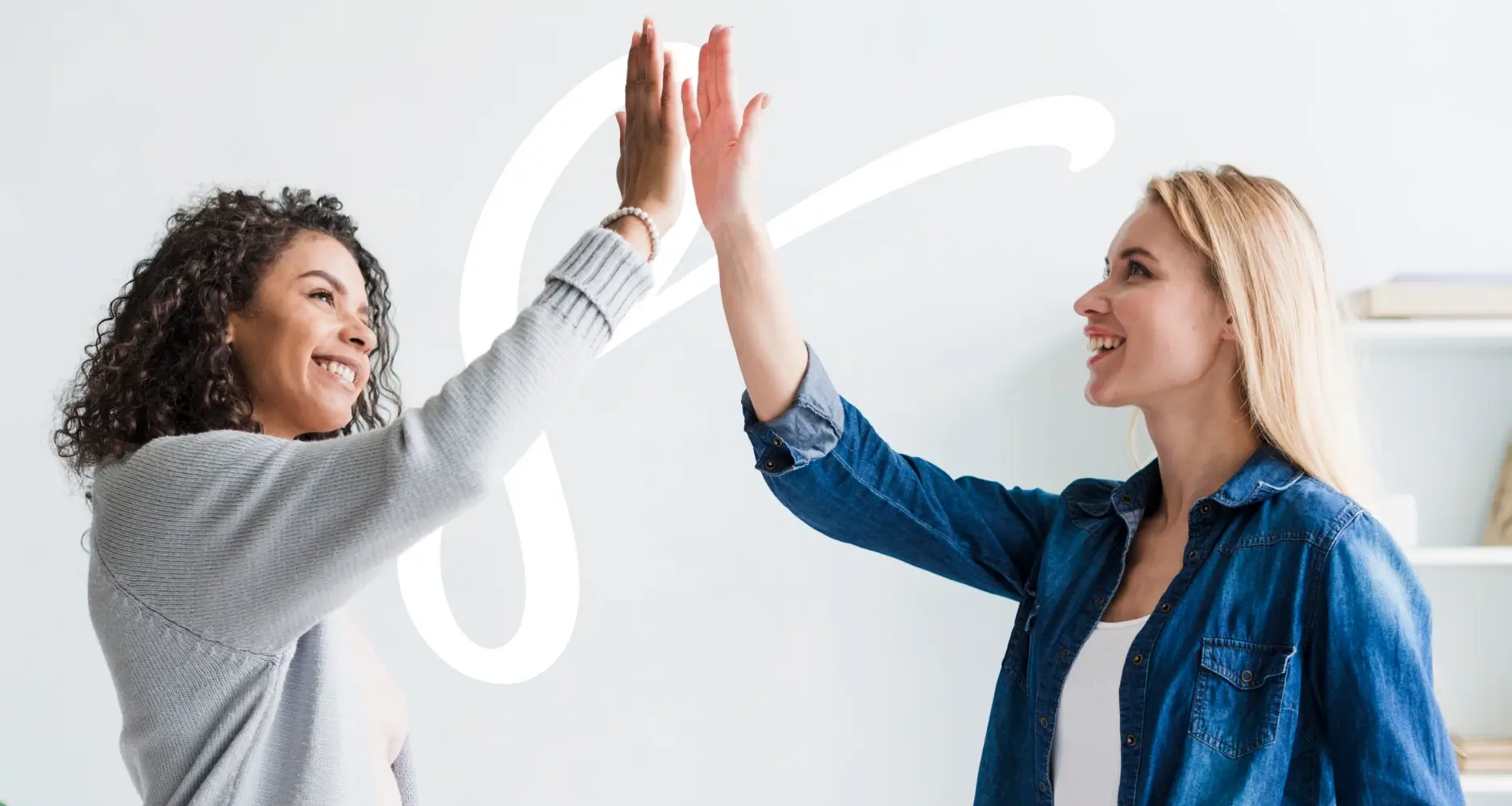
- This training requires knowing the fundamentals of an environmental management system (continuation of our course 4524 "Practical guide to ISO 14001" or other).
Training objectives
Undertake a structured approach to reduce its environmental impacts.
Identify the key points of biodiversity, eco-design, energy efficiency, the circular economy..
125Training program
Before the face-to-face
- A self-diagnosis.
Environmental issues of sustainable development
- Sustainable development and CSR (Corporate Social Responsibility).
- Main standards, ISO 26000, complementarity with ISO 14001.
Act for the climate
- Context and issues, the urgency to act for the climate.
- Conventions, international framework agreements.
- European orientations and territorial variations.
- Regulatory compliance and anticipation.
- Main courses of action.
Reduce your carbon footprint, think about the life cycle
- Concept of carbon footprint and greenhouse gas balance (BEGES).
- The mobility plan: from obligation to opportunity.
- Read and use a BEGES, look for avenues for progress.
- Notion of product life cycle.
- Principle of eco-design.
- Engage in the energy transition: energy balance, ISO 50001, concept of energy policy, action plan.
The fundamentals of the circular economy
- Understand the principles of the circular economy.
- The actors of the circular economy: the community, businesses…..
126Biodiversity and business
- Company-natural environment and biodiversity interactions.
- Regulatory framework, key players.
- Integrate biodiversity into its environmental policy.
After face-to-face - Implementation in a work situation
- A reinforcement program by email.
Environmental regulations - Level 1
★★★★★
- QST-38
- 2 Days (14 Hours)
Description
Environmental protection is an obligation for the company. To do this, those responsible must know the texts concerning it, know how to apply them and communicate effectively with all those involved in environmental protection. This 'Environmental Regulation - Level 1' training gives you the keys to the regulations applicable to businesses.
Who is this training for ?
For whom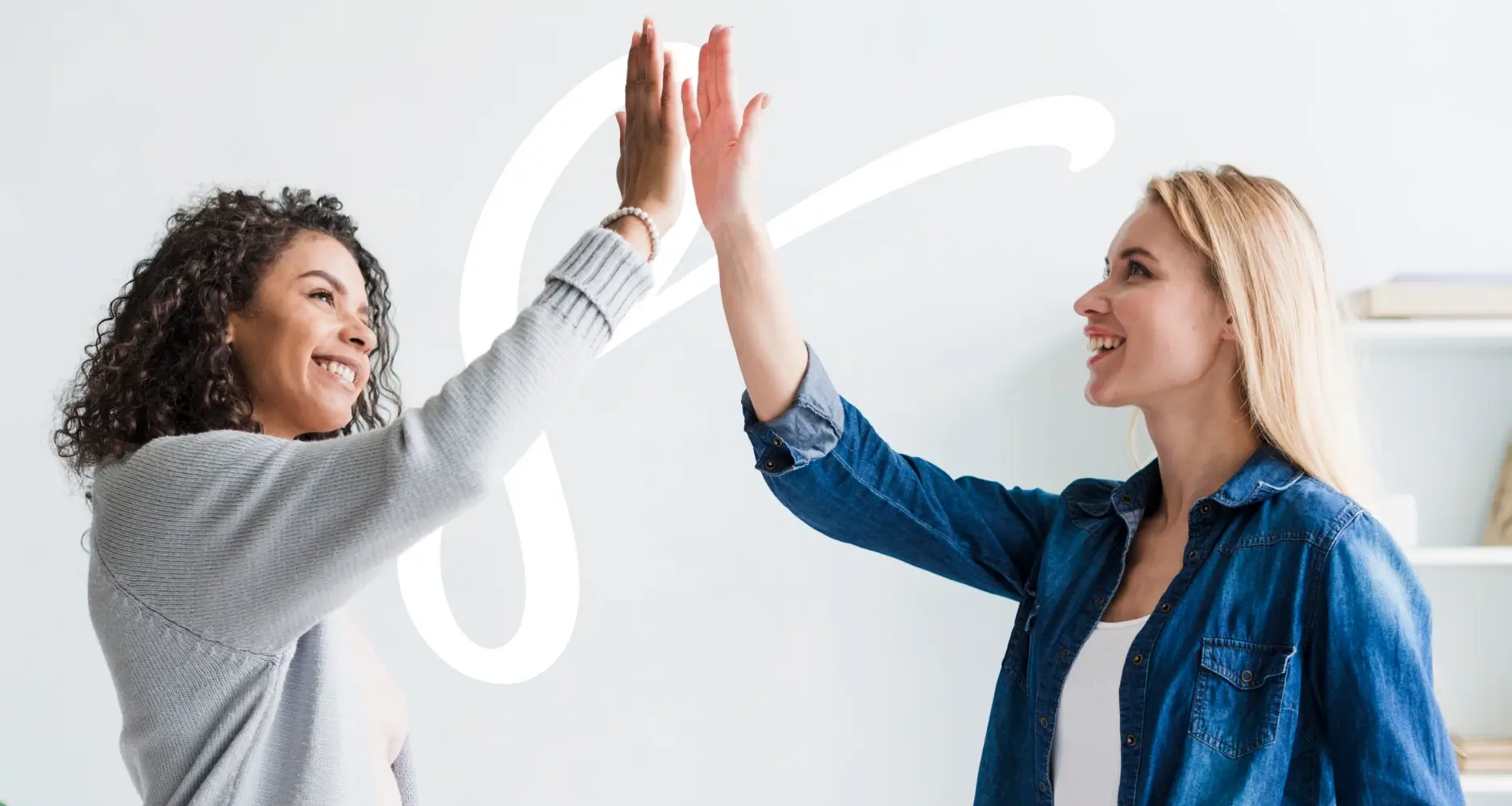
No prerequisites.
Training objectives
Discover the key texts of environmental regulations.
Situate your business with regard to the relevant environmental regulations.
129Training program
Before the face-to-face
- A self-diagnosis.
The legislative and regulatory framework
- The hierarchy of rules, from European texts to prefectural decrees.
- Issues of environmental responsibility, regulatory monitoring.
- Environmental law and other texts applicable: the environmental code, the major regulated themes, cross-cutting regulatory subjects: chemicals, Reach/CLP, fire-explosion...
ICPE regulations
- Practical consequences at start-up, during operation, in the event of cessation of activity.
- Subject to the different ICPE regimes (declaration, registration, authorization).
- ICPE and town planning rules.
- Cerfa forms.
Other key texts
- Water laws.
- Obligations and regulatory framework for waste management.
- Impact studies (nomenclature), environmental assessment, case examination per case.
- The biodiversity law, carbon footprint, BEGES, energy audit, environmental reporting.
After face-to-face - Implementation in a work situation
- A strengthening program: "one challenge per week for 7 weeks".
Environmental regulations - Level 2
★★★★★
- QST-39
- 2 Days (14 Hours)
Description
Environmental regulations continue to evolve and expand. This training, the content of which is updated regularly, allows you to deepen your knowledge to better meet regulatory requirements and anticipate future developments.
Who is this training for ?
For whom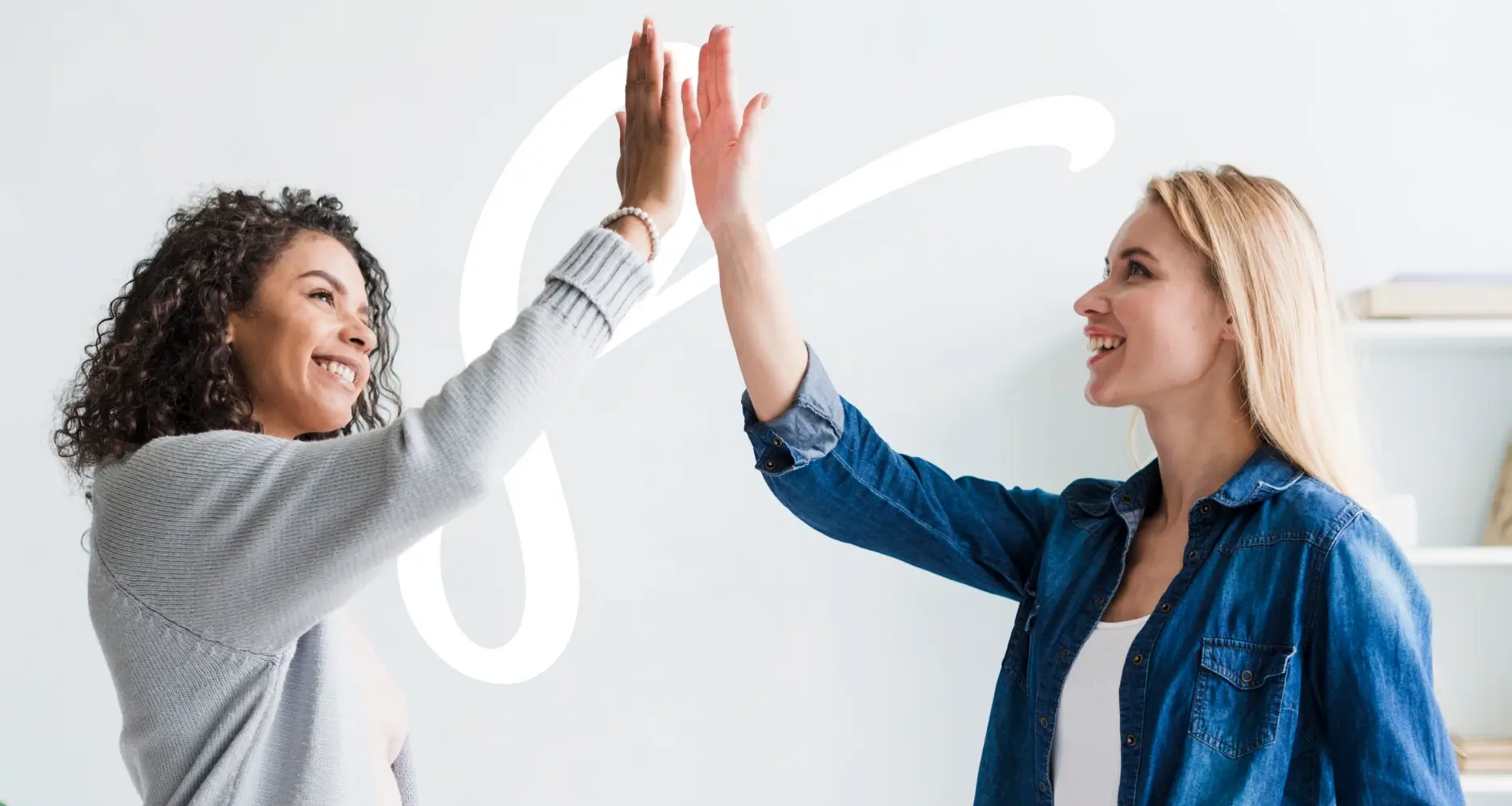
None
Training objectives
Deepen your regulatory knowledge regarding the management of the environmental aspects of industrial companies (during the start-up of a production unit, its operation and, where applicable, the cessation of activity, etc.).
Identify how to respond effectively regulatory constraints.
Know recent developments and identify foreseeable developments.
132Training program
Reminder of the fundamentals
- Environmental Code, ICPE regulations.
Respond to regulatory constraints For all establishments: create specific regulatory monitoring; sanitation (separative system, hydrocarbon separator); waste management (prioritization of treatment methods, waste management
- Biodiversity.
- For classified activities: constitution of the declaration file; anticipate the mandatory technical requirements; constitution of a registration file: determine your project to secure compliance, anticipate ¨additional potential studies (impacts, NATURA 000 incidence); request for authorization: obtain your project certificate, anticipate the updating of studies, check whether the Séveso and IED directives are applicable, health risk assessment, lightning, seismic, financial guarantees; procedure for cessation of activity: determination of the future use of the site, security, soil studies and rehabilitation report.
2Key recent developments
- For all establishments: town planning rules and management of natural spaces.
- For classified activities: single environmental authorization.
Solve problems in the field
★★★★★
- QST-40
- 2 Days (14 Hours)
Description
Making progress, involving staff, and driving continuous progress on a daily basis in the field are challenges that successful industrial or service companies set themselves. These continuous improvement approaches induce simplicity and rigor in the chosen problem solving method. This training allows you to discover the right reflexes to acquire to quickly resolve problems by involving teams in the QRQC (Quick Response Quality Control) spirit.
Who is this training for ?
For whom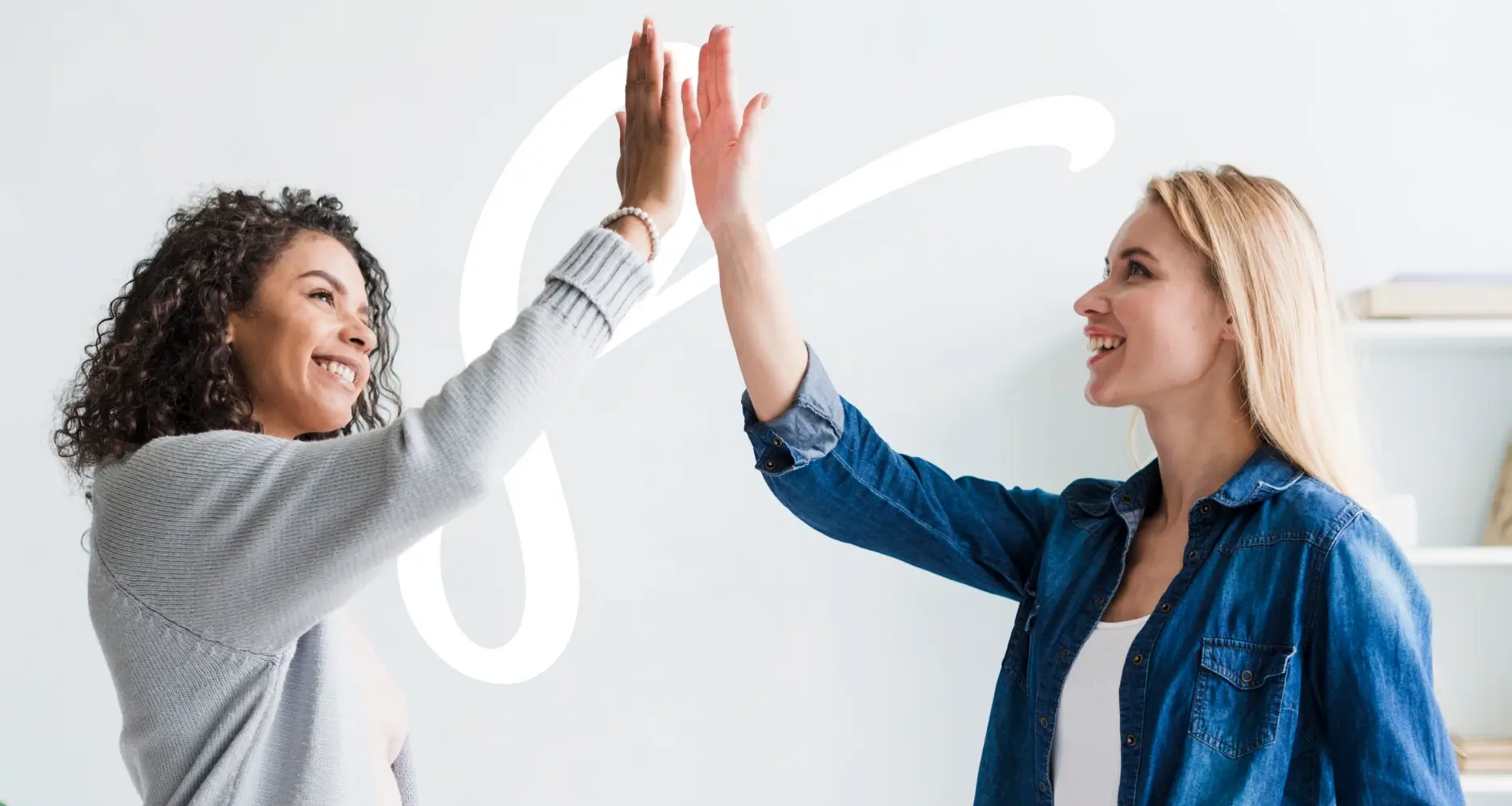
None
Training objectives
Acquire the tools to quickly and efficiently resolve problems in production, in a workshop or in the field
Identify the keys to success of this approach and promote the results
135Training program
Solving problems in the field (QRQC): conditions for success Formalize a simple and structuring problem-solving approach.
- Opt for the logic of D.
- Identify opportunities for progress for your company: complaints, mudas, malfunctions, etc.
- Define the criteria for choosing problems to be addressed.
- Engage management.
- Prepare your animation materials (display board, recording sheets, A).
- notion of quick meeting and more generally QRQC (Quick Response Quality Control).
83The key method and tools to apply in the field
- Identify the issues and share them.
- Collect key information as close as possible to the production or process concerned.
- Search for root causes through creativity in minute meeting, in the field and/or by display (CEDAC.
- M, why?).
- Identify the causes of non-detection upstream of the problem.
- Organize the validation tests of the causes.
- Search for suitable solutions and implement them, generalize and inform.
- Plan the monitoring of the effectiveness of corrective actions .
- Use feedback.
- Practice a case study.
13655Check the progress of actions and their effectiveness Use visual management to animate.
- Manage the progress of the steps of the process.
- Display the success story.
- Check the application of the solutions.
- Measure hot and cold the effectiveness of the actions undertaken using reliable indicators.
Responsible for continuous improvement
★★★★★
- QST-41
- 8 Days (56 Hours)
Description
Industrial and service companies that aim for overall performance (quality-profitability-health-safety-environment, etc.) work tirelessly to improve their working methods and individual and collective behavior. The first part of this cycle allows you to discover the key issues and methods for leading an improvement project, the second part is reserved for practicing the tools, finally, the last module is focused on communication and project management . Ultimately, this training gives you the keys to triggering, undertaking and implementing a continuous improvement process based on participation and the search for efficiency.
Who is this training for ?
For whom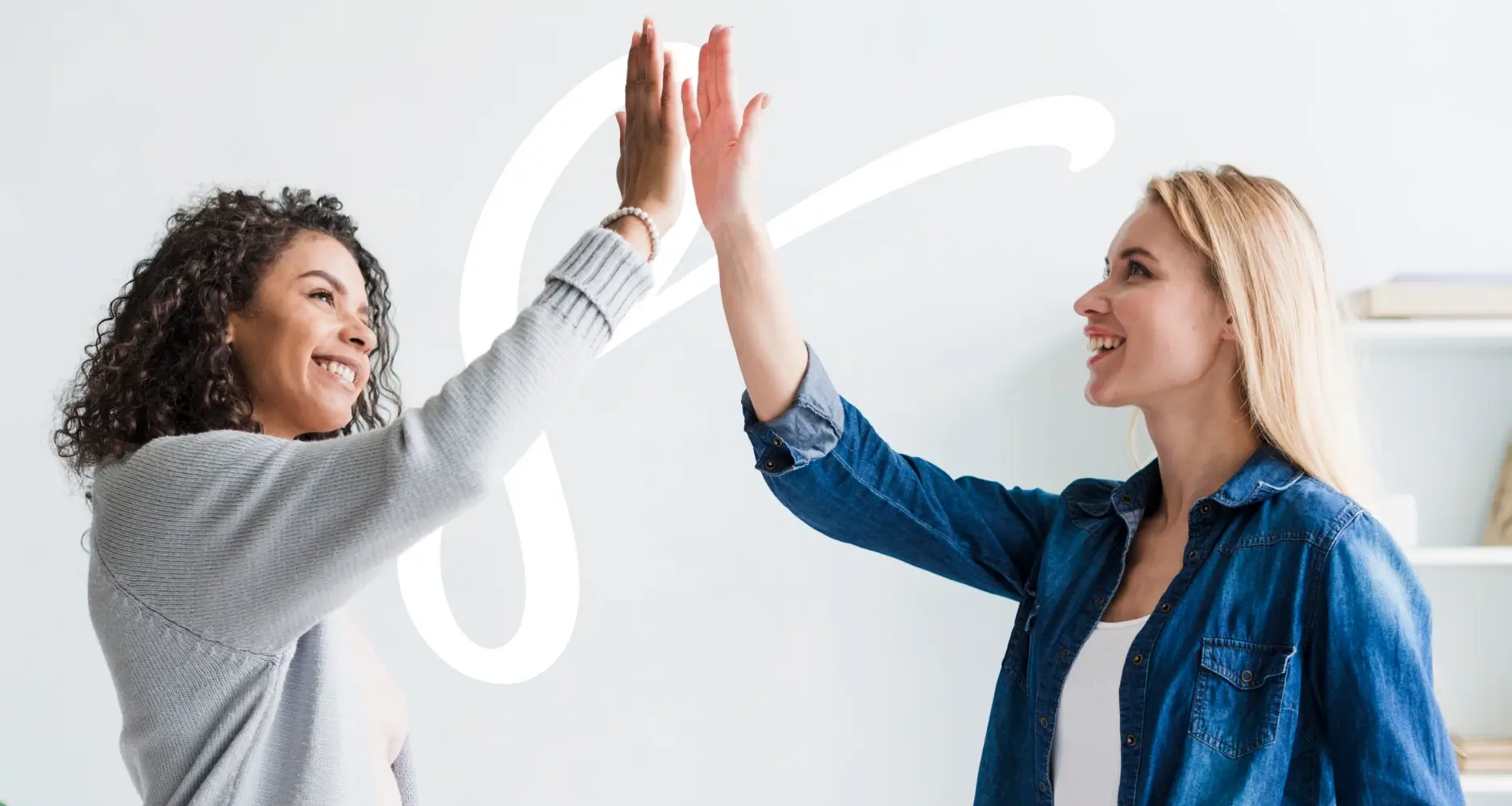
None
Training objectives
Understand the logic of continuous improvement in industrial or service companies
Acquire and practice the tools of permanent progress to improve quality and productivity
Address project management and change management
139Training program
Understand the logic and challenges of continuous improvement
- Discover the overall principle of PDCA and its logic of sequenced continuous improvement.
- Identify the different continuous improvement approaches: Kaizen, Hoshin, Six Sigma, lean management... and
- Identify the different associated tools.
- Similarities and differences of these approaches, know how to choose the right approach for your company.
- Ensure the consistency of the continuous improvement approach with the company's strategy
- The conditions. of success to establish a culture of continuous progress.
- Scenario Practical exercises and educational games
Drive continuous improvement
- Clarify the need, the purposes.
- Write a project sheet, define the conditions for success of the project.
- Create your team in a logic of professional exchanges .
- Clarify, formalize and share the improvement process and associated good practices.
- Plan the steps and tasks (improvement plan and associated monitoring), manage your budget.
- Manage the project. Case study: drafting a framework sheet
Diagnostic tools
- Know the quality diagnostic tools: productivity assessment; measurement of non-quality costs; internal and external benchmarking; collective search for dysfunctions; measurement of quality perceived by customers; choose key indicators of the balanced performance of the company: productivity, health and safety, environment The search for MUDA to reduce waste Situation Implementation of the tools
Remote activities
- To discover a subject related to your training: an e-learning module 'Detecting customer expectations to succeed in your project'; an e-learning module 'The framing of the project'; an e-learning module ' Establish the project budget.
140Practice improvement tools
- To improve quality, practice problem solving: use a relevant problem solving method and proven tools (5M, cause tree, 5-why, tree diagram, analysis matrix). decision...),
- To eliminate waste and increase productivity, rely on: lean management: ensuring greater customer satisfaction with better resource efficiency; , Value Stream Mapping, key areas for progress...
- To control the dispersion of processes: MSP (statistical control of production); more generally, Six Sigma and its principles of action (); DMAIC).
- Scenario Analysis of a practical case in a subgroup
Remote activities
- To discover a subject related to your training: an e-learning module 'Problem solving tools and methods'; an e-learning module 'Project management: mobilizing stakeholders'; an e-module learning 'Lead a project steering committee meeting'}.
Implement improvement in the company
- Know how to present the project to management. Choose and 'sell' the right solutions in the field.
- Check the effectiveness of the actions undertaken.
- Implementation situation.
Make lasting progress, support change
- Identify the possible causes of resistance, prepare your project accordingly.
- Communicate throughout the projects. lead the project in the field.
- Promote the first results, anchor the maintenance of results over time.
- Report the project to management and staff.
- Manage the end of the mission with the project team. ,
- Guarantee the maintenance of results over time.
- Scenario Simulation, construction of a display on an improvement project.
Conclusion of the cycle
- Evaluation of acquired knowledge
Environment Manager
★★★★★
- QST-42
- 8 Days (56 Hours)
Description
Responsible companies have chosen to reduce their environmental impacts. Meeting this challenge requires, beyond regulatory compliance, to undertake actions with high environmental added value. This training cycle allows companies to count among their resources an independent, credible expert ready to take charge of their mission as Environmental Manager and concretely achieve the targeted environmental objectives. The first part covers regulations, the second part develops the ISO 14001 standard, then the last module is reserved for opening up to the issues of sustainable development.
Who is this training for ?
For whom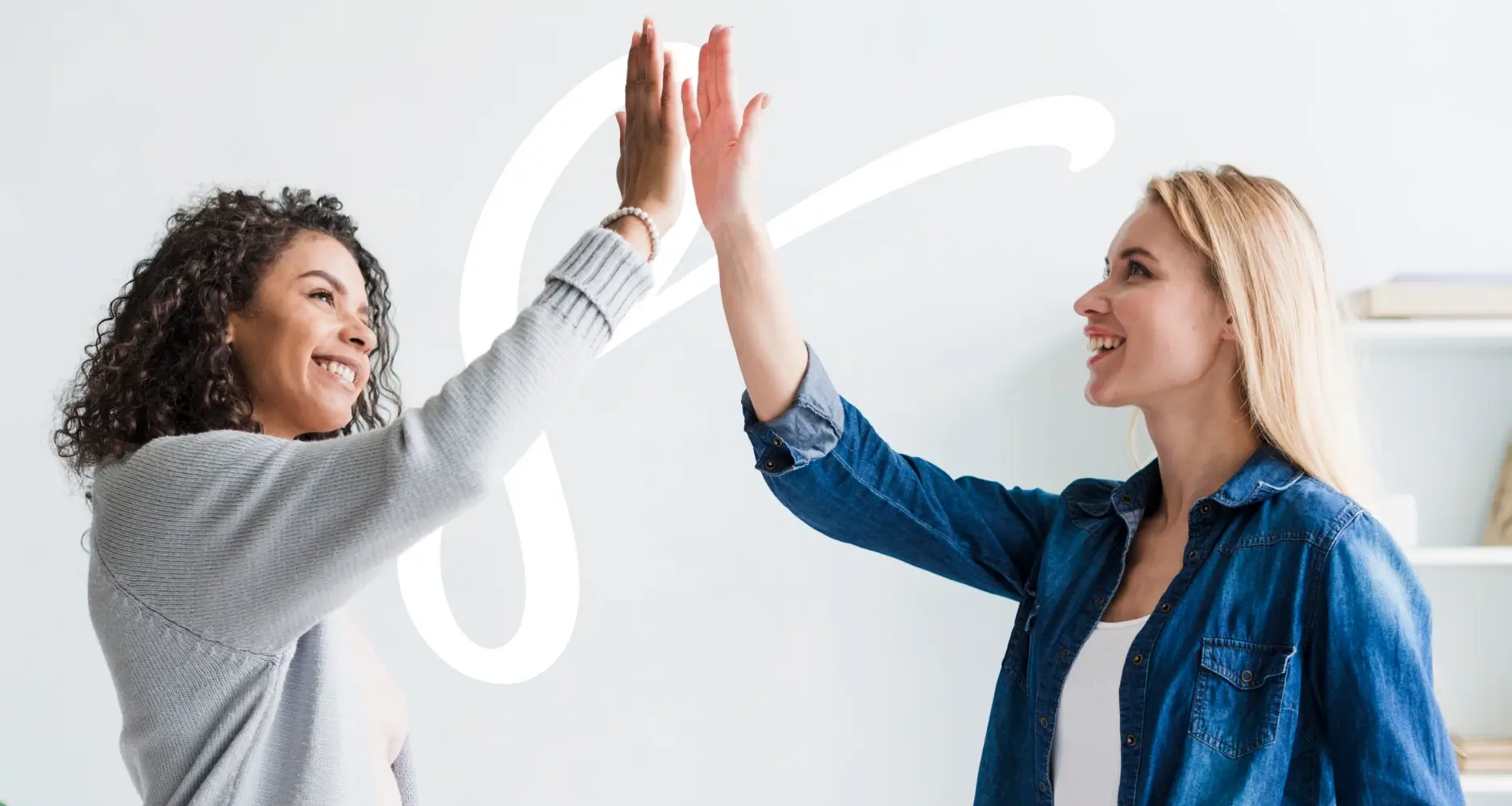
No prerequisites.
Training objectives
Find your way around the regulations.
Identify and know how to implement the key elements of an environmental management system (ISO 14001 V2015 type).
Acquire and use methods and tools for prevention, management and improvement in terms of environment and sustainable development.
143Training program
Environmental vocabulary and principles
- The notion of environment, environments, the environmental impacts of a company.
- Environmental issues in the sustainable development approach.
- The key players, the mission of the Environmental Manager.
The legislative and regulatory framework
- The hierarchy of legal rules.
- The importance of European texts and their influence on French law.
- The notion of environmental responsibility.
Environmental law and other applicable texts
- Scenario Knowledge quiz.
- The major themes regulated in French law (water, air, noise, waste, soil, natural environments, ATEX, VPO , asbestos...) and the main related texts.
- Related regulations.
ICPE regulations
- The importance of the ICPE status.
- The nomenclature of classified installations (content and use).
- Subject to the different regimes of the ICPE regulations (declaration with or without control, registration, authorization).
- The specificities of the SEVESO regime.
- The role of the administration (Prefecture, DRIEE / DREAL, CODERST...) and regulatory compliance control.
- Scenario Practical exercises.
144Other key provisions and significant current regulatory developments
- The 'Grenelle de l'environnement'.
- Mandatory environmental reporting.
- The BEGES report and carbon report.
- The mandatory energy audit.
- The European REACH regulation: substances, candidate list, involvement of downstream users (role, operation, implications for certain categories of companies).
- The new rules 'labelling.
- The transposition into French law of the IED directive.
- The emergence of BAT The new SEVESO III.
- Significant regulatory developments in course.
Regulatory monitoring
- The content of effective monitoring.
- How to obtain the right information.
- Scenario Practical study: the key sites.
The principles of an environmental management system
- The notion of environmental performance, the logic of prevention and improvement (PDCA).
- Presentation of ISO 14001V2015.
145Implementing an EMS: context analysis (Chapter 4)
- Understanding the internal and external context: data analysis.
- The notion of interested parties: knowing how to identify and listen to them.
- The notion of risks and 'opportunities.
- Define the scope of application.
Management Accountability and Planning (Chapters 5 and 6)
- The driving role of management.
- Clarify roles and responsibilities.
- Carry out an initial impact analysis based on the product life cycle .
- Identify priorities, formulate an environmental policy by reasoning threats and opportunities.
- Formalize an action program (objectives, targets, resources, monitoring, etc.).
- Identification of compliance obligations.
Support and control of operational activities (Chapters 7 and 8)
- Adapt material and intangible resources.
- Build an adapted documentation system (concept of documented information, procedures, records).
- Ensure competence, training , staff awareness.
- Establish your communication plan.
- Operational control: deploy good practices in the field (in normal and emergency situations).
146Performance assessment and improvement of the EMS (Chapters 9 and 10)
- Implement essential controls and key indicators consistent with the targeted objectives.
- Conformity assessment.
- Internal audits to make progress.
- React to non-compliance. Trigger corrective actions.
- Organize management reviews to observe and progress.
- Scenario Practical work
Succeed in your ISO 14001 V2015 certification project: the key steps
- Scenario Construction of your individual action plan.
Towards sustainable development
- The notion of CSR: corporate social responsibility.
- The major environmental issues and standards (ISO 26000).
- Complementarity with the ISO 14001 standard.
Acting for the climate and biodiversity
- The context and the issues, the emergency for the climate and biodiversity.
- Conventions, international framework agreements, European guidelines and their territorial variations.
- Respect and anticipate regulatory texts.
- The main courses of action: improve energy performance, reduce greenhouse gas emissions, preserve and contribute to diversity, the circular economy.. .
147Reduce your GHG emissions, improve your carbon footprint
- Regulatory issues and key points.
- References, key principles of a greenhouse gas balance and carbon footprint.
- Initiate a policy relevant energy.
- The mobility plan; from obligation to opportunity.
Think about the life cycle and develop the circular economy
- The notion of product life cycle, eco-design and circular economy.
- Examples of successful experiences, the role of the different actors.
- Scenario Presentations of inspiring practices.
Conclusion of the cycle
Remote activities
- Two experts: "Acting for the climate" and ""Circular economy".
Responsable QSSE
★★★★★
- QST-43
- 9 Days (63 Hours)
Description
The mission of QSSE Manager (Quality-Health/Safety-Environment) covers very varied missions. From QHSE risk analysis to the construction of a continuous improvement plan, the QHSE Manager constantly engages the entire company in a coherent and efficient approach. This 9-day cycle is designed to help you build and deploy a simple and integrated QHSE management system. The first part lays the foundations of QSSE systems in a logic of prevention, improvement and regulatory compliance. The second part allows everyone to understand the requirements of the key standards as well as the associated tools. Finally, the last part gives the keys to running the system on a daily basis.
Who is this training for ?
For whom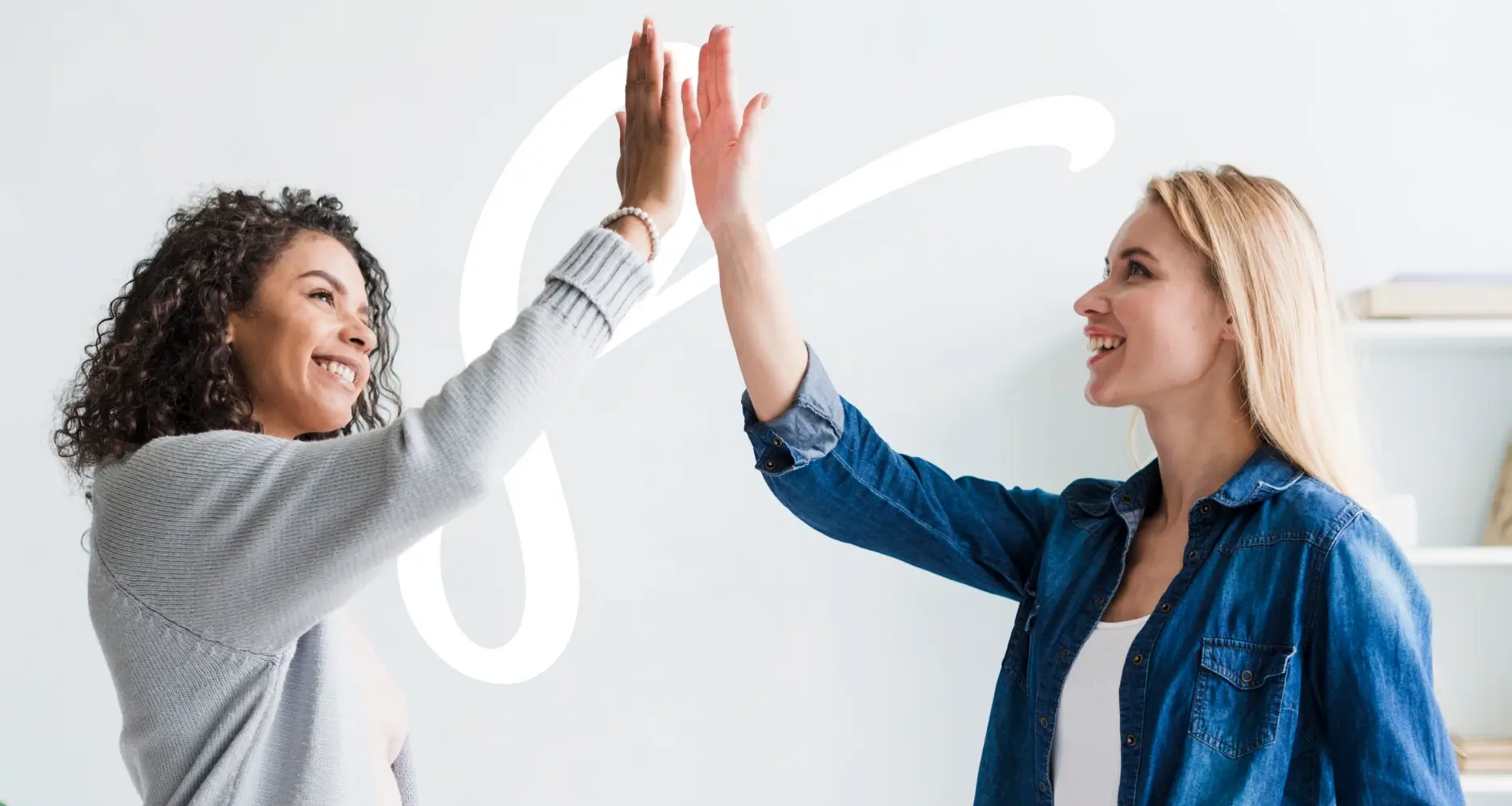
None
Training objectives
Discover the missions of a QSSE Manager.
Understand the issues and principles of a QSSE management system.
Identify the steps and tools to build an integrated, simple and efficient QSSE system.
150Training program
Before the face-to-face
- A self-diagnosis.
Key principles of a QSSE system
- The challenges of a QHSE system.
- The key players in the process.
- The mission of a QHSE manager.
- The combined logic of prevention, continuous improvement and regulatory compliance: QHSE risk analysis; concept of PDCA.
QSSE regulations
- Notion of prevention plan.
- Labor law: requirements in terms of health and safety at work. Concept of arduousness.
- Labour law environment and other key texts.
- The ICPE regulations.
- The regulations linked to dangerous products.
- The Grenelle law, the associated obligations of the company.
Ensure regulatory compliance
- The regulatory monitoring process.
- The key sites to know.
- Regulatory audits.
The key steps to building a QHSE management system
- The key stages.
- The organization to be implemented.
- Practical application: After part 1, participants are invited to carry out an assessment HSE regulations of their company.
151The structure of standards and their scope
- Know the international standards: ISO 9001, IS0 14001, ISO 45001.
- The common logic, the specificities.
- The 10 chapters and their logic.
- The interactions of chapters 4 (context analysis), 5 (leadership), 6 planning, 7 (supports), 8 (operational control), 9 and 10 (analysis, monitoring and improvement).
- The conditions for passing a certification.
Common requirements
- Analysis of the internal and external context.
- QHSE policy and associated planning.
- Risk analysis: product and process risks; l 'assessment of professional risks; initial environmental analysis.
- Control of documented information.
- The competence of personnel to anticipate failures.
- Metrology : mastery of control devices.
- Corrective and preventive actions.
- Management reviews.
152The specificities of ISO 9001 V2015 (quality)
- The notion of a process approach to decompartmentalize the company.
- Listening to customers and more generally interested parties.
- Process review.
- Requirements related to purchasing, HR, design, production processes.
- Key points to guarantee the quality of products and services.
ISO 14001 and ISO 45001: environment and health/safety
- Initial environmental analysis.
- Evaluation of occupational health and safety risks, psychosocial risks.
- Operational control in health - safety and the environment .
- Notion of product life cycle.
- Practical application: During the intersession, everyone chooses a tool and creates an operational implementation sheet.
Monitor your QSSE performance
- Monitor the effectiveness of your action plans.
- Choose your QSSE indicators.
- Format your dashboard.
- Use your dashboard in a PDCA logic.
Organize effective management reviews
- Prepare your meeting: collect key information.
- Prepare your agenda: alternate contributions and participation.
- Write and distribute a report.
153Implement corrective and preventive actions
- Adopt a simple and effective problem solving method.
- Create an easy-to-write corrective action sheet.
- Address the notion of costs associated with malfunctions .
Bringing the dynamics to life on a daily basis
- Involve everyone.
- Train in QSSE.
- Communicate effectively.
After face-to-face - Implementation in a work situation
- A strengthening program: a challenge every week helps you implement your action plan.
Quality Manager
★★★★★
- QST-44
- 3 Days (21 Hours)
Description
The Quality Manager coordinates the quality organization to be implemented in the company to guarantee customer satisfaction with a logic of profitability and continuous improvement. This reference training allows newly appointed quality managers to acquire the key tools to implement and maintain a simple and efficient Quality approach.
Who is this training for ?
For whom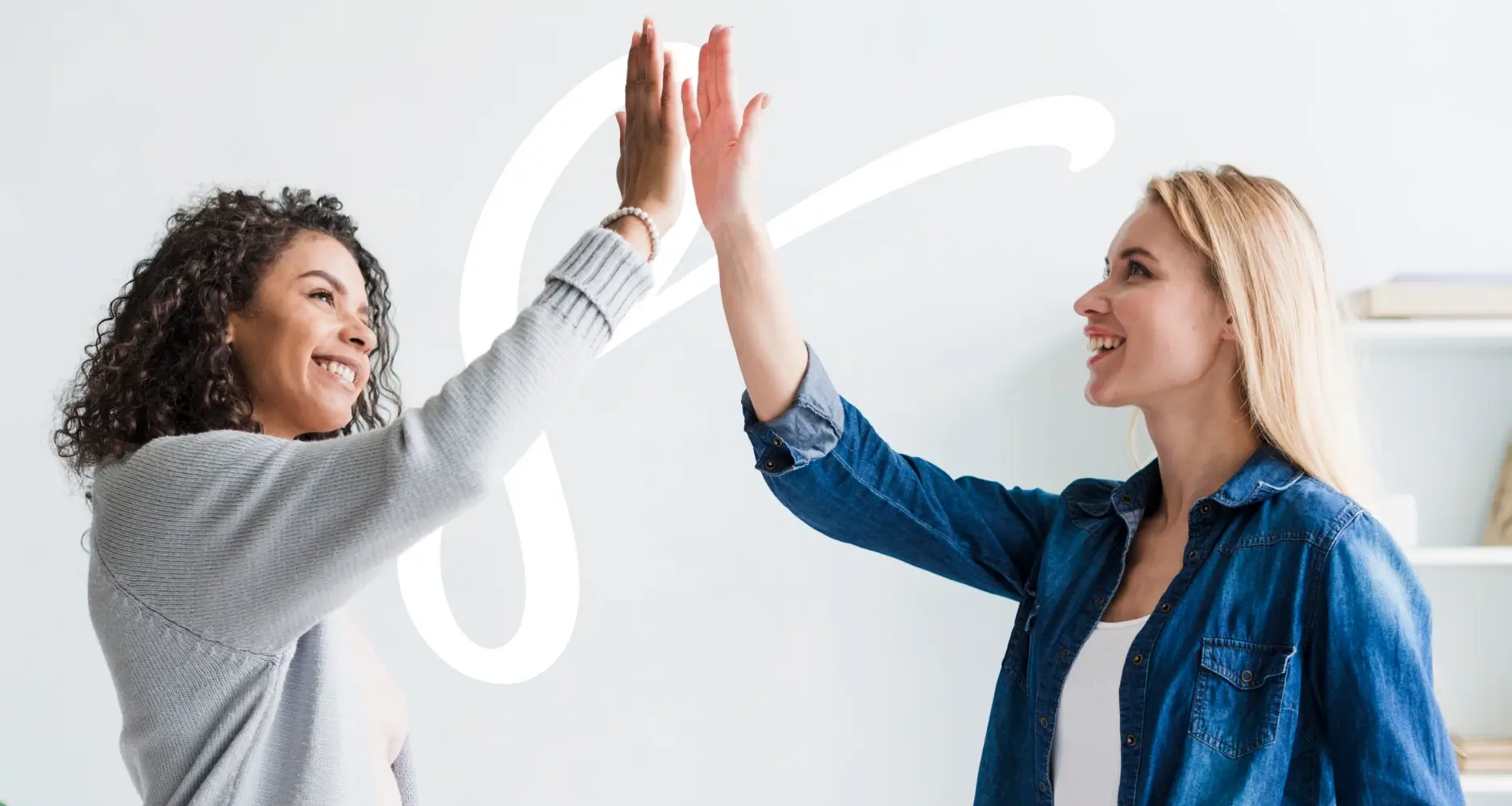
- Know how the company works.
Training objectives
Situate the role of the quality manager. Acquire the quality principles and tools to carry out your mission.
Build your individual action plan to begin your quality approach.
156Training program
Understand quality principles
- The different concepts: Quality Management and Assurance, control, PDCA.
- Issues, benefits of the quality approach. The balance between control and prevention.
- The main requirements of ISO 9001V2015.
- The key stages of a quality approach: from quality policy to operational results.
Carry out a quality diagnosis of your business
- Analyze the context, take stock of the processes
- Measure the costs of non-quality, the quality perceived by customers, key dysfunctions.
Plan and monitor improvement actions
- Engage the PDCA: set quality objectives consistent with the quality policy.
- Formalize and follow your action plan (responsibilities, resources, deadline, etc.).
- Build quality dashboards with relevant indicators.
Formalize a quality system
- Quality manual, process sheets, procedures and instructions: making it simple and effective...
- Processing non-conformities and customer complaints.
- Implementation relevant corrective and preventive actions on a daily basis.
Carry out the missions of the quality manager
- Develop a quality culture.
- The key missions of the position.
Remote activities
- A video "The essentials of the job of Quality Manager" ; two
- experts "4 key industrial quality tools" and "4 essential quality tools on duty".
Quality Manager: 4 attitudes for success
★★★★★
- QST-45
- 2 Days (14 Hours)
Description
Well beyond Quality methods, ensuring adherence is one of the main concerns of Quality managers and directors. As a result, cross-functional management involves knowing how to convince managers and adopting the right attitudes to create enthusiasm around the quality project. Discover in this training the levers that will allow you to make managers key actors of change.
Who is this training for ?
For whom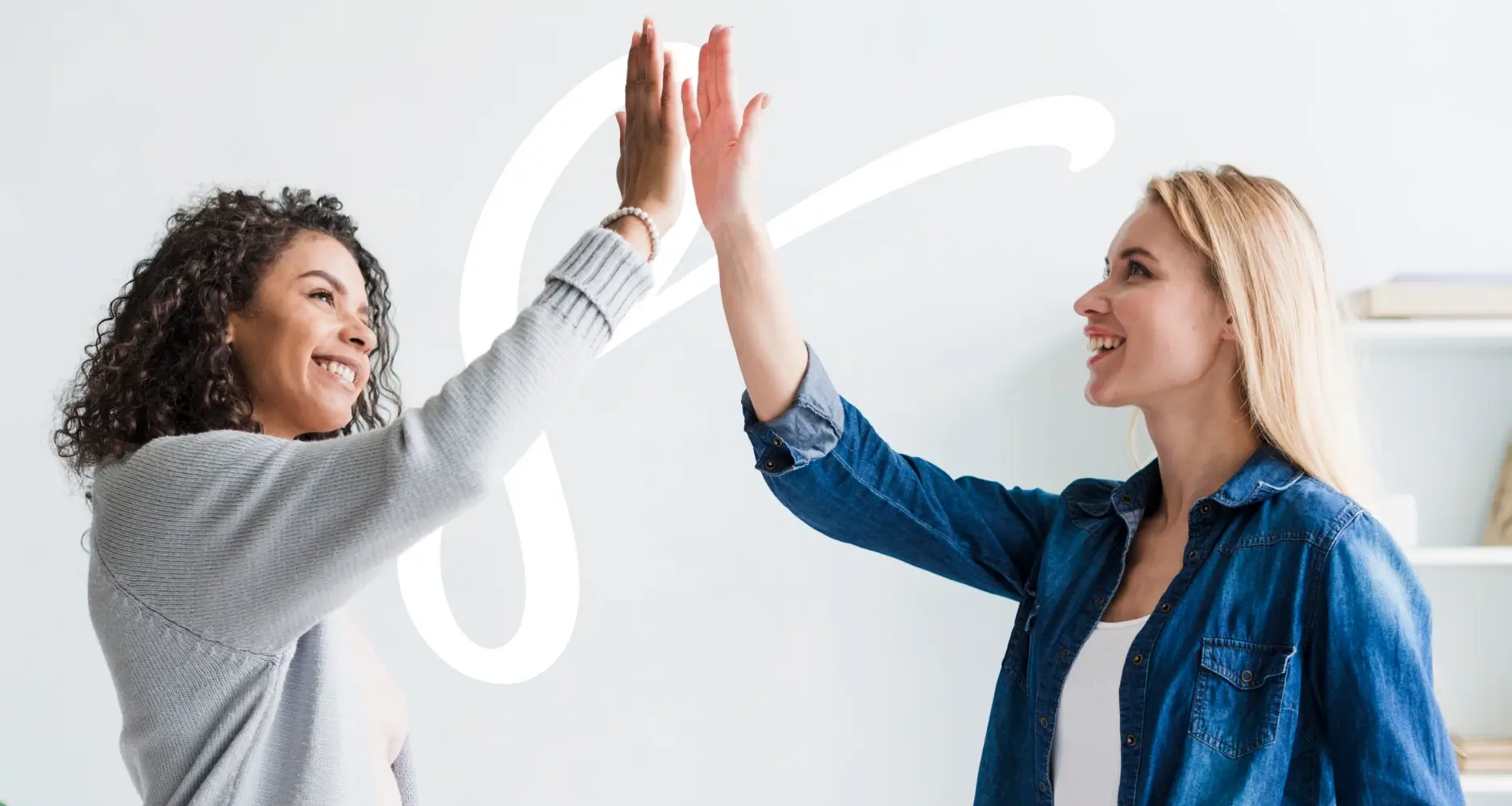
- Basic quality knowledge must be known.
Training objectives
Acquire the tools, the attitudes to manage effectively across departments, convince of the added value of the quality approach.
Reveal your leadership talents: unite, engage managers in action.
159Training program
The specificities of transversal management
- The conditions for success in cross-functional management.
- Knowing how to manage the tripartite relationship: manager - quality manager - resources.
- The key attitudes for success.
Attitude 1: knowing how to convince of the added value of quality
- Reason added value and issues.
- Build a relevant argument adapted to your interlocutors (jobs, interests, functioning).
- Demonstrate the profitability of the approach: adopt financial language, notions of COQ and return on investment.
Attitude 2: position yourself as a 'resource'
- Create your "service catalog".
- Be proactive.
- Know how to say no...delimit the scope of your mission.
Attitude 3: knowing how to listen
- Learn to listen. Accept the perceptions of others.
- Take reviews with management to progress.
- Transform criticism into opportunities for progress.
Attitude 4: develop your leadership
- Understand the difference between manager and leader.
- Express, share a stimulating vision of the quality project.
Build your action plan
- Identify strong points and areas for progress.
Remote activities
- Two e-learning modules "Assertiveness: methods and tools. Go. A" and "Assertiveness: methods and tools. Go. B".
Purchasing Quality Manager
★★★★★
- QST-46
- 6 Days (42 Hours)
Description
Recent scandals point to the lack of purchasing control in certain companies and demonstrate the importance of knowing how to guarantee the conformity of the products and services purchased. From gathering requirements to monitoring the performance of suppliers and subcontractors, the entire purchasing process is concerned. This training helps you set up selection criteria, control and AQF (supplier quality assurance) systems as well as monitoring indicators. It gives you the keys to deploy a real quality policy within the purchasing department with a permanent logic of prevention and continuous progress. In the first part, the basics of the supplier selection process and the reception control methods are discussed. The second part of the cycle is reserved for methods of monitoring suppliers for sustainable purchasing and good practices for preparing internal audits.
Who is this training for ?
For whom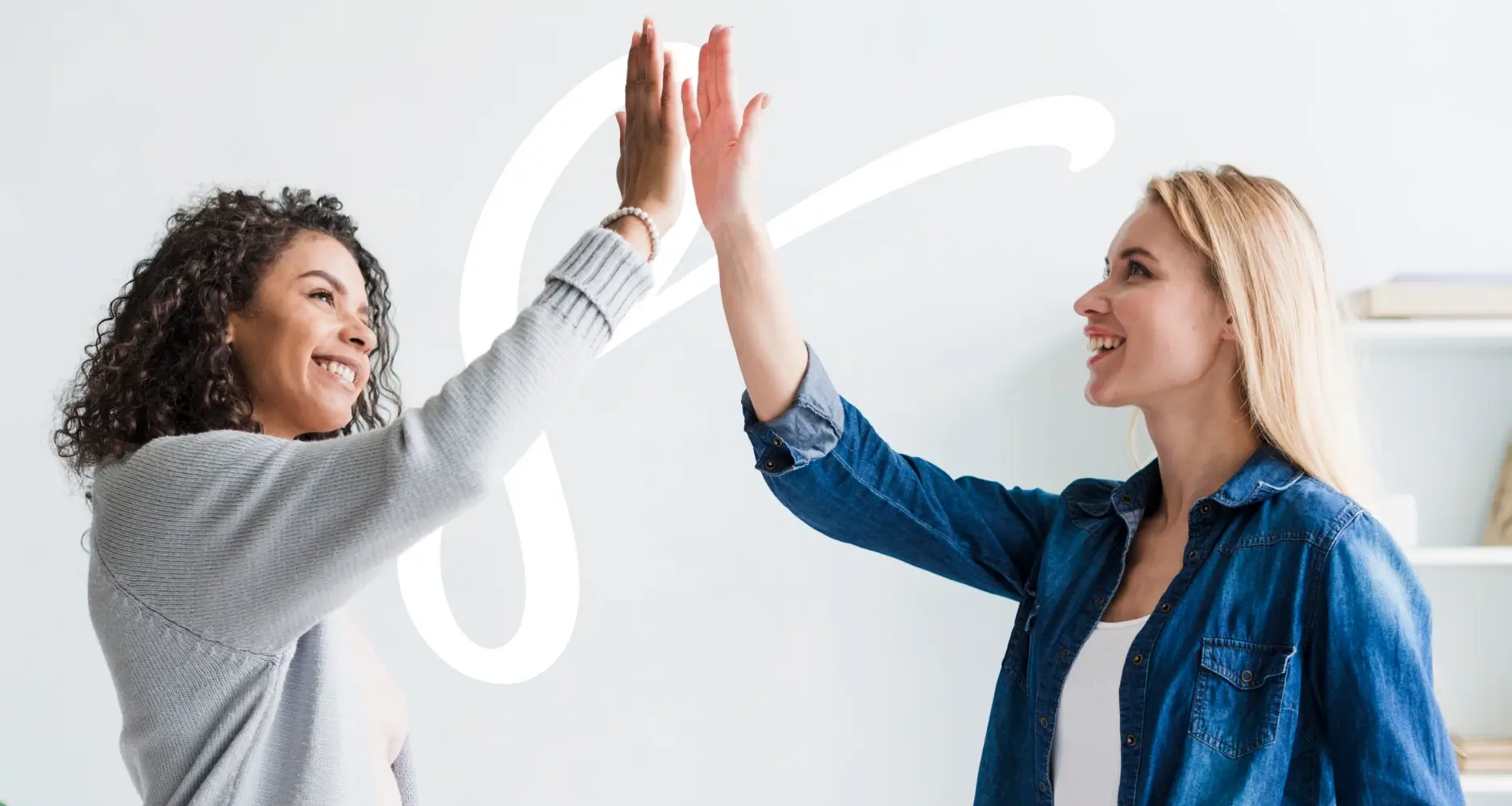
None
Training objectives
Acquire the tools and methods necessary to: evaluate, select and monitor suppliers; implement monitoring of purchased products
Make purchasing processes more reliable
162Training program
The purchasing process
- Understand the purpose and challenges of the purchasing process.
- Identify the risks linked to purchasing, identify critical and strategic suppliers.
- The process of formulating the need to receive compliant products.
- The requirements of the ISO 9001 standard related to purchasing.
- Other key quality standards (ISO TS 16949, EN 9100 etc.). ,
- The missions of the purchasing quality manager.
- Scenario Educational game.
Product and supplier specifications
- Know how to express your product needs, write relevant specifications.
- Know how to define appropriate requirements for your supplier's quality system.
- Scenario Exercise practical.
Supplier assessment and selection
- From potential suppliers to chosen suppliers: what approach? Pre-target suppliers.
- Establish a supplier selection questionnaire.
- Set your selection criteria based on of factual data.
- The two levels of audits: the overall supplier evaluation audit and the process audit to qualify the process/product pair
- Product control. or upstream service: to validate compliance with the specifications.
- Formalize the qualification by drawing up a contract
- Scenario Presentation of examples of selection grids. .
163Define a monitoring system for purchased products/services
- Reception controls: choose the criteria to be controlled; determine the frequency and quantity; the effectiveness of reception controls; use the MILST 105 table: the associated decision rules.
- Check at random.
- Face a delivery refusal, react accordingly to the importance of the non-conformity; initiate a request for corrective action from the supplier.
- The product conformity certificate.
- Organizing supplier quality assurance: the key stages and challenges.
- Practical case scenario.
Remote activities
- To illustrate the contribution of knowledge: a video 'Obtain a progress plan from your suppliers'.
Implement the right monitoring indicators
- Choose the appropriate indicators.
- Know how to measure performance on basic provision and associated services.
- Evaluate the costs of non-quality linked to purchases.
- Reason in specific and global terms: know how to compile the different data into a global indicator.
- Establish a supplier dashboard.
- Define associated management rules .
- Demonstrate the application of PDCA within the purchasing process.
- Integrate quality objectives into supplier contracts.
- Scenario Exercises in the framework of service and industrial companies
164Engage in a logic of continuous improvement
- Manage the panel of suppliers taking into account their results, their strategic importance and market configuration.
- React to supplier dysfunction: trigger a curative audit, strengthen controls.
- Integrate the supplier quality level into the supplier negotiation. 4
- Measure the maturity of suppliers). .
- Scenario Practical exercises, example of maturity grid
Responsible purchasing
- Good practices in responsible purchasing.
- The contribution of the environmental standard ISO 14001, health and safety at work OHSAS, societal SA 8000.
- More generally the key points of ISO 26000 (Social Responsibility).
- Scenario Identification of good practices
Prepare to be audited by a client or certification body
- The key documents to prepare to prove mastery of the purchasing process.
- The records to present.
- The key attitudes to develop.
- In the event of a crisis: what traceability is necessary? Scenario Examples of audit grids, simulation of an audit interview.
Remote activities
- To illustrate the contribution of knowledge: a video 'How to choose the right suppliers?' a video 'How to establish a constructive customer-supplier relationship?' .
- Learning assessment
Health and Safety Manager
★★★★★
- QST-47
- 8 Days (56 Hours)
Description
Why this training: Initiate a dynamic of risk prevention within an organization or a company, advise the management of the organization, structure the approach, ensure everyone's involvement, here are, among other things, the missions of the Managers Health security. The evolution of legislation and the regulation of social demand force the company to take up the permanent challenge of preventing health and safety risks at work. This training allows you to understand all the aspects of carrying out your mission with a view to improving the company's Health and Safety performance. This professional course, by carrying out personal practical application work between sessions in your company, helps you to anchor your learning in a real situation or as close as possible to the field.
Who is this training for ?
For whom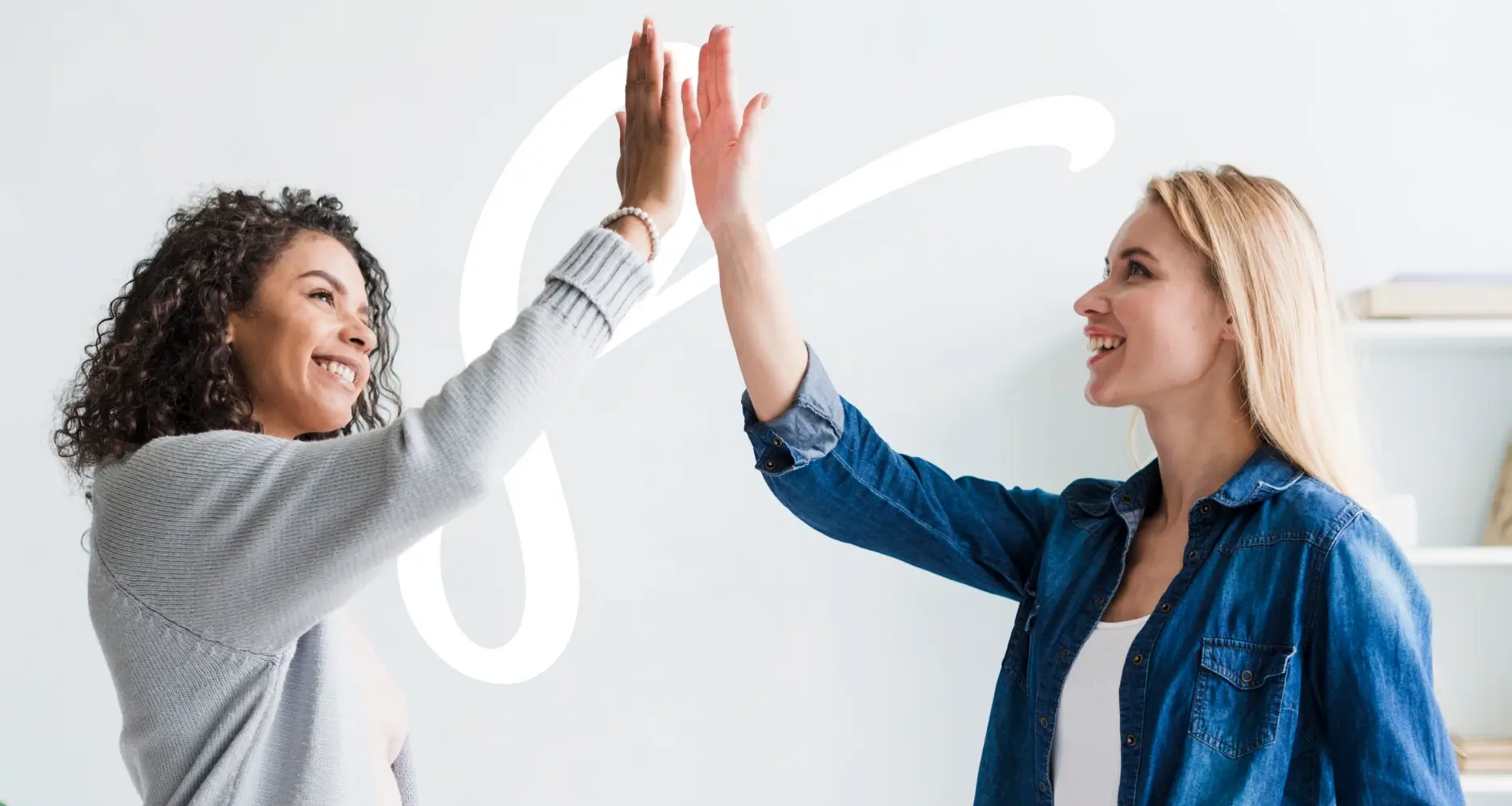
- It is recommended that participants be made aware of health/safety issues and business practices.
Training objectives
Acquire the key knowledge to carry out your mission as a health and safety manager, be a source of proposals for conducting a relevant prevention approach, promote a safety culture.
Integrate the main principles of regulations related to health and safety at work (OSH ).
Implement management principles according to ISO 45001 to improve the company's OHS performance.
167Training program
Before the face-to-face
- A self-diagnosis.
The OHS Manager, the challenges of the function
- Specify your missions. Clarify your role in the organization. Manage the application of general principles of prevention.
The international health and safety standards
- Main requirements and ways to meet them.
The Health and Safety at Work policy
- Help management to define priority areas in terms of prevention, protection and organization.
- Associate pragmatic improvement objectives.
Identification and assessment of OSH risks
- Know the different types of OHS risks (including psycho-social risks and arduousness factors) in the company.
- Evaluate and prioritize these risks.
- Take into account the FOH (Human and Organizational Factors).
- Update your unique document and "bring it to life" and make it a strategic tool.
- Update in situation Practical exercises on the identification, evaluation and prioritization of risks, role play for their presentation A quiz to assess the understanding of newly acquired knowledge.
- Practical application: Before the. part 2, carrying out a self-diagnosis of the SST performance of its site (based on an operational tool given to everyone) to present the most efficient elements.
Understand OHS regulations and responsibilities
- Use the Labor Code and know the fundamental OSH texts. Identify the regulations applicable to your activity.
- Take into account the case law.
- Know the civil responsibilities and criminal, fault, sanctions.
- Receive and transmit a delegation of power.
- Obligations to report work accidents and occupational diseases.
168Implementation of OHS regulatory monitoring
- Know the different sources of information to carry out your regulatory monitoring.
- Manage your regulatory monitoring.
Know the OHS actors: their obligations, roles, functions
- The employer, the CSE, the CSSCT.
- The occupational doctor/CARSAT/Labor inspector.
Manage risk prevention and control
- Establish your OHS management program based on risk analysis.
- Establish the training, awareness and communication program to involve everyone.
- Formalize the 'organization defined based on a documentary system compatible with the quality and/or environment system.
- Control operations, processes and their modifications (operational control - part 1).
- Ensure the application of instructions, Promote good practices.
- Take the economic dimension into account
- Scenario Practical exercises for drafting a management plan actions related to the risk assessment carried out in part 1. A role play on the communication plan Searching for texts on a regulatory database to facilitate the appropriation of knowledge.
- Practical application: Before part 3, everyone is invited to bring together in their company: the risk assessment, a prevention plan and the key OHS indicators.
Managing the risks linked to coactivity (operational control - part 2)
- Prevention Plan, Safety Protocol. General Coordination Plan. Special Safety and Health Protection Plan.
Respond to emergency situations
- Define emergency situations and measures to take.
Monitor regulatory controls and measure OHS performance
- Operational and functional controls: evaluate and improve performance.
- Measurements, equipment and metrology.
169Define and monitor relevant SST indicators for management and results
- Choose OHS indicators to evaluate the company's OHS performance.
- Build and manage your dashboard.
Improve your health and safety performance
- Analysis of incidents, accidents and non-conformities. Corrective actions and preventive actions to avoid accidents or their recurrence.
Prepare for the internal audit
- Place the audit in a prevention approach. The specificities of the Health-Safety audit to analyze a workstation.
Prepare the management review
- Collect, analyze key data. Help management make the right decisions.
Feedback on health risk management (COVID 19 type)
- Scenario Practical exercises for drafting a prevention plan, concrete accident analysis using the "tree of causes" method. In summary of the cycle: establishment of your prevention plan personal actions according to their professional objectives.
After face-to-face - Implementation in a work situation
- Three
- expert:"Road risks" ; "Psychosocial risks" ; "Addictions". A reinforcement program by email: one challenge per week for help you implement your action plan and after the face-to-face session, an activity personalized to your challenges which will allow you to transpose it into a work situation.
Monitor and improve the quality of your suppliers and subcontractors
★★★★★
- QST-48
- 2 Days (14 Hours)
Description
The quality of your products and services depends on those of your suppliers and subcontractors. Once evaluated and selected, they must be regularly monitored and encouraged to engage in a process of permanent improvement. This training gives you the keys to measuring and improving the performance of your subcontractors and suppliers.
Who is this training for ?
For whom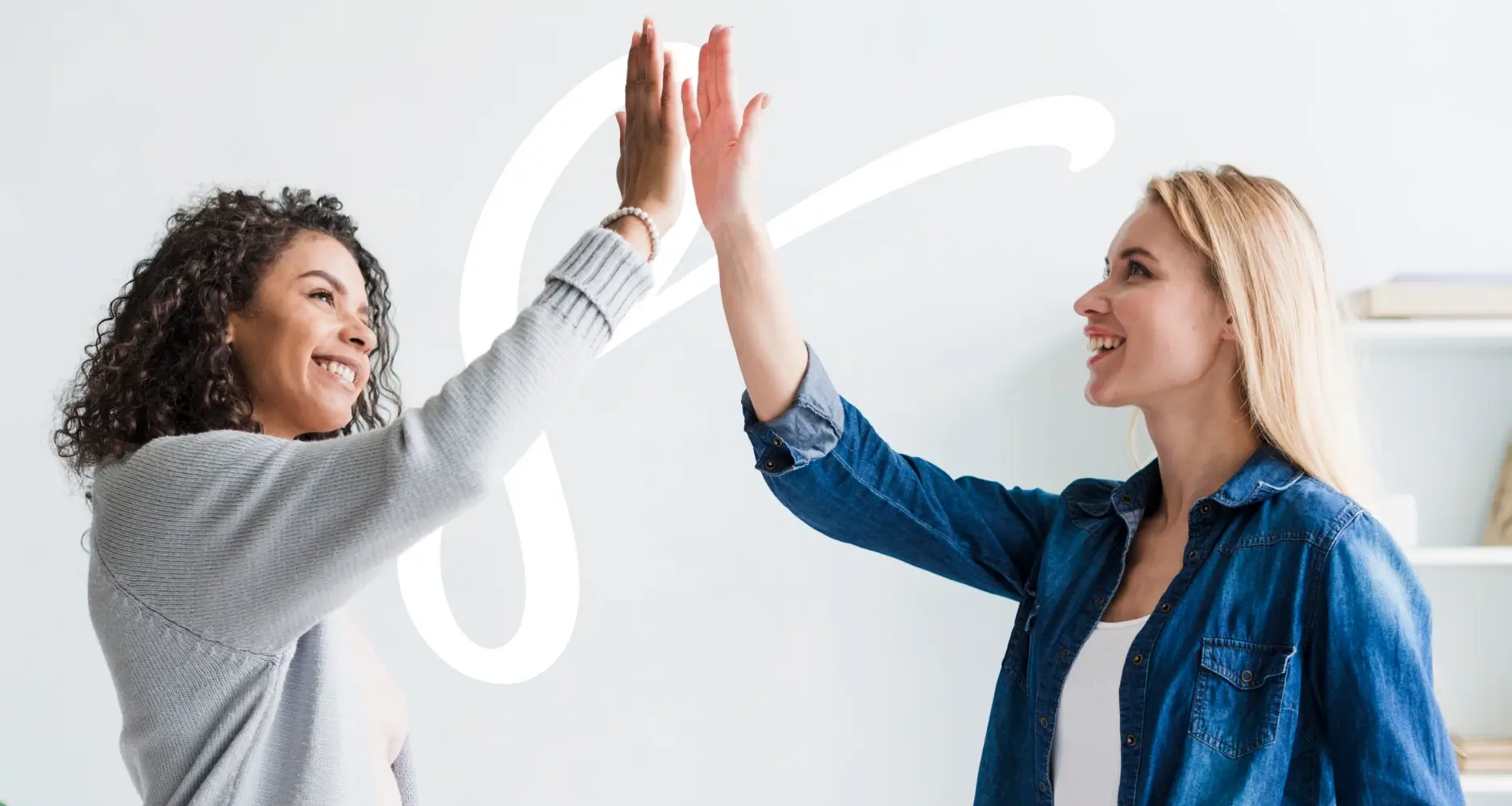
None.
Training objectives
Identify good practices for monitoring suppliers and subcontractors.
Beyond simply observing the quality of the services and products provided, establish a dynamic of progress with suppliers.
172Training program
The essentials of supplier selection and monitoring
- The list of critical and/or strategic suppliers and subcontractors.
- Key points of the purchasing process: the upstream product and system specifications; the evaluation criteria and selection of suppliers.
Choosing the right monitoring indicators
- The RUSAC method for finding the right indicators.
- Create your dashboard using simple and relevant indicators: reception quality level (deadline, compliance), quality level in production, rating of associated services... evaluate the costs of non-quality due to purchases.
- Consolidate the results with overall performance indicators.
Manage your supplier panel
- Send a regular assessment to your partners.
- Manage your panel: make the right decisions based on the results.
- Transform your suppliers to AQF (Supplier Quality Assurance) ).
React in the event of quality deviation Make a clear request for corrective action and follow it.
- Obtain a progress plan.
- Trigger audits if necessary.
- Manage crises.
- Help your subcontractors progress .
Remote activities
- Three videos "How to choose the right suppliers?" ; "How to establish a constructive customer-supplier relationship?" ; "Obtain a progress plan from your suppliers".
ISO 20000, Foundation, certification (understanding the Service Management System)
★★★★★
- QST-82
- 2 Days (14 Hours)
Description
This training allows you to understand the concepts, definitions and context of the ISO 20000 standard. You will acquire fundamental knowledge of the Service Management System and you will pass the ISO 20000 Foundation certification exam.
Who is this training for ?
For whomAny person working within an organization providing IS services and needing knowledge of the ISO 20000 standard.
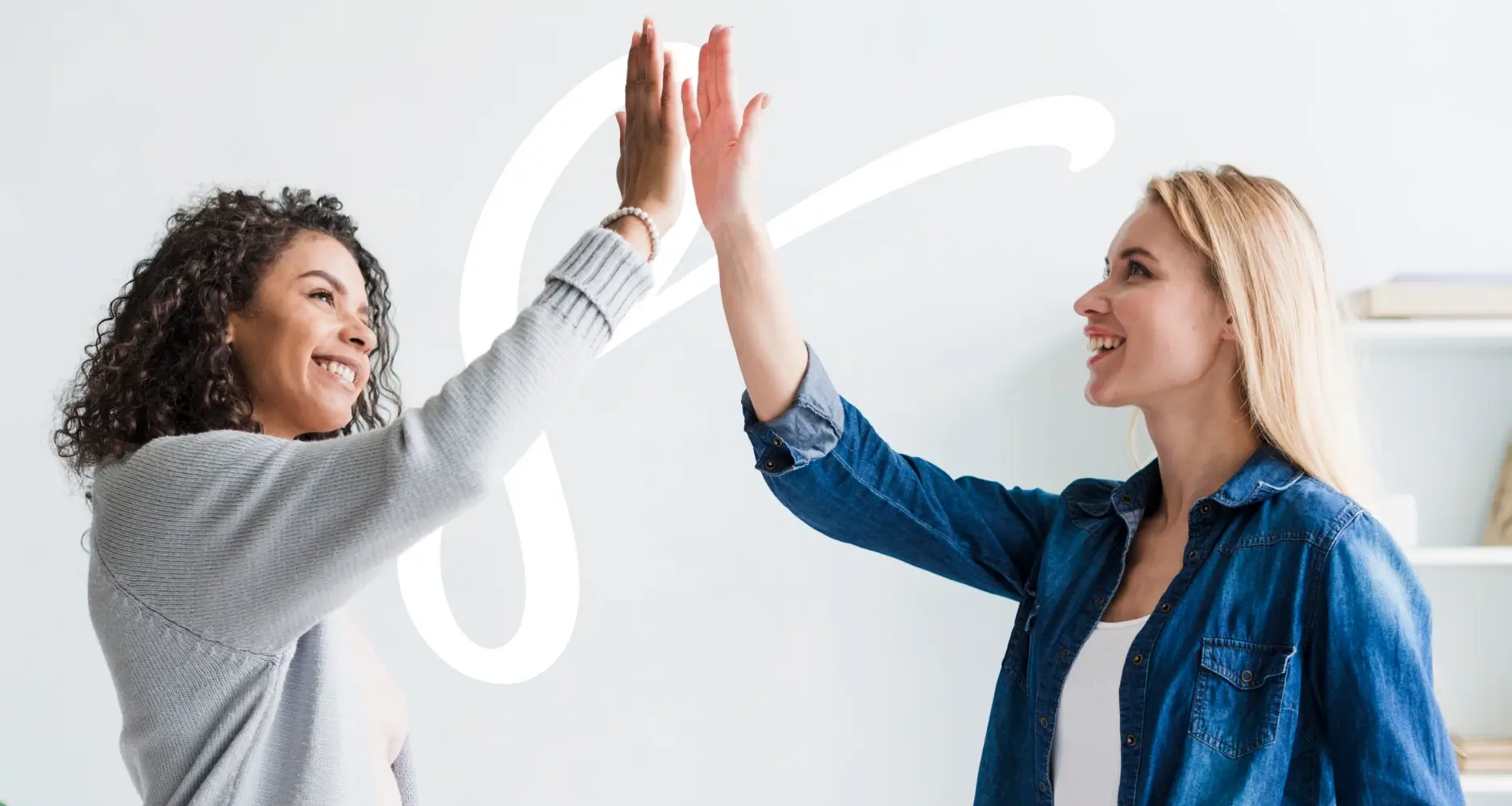
None
Training objectives
Understand what a service management system is
Define the different processes of the service management system
Understand the organization certification process
Prepare for the APMG ISO 20000 Foundation exam
175Training program
Introduction to the fundamentals of the ISO 20000 standard
- Service definitions, Service Management and Service Management System.
- History of the ISO 20000 standard for IT Service Management.
- The content of ISO 20000 .
- Link and differences from
- Continuous improvement and PDCA.
- The different levels of ISO 20000 certification.
- Collective reflection.
General requirements of a Service Management System
- Management responsibilities.
- Process governance.
- Document management.
- Resource management.
- The PDCA integrated into the Service Management System.
The scope of applicability of the ISO 20000 standard
- Presentation of the ISO 20000 part 3 standard linked to the scope of application.
- Define the scope of applicability.
- Good practices.
- How to take suppliers into account within the scope of applicability of ISO 20000?.
176Certification of organizations
- Why get ISO 20000 certified? Complementarity with ISO 9001.
- The certification audit.
- Types and principles of audit.
- The certification process of organizations.
ISO 20000 Lead Auditor ''Service Management System''
★★★★★
- QST-82
- 5 Days (35 Hours)
Description
In this course, you will discover the context, content, requirements, objectives and application of ISO/IEC 20000-1. This course also covers the scope and application of Parts 1, 2, 3 and 5 of the standard, and shows how they can be used during the certification audit.
Who is this training for ?
For whomThis qualification is primarily aimed at information technology auditors internal to the organization providing the service or belonging to a certification body.
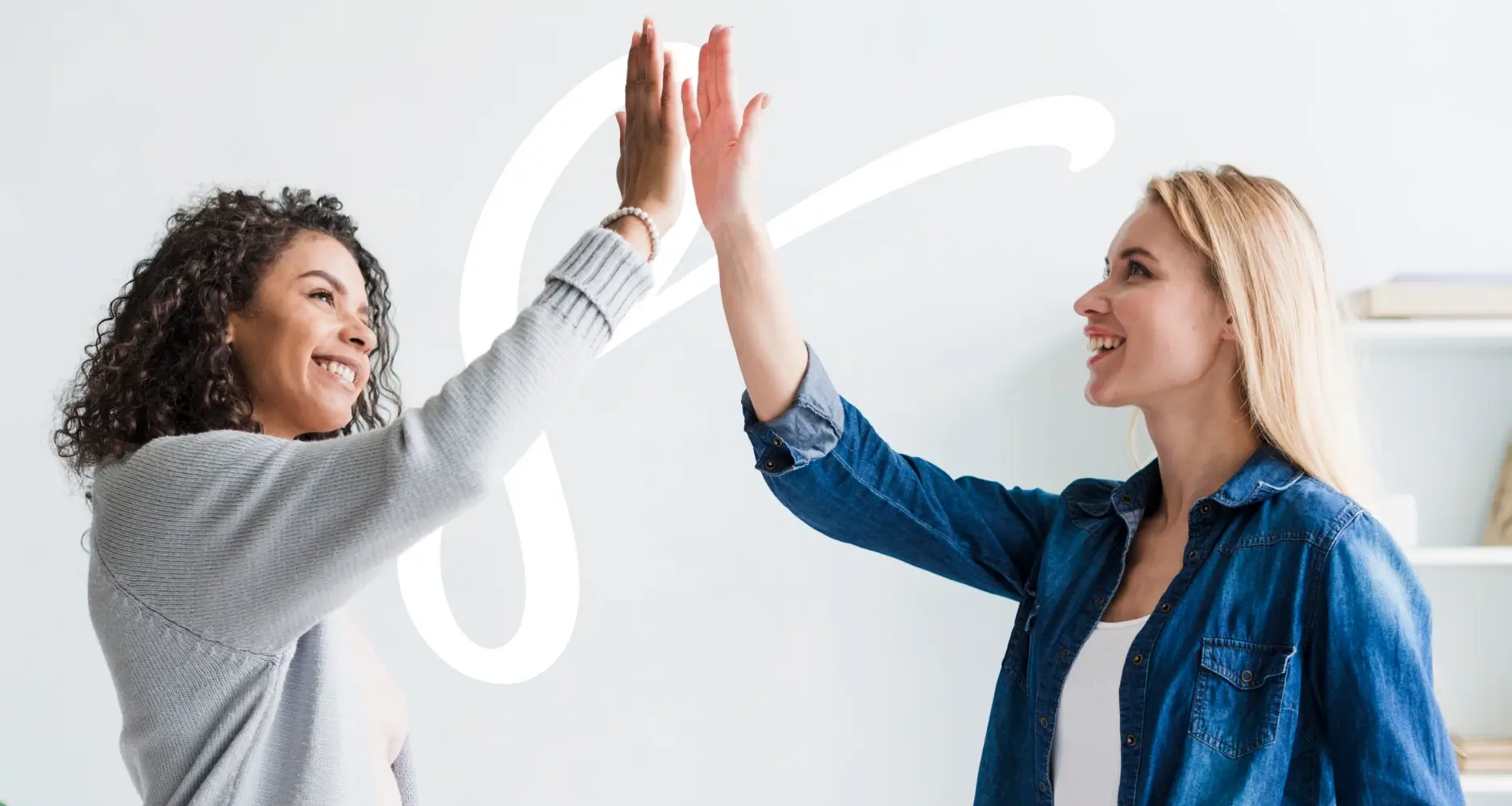
None
Training objectives
178179Training program
Introduction and discovery of ISO / IEC 20000
- The principles and basic elements of the ISO /IEC 20000 standard.
- The concepts: service, process, quality...
- Principles of the IT Service Management.
- IT service management.
- Business / IT alignment.
- The ISO /IEC 20000 standard and quality .
- Implementation risks.
- Relations with other standards/standards (COBIT®, ISO 9000, etc.).
- The ISO /IEC 20000 APMG certification scheme.
- Collective reflection.
- Collective discussion to understand what a Service Management strategy represents.
180ISO / IEC 20000, scope and use
- Structure of ISO / IEC 20000 part - 1.
- The objectives and application of ISO / IEC 20000 - 1.
- Scope and structure of ISO / IEC 20000 part - 2.
- Main differences between ISO / IEC 20000 part - 1 and ISO / IEC 20000 part - 2.
- Scope and structure of ISO / IEC 20000 part - 3.
- Scope and structure of ISO / IEC 20000 part - 5.
- Requirements for a pre-audit, a certification audit and periodic control audits.
- Practical work: How to resolve the issues of defining the scope of application and eligibility for the certification of the service provider.
ISO/IEC 20000, implementation
- Eligibility.
- The scope of the standard.
- The obligation to cover all processes.
- Integration with another quality management system.
- Exercise: Analysis of the eligibility of an organization.
181ISO/IEC20000 process audit
- Roles and responsibilities.
- Non-conformities.
- Observations.
- After certification.
- Collective reflection.
- Conduct the audit of ISO /IEC20000 processes.
Revision, exam preparation and certification
- Revision session and completion of a mock exam.
- Correction of the mock exam.
- Preparing for the exam.
- Practical work.
- Certification exam.
CGEIT®, IT governance, preparation for Certified in the Governance of Enterprise IT certification
★★★★★
- QST-64
- 3 Days (21 Hours)
Description
This course is designed for IT and business professionals who wish to pass the CGEIT exam. The program covers the five key areas covered in the exam: corporate IT governance framework, strategic management, service delivery, risk optimization, resource optimization.
Who is this training for ?
For whom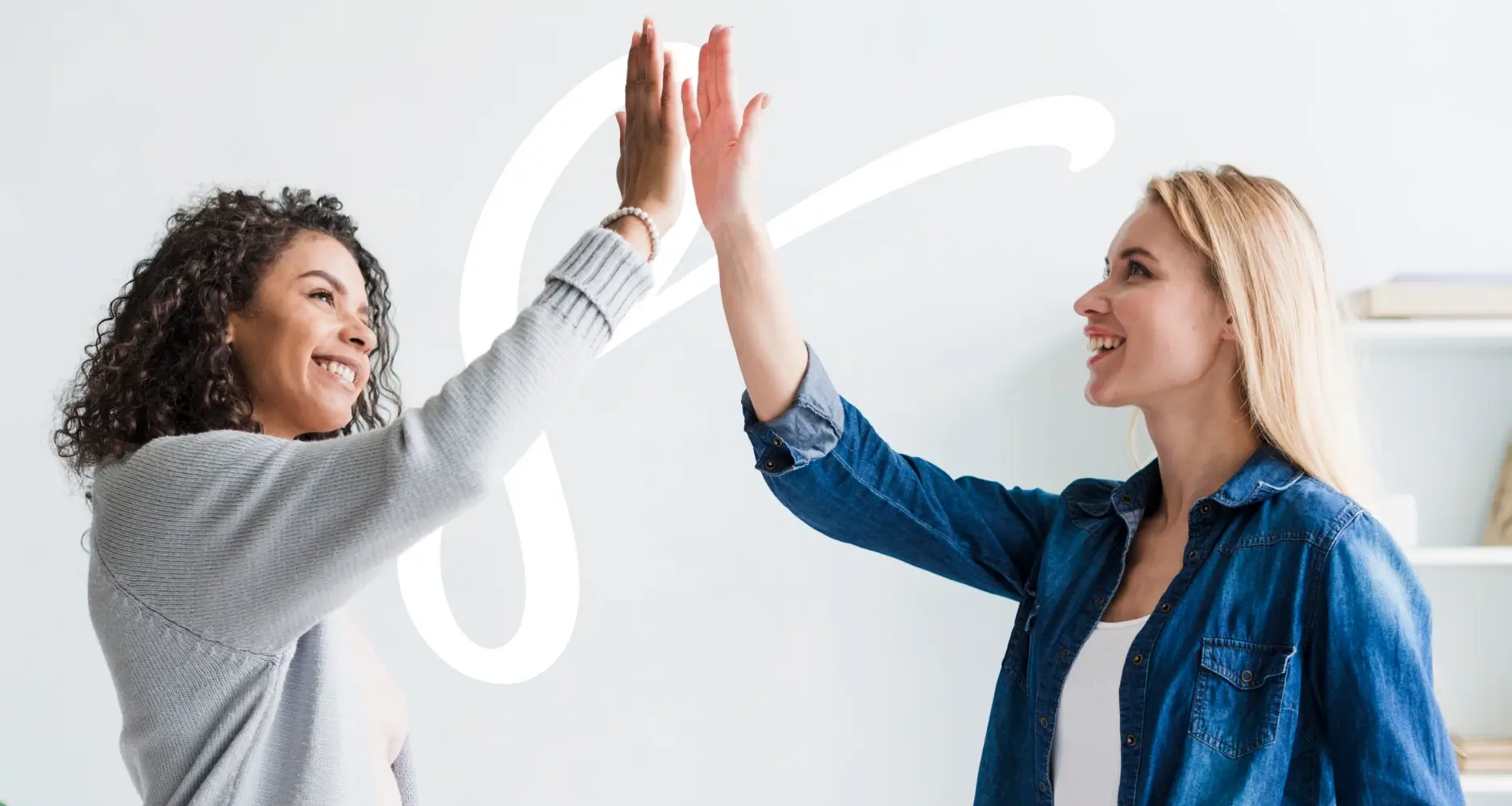
None
Training objectives
Apply best practices in IS governance in an organization
Understand the tools and concepts of strategic management in IS governance
Use good practices as levers to master the value of IS for the organization
Use risk management and methods for optimizing IS governance
Optimize resources to ensure that they will be used as essential support for IS governance
184Training program
Introduction au Certified in the Governance of Enterprise IT
- General presentation of the CGEIT.
- Presentation of the exam model and certification.
Understand the context and associated repositories
- COBIT, ITIL, ISO20000, ISO38500, ISO31000.
- SWOT, BCG Matrix, Balanced Scorecard.
- Val IT, maturity models.
- RISK IT, COSO ERM.
- Business continuity and disaster recovery.
- Exercise: IS governance frameworks.
Domain 1: IS governance framework
- IS governance in business.
- Governance practices, standards and benchmarks.
- Enterprise architecture: components and principles.
- Continuous improvement processes and techniques.
- Exercise: IS governance and associated standards.
185Domain 2: strategic management
- Corporate strategic plan.
- Impacts of business changes - IS.
- Barriers to strategic alignment.
- Policies and procedures necessary to support alignment.
- Strategic planning process.
- Scope, objectives and benefits of investment programs.
- Exercise: Management strategic.
Domain 3: benefit of risk optimization
- Investment management.
- Portfolio management.
- Process and service measurement.
- Planning, development, transition and support of services.
- Continuous improvement of services.
- Performance and results.
- Evaluation of investments.
- Cost optimization.
- Exercise: Benefits of risk optimization.
186Domain 4: Risk Optimization
- Risks at different levels of the company.
- Standards and benchmarks.
- Risk management & business resilience.
- Appetite for risk & risk tolerance.
- Key risk indicators (KRI).
- IS risk mitigation.
- Exercise: Risk optimization.
Domain 5: resource optimization
- Human, application, informational and infrastructure resources.
- Outsourcing and Offshoring.
- OLA and SLA.
- Performance evaluation.
- Service level management.
Preparing for the exam
- Best practices for passing the exam.
- Exam simulation.
Lean Six Sigma®, Green Belt, certification
★★★★★
- QST-83
- 6 Days ( Hours)
Description
This training will allow you to consolidate your knowledge of the Lean Six Sigma method. You acquire the necessary knowledge to lead an improvement project independently within your company. You will also be prepared to pass the IASSC Lean Six Sigma Green Belt certification.
Who is this training for ?
For whomProfessionals who wish to consolidate their knowledge of Lean Six Sigma® and become an actor in improvement projects based on Lean Six Sigma.
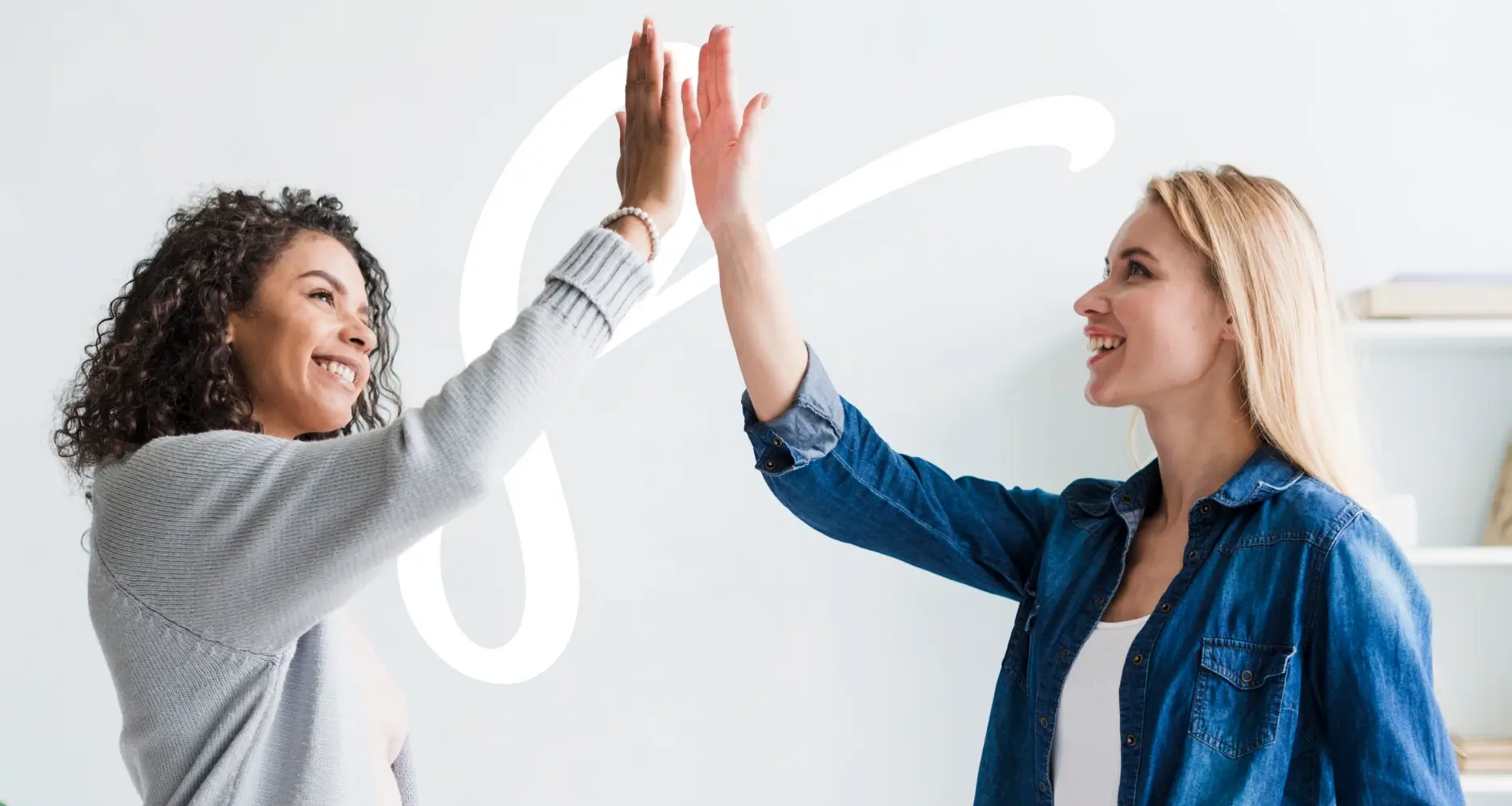
It is recommended to have completed the Lean Six Sigma Yellow Belt course or to have equivalent knowledge.
Training objectives
Analyze the data collected, extract relevant variables and manipulate hypothesis tests.
Design simple experimental plans to collect data.
Master process modeling and detect correlations between variables.
Pass the Lean Six Sigma Green Belt certification.
189Training program
Introduction and reminders
- The objectives of the Green Belt. The certification process.
- Reminders of the DMAIC approach. The fundamentals of Six Sigma.
- Reminders of the Lean principles. The different types of waste.
- Reminders of the
La phase "Analyze" - Analyser
- Variation models: multi-variance analysis and graph, application cases, interpretation of analysis data.
- Statistical inference: central limit theorem, standard error...
- Introduction to hypothesis testing: objectives, concept of central tendency, types of hypothesis testing...
- Hypothesis testing with normal data: sample sizes, hypothesis testing 'varied hypotheses on means, analysis...
- Hypothesis testing with non-normal data: equal variance data, medians, proportion tests, contingency.
The “Improve” phase – Improve
- Process modeling by regression.
- Advanced process modeling.
- Linear and non-linear regression.
- Multiple linear regression (MLR ).
- Introduction to the design of experiment.
- Describe the differences between the physical model and a design of experiment (DOE: Design Of Experiment).
- Explain an OFAT experiment and its weaknesses.
190The “Control” phase – Control
- Reminders: Lean control and tools, 5S, Kanban, Poke-Yoke...
- Reminders: Six Sigma control plan, cost-benefit analysis...
- Advanced experimentation: using the results of a DOE to determine the degree of process improvement.
- Capacity analysis: process capacity, selection of analysis method, interpretation...
- Fault control: prevention methods, tools and techniques...
- Presentation of SPC: Statistical Process Control.
- Describe the elements of an SPC graph and the objectives of the SPC graph.
- Describe the 9 steps of the methodology for implementing a control chart.
Preparing for and taking the certification exam
- Case study implementing the phases of the DMAIC.
- General revisions.
- Taking the exam: 100 questions, 3 hours.
★★★★★
- QST-68
- 2 Days (14 Hours)
Description
Who is this training for ?
For whom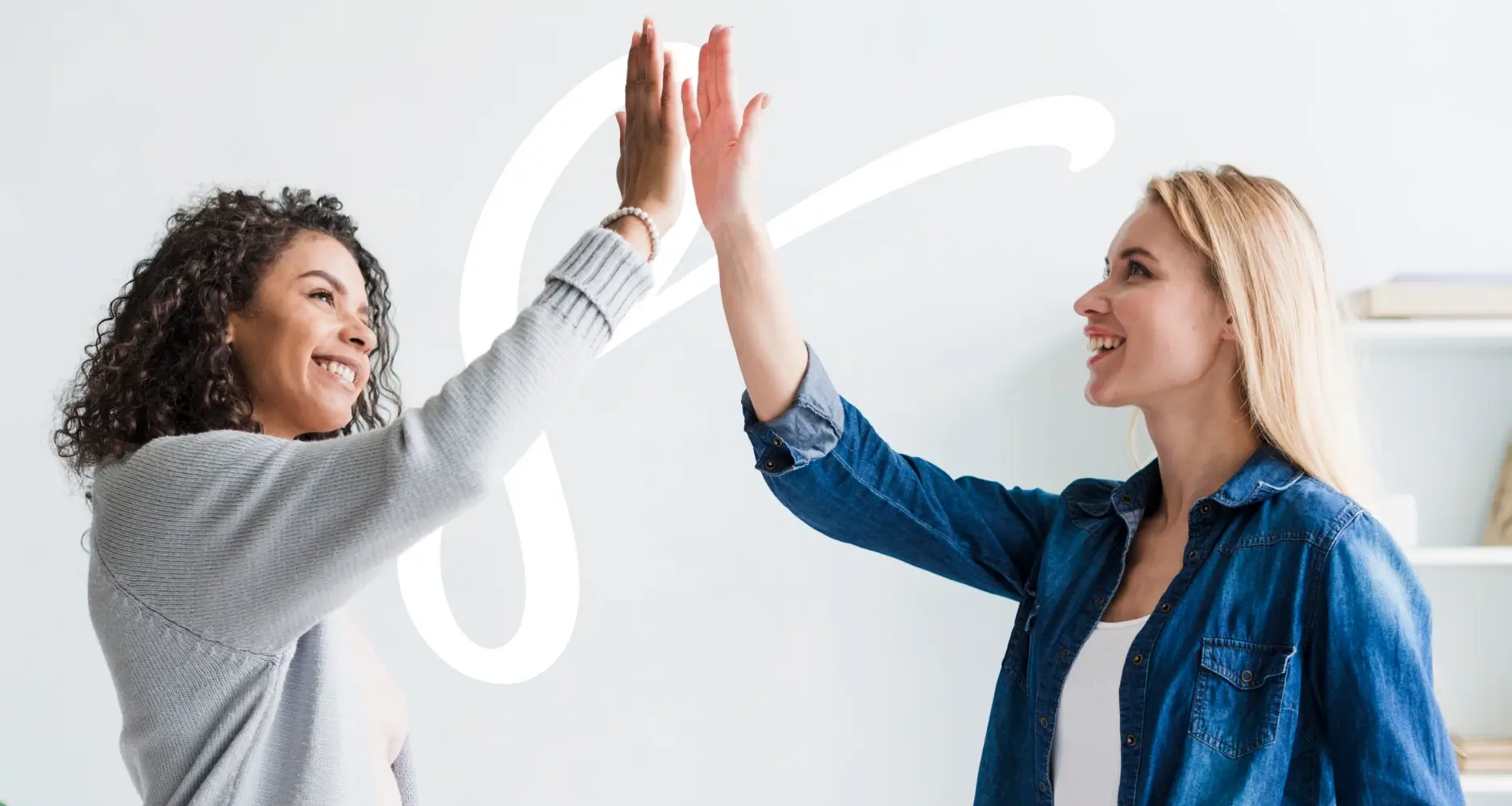
Training objectives
192193Training program
Introduction au Lean
- Presentation of Lean.
- The history of Lean.
- Understanding the mindset of Lean Management.
- Lean and continuous improvement approaches.
- The key elements of Lean.
- The notion of waste, variability and inflexibility.
- process model.
- The five dimensions of Lean IT.
- Collective reflection.
- Participants' reflection on what added value represents for them.
The customer
- Principle of added value for the customer.
- Voice of the customer: CRM tools, Kano diagram tool.
- Value-added work and non-value-added work .
- Critical elements of quality.
- Information systems value streams.
- Costs of poor quality.
- Exchanges: Arriving at a definition of added value.
194The process
- What is performance?
- Key performance indicators.
- The effectiveness of the operational process.
- Skills and the knowledge matrix.
- Exercise: Determining performance indicators.
The organization
- The client's organizational structure.
- Customer orientation.
- The performance dialogue.
- Visible management.
Problem solving, behavior and attitude
- Structured problem solving.
- DMAIC and problem solving.
- The Kaizen approach.
- Implementation of Kaizen projects.
- Lean Leadership & Behavior.
- Organizational change.
- The story of change.
- Exercise: Implementation of a problem solving method.
195Revision, exam preparation and certification
- Revision.
- Carrying out a mock exam and correction.
- Preparing for the exam.
- Practical work:r nCertification exam.
CRISC®, IS risk management, preparation for certification (Certified in Risk and Information Systems Control)
★★★★★
- QST-69
- 3 Days (21 Hours)
Description
This course is designed for professionals who want to pass the CRISC exam. The program covers the five key areas covered in the exam: risk identification, analysis and assessment, risk responses, risk monitoring, IS controls, IS controls life cycle.
Who is this training for ?
For whom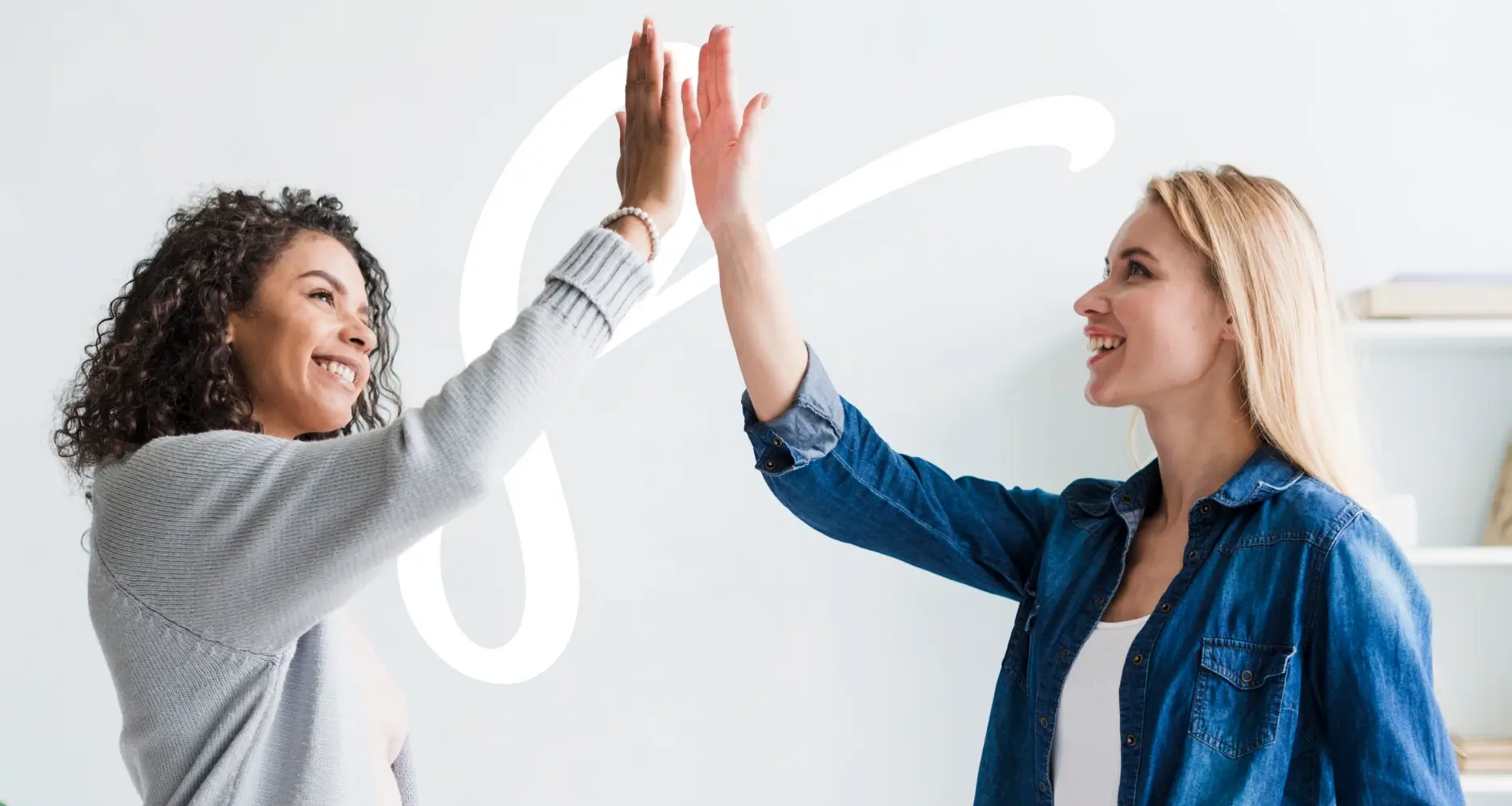
None
Training objectives
Master the risk management approach according to CRISC
Apply the best response strategies to the risks weighing on the information system
Use the best risk monitoring practices
Define information system controls
Use the best practices to monitor and maintain these controls
198Training program
Introduction au Certified in Risk and Information Systems Control
- General presentation of CRISC.
- Presentation of the exam model and the certification process.
Domain 1: identification, analysis and assessment of risk
- Risk management standards: ISO 31000, ISO 27005...
- Risk management standards: RISK IT, COSO ERM, COBIT...
- Components, principles and concepts of enterprise risk management.
- Risks at different levels of the enterprise.
- Risk identification methods.
- Risk analysis and assessment methods.
- Quantitative and qualitative risk analyses.
Domain 2: responses to risk
- Risk treatment methods.
- Risk mitigation and information system control.
- Risk reduction.
- Transfer of risk.
- Acceptance of residual risks.
- Risk treatment plans.
199Domain 3: Risk monitoring
- Risk treatment life cycle.
- Monitoring treated risks.
- Monitoring residual risks.
- Performance evaluation of the risk management and risk reporting.
- Key risk indicators (KRI).
- Risk management & business resilience.
Domain 4: Information system controls
- Definition of IS controls.
- Implementation of IS controls.
- Measurement of processes and services related to IS controls.
Domain 5: life cycle of IS controls
- Strategic planning for life cycle management of IS controls.
- Scope, objectives and benefits of life cycle management programs for IS controls.
- Continuous monitoring of IS controls.
- Maintenance of IS controls.
- Continuous improvement of risk management and IS controls.
- Reporting periodic review of the effectiveness of IS controls.
200Preparing for the exam
- Discussions and exchanges.
- Good practices for passing the exam.
- Exam simulation and collective correction.
- Mock exam .
M_o_R®, Risk Management, Practitioner, certification
★★★★★
- QST-70
- 2 Days (14 Hours)
Description
M_o_R® practices address the risks facing an organization at the strategic, program, project and operational levels. This internship will allow you to consolidate your knowledge of this framework and also prepare you for the M_o_R Practitioner level certification from APMG.
Who is this training for ?
For whom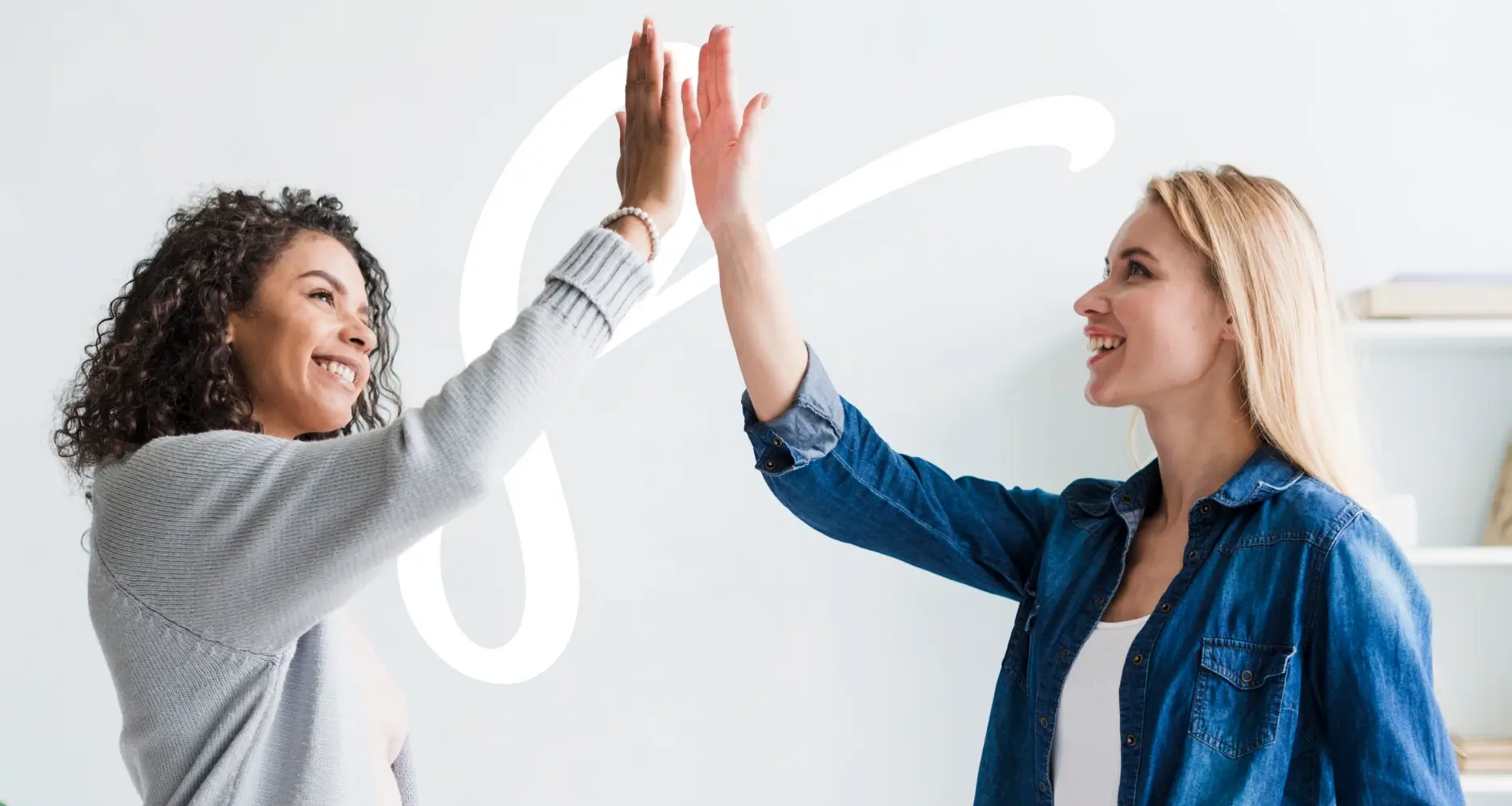
None
Training objectives
Define the key principles of effective risk management
Apply the main components of the M_o_R® risk management process
Know how to manage risks at the strategic level, at the program and project level, and at the operational level
Identify techniques useful in the different stages of the risk management process
203Training program
Introduction to M_o_R® Practitioner
- Reminders of M_o_R® objectives.
- Specific objectives of M_o_R Practitioner.
- The M_o_R® Practitioner certification exam.
- Preparation tips.
- Presentation of the official M_o_R® manual.
- The M_o_R® approach to risk management.
- Identify the benefits provided by M_o_R ®.
- Exchanges Exchanges on the practice of risk management in different organizational contexts.
- Use of the M_o_R® framework and its contributions.
The princes of M_o_R®
- Details of the eight principles of M_o_R®.
- The benefits associated with the application of these principles.
- The mechanisms that support these principles: KPI, EWI, tolerance threshold, stakeholders, maturity model.
- The adaptation of the principles to the practice of risk management in a specific organizational context.
- The role of communication and stakeholders in a risk management process according to M_o_R®.
204The M_o_R® approach, the content of the reference documents
- The risk management policy.
- The process guide.
- The risk management strategy.
- The risk register and the problem register.
- The risk management improvement plan.
- The communication plan.
- The risk response plan.
- Organizational factors to consider when creating M_o_R® reference documents.
The prospects of M_o_R®
- The integrated approach to risk management through perspectives (strategic, program, project, operation).
- The performance of the process of measuring the added value of risk management .
- Adapt the M_o_R® model to the specificities of the organization for the four perspectives.
- Identify the appropriate actions, techniques, roles and responsibilities for the implementation of the M_o_R® model .
- Useful techniques: Delphi, hypothesis analysis, constraint analysis.
Generation Y: good managerial practices
★★★★★
- QST-72
- 2 Days (14 Hours)
Description
Understanding the specificities of the new generations (Y) is becoming essential for any manager. Beyond this understanding, this training will allow you to find the appropriate posture for successful collaboration.
Who is this training for ?
For whom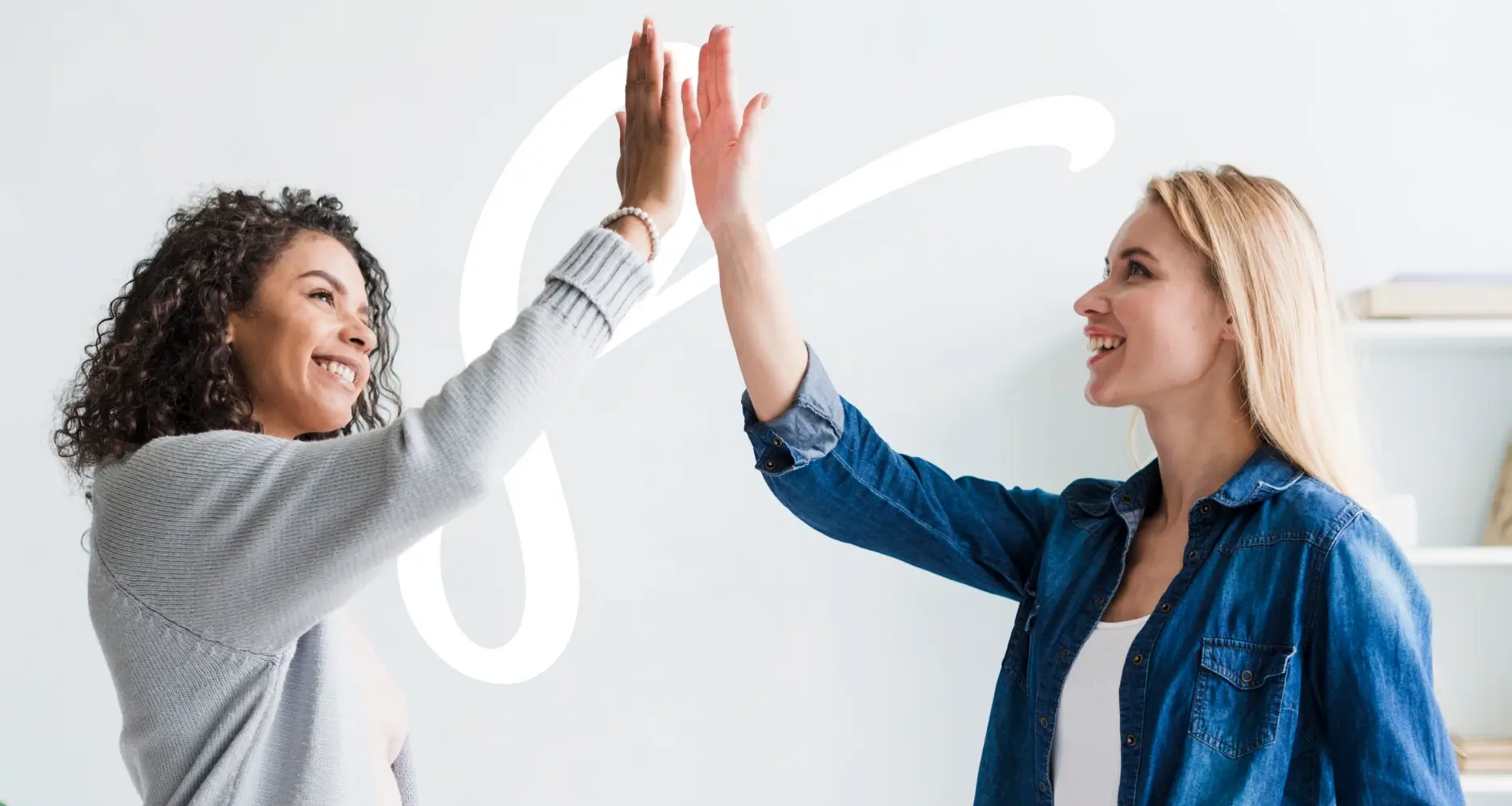
None
Training objectives
Understand the expectations and motivations of Generation Y at work
Build relationships based on common values
Adopt a managerial posture adapted to Generation Y
Strengthen the cohesion of an intergenerational team
207Training program
Understanding the “Y”s
- Awareness of transgenerational differences.
- Understand the "Y" in relation to work and the company, their values.
- Integrate relational modes of the Y, their relationship to hierarchy, to authority.
- Understand the real motivations of the new generation regarding the company.
- Exercise: Discussion-debate : my role as manager facing the "Y".
Communicate effectively and find the right posture when facing the “Y”
- Find an appropriate posture taking into account the expectations of "Y".
- Search for source information for effective communication.
- Understand limiting representations .
- Know how to question oneself in the relationship with others, be open.
- Use the difference to strengthen the relationship.
- Exercise: rnAdapt your mode of communication to the situation and the interlocutor.
208Find a suitable management method, create cohesion
- Dare new ways of managing.
- Know the motivational levers.
- Do not fight against difference, but build with it.
- Learn to co-build with the new generation.
- Know how to manage the tensions linked to differences.
- Allow the team to integrate new elements.
- Know use the strengths and skills of "Y".
- Find team cohesion that takes differences into account.
- Exercise: Invent new managerial methods.
- Role games: put yourself in the place of "Y" to better understand their reactions and behavior towards the manager.
Analyze your own managerial practices
- Understand what manager I am.
- Enrich your practices with the contribution of training while respecting your style.
- Know how to reconcile your own challenges, those of
- Exercise: rnAnalysis of managerial practices based on real-life experiences.
Integrate and manage generation Z how to bet on the new generation
★★★★★
- QST-73
- 2 Days (14 Hours)
Description
This training will allow you to better understand Generation Z, their values, their needs, their expectations to better motivate them. She will show you how to apply appropriate management methods to them.
Who is this training for ?
For whom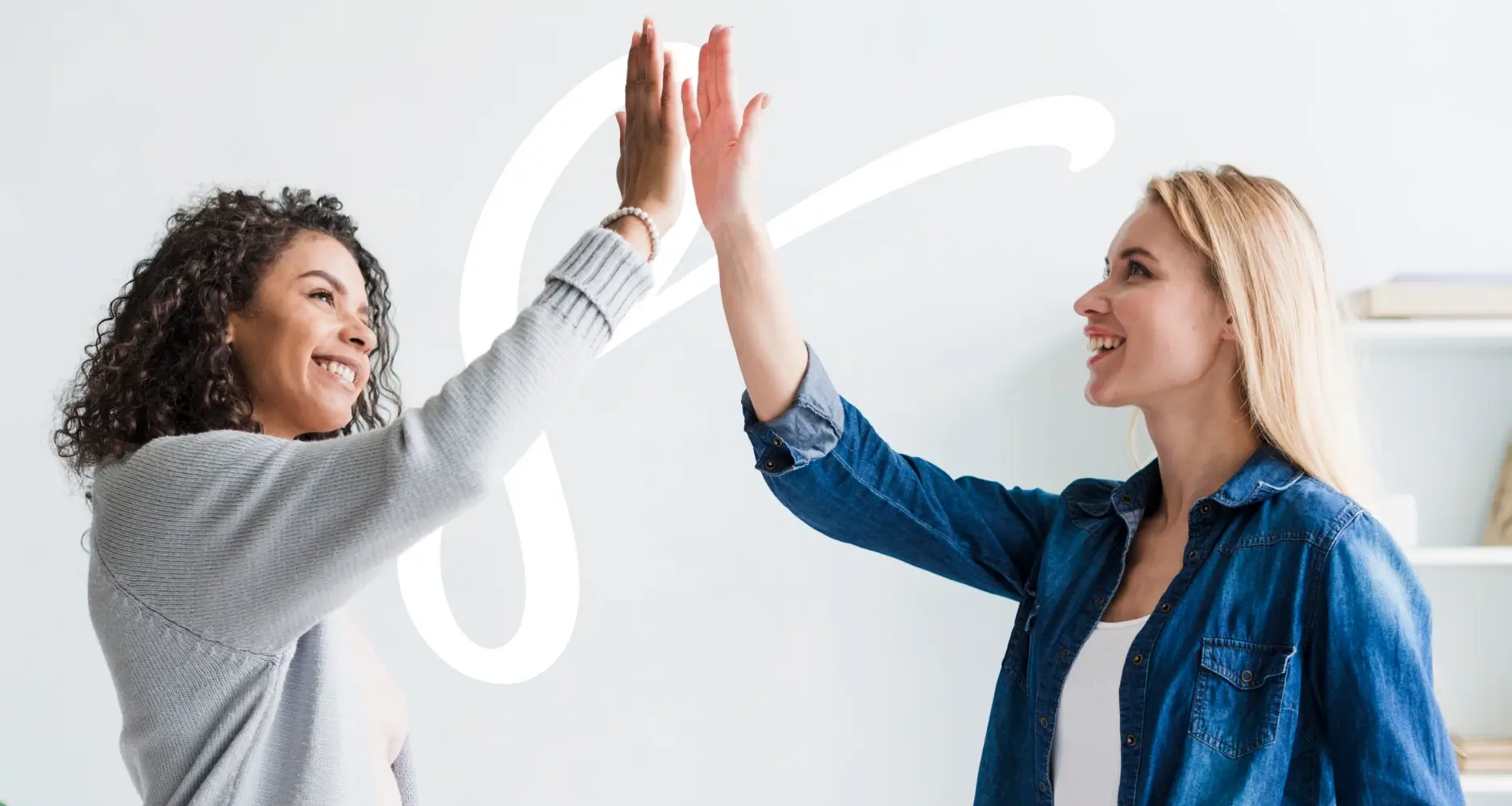
None
Training objectives
Understand the ways Generation Z operates at work
Choose a flexible and personalized mode of communication
Successfully integrate Generation Z into a team
Act on motivation levers adapted to “Z”Manage delicate situations
211Training program
Understanding Generation Z in Business
- Analyze behavior: sociological and cognitive approach.
- Take a new look at the Z.
- Understand the relational mode of the Z and their relationship to the hierarchy.
- Comparative study of Z with other generations.
- Collective reflection Exchanges on the characteristic traits of generation Z.
Communicate effectively with Z
- Know how to create real contact with the Z.
- Develop a circular, flexible and adaptable mode of communication.
- Make your communication with the Z a strategic asset .
- Make difference an effective lever.
- Dare to invent new modes of communication.
- Role play Develop a mode of interaction effective with the Z.
- Collective debriefing.
212Integrate the Zs into the teams
- Investing in the complementarity of actors.
- Dare to bet on the advantage of the Z in the company of tomorrow.
- Know how to manage transgenerational conflicts, create partnerships.
- Play the adapted integration card.
- Practical work Case study: from a given scenario, identify innovative solutions for integrating Generation Z.
- Role play: effectively manage transgenerational conflicts.
- Collective debriefing.
Understand how to motivate Z
- Understand the real sources of motivation and integrate them.
- Make the link between weak and strong signals and motivation levers.
- Reconcile the motivation of Z and the needs of the company.
- Collective reflection Theoretical contribution followed by reflection on the links between personal motivation and the needs of the organization.
Managing Generation Z on a daily basis
- Manage new behaviors effectively.
- Know how to use appropriate management methods.
- Know how to take responsibility and reframe the Zs without creating blockages.
- Effectively manage tense situations with Z.
- Practical work rnWorkshops on real cases contributed by the trainees.
- Sharing experiences.
CSR communication: enhancing the image of your company responsibility for the message, support and dissemination
★★★★★
- QST-80
- 2 Days (14 Hours)
Description
This course will show you how to develop an effective CSR communication strategy. After discovering the challenges of this type of communication, you will see how to avoid the main pitfalls and implement the appropriate approach and tools.
Who is this training for ?
For whomCommunication managers and managers (companies, associations, NGOs, administrations, communities, etc.).
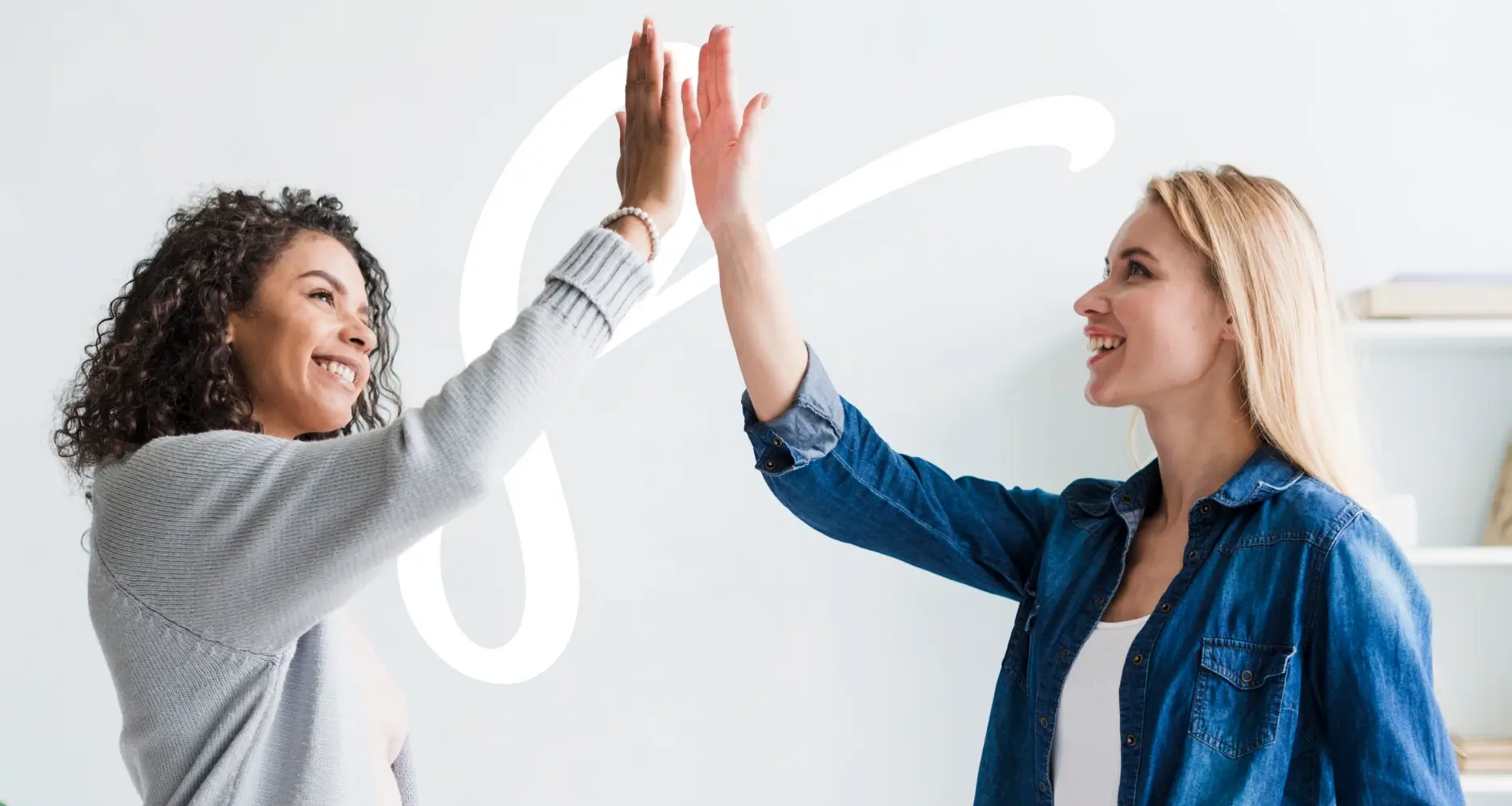
None
Training objectives
Identify your role and its limits in a CSR approach
Define the objectives of CSR communication
Choose the focus of your CSR communication
Select the media for your communication
215Training program
Understand the context of CSR and sustainable development (SD)
- Definition and principles of SD, CSR and responsible communication.
- Environmental awareness.
- The influence of NGOs.
- What are the consequences of this changing society for the company? Why communicate on its CSR? Example International benchmark.
Develop a responsible organizational approach
- What role for the communications department in a CSR approach?rnKnow the regulations and standards (ISO 26000, ISO 14001, ISO 20121).
- Responsibility for the message, support and dissemination.
- Focus: how to avoid Greenwashing?rnThe method of 3 prerequisites and 3 stages: message, support and control.
- The governance of organization for a responsible communication strategy.
- Evaluation and control.
- Exercise: rnLabels, product labels and claims.
- How to identify yourself? What perception do you have of your company's CSR? What impact in terms of communication?
Define the objectives of your CSR communication
- What are the goals to achieve? Conduct an analysis and define them.
- Identify your stakeholders.
- Build your positioning.
- Choose coherent lines of communication.
- More information, less dreams.
- Collective reflection Examples and discussions on good and bad practices.
216Define what to communicate and on what media
- Mobilize internally on the CSR approach.
- Highlight the company's commitment to stakeholders, product and service offerings.
- CSR content strategies On and Offline, the opportunity of Web 2.
- 0.
- Know the different elements of the CSR report.
- The public relations: what angle of attack for which media? What distribution? The case of advertising on CSR and sustainable development.
- Recommendations for eco-socio-responsible media.
- Life cycle analysis tools.
- How to select your partners and subcontractors for a lasting relationship? Case study Case study based on the examples of the participants and the communication actions resulting from the activity.
Managing through quality processes
★★★★★
- QST-81
- 2 Days (14 Hours)
Description
Course focused on the management and communication in transversal management of the different typologies of Quality processes, in relation to the ISO 9001 standard. Study of their environments and interactions, development of methods of creation, monitoring and optimization, priority management.
Who is this training for ?
For whomQuality manager, process manager, quality facilitator, internal auditor.
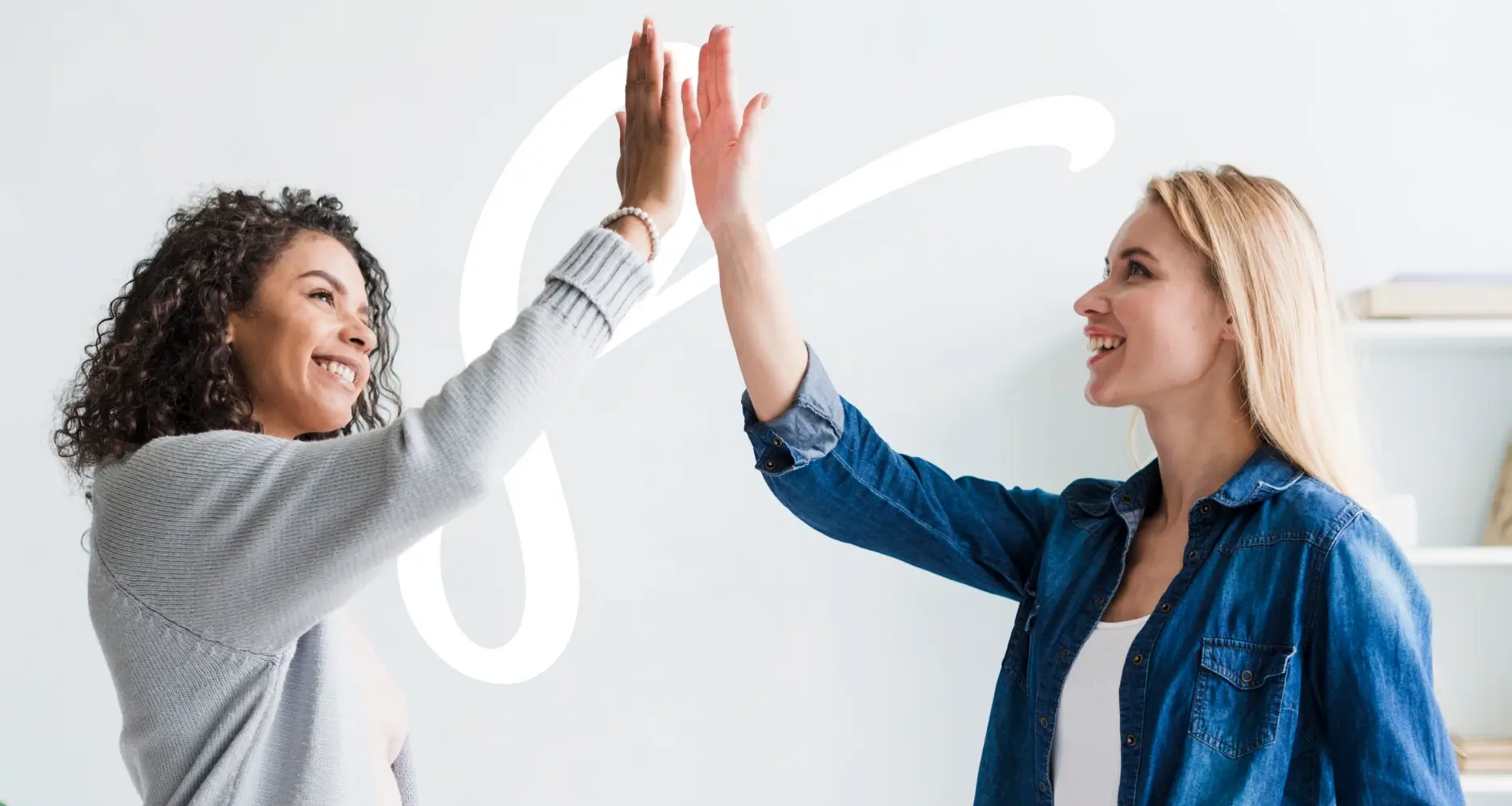
No special knowledge.
Training objectives
Understand the concept of the process approach in the organization of the company
Know how to identify and describe processes
Manage company processes using relevant indicators
Understand transversal management (management pilot process)
Be able to optimize processes by creating value
219Training program
Understanding the process approach
- Share an understanding of organizations and management methods.
- Understand the concept of the process approach, decompartmentalization of the business.
- Identify the typologies of processes and represent their mapping.
- Model the interrelationships and develop the internal customer/supplier relationship.
- Practical workrnIn subgroups: Develop the process mapping of 'a typical company and identify the interrelationships.'}
Create processes
- Define a process and delimit its scope.
- Determine the flows and analyze the interrelations.
- Identify and represent the activities of the process: flowchart, identity card .
- Apply the principle of functional analysis to structure and describe the process.
- Define the roles and responsibilities of stakeholders: RACI method.
- Give yourself measuring points to manage calmly.
- Practical work In sub-groups: Formalize a typical company process, define the interactions and fill in the RACI.
Managing by process (transversal management)
- Understand the fundamentals of management and identify manager styles.
- Identify the differences between hierarchical and transversal management.
- Share and define the role of management pilot process, mission, responsibility, authority, interpersonal skills.
- Determine the key actions for successful management: conduct process reviews, build a maturity grid.
- Practical work rnIn subgroups: share situations experienced in the company.
220Optimize processes
- Anchor the problem-solving method in the functioning of the process (PDCA method).
- Structure an action plan to monitor progress and evaluate effectiveness.
- Integrate opportunity and risk management into processes (SWOT matrix).
- Determine the criticality of the process to better anticipate.
- Create the conditions to innovate and improve performance.
- Practical work In a subgroup: identify the opportunities and risks of a process.
ISO 9001, quality, Foundation, certification
★★★★★
- QST-82
- 2 Days (14 Hours)
Description
This course will allow you to become aware of the concepts and good practices for implementing a Quality Management System as specified in ISO 9001:2015 as well as in ISO 9004:2009 and pass the Foundation certification.
Who is this training for ?
For whomMembers of a quality team, personnel involved in the implementation of the ISO 9001 standard or in operations linked to a QMS, auditors.
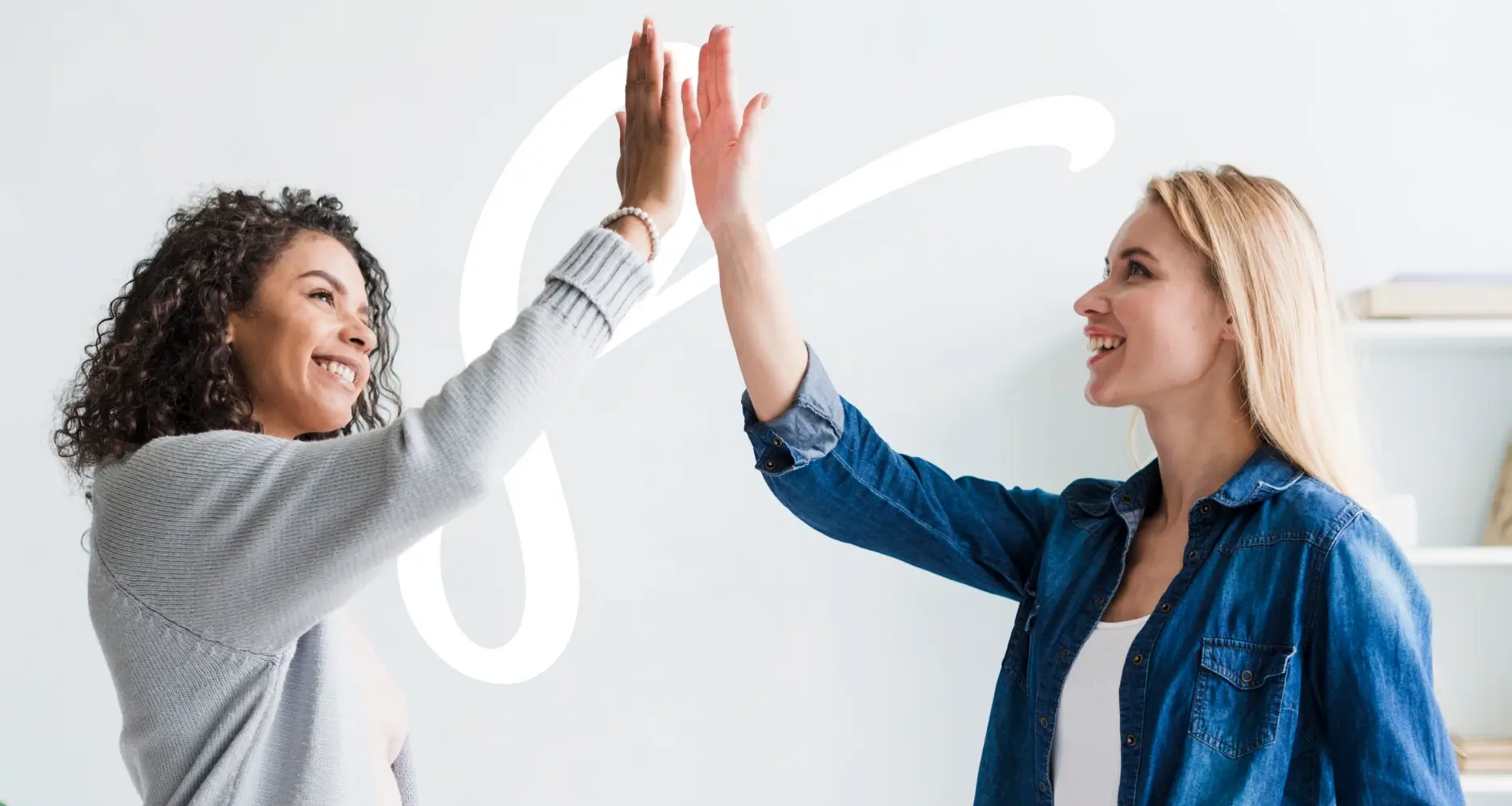
None
Training objectives
Understand the challenges of a Quality Management System
Interpret the ISO 9001 standard Know the essential aspects of implementation
Prepare for the ISO 9001 Foundation certification exam
223Training program
Introduction to ISO 9001 Quality Management System concepts
- Introduction to the ISO 9001 family of standards.
- Introduction to management systems and the process approach.
- Understanding the fundamental principles of quality management .
- Know the general requirements: presentation of clauses 4 to 8 of ISO 9001.
- Management responsibility: presentation of chapter 5.
- Resource management: presentation of chapter 6Production of the product: presentation of chapter 7.
- Measuring analysis and continuous improvement: presentation of chapter 8.
Implement requirements consistent with ISO 9001:2015
- Selection of the approach and methodology implemented within the ISO 9001 framework.
- Identification and analysis of customer needs and requirements.
- Implementation work of document management.
- Follow the process of resource management, product production and purchasing.
- Control and monitor a Quality Management System.
- Measure customer satisfaction.
- Conduct an internal ISO 9001 audit and carry out the management review of the Quality Management System.
- Implementation of a continuous improvement program.
- Preparation for the ISO 9001 certification audit and plan for registration with a certification body.
224Examen Certified ISO 9001 Foundation
- Domain 1: Fundamental principles and concepts of quality.
- Domain 2: Quality Management System (QMS).
ISO 9001 Lead Implementer, ''QUALITY MANAGEMENT''
★★★★★
- QST-87
- 5 Days (35 Hours)
Description
This intensive course will provide you with the expertise necessary to assist an organization in the implementation and management of a Quality Management System (QMS) as specified in ISO 9001:2015. At the end, you will be able to take the Lead Implementer certification exam.
Who is this training for ?
For whom- Quality Management Systems (QMS)
- Certification auditors
- Project managers or consultants
- Responsible persons or members of a quality team in an organization.
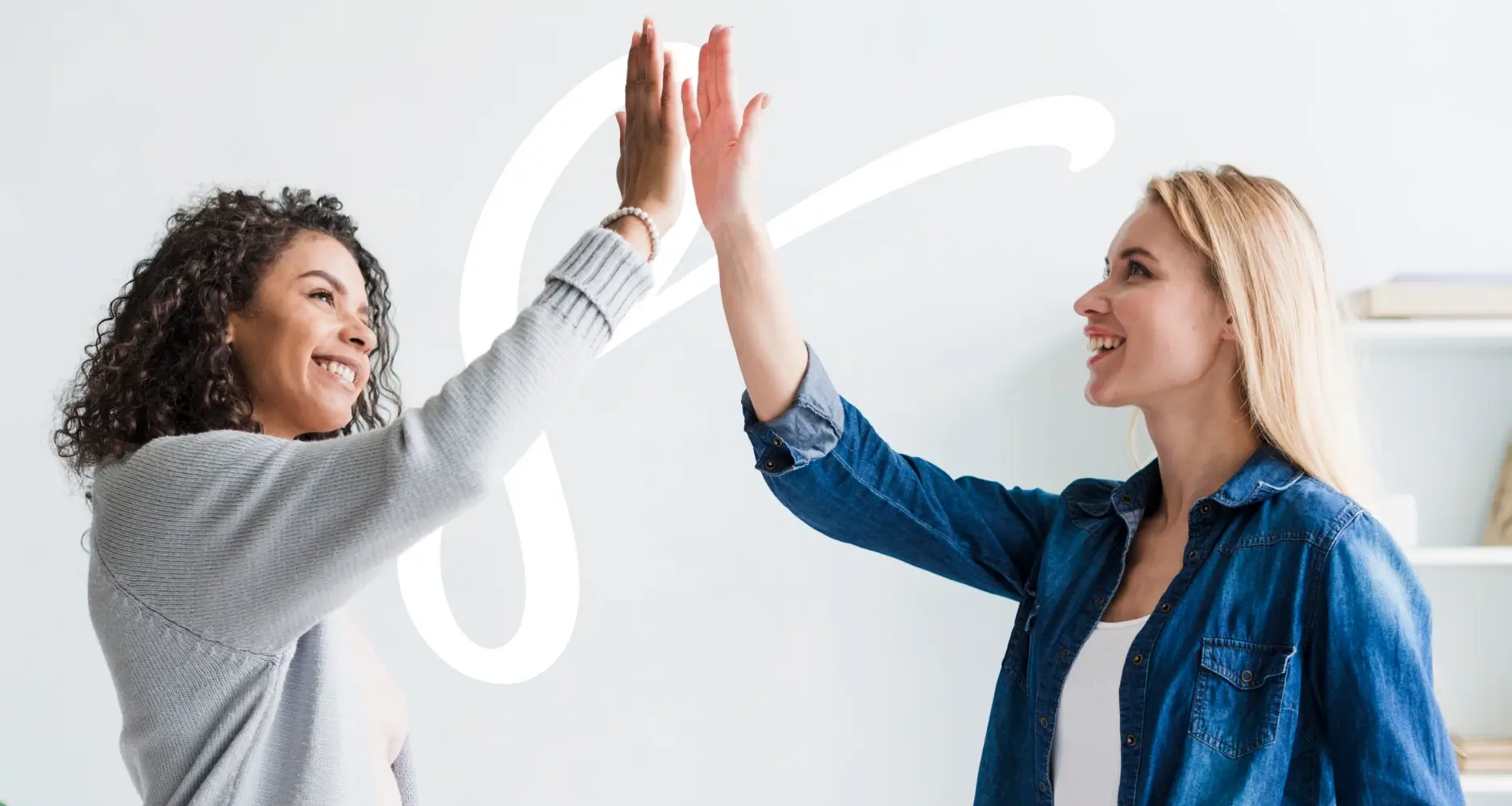
Training objectives
- This training program aims to provide participants with an in-depth understanding of ISO 9001 and its relationship to other standards and regulatory frameworks
Participants will learn to master the concepts, approaches, methods and techniques necessary to effectively implement and manage a QMS - Participants will also gain the ability to interpret the requirements of ISO 9001 in the specific context of the organization
They will be able to support an organization in planning, implementing, managing, monitoring and updating the QMS - Finally, participants will gain the expertise necessary to advise an organization on the implementation of best practices relating to the Quality Management System
They will be able to guide the organization in implementing effective processes and ensuring that the requirements of ISO 9001 are met - At the end of the training, participants will be ready to apply their knowledge to help an organization achieve excellence in quality and process management
227Training program
Introduction to the concept of ISO 9001 Quality Management System
- This introductory program aims to provide an in-depth understanding of management systems, the process approach and the fundamental principles of quality. It also introduces the ISO 9000 standards and the requirements of ISO 9001 The practical work includes the analysis of the reasons for implementing the standard, the exploration of quality tools, the application of ISO management principles to quality and the interpretation of the clauses.
Start of an ISO 9001 Quality Management System project.
- The selection of the approach and methodology is implemented.
- The identification and analysis of customer needs and requirements are necessary.
- It is essential to write a feasibility study and a project plan for a QMS.
- The implementation of document management is crucial.
- Writing a QMS must be carried out carefully.
- Practical work includes establishing specific objectives, preparing a QMS project, defining a scope and writing a quality policy.
Implement an ISO 9001 QMS
- Development of a training, awareness and communication program on quality.
- Resource management process.
- Product production process and purchasing.
- Operational management of a QMS.
- Practical work: Training and awareness plan, problem solving, process improvement, management operations 'a QMS.
228Controlling, monitoring, measuring and improving are necessary actions for a QMS.
- Control and monitoring are essential for managing a QMS.
- Measuring customer satisfaction is a key indicator for evaluating the effectiveness of the system.
- The ISO 9001 internal audit makes it possible to verify the conformity of the QMS with the requirements of the standard.
- The management review is a crucial step in evaluating the performance of the QMS.
- Implementing a continuous improvement program is a proactive approach to improving quality.
- Preparing for the certification audit is necessary to obtain ISO 9001 certification.
- A plan for registration with a certification body must be established to begin the certification process.
- Practical work includes the use of quality control tools, measuring customer satisfaction, carrying out internal audits and developing corrective action plans.
Certification exam
- Domain 1: Fundamental principles and concepts of quality.
- Domain 2: Quality code of practice.
- Domain 3: Planning an ISO 9001 QMS .
- Domain 4: Implement an ISO 9001 QMS.
- Domain 5: Performance evaluation, monitoring and measurement.
- Domain 6: Continuous improvement of an ISO 9001 QMS.
- Domain 7: Preparation for the certification audit.
- Practical work: 3-hour exam.
Build and manage an integrated QSE system
★★★★★
- QST-76
- 2 Days (14 Hours)
Description
This training will allow you to understand the ISO 9001, ISO 14001 and OHSAS 18001 standards. You will model the approach to building an integrated QSE system and will be able to lead a QSE project within your company.
Who is this training for ?
For whom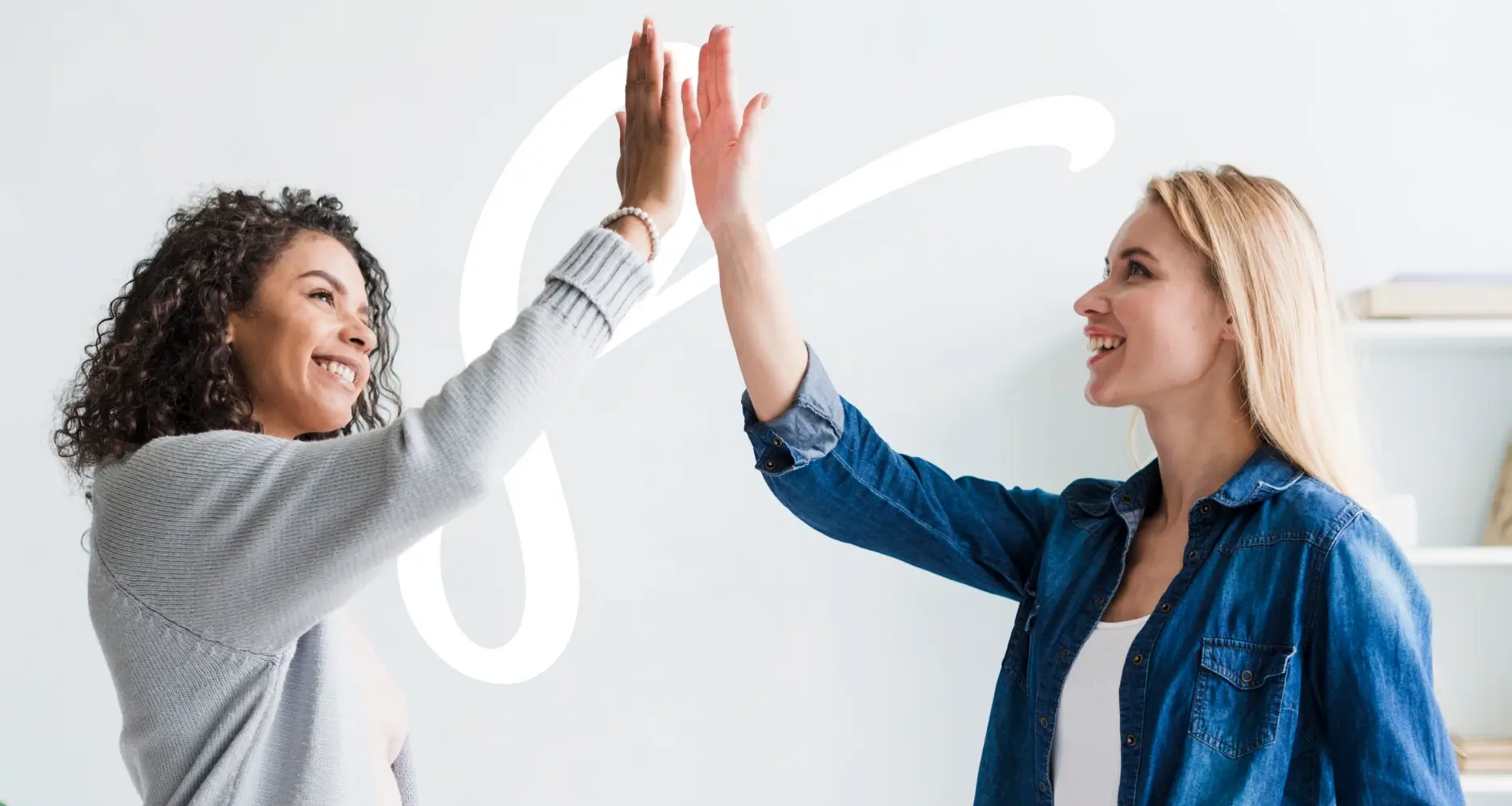
None
Training objectives
Define and understand the principles and issues of an integrated QSE system
Identify the main quality standards and their specificities
Model and frame the approach to building an integrated QSE system
Deploy and manage the integrated QSE system in your organization
231Training program
Foundations and purposes of an integrated QSE system
- Definition of an integrated QSE system.
- Understand the purpose and challenges of such a system for the company.
- Identify the key players, their level of involvement and their role.
- Understand the current state of the organization in place.
- Collective reflection Exchanges with participants on the situation in their company .
Distinguish the three integrated repositories
- Understand the elements common to QSE standards (ISO 9001, ISO 14001, OHSAS 18001).
- Know the specificities of ISO 14001.
- Know the specificities of OHSAS 18001.
- Practical work In subgroups, identification and synthesis of requirements on the three standards, restitution and consolidation.
Build the QSE system structure
- Carry out the initial diagnosis necessary for building the QSE system.
- Map the processes within the framework of the QSE approach.
- Define the documentary structure of the 'company.
- Determine a sustainable organization of the QSE management system.
- Select the documents to create and those to modify.
- Plan the updating steps level to achieve the objectives of the QSE project.
- Constitute, structure and write a pragmatic QSE manual.
- Practical work In subgroups, description of the system, planning and communication , restitution and consolidation of the concept.
232Managing your new integrated system
- Draft the QSE Management System steering dashboard.
- Structure an action plan.
- Monitor and evaluate its effectiveness.
- Determine the communication adapted to the deployment of the system.
- Evaluate the effectiveness of the QSE management system, conduct process reviews.
- Practical work Below groups, creation of the dashboard, role plays, animation of the QSE management review, restitution and consolidation of the concept.
Managing good communication practices in the health and medico-social sector
★★★★★
- QST-77
- 3 Days (21 Hours)
Description
Communication is a management lever that impacts the quality of life at work, the prevention of psychosocial risks and collective performance. This training will allow you to master the main techniques for effectively conveying your messages and managing conflicts.
Who is this training for ?
For whom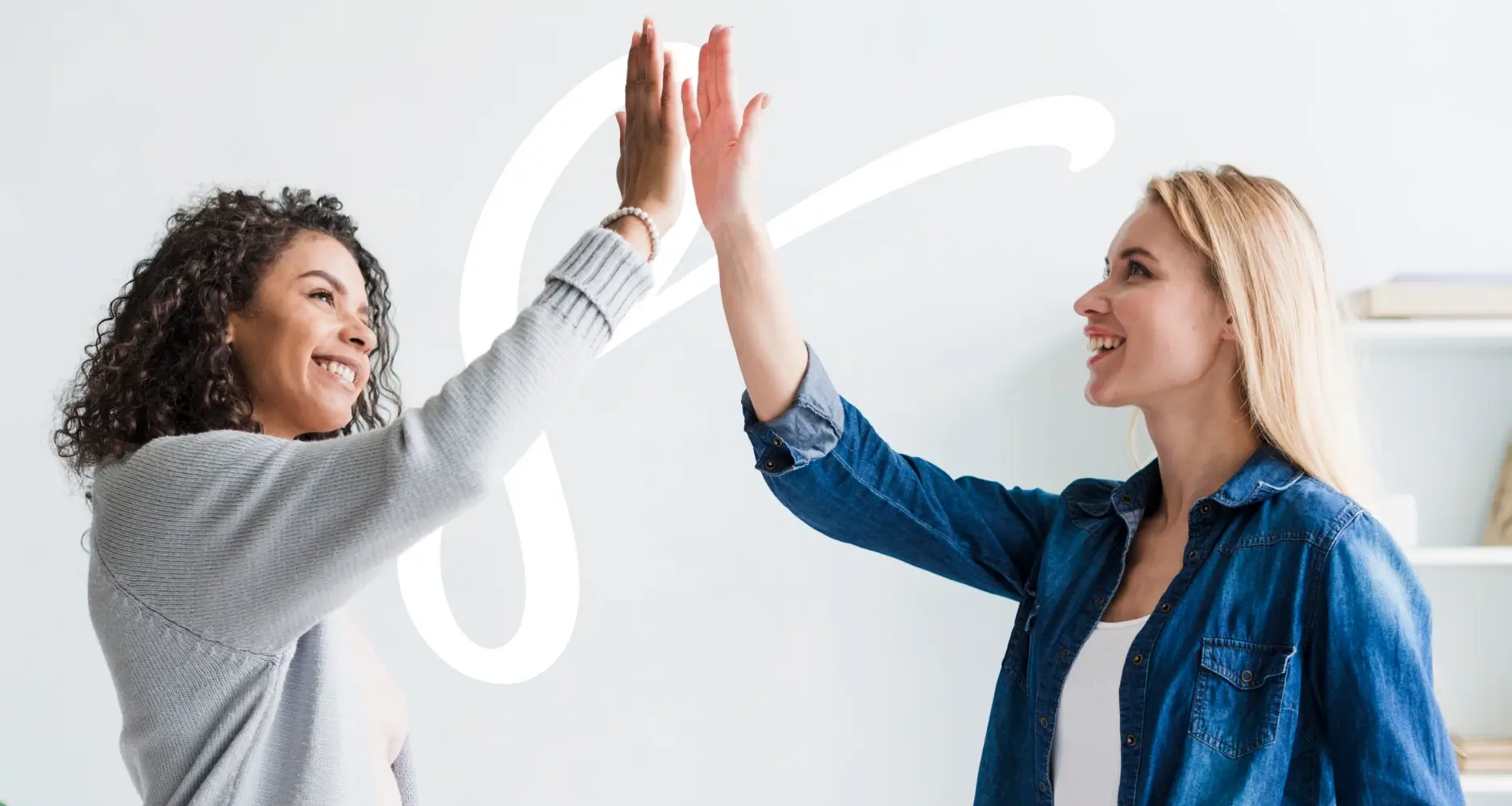
None
Training objectives
Develop effective communication adapted to your management context
Acquire skills and tools useful for good managerial communication
Master the emotional dimension of communication
Know how to communicate in your daily life as a manager and in difficult situations
235Training program
Develop your posture as a “communicating manager”
- Identify your preferred mode of communication.
- Identify your listening style according to Porter's study.
- Increase your potential and identify your areas of progress.
- Measure the impact of managerial communication on work efficiency.
- Identify good managerial communication practices.
- Practical work Self-diagnosis on his preferred mode of communication.
- Case study of interpersonal communication.
Optimize communication with colleagues
- Identify the communicator typologies of your employees.
- Discern the needs of your employees: the MASLOW pyramid.
- Appropriate the principles of non-public communication violent (C.
- N.
- V).
- Practice active listening techniques to communicate well.
- Take into account takes into account non-verbal communication.
- Practical work Behavioral scenarios on active listening and non-violent communication techniques.
- Video: analyzing the semiology of communication non-verbal.
236Master the emotional dimension of managerial communication
- Define the role of emotion in managerial communication.
- Analyze our emotional reactions and those of our employees: main strengths and obstacles.
- Understand the messages delivered by emotions to create connections and communicate better.
- Practice managing emotions on a daily basis.
- Practical work Case study on emotions and their manifestations at work .
- Exercise: anchoring.
- Role playing: deciphering emotions and identifying associated behaviors.
Knowing how to communicate in your daily life as a manager
- Communicate in difficult situations with tool D.
- E.
- S.
- C.
- Know how to say no.
- Practice the reframing interview and feedback techniques.
- Know how to break bad news to a colleague or their group.
- Write your individual action plan: set objectives and desired results.
- Scenarios Scenarios filmed based on real-life professional scenarios.
- Debriefing in a group on the behaviors implemented.
HACCP method in health establishments food hygiene
★★★★★
- QST-87
- 2 Days (14 Hours)
Description
The HACCP system is a method of controlling food safety. This training will allow you to meet the requirements of the law and to implement this method of defining, evaluating and controlling the dangers that threaten the health and safety of food.
Who is this training for ?
For whomHealth and catering staff.
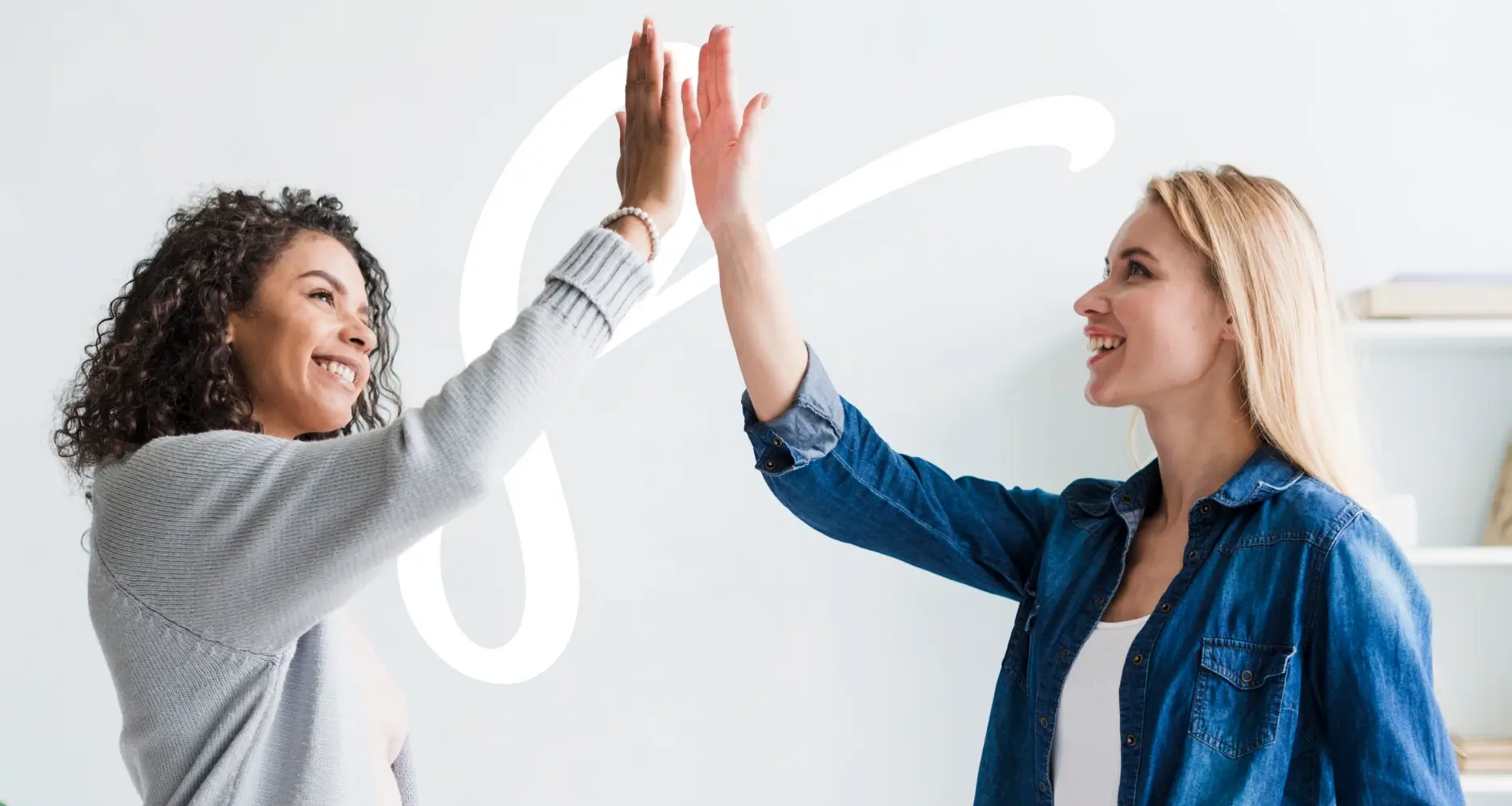
None
Training objectives
Understand and master the rules of food hygiene
Understand the importance of the HACCP method and put it into practice
Build a HACCP plan in its 12 steps
Analyze the risks and implement the necessary measures to mitigate food risks
239Training program
Understand the legislation governing the HACCP method
- First definitions: bacteriology and the main rules of food hygiene.
- The "hygiene package" and other European regulations.
- The principle of
- The responsibility of the actors.
- The new health inspection provisions.
- The documents to be produced during an inspection.
- Collective reflectionrnPractical illustrations on the interpretation of texts.
Know and control dietary risk factors
- The five main sources of contamination.
- The multiplication factors of micro-organisms.
- Responsible behavior: clothing, personal hygiene, state of health, hands, PPE.
- Obligations relating to the environment and its maintenance: premises, circuits and equipment.
- Compliance and maintenance of equipment (equipment manufacturing and distribution).
- Methods: rational organization of work, respect for the hot and cold chain.
- Raw materials: storage temperatures, management used oils.
- Collective reflection Individual and collective reflections on hygiene rules and responsible behavior.
240Understand and apply the HACCP method
- Developing and verifying manufacturing diagrams.
- Identify and classify critical points.
- Establish limits and thresholds.
- Create documents allowing readings and recording.
- HACCP evaluation.
- Scenario Implementation based on a situation provided by the trainer.
- Linking with the participants' practice.
Implement the HACCP method
- Developing and verifying manufacturing diagrams.
- Identify and classify critical points.
- Establish limits and thresholds.
- Create documents allowing readings and recording.
- HACCP evaluation.
- Scenario Implementation based on a situation provided by the trainer.
- Linking with the participants' practice.
Quality and safety of care preparation for V 2014 certification
★★★★★
- QST-79
- 3 Days (21 Hours)
Description
This training will allow you to prepare effectively for obtaining V2014 health establishment certification. You will discover the new features and learn to respect the requirements, particularly in terms of operational expectations and production elements expected by the surveyors.
Who is this training for ?
For whom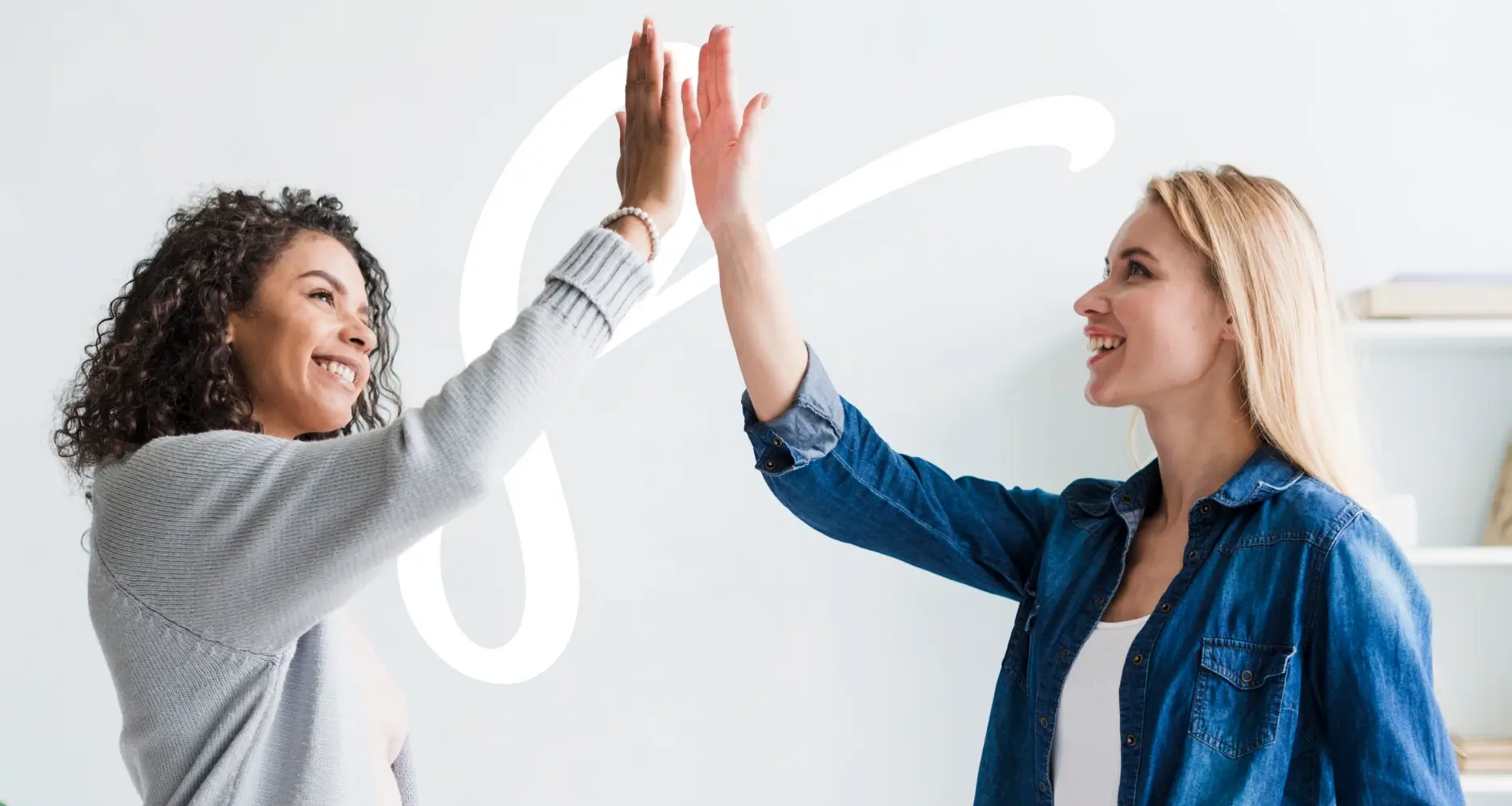
None
Training objectives
Know and understand the level of requirements of V2014
Identify the developments to be integrated into the quality approach of establishments
Understand and take into account the new expectations of the HAS
243Training program
Understand the specificities of the V2014 certification process
- Introduction: history, issues and societal aspects of the certification process.
- Certifications: from V1 to V4.
- The new principles and issues of HAS certification version 2014.
- The principles of the continuous improvement cycle: plan, implement, evaluate and improve.
- The integration of quality into daily tasks and routines of the teams.
- Risk management in V2014: the different risk profiles.
- The results for the establishments.
- Collective reflectionr nEthical reflection around the concept of
Find out what's new in the certification of health establishments
- Required Priority Practices (PEP).
- Evaluation of Professional Practices (EPP): EPP and V2014, the practical implementation of the EPP in hospitals.
- Clinical practice indicators: mapping, framing.
- Implementation of the "Patient-Tracers" methodology.
- Implementation of "Crex Ressources Management".
- Risk management methods and tools.
- Practical work Exercise: role-playing allowing you to master the different approaches and their associated tools, for EPP.
- Analysis of the root causes of adverse events.
244Develop the roadmap to prepare for your establishment
- The V2014 retro planning.
- The quality communication plan.
- Self-assessment: the method of filling out the grids, the particular case of references in link with the EPP.
- The production elements expected in accordance with the methodological and calendar aspects.
- Practical work Application of the tools covered.
Welcome the experts
- Preparing employees and bodies for the visit.
- The requirements of visiting experts: the key points to master and the errors/pitfalls to avoid.
- The course of the visit: from the opening meeting to the restitution.
- The conclusions of the visit.
- Exercise: Creation of a summary sheet covering the points keys to training.
Improving hygiene in health establishments risk prevention
★★★★★
- QST-82
- 2 Days (14 Hours)
Description
This training will allow you to understand and know the importance of hygiene in your professional practice. Beyond hand or clothing hygiene, you will discover other specific procedures essential to prevent infections and contamination.
Who is this training for ?
For whomAll personnel concerned with hygiene in healthcare establishments.
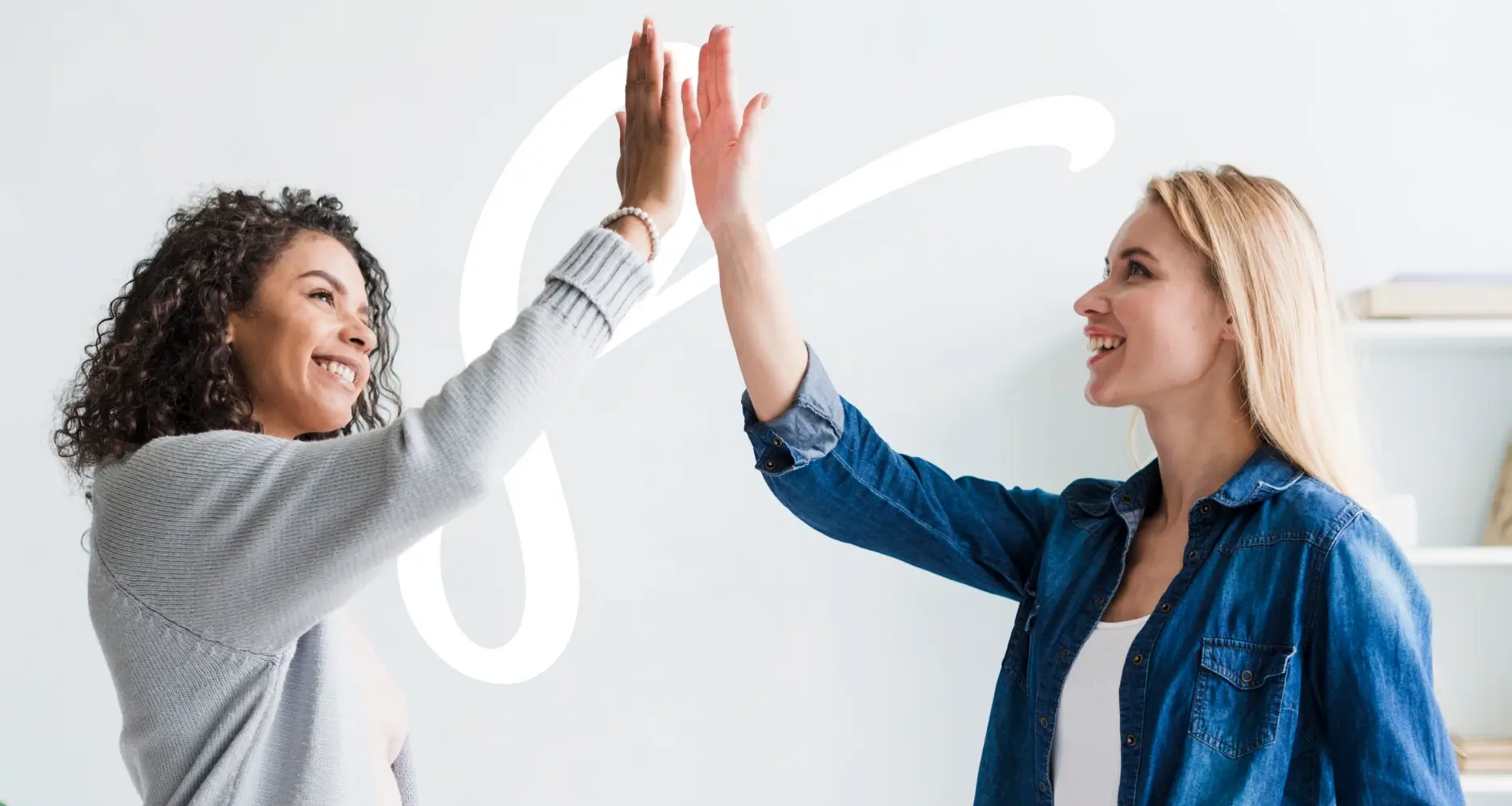
None
Training objectives
Master the regulations and organizational bases relating to hospital hygiene
Know the infectious risks linked to care
Adopt the essential rules to prevent infections
Apply good practices around linen care
Understand the recommendations in food hygiene matters
247Training program
Understanding the fight against hospital infection
- Individual representations linked to the theme.
- Institutional aspects of hygiene: C.
- L.
- I.
- N.
- and C.
- H.
- S.
- C.
- T.
- Healthcare-related infections: nosocomial infections.
- General means: disinfection, sterilization.
- Specific means: l asepsis, antiseptics.
- Technical means: microbiological controls, high-risk services.
- Practical work Collection of knowledge and practices of participants.
- Creation of a summary sheet covering the key points of the fight against hospital infection.
248Apply the recommendations regarding laundry care
- Linen and the choice of textiles.
- Quantification of the barrier effect of textiles.
- Recommendations for appropriate clothing in a hospital environment.
- The various checks carried out in the laundry.
- Clean linen: a mission impossible?r nScenariornPresentation of good practices and comparison with the usual practice of the participants.
Develop the mission of maintaining the living environment
- The three aspects of hygiene of the premises.
- Daily and periodic maintenance of the room.
- Maintenance of the sanitary facilities.
- Fire safety and knowledge of patient evacuation circuits.
- Scenario Presentation of good practices and comparison with the participants' usual practice.
Understand the recommendations around food hygiene
- Basic concepts: bacteriology, food hygiene rules, the HACCP method.
- The food circuit and meal distribution.
- Dishes : cleaning and disinfection.
- Maintenance and cleaning of the office.
- The waste circuit.
- Collective reflection Presentation of the educational sheet relating to HACCP standards.
- Understand the content of the texts and transpose it into your daily life.
ISO 13485 Lead Auditor "Quality management - Medical devices"
★★★★★
- QST-85
- 5 Days (35 Hours)
Description
By completing the ISO 13485 Lead Auditor training, you will develop the skills required to conduct Medical Device Quality Management Systems (QDMS) audits using the most commonly used audit principles, procedures and techniques. used.
This training will allow you to master the planning and carrying out of internal and external audits, in accordance with the ISO 19011 standard and the ISO/IEC 17021-1 certification process. Emphasis will be placed on practical exercises to enable you to master audit techniques and manage an audit program, an audit team, client communication and conflict resolution.
Once you have acquired the skills necessary to perform these audits, you can take the exam and apply to obtain the title of "PECB Certified ISO 13485 Lead Auditor". This certificate is proof that you have acquired the skills necessary to audit organizations according to best auditing practices.
Who is this training for ?
For whom- Auditors wishing to carry out and lead certification audits of the Quality Management System for Medical Devices (SMQDM)
- Managers or consultants wishing to master the audit process of the Quality Management System for Medical Devices
- Any person responsible for maintaining compliance with the requirements of the Medical Device Quality Management System
- Technical experts wishing to prepare an audit of the Medical Device Quality Management System
- Consultants specialized in medical device quality management
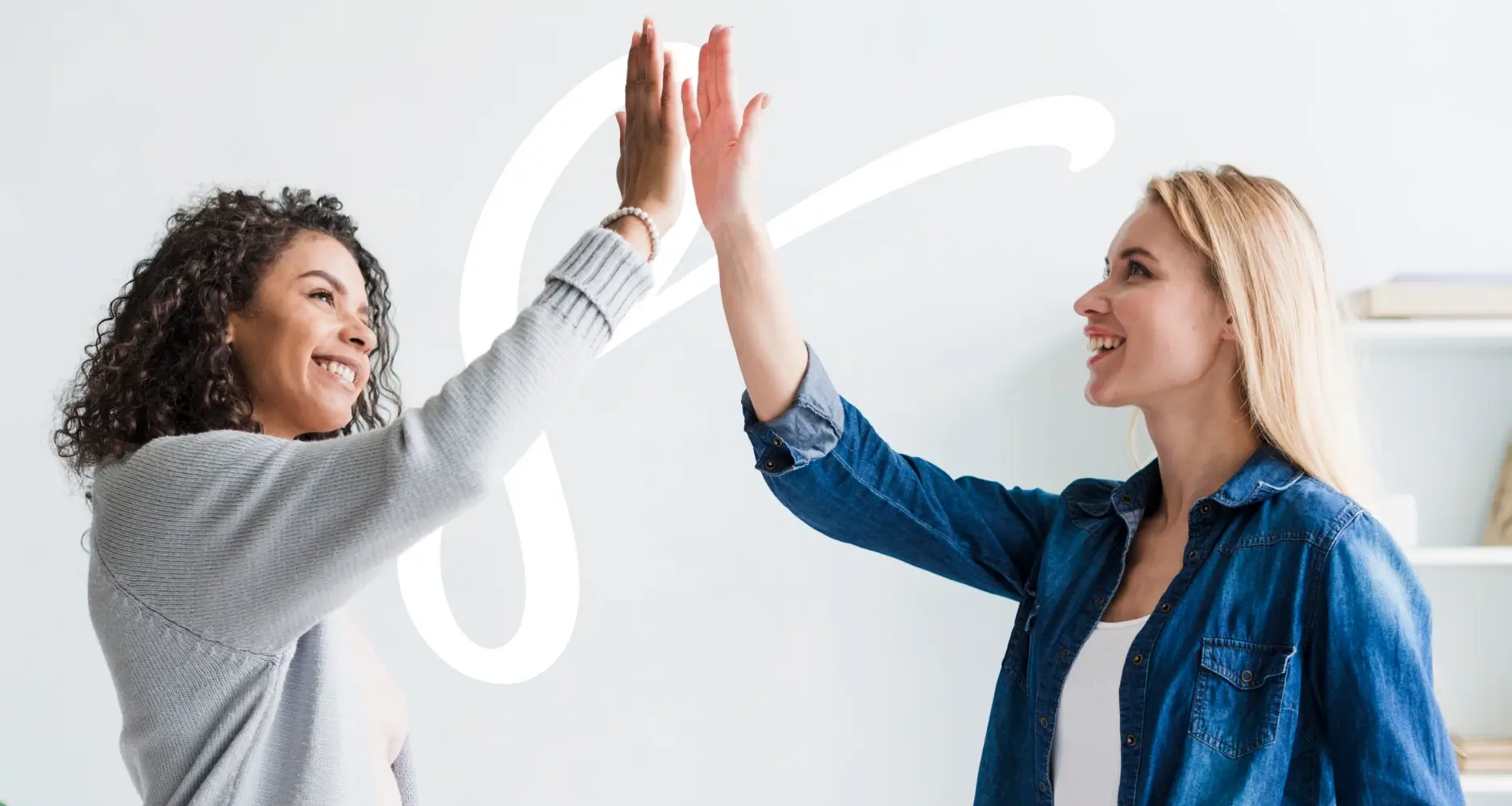
Good knowledge of the ISO 13485 standard and in-depth knowledge of audit principles.
Training objectives
- The training will allow you to understand the operation of a quality management system for medical devices compliant with the ISO 13485 standard
- Participants will be able to explain the correlation between ISO 13485 and other standards and regulatory frameworks
- The training will allow you to understand the role of an auditor and to know how to plan, direct and monitor a management system audit in accordance with the ISO 19011 standard
- Participants will be able to lead an audit and an audit team, as well as interpret the requirements of ISO 13485 in the context of a SMQDM audit
- Through this training, participants will acquire the skills necessary to plan an audit, lead an audit, write reports and follow up on an audit in accordance with the ISO 19011 standard
251Training program
programme
- Day 1: The training program includes a presentation of the Medical Device Quality Management System and the ISO 13485 standard.
- Day 2: Participants will learn the fundamental principles of the audit as well as the stages of preparation and implementation of the audit.
- Day 3: will be devoted to on-site audit activities.
- Day 4: Participants will be introduced at the end of the audit.
- Day 5: the last day of training will be dedicated to the certification exam.
ISO/IEC 17025 Lead Implementer "Quality Management – Laboratory Management System"
★★★★★
- QST-85
- 5 Days (35 Hours)
Description
To ensure precise and reliable results in your testing and calibration laboratory, it is crucial to follow a quality management process compliant with the ISO 17025 standard. This international standard defines the criteria for competence and recognition of the ability of laboratories to perform tests, calibrations, and sampling.
The ISO 17025 Lead Implementer training will enable you to understand all the technical requirements necessary for establishing a Laboratory Management System (LMS), both in the general organization of the laboratory and in the testing and calibration methods. This will help you implement a robust quality system for your laboratory.
Who is this training for ?
For whomThe introductory training on the ISO/IEC 17025 standard will allow you to grasp the fundamental concepts of a Laboratory Management System.
By participating in the ISO/IEC 17025 introductory training, you will understand the importance of a Calibration and Testing Laboratory Management System and the benefits it can bring to businesses, society, and the government.
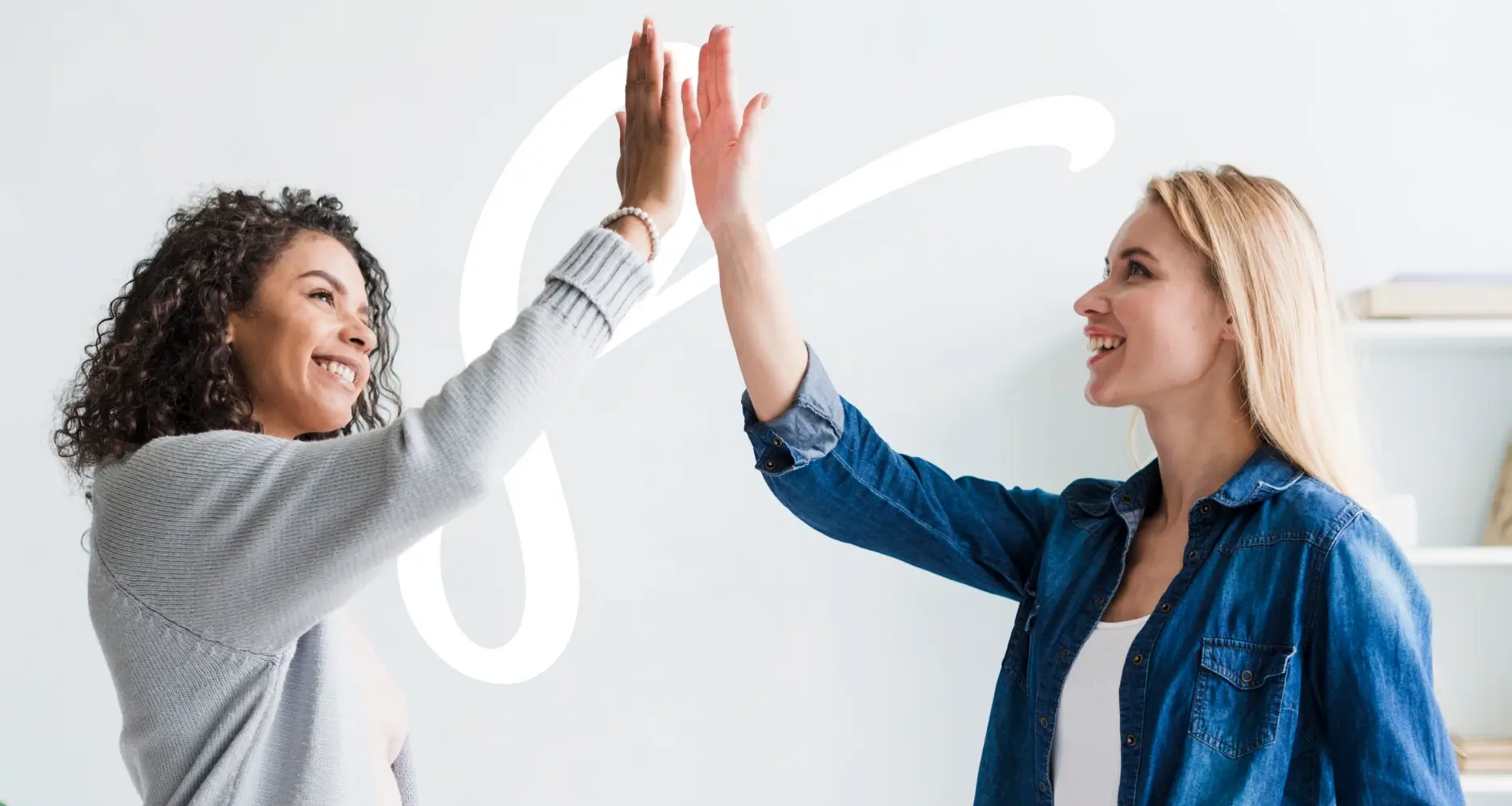
A general knowledge of the ISO 17025 standard is recommended.
Training objectives
Implementing a process for the recognition of testing competencies in your laboratory offers several advantages
Firstly, it demonstrates your expertise and professionalism to your clients, which can serve as a marketing advantage for your business
Additionally, the recognition of testing competencies can act as a benchmark for your laboratory's performance, allowing you to identify areas for improvement and maintain a high level of quality
Finally, this international recognition can enhance the credibility of your laboratory and enable you to work with partners abroad
254Training program
Day 1: Discovery of the fundamental concepts of the Laboratory Management System (MLS) as defined by the ISO/IEC 17025 standard.
- Introduction to the management system and the process approach, presentation of the ISO 17025 standard and the regulatory framework, as well as the fundamental principles of Laboratories and their accreditation.
Day 2: Planning the implementation of an ISO/IEC 17025 compliant SML.
- Defining the scope of an SML, management requirements and technical requirements.
Day 3: Implementation of an ISMS compliant with the ISO/IEC 17025 standard.
- Understand the implementation of the document management framework, design measures and drafting procedures, implement measures, develop a quality training, awareness and communication program and manage operations of an SML.
Day 4: Control, monitoring and measurement of an SML and certification audit in accordance with the ISO/IEC 17025 standard.
- Understand SML control and monitoring, develop metrics, performance indicators and dashboards, perform SML internal audit, implement a continuous improvement program and prepare for an ISO 17025 certification audit.
Day 5: ISO 17025 Lead Implementer certification exam.
ISO 45001 Foundation “Health and safety at work”
★★★★★
- QST-82
- 2 Days (14 Hours)
Description
The ISO 45001 standard is the first international standard relating to occupational health and safety management systems which replaces the OHSAS 18001 standard. The ISO 45001 Foundation training will allow you to understand the fundamental elements to implement and manage an Occupational Health and Safety Management System (OHSMS) in accordance with the ISO 45001 standard. During this training, you will learn the different modules of an Occupational Health and Safety Management System (OHSMS), including the OHSMS policy, procedures, performance measurement, management commitment, internal audit, management review and continuous improvement. After completing the training, you can take the exam and apply for the “PECB Certified ISO 45001 Foundation” title. The PECB Foundation certification certifies that you have understood the fundamental methods, requirements, framework and management approach.
Who is this training for ?
For whomAny person involved in or affected by the management of health and safety at work People wishing to acquire knowledge relating to the main processes of the Health and Safety Management System at work People wishing to pursue a career in management health and safety at work
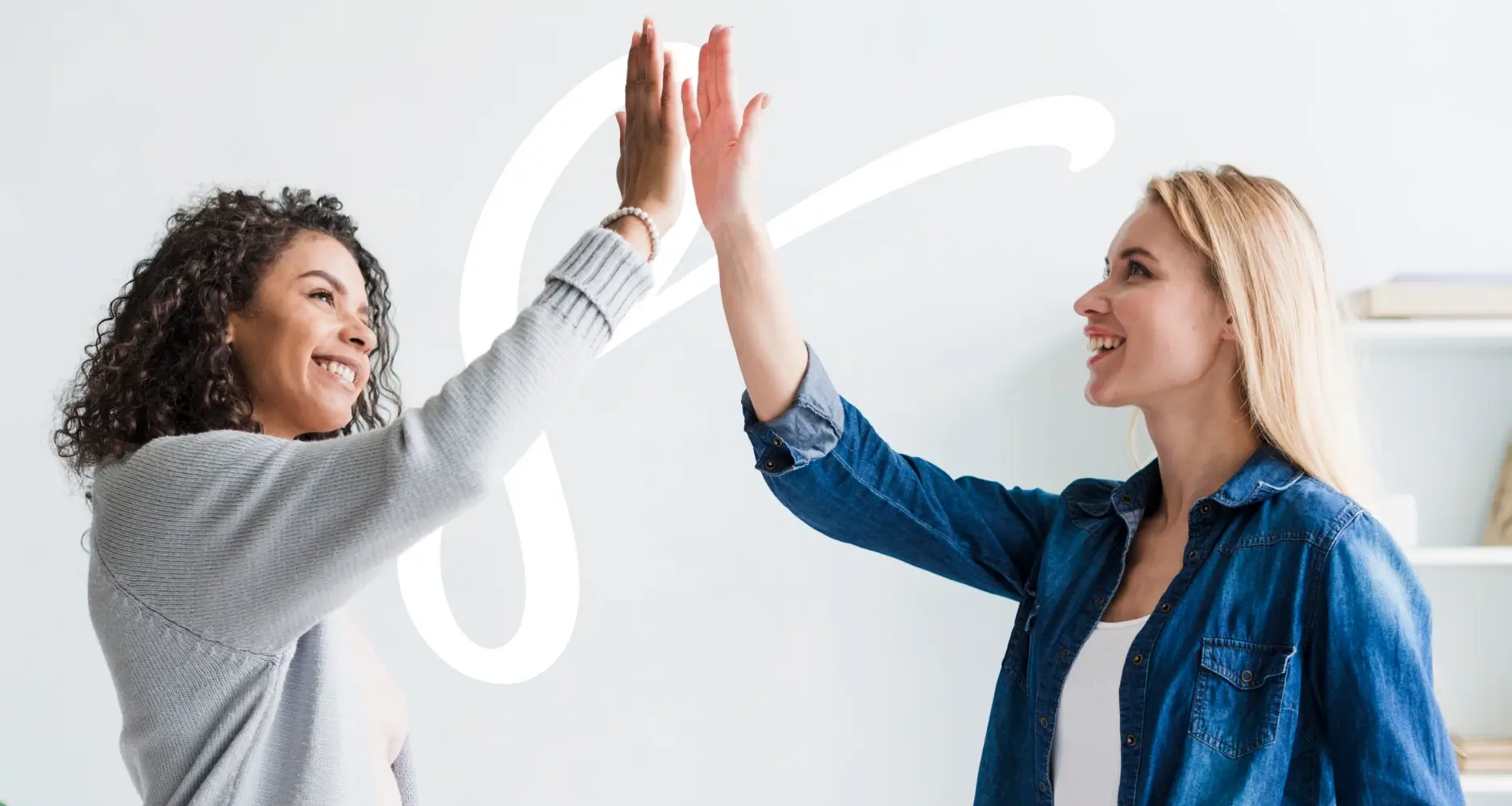
None
Training objectives
Understand the elements and operation of an occupational health and safety management system and its main processes
Understand the correlation between the ISO 45001 standard and other standards and regulatory frameworks
Know the approaches, methods and techniques for implementing and managing an occupational health and safety management system
257Training program
The program
- Day 1: Introduction to the concepts of the Occupational Health and Safety Management System, as defined by ISO 45001
- Day 2: Requirements for the Management System Occupational Health and Safety and Certification Examination
ISO 45001 Lead Auditor "Health and safety at work"
★★★★★
- QST-85
- 5 Days (35 Hours)
Description
The ISO 45001 standard is the first international standard relating to occupational health and safety management systems. This ISO 45001 Lead Auditor training course is designed to provide participants with the knowledge and skills necessary to carry out OHSMS audits by applying generally accepted auditing principles, procedures and techniques.
During the training, participants will learn how to plan and carry out internal and external audits in accordance with the ISO 19011 standard and the ISO/IEC 17021-1 certification process.
Practical exercises will help participants master audit techniques and develop the skills needed to manage an audit program, an audit team, client communication and conflict resolution.
At the end of the training, participants will be able to take the exam and apply for the title of “PECB Certified ISO 45001 Lead Auditor”. This certificate certifies that participants have acquired the skills necessary to audit organizations according to best audit practices.
Participants will be able to carry out OHSMS audits compliant with ISO 45001 and provide recommendations to improve the organization's occupational health and safety management system.
Who is this training for ?
For whom- Auditors wishing to carry out and lead certification audits of the Occupational Health and Safety
- Management system managers or consultants wishing to master the audit process of the Occupational Health and Safety Management System.
- Any person responsible for maintaining compliance with SMSST requirements.
- Technical experts wishing to prepare an audit of the occupational health and safety management system
- Advisors specializing in occupational health and safety management.
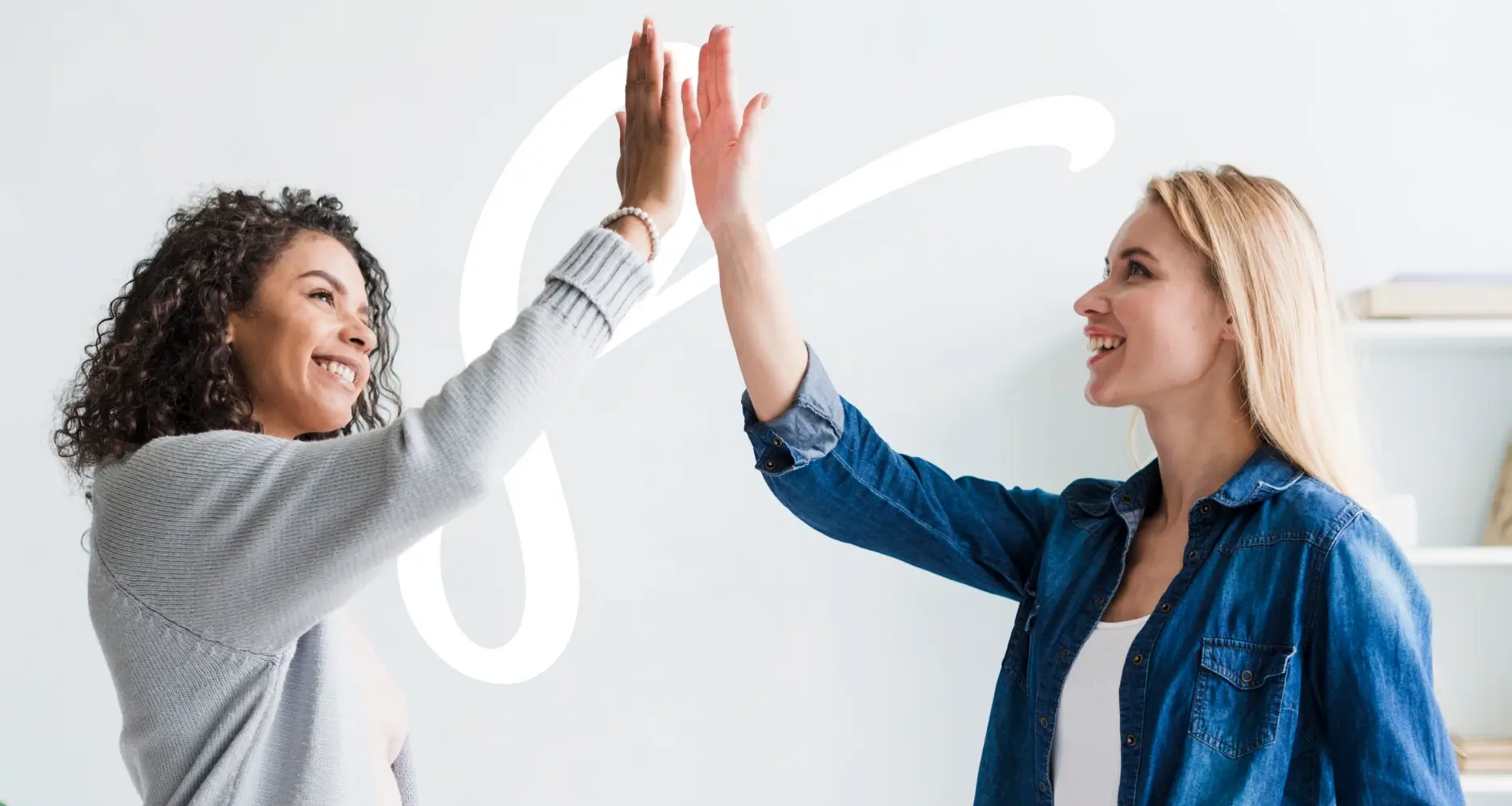
ISO 45001 Foundation certification or basic knowledge of ISO 45001 is recommended.
Training objectives
- To understand the operation of an Occupational Health and Safety Management System compliant with ISO 45001, it is necessary to become familiar with the policies, procedures and practices that ensure safety and employee health
- The ISO 45001 standard is designed to be compatible with other standards and regulatory frameworks
It is therefore important to explain the correlation between this standard and other regulatory frameworks - The role of an auditor is to plan, direct and monitor a management system audit in accordance with the ISO 19011 standard
- To lead an audit and an audit team, it is important to know how to interpret the requirements of ISO 45001 in the context of an OHSMS audit
- The skills of an auditor consist of planning an audit, leading an audit, writing reports and following up on an audit, in accordance with ISO 19011
260Training program
This training program aims to provide participants with the knowledge and skills necessary to conduct occupational health and safety audits in accordance with ISO 45001.
- The first day of the training will be devoted to the introduction to the Occupational Health and Safety Management System and the ISO 45001 standard. Participants will learn the basic principles of SMSS and the requirements of the ISO 45001 standard.
- On the second day, participants will learn the principles of preparing for and initiating the audit. They will understand the different stages of the audit and the skills necessary to conduct an audit. effective.
- The third day will be dedicated to on-site audit activities. Participants will learn how to conduct effective interviews, collect objective evidence and evaluate audit results.
- The fourth day will be dedicated to closing the audit. Participants will learn how to write a clear and concise audit report and provide recommendations for improving the SMSS.
- The last day will be. dedicated to the certification exam Participants will have the opportunity to take the certification exam to become an ISO 45001 certified auditor. At the end of the training, participants will be able to conduct SMSS audits compliant with the standard. ISO 45001 and provide recommendations for improving the organization's occupational health and safety management system.
ISO 45001 Transition “Health and safety at work”
★★★★★
- QST-81
- 5 Days (35 Hours)
Description
The ISO 45001 transition course will allow you to better understand the differences between OHSAS 18001 and ISO 45001. During this training, you will be able to develop the knowledge and expertise necessary to support an organization in planning and implementing implementation of the transition process from a current OHSAS 18001 management system to ISO 45001 in a timely manner. After having mastered the new concepts and requirements of the ISO 45001 standard, you can take the exam to obtain the “PECB Certified ISO 45001 Transition” certification. The PECB certificate certifies that you have the practical knowledge and professional abilities necessary to successfully apply ISO 45001 changes to your existing management system.
Who is this training for ?
For whomManagers, trainers and/or consultants involved in the OSHMS transition to ISO 45001 Individuals responsible for planning and implementing a transition to ISO 45001 Auditors wishing to carry out and lead management audits transition certification to ISO 45001
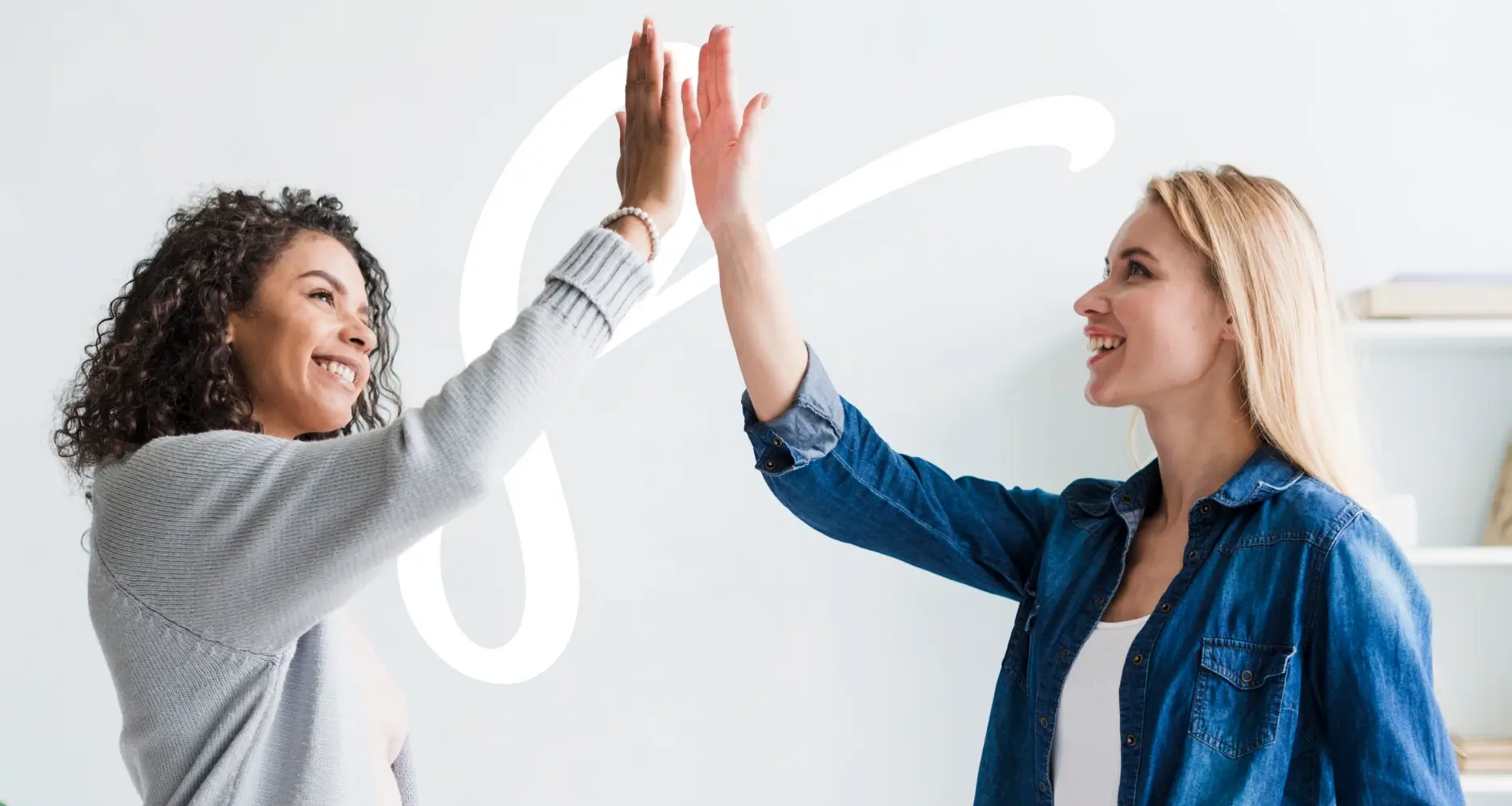
None
Training objectives
Discover the main differences between OHSAS 18001 and ISO 45001
Master the new concepts and requirements of ISO 45001Learn how to effectively apply ISO 45001 changes to a current management system
Understand the new High Level Structure of the standard ISO 45001 and learn how to apply it to a current SM.
263Training program
The program
- Day 1: Introduction to ISO 45001
- Day 2: ISO 45001 clause by clause and certification exam
ISO 45001 Lead Implementer “Health and safety at work”
★★★★★
- QST-85
- 5 Days (35 Hours)
Description
The ISO 45001 standard is the first international standard that deals with Occupational Health and Safety Management Systems. It replaced the OHSAS 18001 standard.
The ISO 45001 Lead Implementer training will allow you to acquire the necessary expertise to help an organization set up, manage and maintain an Occupational Health and Safety Management System (OHSMS). ) compliant with ISO 45001.
This training will give you in-depth knowledge of OHSMS best practices and enable you to apply them effectively to ensure a safe and healthy working environment for employees.
After mastering all the concepts related to OHSMS, you can take the exam and obtain the PECB Certified ISO 45001 Lead Implementer certification.
This certification will prove that you are able to implement ISO 45001 in an organization through your practical knowledge and professional skills.
Who is this training for ?
For whom- Managers or consultants involved in the management of health and safety at work
- Specialist advisors wishing to master the implementation of a health and safety management system at work
- Any person responsible for maintaining compliance to OHSMS requirements Members of an OHSMS team
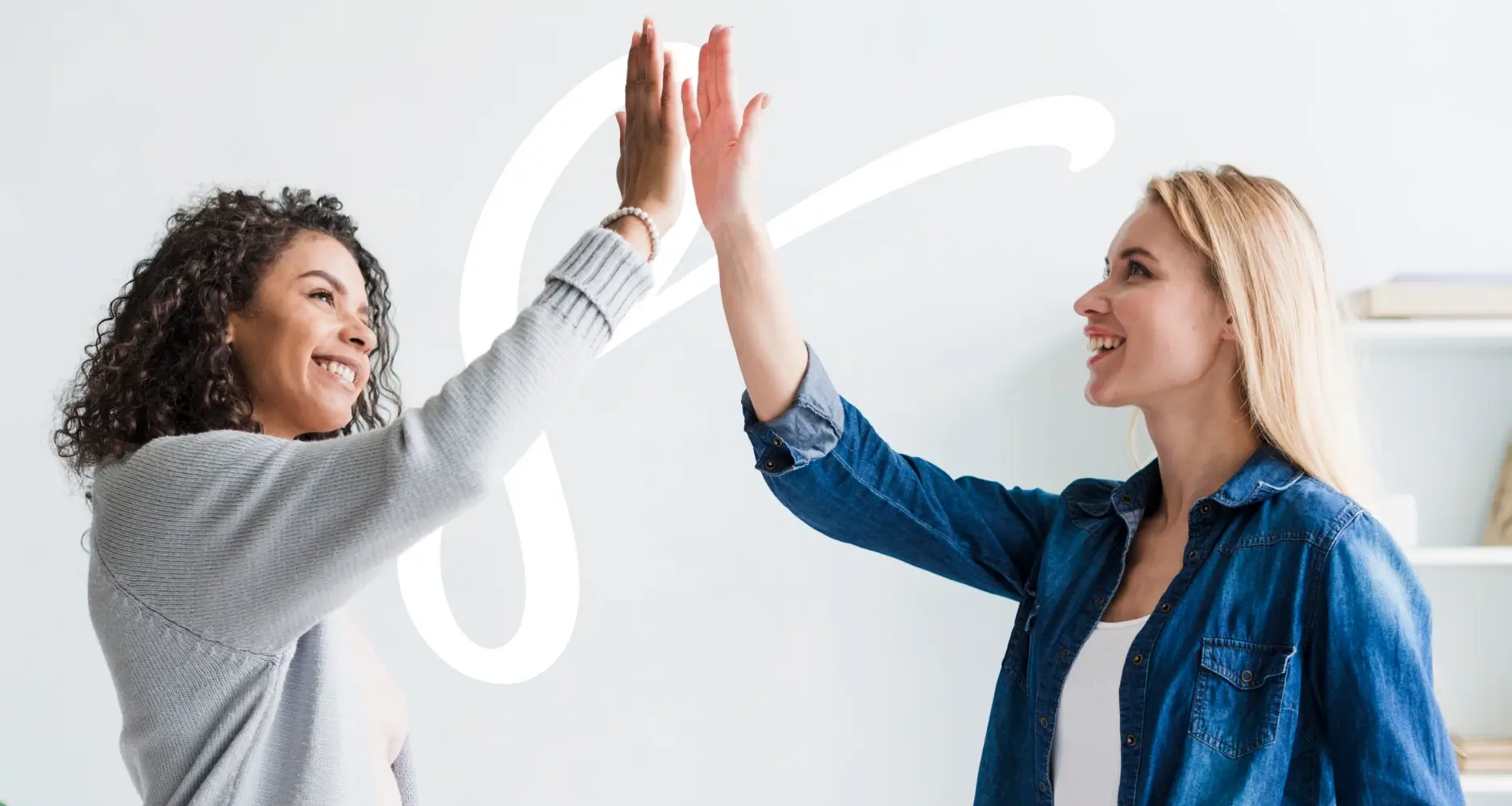
ISO 45001 Foundation certification or basic knowledge of ISO 45001 is recommended.
Training objectives
- Have a thorough understanding of the relationship between ISO 45001 and other relevant standards and regulatory frameworks
- Be able to master the concepts, approaches, methods and techniques necessary to effectively implement and manage an SMSST
- Be able to interpret the requirements of the ISO 45001 standard in a specific context of the organization
- Provide support for planning, implementing, managing, monitoring and maintaining OHSMS for organizations
- Acquire solid expertise to advise organizations on best practices in occupational health and safety management systems
266Training program
The program
- Day 1 is dedicated to the introduction of the ISO 45001 standard and the initialization of an Occupational Health and Safety Management System (OHSMS).
- Day 2 focuses on planning for the implementation of an OHSMS, including the policies, objectives and processes necessary to achieve ISO 45001 compliance.
- Day 3 focuses on implementing an OHSMS, ensuring that policies, procedures and practices are properly implemented and followed.
- Day 4 focuses on monitoring, measurement and continuous improvement of OHSMS, as well as preparation for the OHSMS certification audit.
- Day 5 is dedicated to the certification exam, which assesses understanding and the individual's ability to implement an OHSMS compliant with the ISO 45001 standard.
★★★★★
- QST-85
- 2 Days (14 Hours)
Description
Who is this training for ?
For whom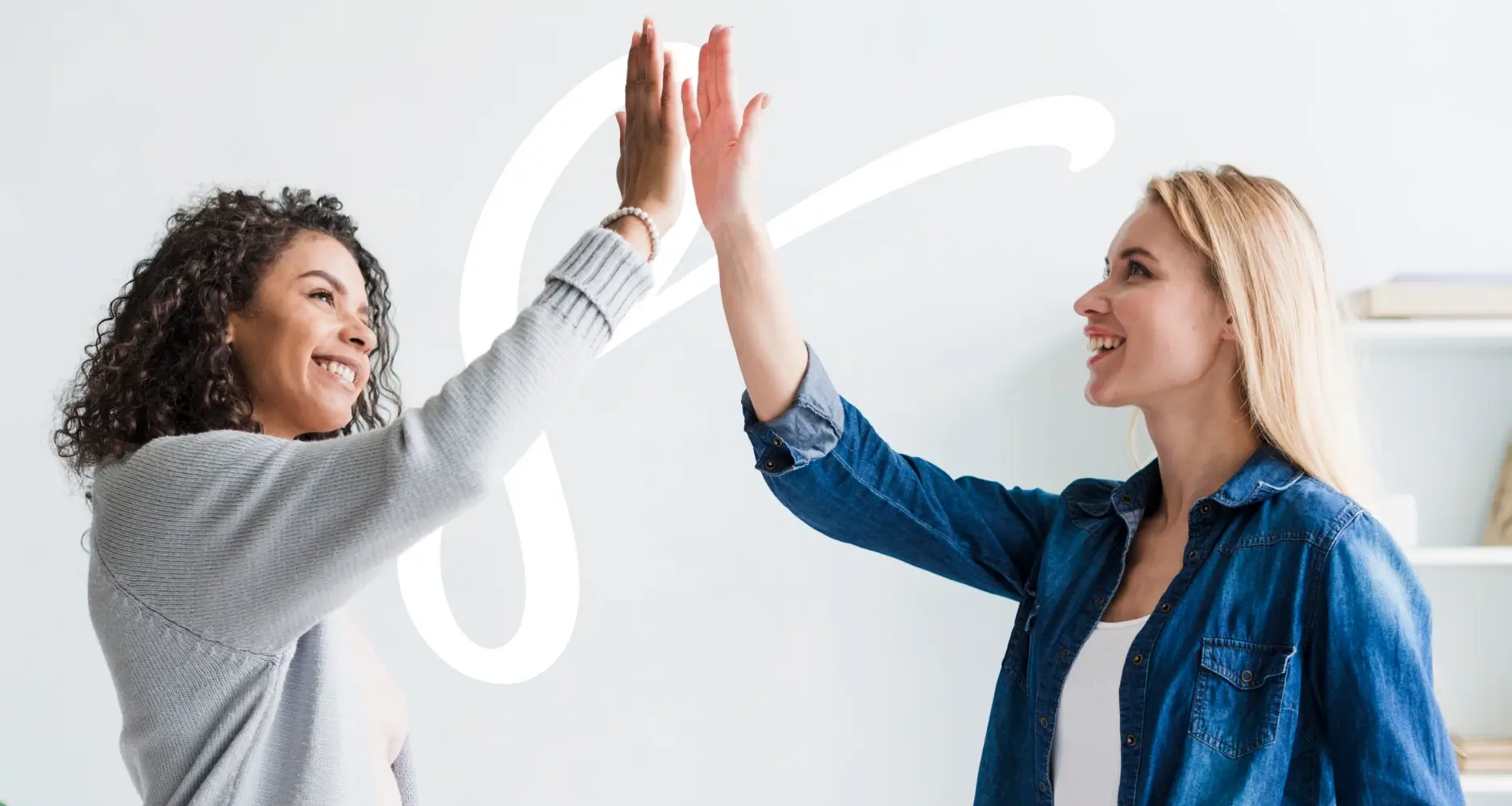
None
Training objectives
268269Training program
The program
- Day 1: Introduction to the concepts of the Medical Device Quality Management System, as defined by ISO 13485
- Day 2: Quality Management System requirements medical devices and certification exam
ISO 13485 Lead Implementer "Quality management - Medical devices"
★★★★★
- QST-85
- 5 Days (35 Hours)
Description
The ISO 13485 Lead Implementer training will allow you to develop the skills necessary to guide an organization in the establishment, implementation, management and maintenance of a medical device quality management system (QMSD) compliant with ISO 13485.
This training will allow you to gain expertise in best practices in QMSD and develop your skills to improve the overall performance of the organization by consistently providing safe and quality medical devices.
After having assimilated all the concepts related to SGQDM, you will be able to take the exam and obtain the “PECB Certified ISO 13485 Lead Implementer” certification. This PECB certification demonstrates your practical ability and professional skills to implement ISO 13485 within an organization.
Who is this training for ?
For whom- Managers or consultants involved in the quality management of medical devices
- Specialized advisors wishing to master the implementation of a Quality Management System for medical devices
- Any person responsible for maintaining compliance with SMQDM requirements Members of 'a SMQDM team
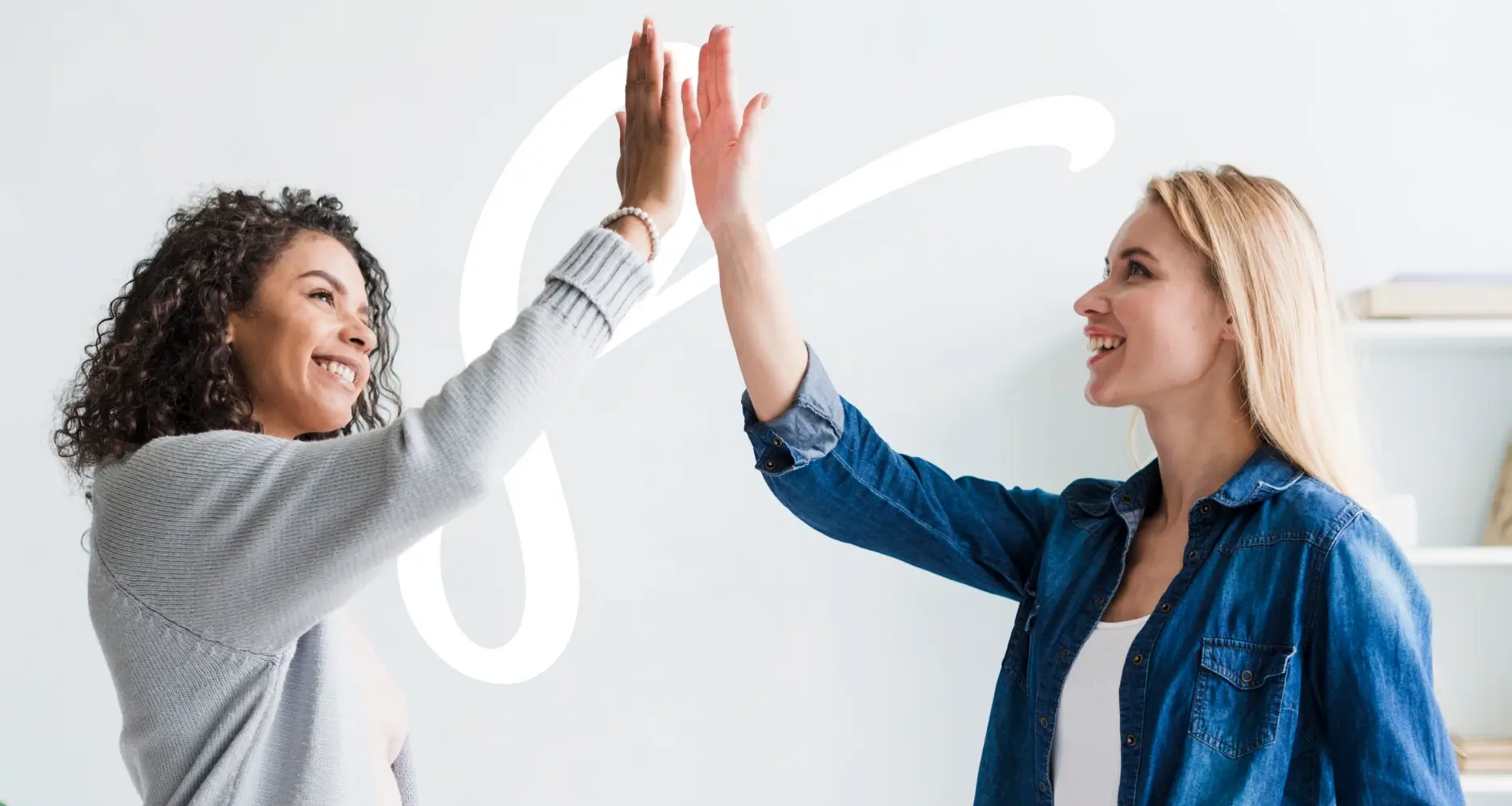
Participants in this training should have a fundamental understanding of ISO 13485 and in-depth knowledge of implementation principles.
Training objectives
- The correlation between ISO 13485 and other standards and regulatory frameworks must be understood
- The concepts, approaches, methods and techniques necessary to effectively implement and manage a SMQDM must be mastered
- The requirements of the ISO 13485 standard must be interpreted in a specific context of the organization
- An organization must be supported in the planning, implementation, management, monitoring and updating of the SMQDM
- The expertise necessary to advise an organization on the implementation of best practices relating to the Medical Device Quality Management System must be acquired
272Training program
Day 1: Introduction to ISO 13485 and initiation of a SMQDM
- The first day of training would be dedicated to the presentation of the ISO 13485 standard and the initiation of the quality management system for medical devices (QMSD). Participants will learn the requirements of the ISO standard 13485, the associated terminology, as well as the basic principles of SMQDM.
Day 2: Planning the implementation of a SMQDM
- On the second day, participants will learn how to plan the implementation of SMQDM. This will involve understanding the requirements of ISO 13485, identifying relevant processes, defining objectives and performance indicators keys, and to put in place an action plan.
Day 3: Implementation of a SMQDM
- The third day will be dedicated to the implementation of the SMQDM. Participants will learn how to set up the necessary processes, identify the necessary resources, train staff and implement documented procedures to support the implementation of the SMQDM.
Day 4: Monitoring, measurement, continuous improvement and preparation for the certification audit of a SMQDM
- On the fourth day, participants will learn to monitor and measure the effectiveness of the SMQDM. They will also learn to identify opportunities for continuous improvement, implement corrective and preventive actions and prepare for the SMQDM certification audit.
Day 5: Certification exam
- The fifth day will be dedicated to the certification exam. Participants will take an exam to assess their understanding of ISO 13485 and SMQDM implementation. Those who pass the exam will receive certification of their competence in quality management for medical devices in accordance with the ISO 13485 standard.
★★★★★
- QST-82
- 2 Days (14 Hours)
Description
Who is this training for ?
For whom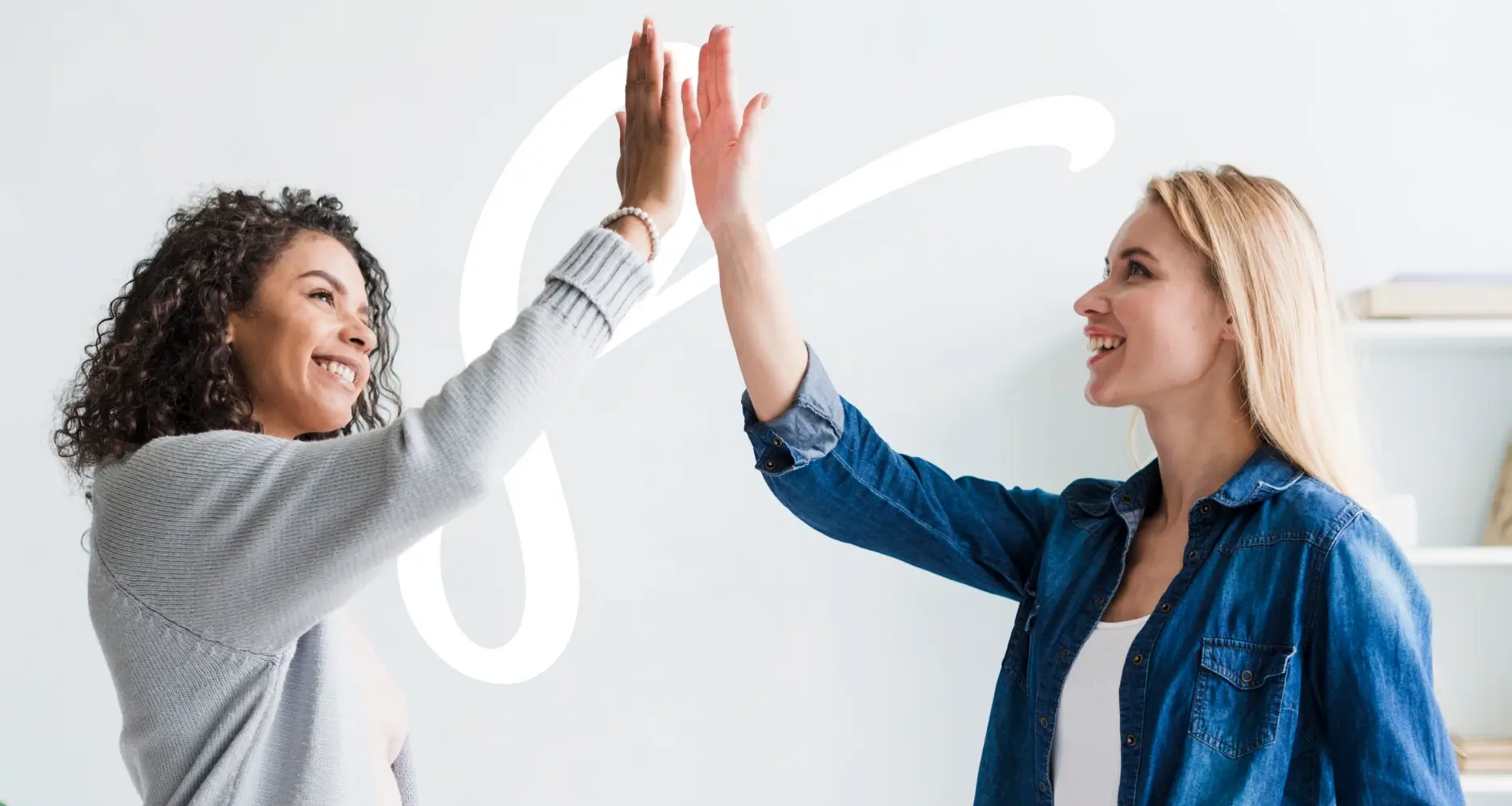
None
Training objectives
274275Training program
The program
- Day 1: Introduction to Quality Management System concepts, as defined by ISO 9001
- Day 2: Quality Management System requirements and review certification
ISO/IEC 17025 Lead Assessor "Quality Management – Laboratory Management System"
★★★★★
- QST-85
- 5 Days (35 Hours)
Description
The ISO/IEC 17025 Lead Assessor training will enhance your understanding of quality, administrative, and technical operations to effectively lead a laboratory towards ISO/IEC 17025 accreditation.
Through this training, you will be able to plan and conduct an ISO/IEC 17025 assessment with the required knowledge and skills. Practical exercises will help you master assessment techniques and evaluate compliance with the principles and requirements of a quality management system as well as the technical demands of ISO/IEC 17025.
After acquiring the necessary expertise to perform an assessment in accordance with this standard, you can take the exam and apply for the "PECB Certified ISO/IEC 17025 Lead Assessor" certification. This certification demonstrates your capability to assess the competence of calibration and testing laboratories according to best practices.
Who is this training for ?
For whom- Anyone wishing to become an assessor for an ISO/IEC 17025 accreditation
- Assessors wishing to conduct evaluations of calibration and testing laboratories' competencies
- Managers or consultants aiming to master ISO/IEC 17025 assessment
- Laboratory technicians responsible for maintaining compliance with the competency requirements of calibration and testing laboratories
- Technical experts wanting to prepare for the assessment of calibration and testing laboratories' competencies
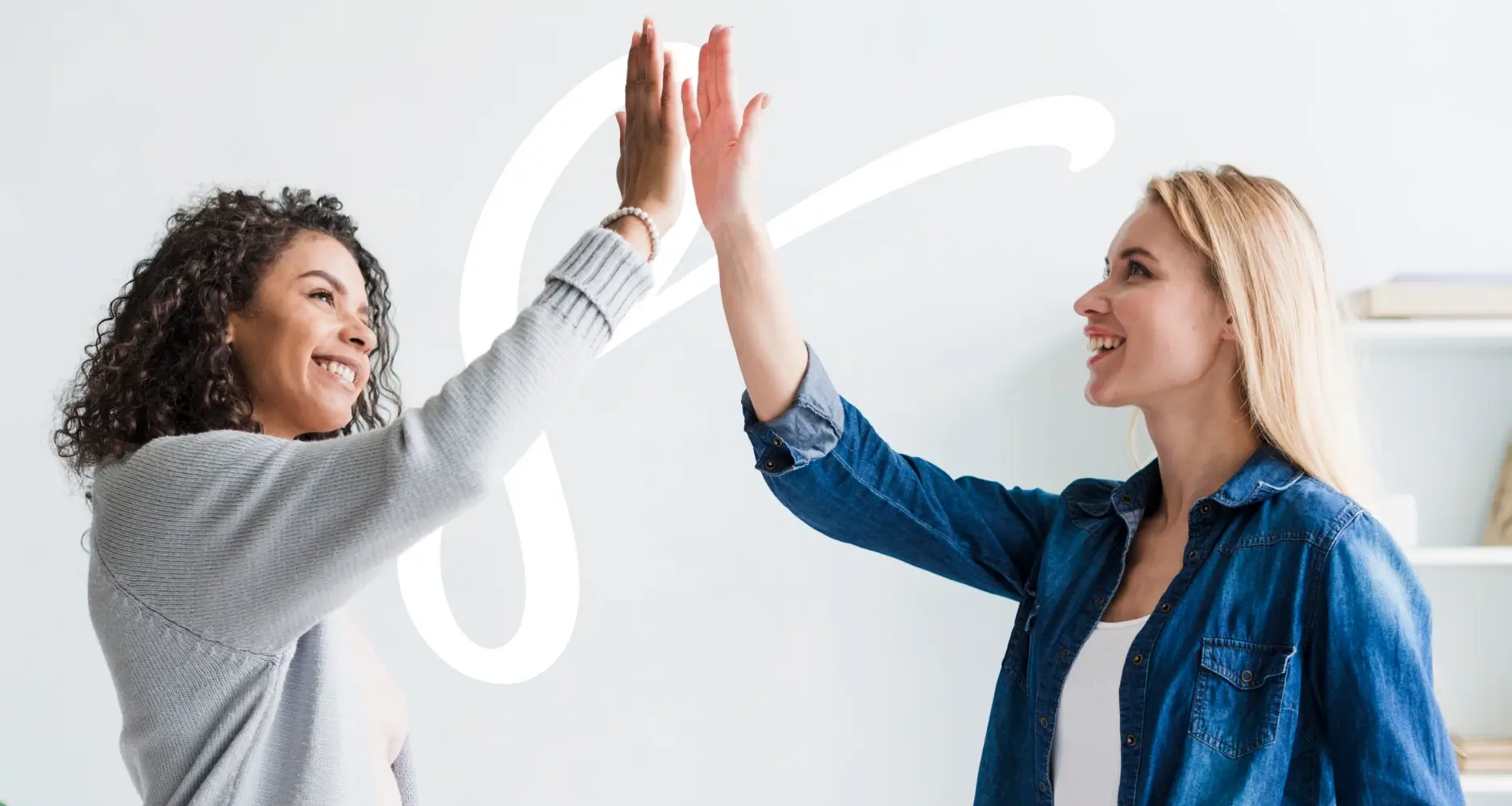
Knowledge of ISO 17025 standards
Training objectives
- Master the ability to assess the calibration and testing activities of a quality management system by interpreting the requirements of the ISO/IEC 17025 standard
- Gain a comprehensive understanding of the structure and operation of a calibration and testing laboratory according to the principles of the ISO/IEC 17025 standard
- Understand the relationship between the ISO/IEC 17025 standard and other regulatory frameworks, as well as the ISO 9001 standard
- Be able to plan, lead, and follow up on a laboratory assessment while understanding the role of an assessor and the requirements of the ISO/IEC 17011 standard
- Acquire the necessary skills to write assessment reports and successfully achieve laboratory accreditation
278Training program
The program
- The first day of the training will be devoted to an introduction to Laboratory Management Systems, as well as the ISO/IEC 17025 standard.
- The second day will cover the principles, preparing and initiating an evaluation.
- The third day will focus on on-site evaluation activities,
- The fourth day will be dedicated to closing the evaluation.
- Finally, the fifth day of the training will be reserved for the certification exam.
fire safety in business
★★★★★
- QST-87
- 1 Days (7 Hours)
Description
Taking fire risk into account is part of the overall approach to business risk assessment and prevention. Theoretical and practical training covers the elements of regulatory, technical and normative information necessary for the implementation of a fire prevention and fight policy.
Who is this training for ?
For whom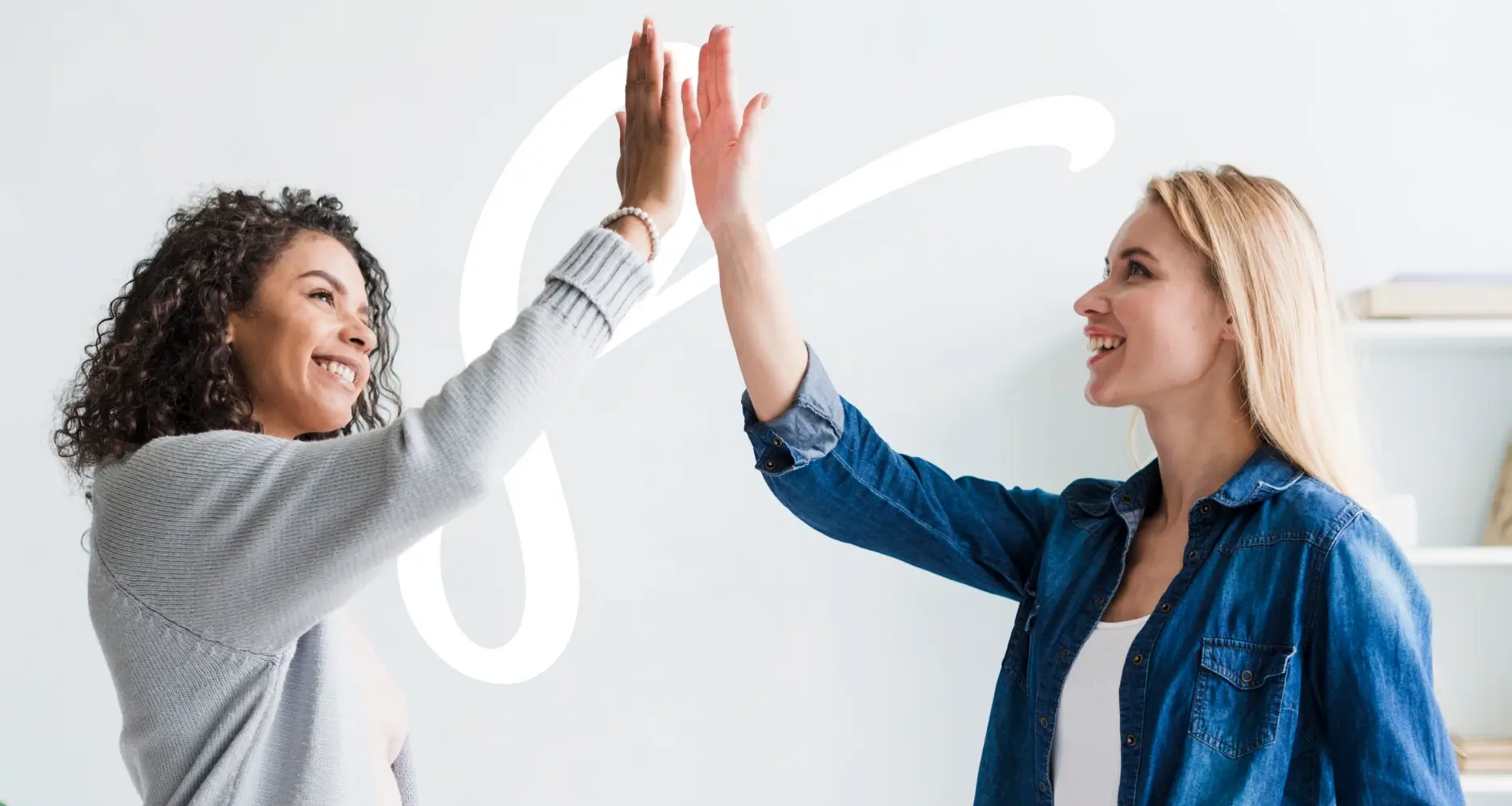
None
Training objectives
Know how to react to the start of a fire in the company
Know the evacuation instructions
Know how to recognize and use fire extinguishers
Know the consequences of traveling in a smoky environment
281Training program
Introduction to the theoretical part of corporate fire safety training
- Familiarize yourself with the safety instructions
- Define the specific risks of the establishment
- Reminder of internal procedures
- Understand the actions to take in the event of a fire
- know the instructions for using fire extinguishers
Practical part of company fire safety training: Handling fire extinguishers
- Practice of the extinguishing exercise on a real fire - First Fire Witness
Evacuation practice - First Fire Witness
- Carrying out a role-playing exercise in a smoky area
- Carrying out a behavior check in a hostile environment
Concepts of risk management and site security
★★★★★
- QST-88
- 1 Days (7 Hours)
Description
It is necessary to understand and apply concrete and consistent construction site prevention principles when working on any type of construction site. Because the site safety of the various stakeholders must be respected, we provide this 1-day course to give you solutions aimed at implementing a safety and risk prevention policy on a construction site. This risk prevention training on a construction site will cover theory and, above all, practice to be in tune with the issues relating to health and safety.
Who is this training for ?
For whom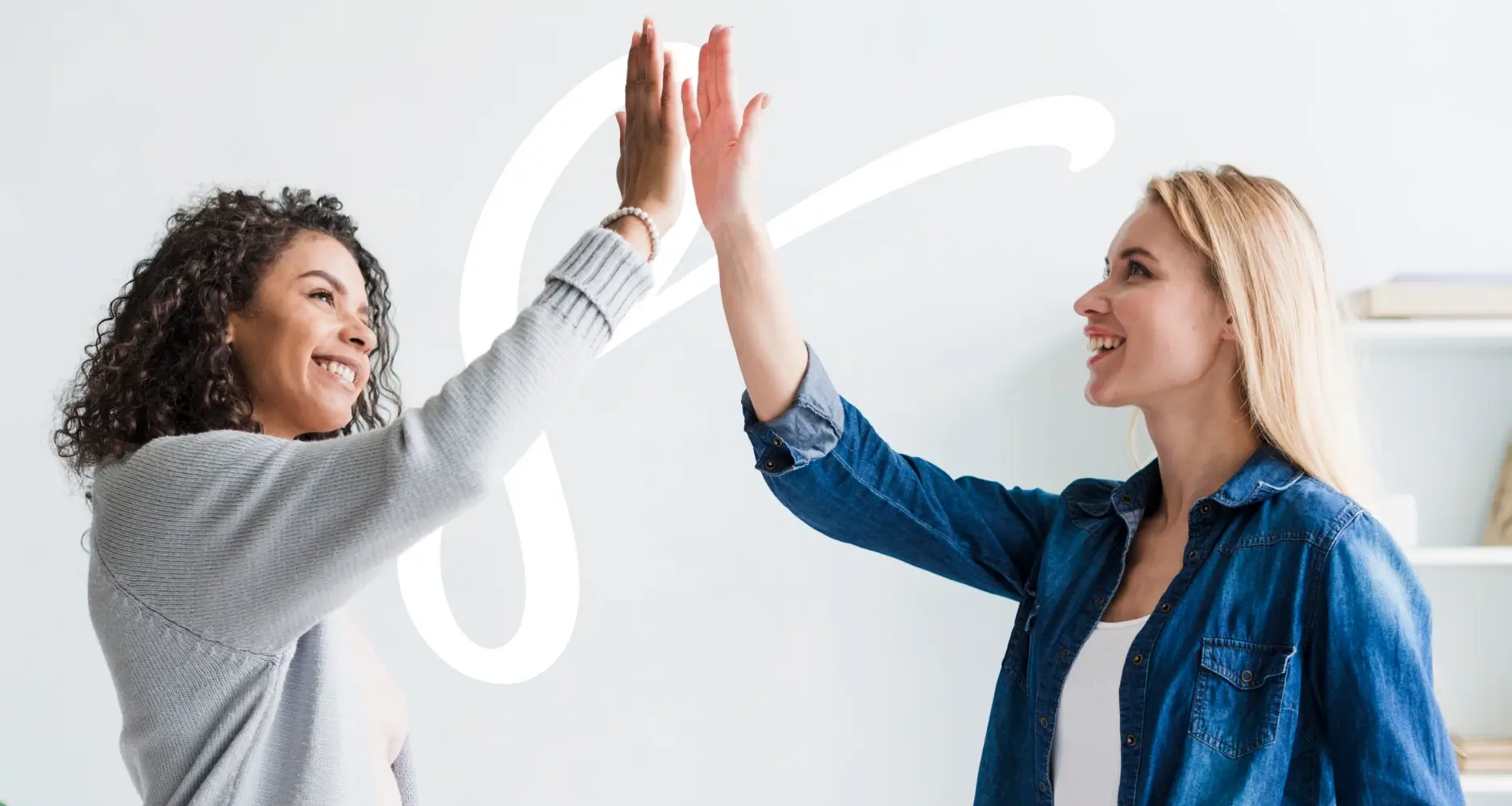
None
Training objectives
Understand the regulatory framework relating to the safety of a construction site.
Implement a safety and risk prevention policy on a construction site.
284Training program
Introduction to construction site safety training: mastering the challenges of risk prevention
- Know how to define the different types of risk: work accident, commuting accident, occupational illness
- Understand the financial/economic issues for the company
- Focus on the cost of work accidents
- Focus on the cost of occupational diseases
- Focus on the cost of the administrative management of work accidents
Know the issues related to construction site safety regulations
- Return to the obligation of security of results of the employer and employees
- Take stock of the different responsibilities: civil, inexcusable fault, criminal, professional
How to operate to ensure the management and prevention of risks on a construction site?
- Identify the general principles of risk prevention on a construction site
- Implementation of a risk assessment
- Review of the regulatory obligation of the code of work
Know your work environment and the documents related to the prevention plan
- Analyze the different security documentation and useful websites
- Determine the role of internal and external security stakeholders
- Focus on the different permits to obtain depending on of the type of construction site
ISO 55001 Lead Implementer
★★★★★
- QST-81
- 5 Days (35 Hours)
Description
his ISO 55001 Lead Implementer training will allow you to acquire the expertise necessary to support an organization during the establishment, implementation, management and maintenance of an Asset Management System ( SMA) compliant with the ISO 55001 standard. This training is designed to provide you with a mastery of best practices in asset management systems and to develop your skills in improving the management of the organization's assets by allowing it to use its assets to their full potential.
Who is this training for ?
For whomManagers or consultants involved in asset management. Specialized advisors wishing to master the implementation of an Asset Management System. Any person responsible for maintaining compliance with SMA requirements. Members of an ADM team.
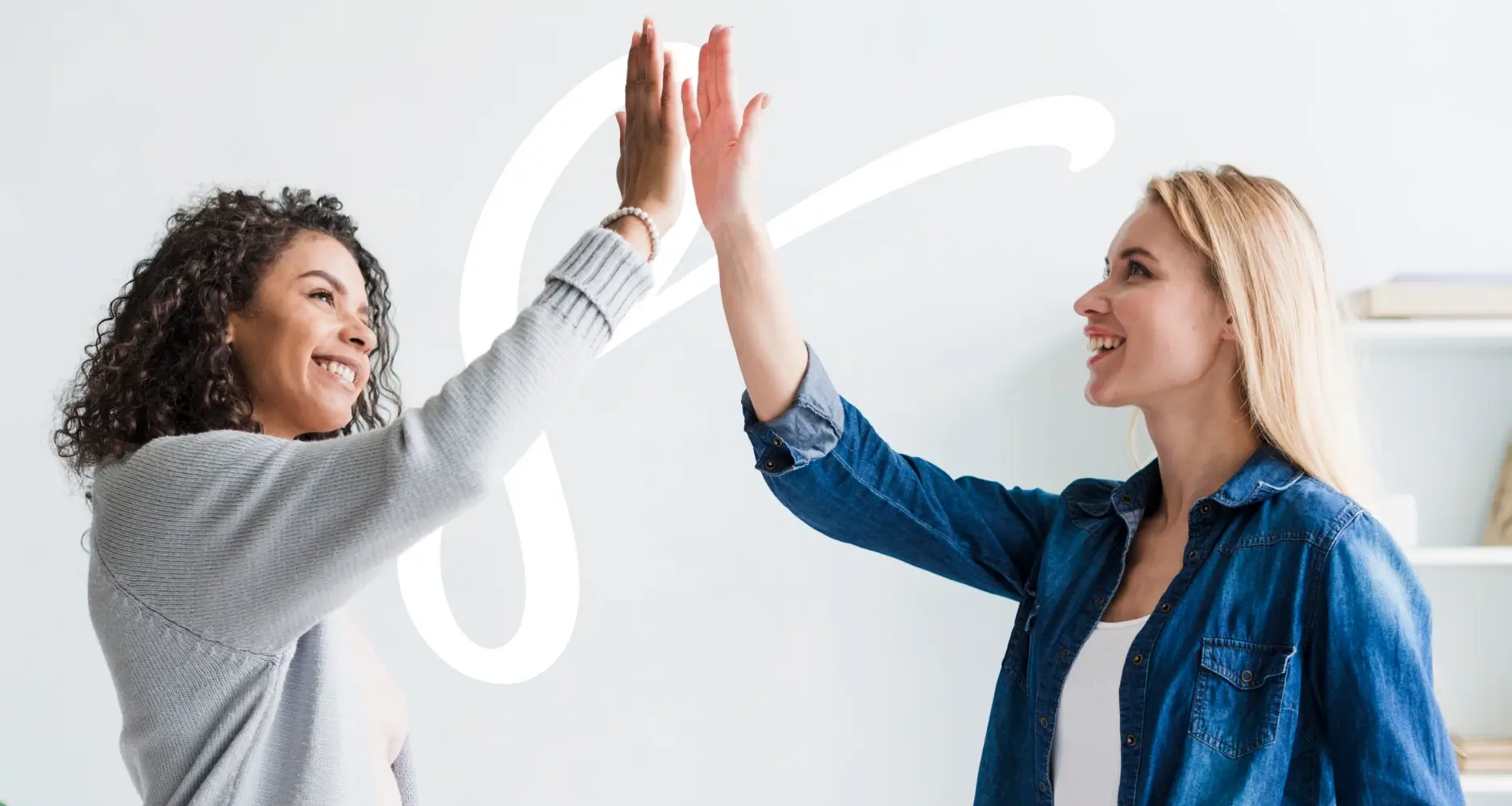
Good knowledge of the ISO 55001 standard and in-depth knowledge of implementation principles.
Training objectives
Understand the correlation between the ISO 55001 standard and other standards and regulatory frameworks
Master the concepts, approaches, methods and techniques necessary to effectively implement and manage an AMS
Know how to interpret the requirements of the ISO 55001 standard in a specific context of the organization
Know how to support an organization in the planning, implementation, management, monitoring and updating of the SMA
Acquire the necessary expertise to advise an organization on the implementation of best practices relating to the Asset Management System
287Training program
Introduction to the ISO 55001 standard and initialization of an SMA
Planning the Implementation of an MAS
Implementation of an SMA
Monitoring, measurement, continuous improvement and preparation for the SMA certification audit
Certification exam
Electrical authorization
★★★★★
- QST-81
- 3 Days (21 Hours)
Description
Electrical accreditation is essential training intended for workers required to work near electrical installations or to carry out electrical work. This certification aims to guarantee the safety of individuals and the preservation of equipment against electrical risks. By obtaining an electrical clearance, professionals are better prepared to work in environments where electricity is present.
Who is this training for ?
For whomThis training is aimed at anyone (electrician or non-electrician) who must obtain electrical authorization in a professional context.
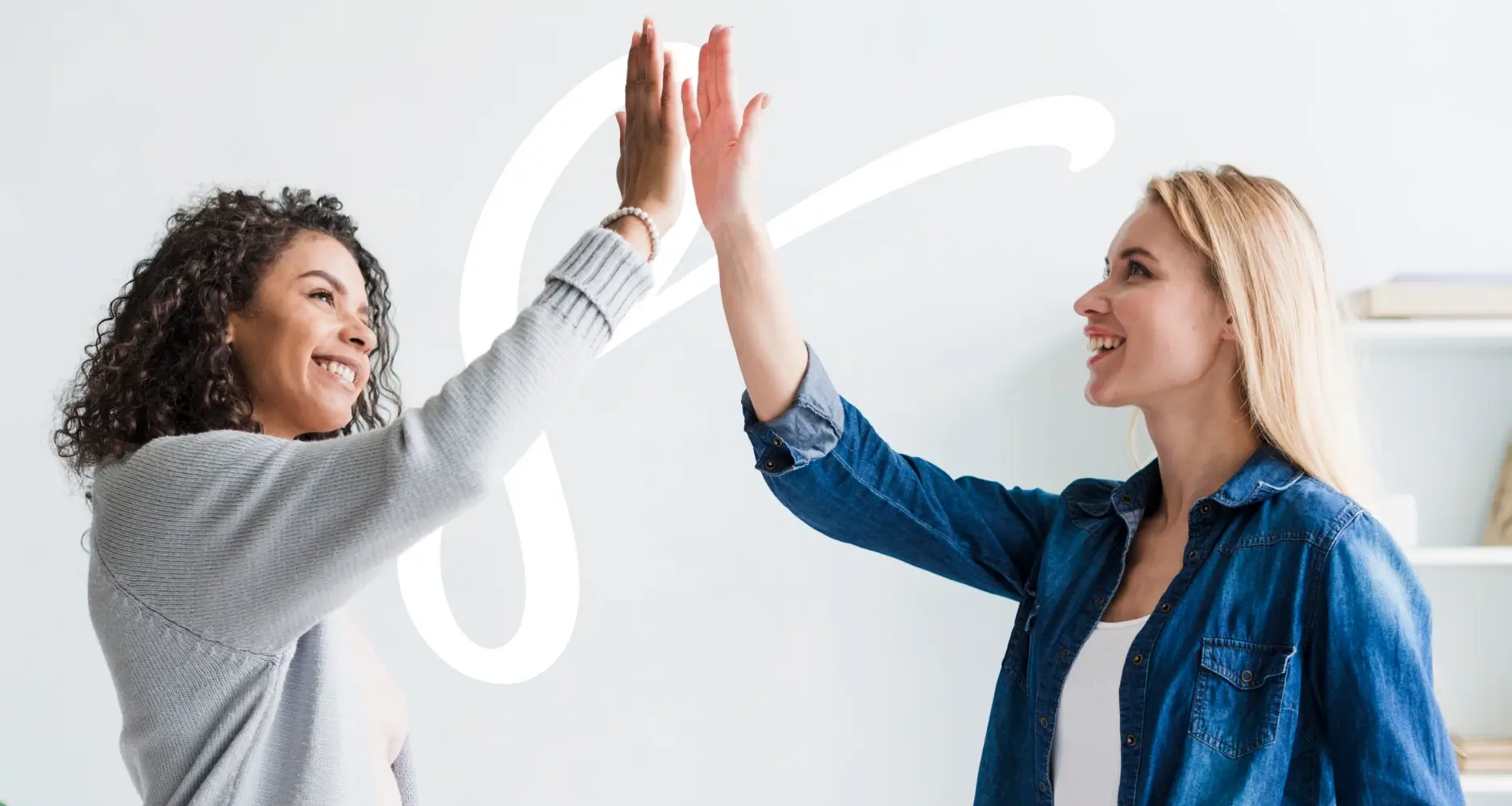
None.
Training objectives
Know the dangers of electricity and analyze the electrical risk.
Integrate prevention into work organization.
Implement prevention measures and the employer's instructions.
Know what to do in the event of an accident or fire of electrical origin.
290Training program
General information on electrical accreditation: introduction to training
- Presentation of the electrical authorization procedure according to the NFC 18510 standard in relation to voltage areas
- Assessment of risks and physiopathological effects of electric current
- Examples of accidents in the event of electrical contact (direct, indirect contact, short circuit)
- Know how to classify installations
- Awareness of the safety rules arising from the dangers of the electric current
- Know the role of the people involved
- Recognize electrical works
- Feedback on the operations of the person involved according to their level
- Recognize environmental zones
- Know how to produce written documents
- Review of the functions of equipment, the use of plans and diagrams and the benefit of interlocks and interlocks
- Know how to evaluate the impact of equipment design on personnel safety
Understand the concepts in terms of electrical safety
- Evaluate collective protection equipment and their function (barrier, screen, banner, etc.)
- Evaluate individual protection means and limits of use
- Know how to define the risks linked to the use and handling of materials and tools used in the environment
- Learn what to do in the event of a bodily accident
- Learn how to drive to take in the event of a fire in an electrical environment
Practical part of the electrical accreditation
291Theoretical and practical assessment
- Questionnaire with fundamental questions defined by the standard
- Practical exercise with acceptance criteria defined by the standard
Work at Height
★★★★★
- QST-82
- 1 Days (7 Hours)
Description
Working at height is a risk factor requiring specific training for the personnel concerned. A simple fall from a ladder or scaffolding can cause serious or even irreversible injuries.
Who is this training for ?
For whomThis training is aimed at:
- Employers
- Frames
- Supervisors required to carry out work at height
- Workers
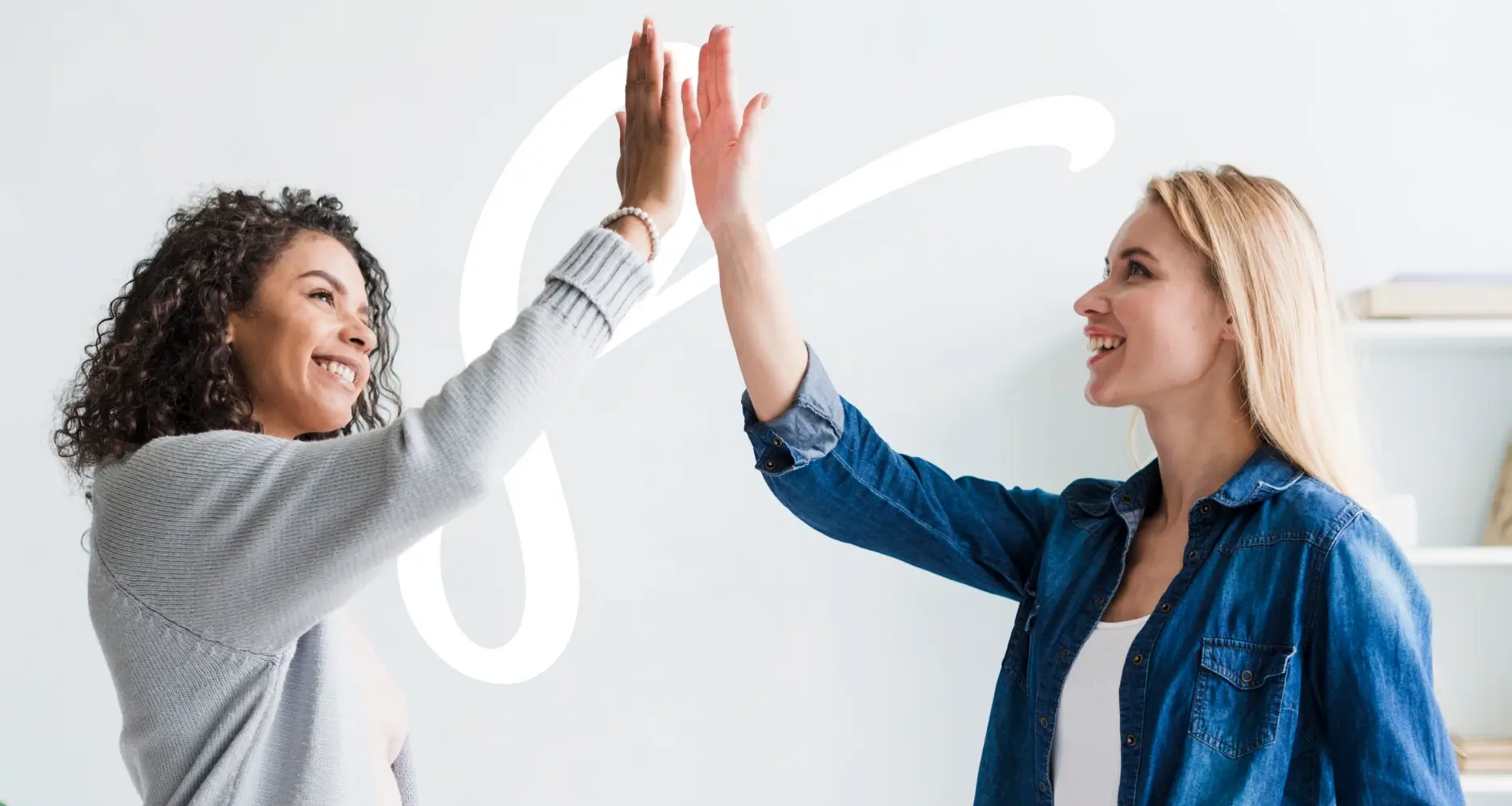
No prerequisites are necessary
Training objectives
Identify and prevent risks linked to work at height.
Provide technical, organizational and human solutions while respecting the general principles of prevention.
Master the regulations and obligations relating to working at height
294Training program
Carry out the prevention of professional risks when working at height
- What is working at height? Definition
- Know how to identify the general principles of prevention
- Understand the notion of risk when working at height
- - Return of work accident statistics, frequency indices and cost
- - Modeling of the
- Focus on regulations on working at height
- - Study of the design of workplaces and temporary work at height
- - Make specific arrangements for building and civil engineering work
- - Evaluate the ability to work at height, the skills and training of those involved
Lead a fall prevention campaign
- identify risky work situations when working at height
- Know how to prepare your intervention
- Identify what action to take in the event of dangerous situations
- - Focus on the causes and consequences of a fall
- Focus on technical, organizational and human solutions to limit risks
295Ensure the verification and use of safety equipment with professionalism
- Carry out a safety assessment of personal lifting devices: ladders, scaffolding, work platforms, etc.
- Make the right choice of equipment (Standards relating to ladders)
- Know how to use/identify collective protective equipment
- - Respect the requirements of temporary and permanent guardrails
- - Respect the requirements of stairs, ladders fixed steps and ladders
- - Comply with the requirements of platforms
- - Comply with the requirements of flexible collection devices (nets in large layers and nets on consoles)
- Know how to use/identify personal protective equipment (PPE)
- - Ensure the management and mandatory wearing of PPE (safety shoes, helmets, etc.)
- - Understand the use and installation of fall arrest systems
- - Understand the use and installation of restraint systems
- - Understand the use and 'installation of workstation systems
Electrical safety
★★★★★
- QST-83
- 2 Days (14 Hours)
Description
Every year, the use of electrical equipment causes numerous accidents. The risks related to electricity are too often underestimated.
Who is this training for ?
For whomThis training is aimed at management personnel as well as workers exposed to the dangers associated with electrical equipment.
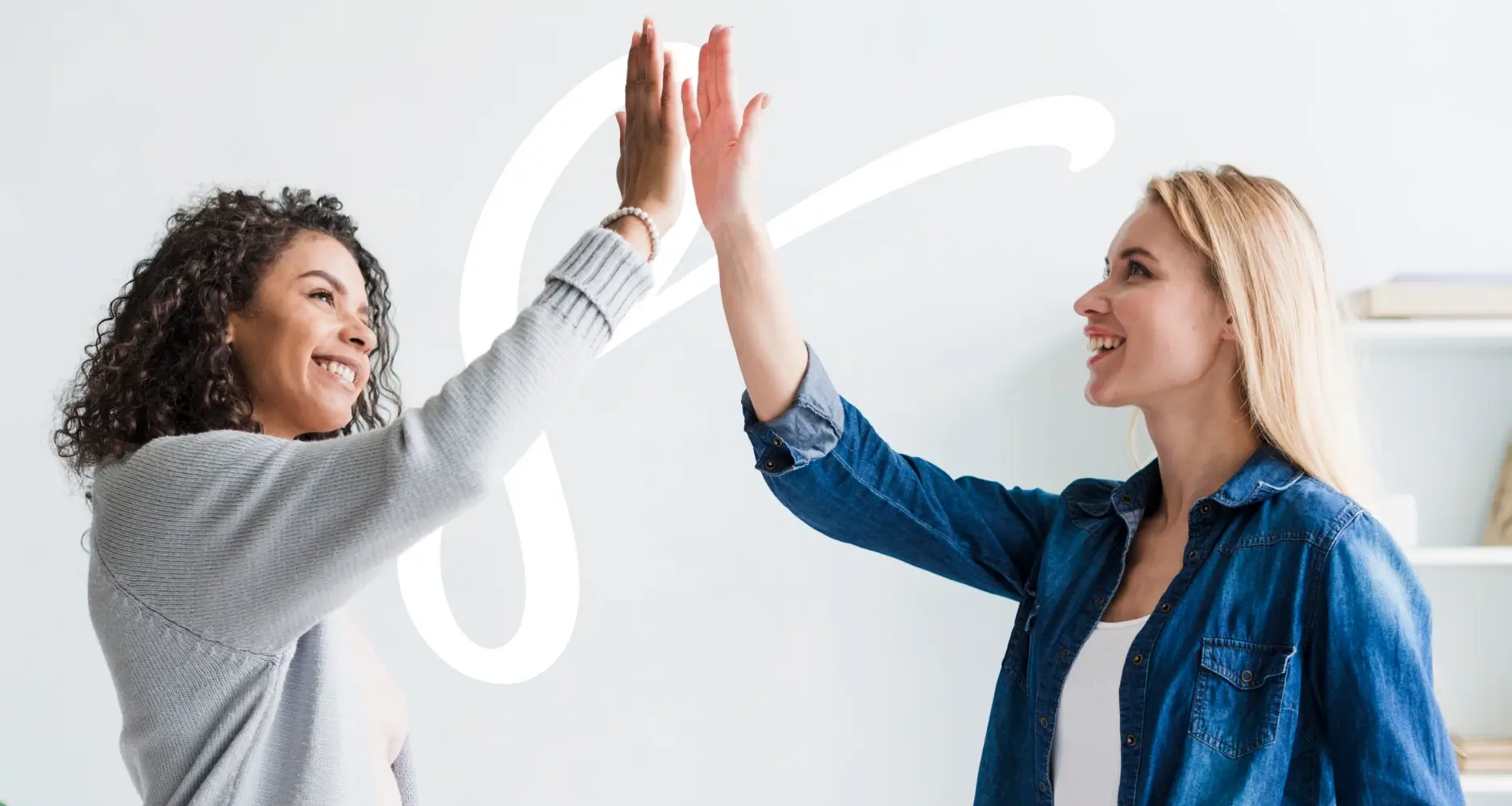
None.
Training objectives
Identify and prevent electrical risks.
Ensure the safety of people against electrical dangers.
Know what to do in the event of an accident.
298Training program
Safety Basics
Current regulations
Electrical authorization
Electrical safety, dangers...
Prevention and principles
Personal protective equipment
What to do in the event of an accident
Lean Six Sigma®, Black Belt, certification
★★★★★
- QST-87
- 8 Days ( Hours)
Description
The Black Belt generally intervenes on complex projects, leading to significant financial gains for the company. This course will prepare you for the "Black Belt" certification, which will allow you to master the advanced methods and tools of Lean Six Sigma and apply them in your projects.
Who is this training for ?
For whom- Any manager (Green Belt certified) wishing to take charge of complex and large-scale improvement projects.
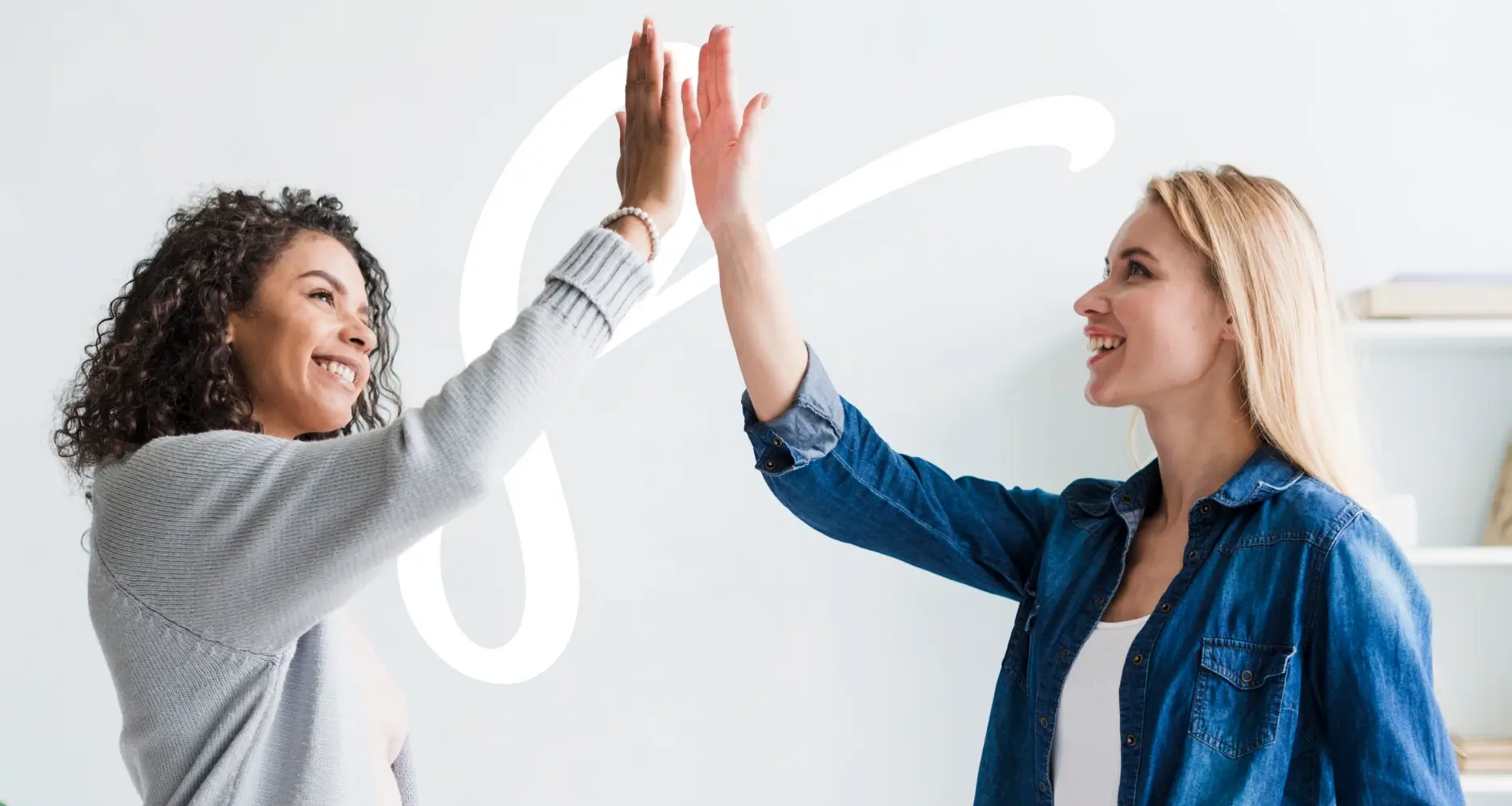
Training objectives
- Master the DMAIC model.
- Be able to select the appropriate Lean Six Sigma tools.
- Know how to lead a large-scale Lean Six Sigma project.
- Coach Green Belts
Obtain Black Belt certification.
301Training program
Introduction
- Knowledge test to identify the level of participants.
- Correction of the knowledge test.
- Presentation of the case study.
- Launch of the project.
- Setting up the production line.
- Launching the production line.
- Feedback (each group presents its results).
- Case study
Phases "Define" and "Measure" of the DMAIC model
- Estimate the Gap Analysis between the achievement and the customer objective.
- Realize the
- Translate the VOC into
- Create a SIPOC (Suppliers, Inputs, Processes, Outputs, Customers).
- Establish the project charter.
- Draw the
- Feedback (each group presents their results).
- Case study
302Phases "Measure" and "Analysis" of the DMAIC model
- Create the Value Stream Map.
- Identify the process steps to measure.
- Know how to calculate the performance of the process.
- Repeat measurements if necessary.
- Use of MINITAB (hypothesis tests, regression line, Anova one and two way).
- Feedback experiment (each group presents its results).
- Case study
“Analysis”, “Improve” and “Control” phases of the DMAIC model
- Finalize the analysis and find the Root Cause.
- Find solutions: Brainstorming, experiment plan with MINITAB.
- Create KPIs and control charts with MINITAB.
- Feedback (each group presents their results).
- Case study
Preparation for the IASSC “Black Belt” exam
- Revision of vocabulary and concepts.
- Mock tests (100 questions).
- Correction of the mock test.
Lean Six Sigma®, Yellow Belt, certification
★★★★★
- QST-85
- 2 Days ( Hours)
Description
The Lean Six Sigma approach is a powerful tool for optimizing process performance, it combines the Lean method of continuous improvement and the Six Sigma method of statistical analysis. The “Yellow Belt” certification, included, allows you to participate in Lean or Lean Six Sigma projects with a good understanding of the issues and methods at work.
Who is this training for ?
For whomAnyone wishing to participate in a Lean or Lean Six Sigma project.
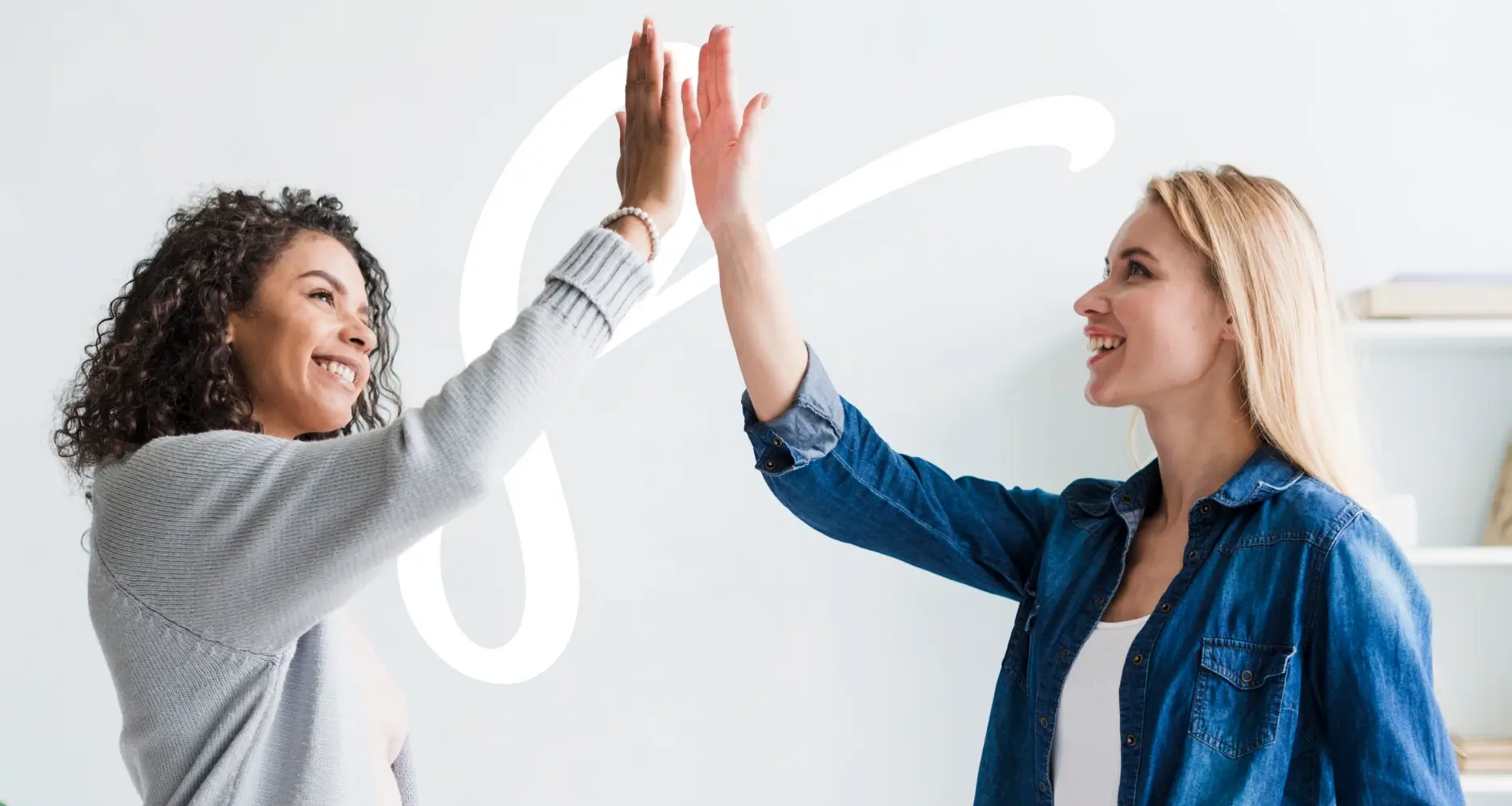
No special knowledge.
Training objectives
Clarify the meaning and challenges of Lean and Six Sigma methods.
Know the tools used: DMAIC, Kaizen, 5S, etc.
305Training program
Discover Lean and Six Sigma methods
- Six Sigma.
- Lean.
- The combination of the two methods.
- The 4 M.
- Waste.
- The DMAIC.
“Define” phase
- Voice of Customer, Critical Characteristics, SIPOC.
- Define the project.
“Measure” phase
- Flow diagram, cause and effect, Pareto.
- Definitions around measurement: variation, mean, median...
Phase "Analyser"
- Analysis of measurements, indicators.
- The Sigma of the process.
- Process capacity.
“Improve” phase
- Design of experiments method.
- Continuous improvement: tools.
- Error prevention.
- Generation and selection of solutions.
306“Check” phase
- Statistical control of the process.
- Monitoring plans.
- Monitoring indicators.
Exam
- Pass the Lean Six Sigma Yellow Belt IASSC certification:
- MCQ: 60 questions in French;
- Identifiers will be provided to each participant;
- duration: 2 hours with a PC connected to the Internet;
First aid training
★★★★★
- QST-85
- 2 Days ( Hours)
Description
First aid training combines theoretical sessions with practical exercises. Participants will have the opportunity to practice first aid techniques in realistic scenarios. Emergency simulations will allow participants to develop their confidence and their ability to respond quickly and effectively.
Who is this training for ?
For whomThis training is aimed at a broad audience, including healthcare professionals, corporate workers, teachers, parents and anyone interested in learning essential first aid skills.
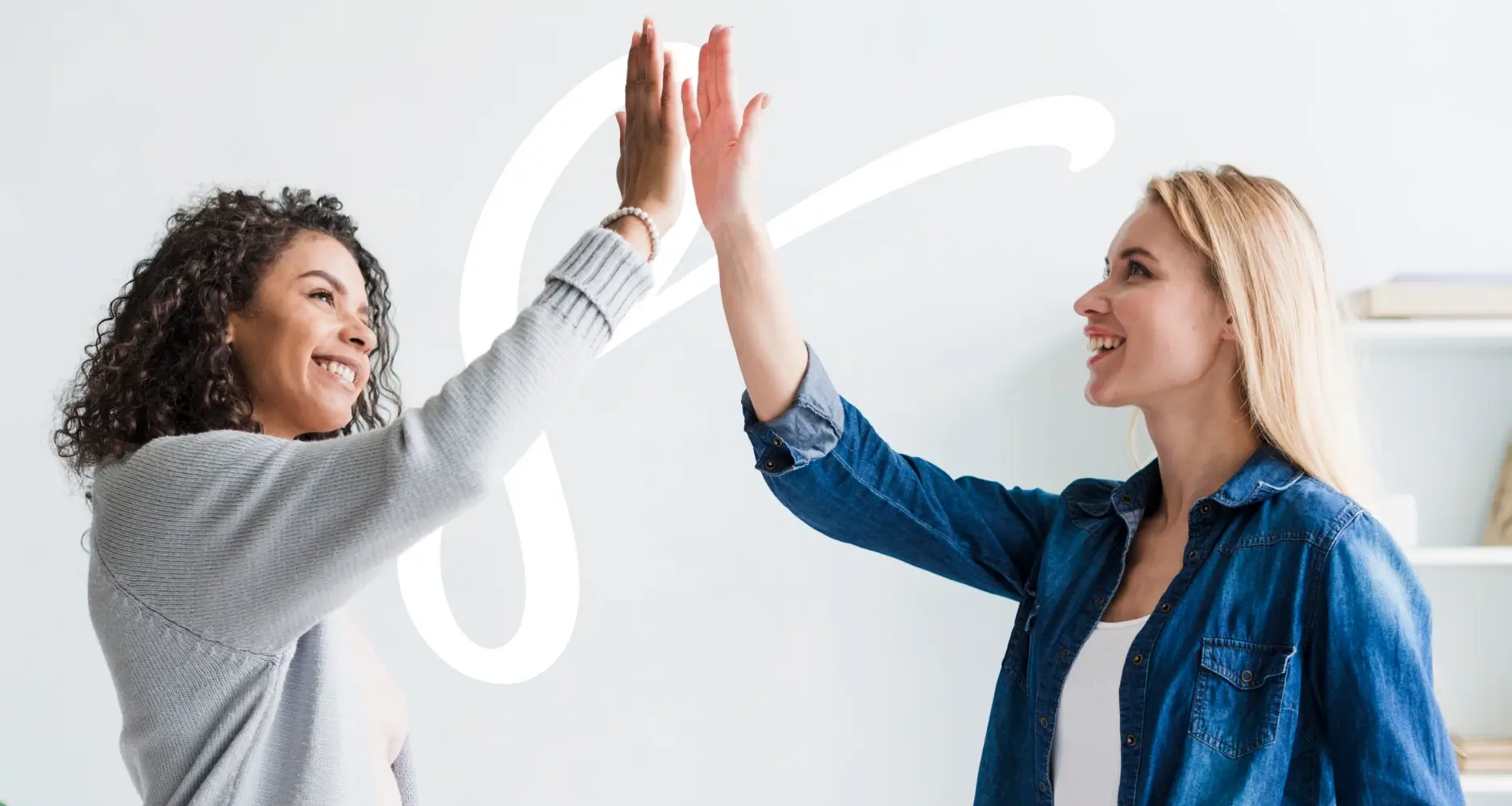
No specific prerequisites are necessary. The training is open to anyone wishing to acquire first aid and first aid skills.
Training objectives
Equip participants with the skills necessary to intervene effectively in an emergency situation.
0Capable of providing necessary first aid while ensuring the safety of the victim until medical professionals arrive.
★★★★★
- QST-85
- 2 Days (14 Hours)
Description
Who is this training for ?
For whom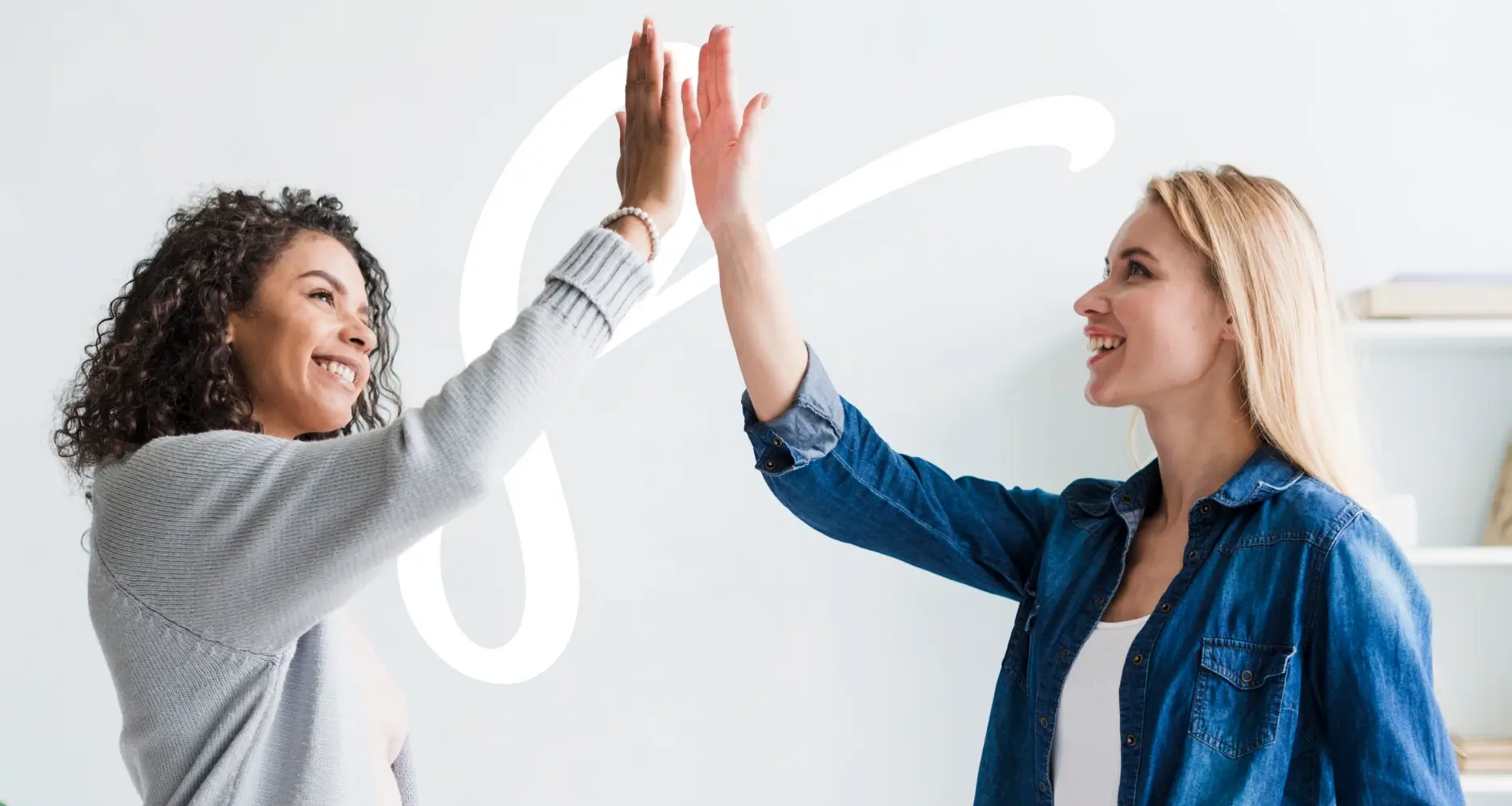
Training objectives
310311Training program
★★★★★
- QST-86
- 1 Days (7 Hours)
Description
Who is this training for ?
For whom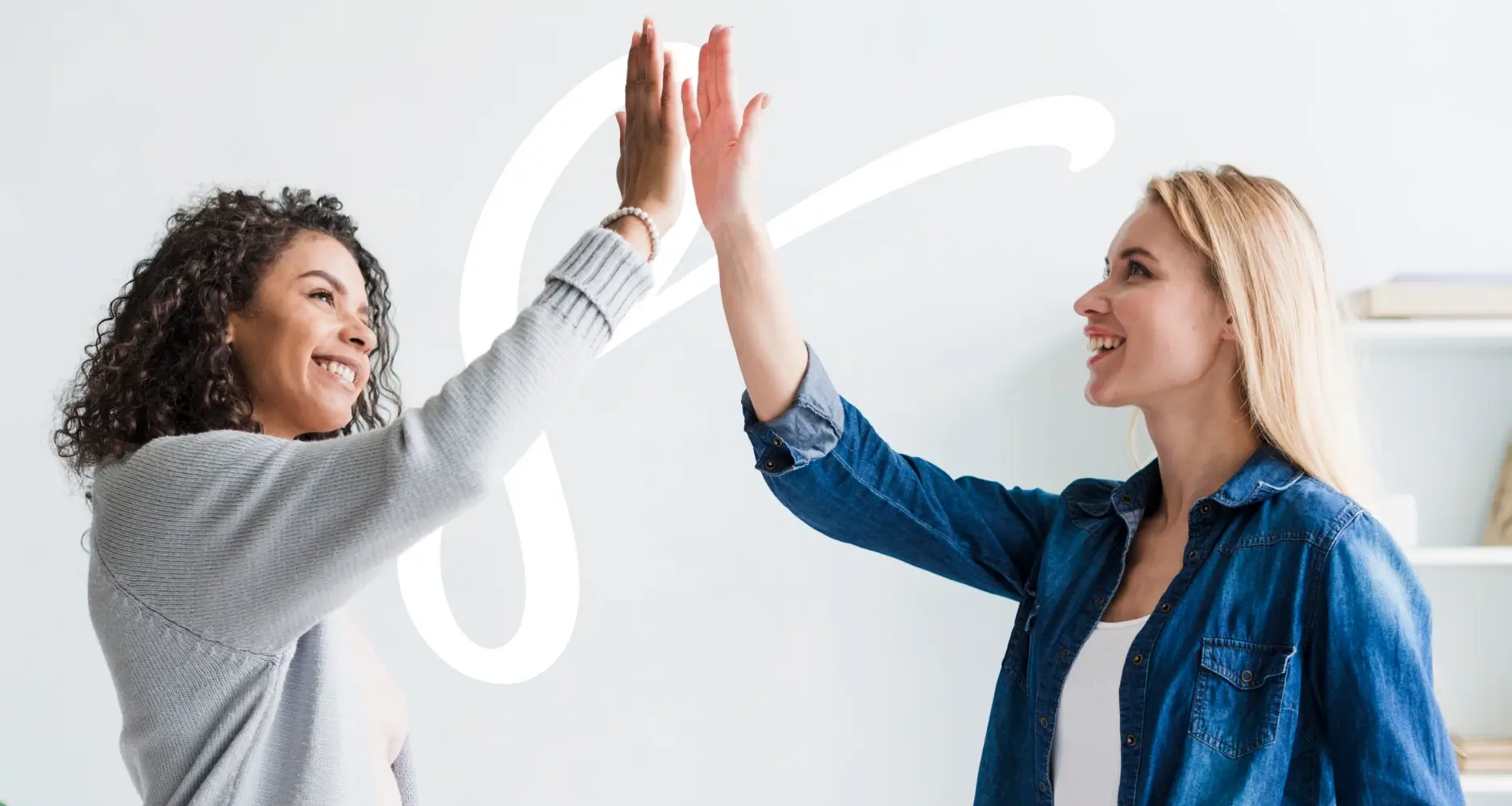
Training objectives
313314Training program
★★★★★
- QST-86
- 2 Days (14 Hours)
Description
Who is this training for ?
For whom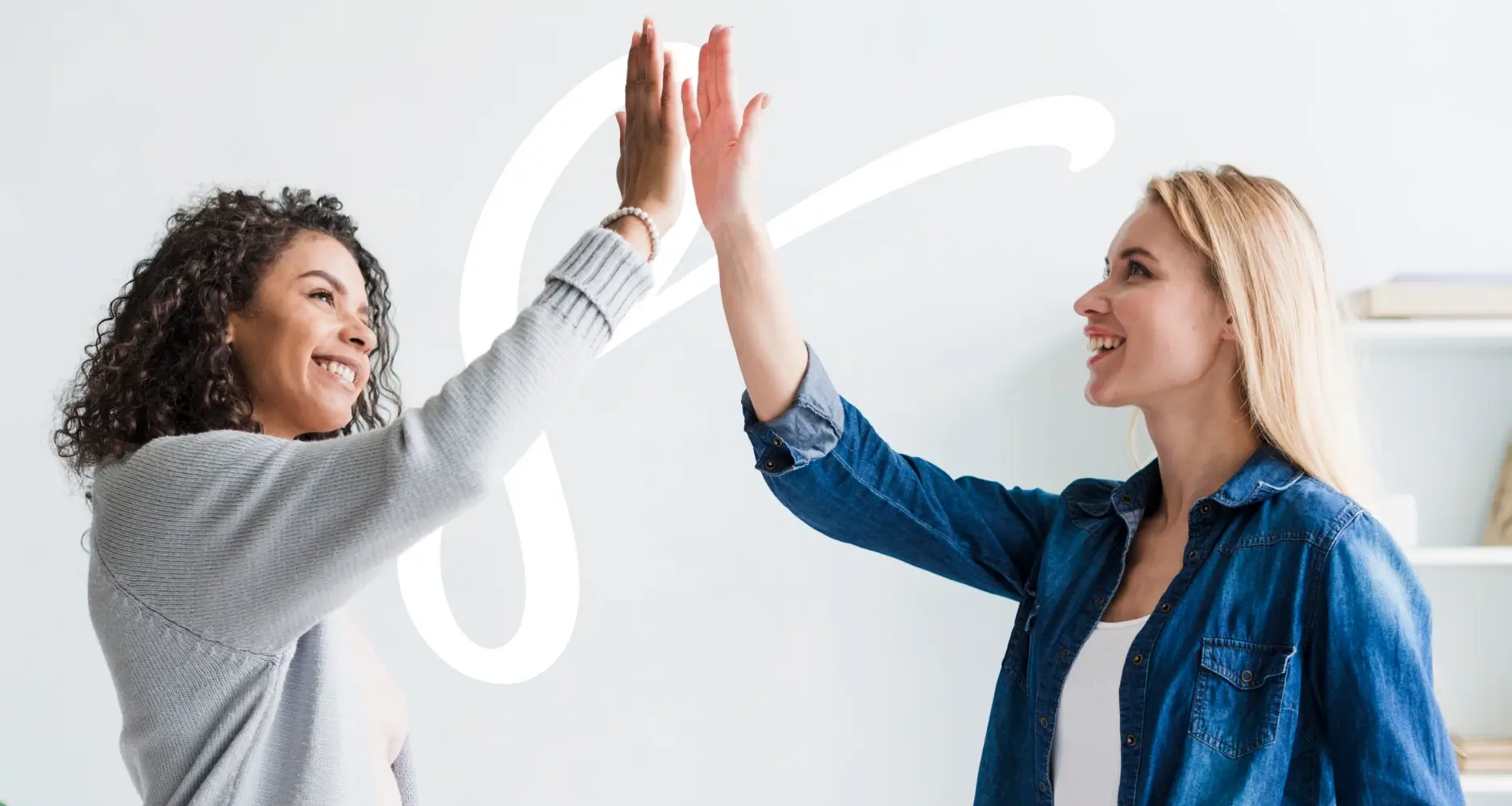
Training objectives
316317Training program
Safety and Risk Management
★★★★★
- QST-87
- 2 Days (14 Hours)
Description
This trainig provides a clear understanding of the fundamental principles of safety and risk management, tailored to the TMSA context. It enables participants to identify and analyze risks, master applicable standards, and develop effective prevention plans while promoting a safety culture.
Who is this training for ?
For whom- New Managers.
- HSE Officers.
- Team Leaders.
- Site Supervisors.
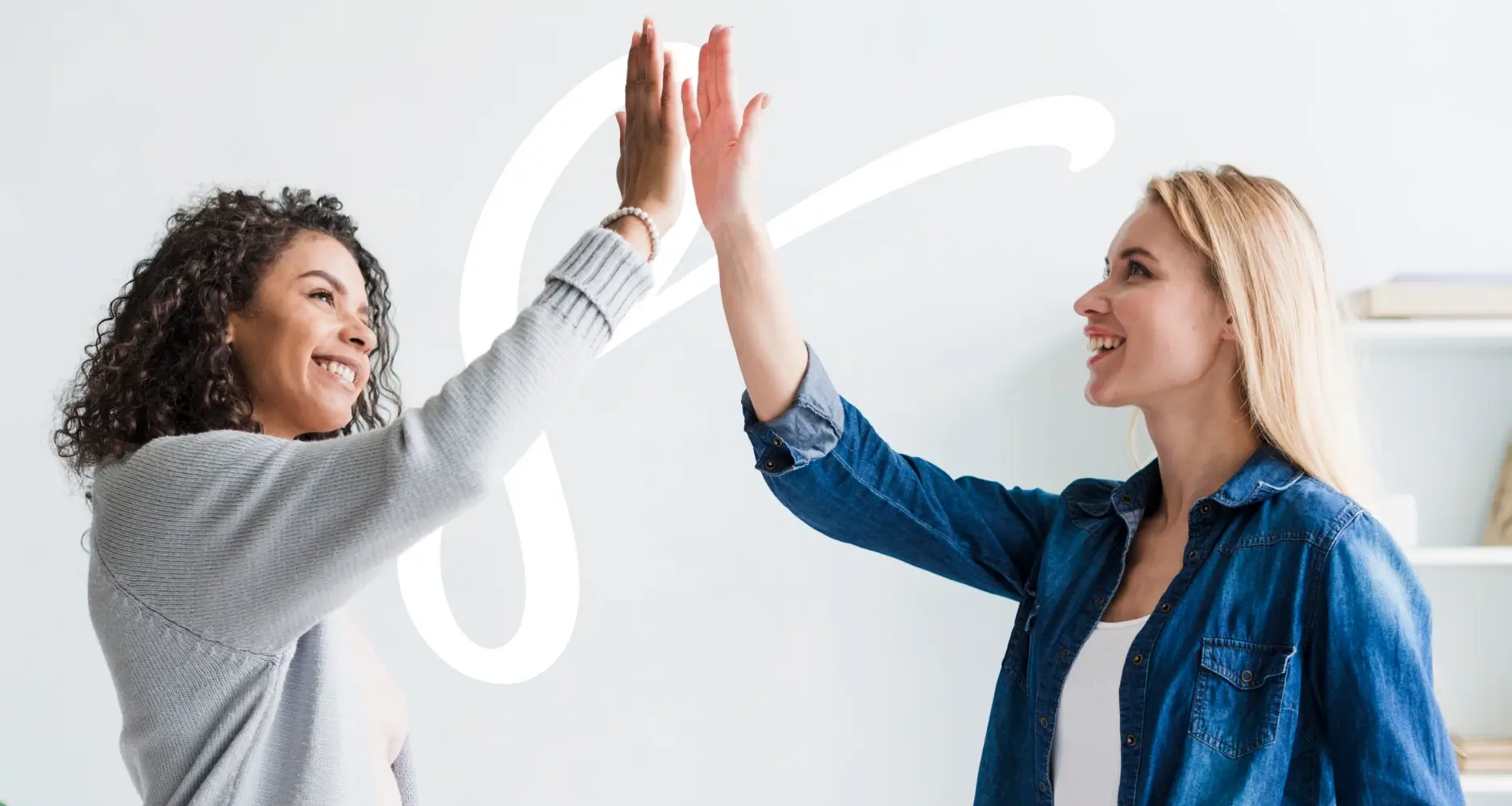
- Basic knowledge of business management or industrial/maritime operations. Interest in safety and risk management topics.
Training objectives
- Understand the basic principles of safety and risk management within the TMSA framework
- Identify and analyze risks using tools such as risk matrices and risk mapping
- Learn to develop and implement effective risk prevention and management plans
- Promote a strong safety culture and engage team members in risk management
320Training program
Fundamentals of Safety and Risk Management in Business
- Key definitions: hazard, risk, prevention, accident, incident.
- Risk management framework.
- The TMSA approach: requirements and recommendations for safety.
- Strategic importance of safety in business.
- Case studies: incidents caused by poor risk management.
Risk Identification, Assessment, and Mapping
- Types of risks (operational, human, environmental, etc.).
- Analysis methods: root cause analysis, FMEA, HAZOP.
- Use of risk matrices (likelihood / severity).
- Creating and interpreting risk maps.
- Practical case studies: identifying risks on a site or vessel.
Regulatory and Normative Framework
- Overview of key ISO standards (ISO 31000, ISO 45001).
- Local health and safety regulations.
- Maritime-specific standards (ISM Code, OCIMF, TMSA, SOLAS, MARPOL).
- Compliance and audit preparation for TMSA.
- Exercises: comparative analysis of standards.
Developing Risk Prevention and Mitigation Plans
- Methodology for developing prevention plans.
- Corrective and preventive actions: tools and indicators.
- Integrating risks into decision-making processes.
- Case study: drafting a prevention plan for a real scenario.
- Setting up safety performance KPIs.
Developing a Safety Culture and Leadership in Risk Management
- Risk behaviors and change management levers.
- Awareness, continuous training, and internal communication.
- Leadership, managerial commitment, and role modeling.
- Participatory methods: quality circles, safety suggestion boxes.
- Practical cases: launching a safety awareness campaign.
Simulation Workshops and Lessons Learned
- Incident simulations (leaks, fires, critical failures, etc.).
- Post-simulation analysis: what could have been done differently?.
- Role-playing and real-time crisis management.
- Feedback, knowledge sharing, and updating management plans.
Summary: transferring learnings to real environments.
Fire Prevention and Firefighting
★★★★★
- QST-88
- 2 Days (14 Hours)
Description
This training course on Fire Prevention and Firefighting aims to equip participants with the essential skills to effectively prevent and combat fires in the workplace. Through a comprehensive understanding of fire causes, types, and risks, as well as practical exercises on using safety equipment and managing evacuations, attendees will learn to ensure safety while complying with fire safety and hygiene standards.
Who is this training for ?
For whom- All employees.
- Security officers.
- HSE managers.
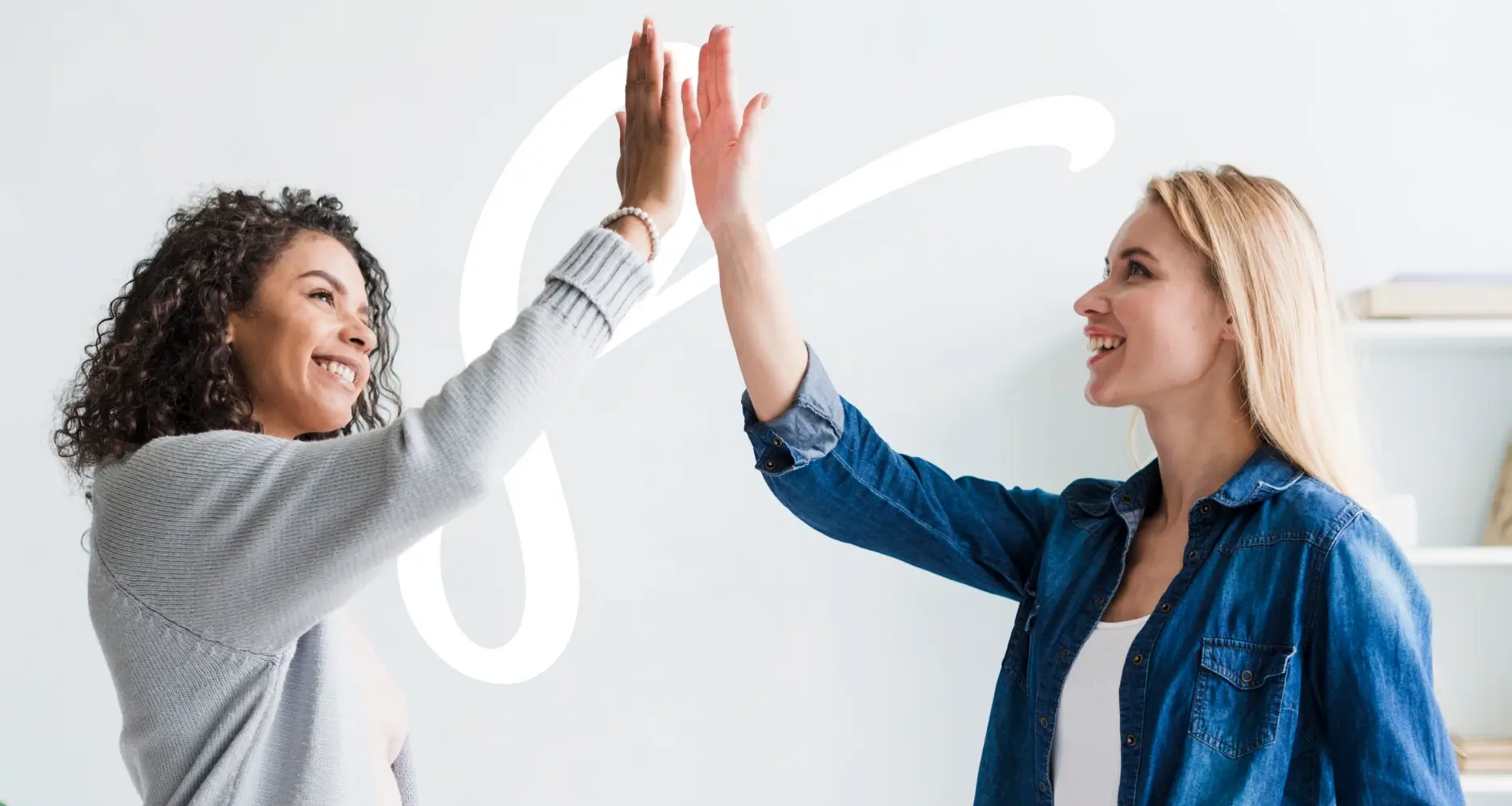
- Basic understanding of workplace safety principles.
- No prior firefighting experience required.
- Willingness to actively participate in practical exercises and drills.
Training objectives
- Understand the causes and risks of fires in the workplace
- Acquire practical skills to use firefighting equipment effectively
- Know how to organize and participate in a safe evacuation in case of fire
323Training program
Introduction to Fires
- Understand the nature of fire: necessary elements for ignition (fire triangle).
- Identify common causes of fires in the workplace (electrical equipment, flammable products, human error, etc.).
- Recognize different types of fires (Class A, B, C, D, and F) and their specificities.
- Analyze specific risks related to the industry sector and work environment (storage, ventilation, materials, etc.).
Fire Safety Standards and Workplace Responsibilities
- Overview of key fire safety regulations and standards (Labor Code, local regulations, HSE recommendations, etc.).
- Roles and responsibilities of employers in fire prevention (risk assessment, equipment implementation, employee training).
- Duties and expected behaviors of employees regarding fire risks.
- Importance of collaboration among all company stakeholders to ensure safety.
Effective Fire Prevention Practices
- Management and maintenance of electrical equipment to minimize risks (inspection, repair, proper use).
- Safe storage and handling of flammable and combustible products.
- Organizing the workspace to avoid potential fire hazards.
- Implementation of preventive procedures (cleaning, regular checks, no smoking policies, etc.).
Firefighting Equipment: Usage and Maintenance
- Overview of safety devices: fire extinguishers (types, classes), fire alarms, sprinklers, fire doors.
- How to choose and properly use a fire extinguisher according to the type of fire.
- Inspection, maintenance, and regular checks of firefighting equipment.
- Signage and access to equipment: best practices for quick intervention.
Fire Evacuation Management
- Organizing an evacuation plan: roles, routes, assembly points.
- Procedures to follow when a fire alarm sounds.
- Communication and coordination during evacuation.
- Awareness of safe behaviors (no use of elevators, assisting vulnerable people, etc.).
Practical Exercises and Simulations
- Fire simulation and practicing alert response.
- Hands-on use of fire extinguishers under supervision.
- Conducting a simulated evacuation to test responsiveness and adherence to the evacuation plan.
- Debriefing and feedback to identify areas for improvement.
QHSE / ISPS Standards
★★★★★
- QST-89
- 2 Days (14 Hours)
Description
This training program provides a comprehensive overview of QHSE (Quality, Health, Safety, Environment) and ISPS (International Ship and Port Facility Security) standards. It is designed to equip professionals with the knowledge and tools needed to ensure compliance with international requirements, manage operational risks, and implement effective safety and environmental systems. Through practical modules, participants will learn to apply legal standards, conduct internal audits, and continuously improve their organization’s performance.
Who is this training for ?
For whom- New managers.
- Department heads.
- Quality managers.
- QHSE coordinators.
- ISPS security officers.
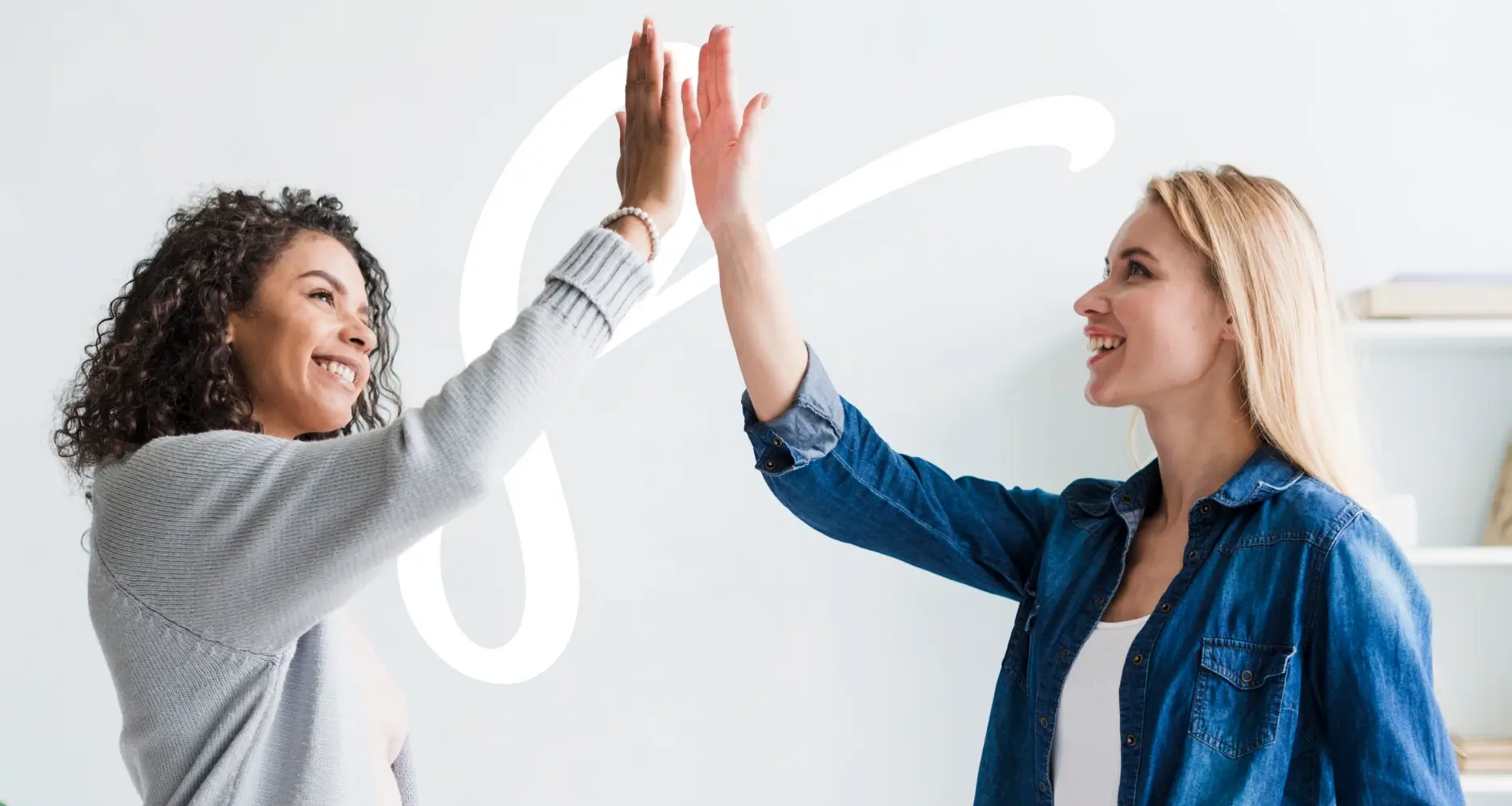
- Basic knowledge of operational or logistics processes.
- Prior exposure to safety, quality, or environmental management (recommended).
- Suitable for professionals in port operations, logistics, HSE roles, or international compliance.
Training objectives
- Understand the principles and legal requirements of QHSE and ISPS standards
- Develop and implement compliance procedures and performance monitoring systems
- Conduct internal audits and apply corrective actions for continuous improvement
326Training program
Fundamentals of QHSE and ISPS Standards
- Definition and objectives of QHSE (Quality, Health, Safety, Environment).
- Introduction to the ISPS Code (International Ship and Port Facility Security).
- Importance for international operations and global supply chain.
- Role of QHSE culture in organizational performance.
Legal and Regulatory Requirements
- International frameworks: IMO, ISO, OHSAS, ISO 45001, ISO 14001.
- National vs. international legal obligations.
- Impact of non-compliance: legal, financial, reputational risks.
- Integrating legal requirements into management systems.
Implementing an Effective QHSE System
- Developing QHSE policies and procedures.
- Defining responsibilities and organizational roles.
- Document control and internal communication.
- Monitoring QHSE performance indicators (KPIs).
Port Security and ISPS Compliance
- Identifying port facility risks and vulnerabilities.
- Security zones and access control measures.
- Port Facility Security Assessment (PFSA).
- Port Facility Security Plan (PFSP) and emergency protocols.
Internal Audits and Non-Conformity Management
- Audit methodology for QHSE and ISPS.
- Tools for identifying gaps (checklists, interviews, observations).
- Audit reporting and result communication.
- Implementing corrective and preventive actions.
Continuous Improvement and Feedback
- Action plan follow-up and management reviews.
- Incident reporting and lessons learned (feedback system).
- PDCA cycle (Plan – Do – Check – Act) in QHSE and ISPS.
- Ongoing awareness and training programs.
★★★★★
- QST-90
- 2 Days (14 Hours)
Description
This training provides a comprehensive overview of IMO standards essential for maritime professionals. Participants will learn the history, objectives, and key regulations such as ISO 9001, ISM Code, SOLAS, and MARPOL. The course covers compliance requirements, integration of standards into quality management systems, practical case studies, and internal audit techniques. By the end, attendees will be equipped to ensure their organization meets IMO regulations effectively and continuously adapts to regulatory changes.
Who is this training for ?
For whom- QHSE Managers.
- Maritime Sector Managers and Technicians.
- Internal Auditors.
- Fleet or Maritime Operations Managers.
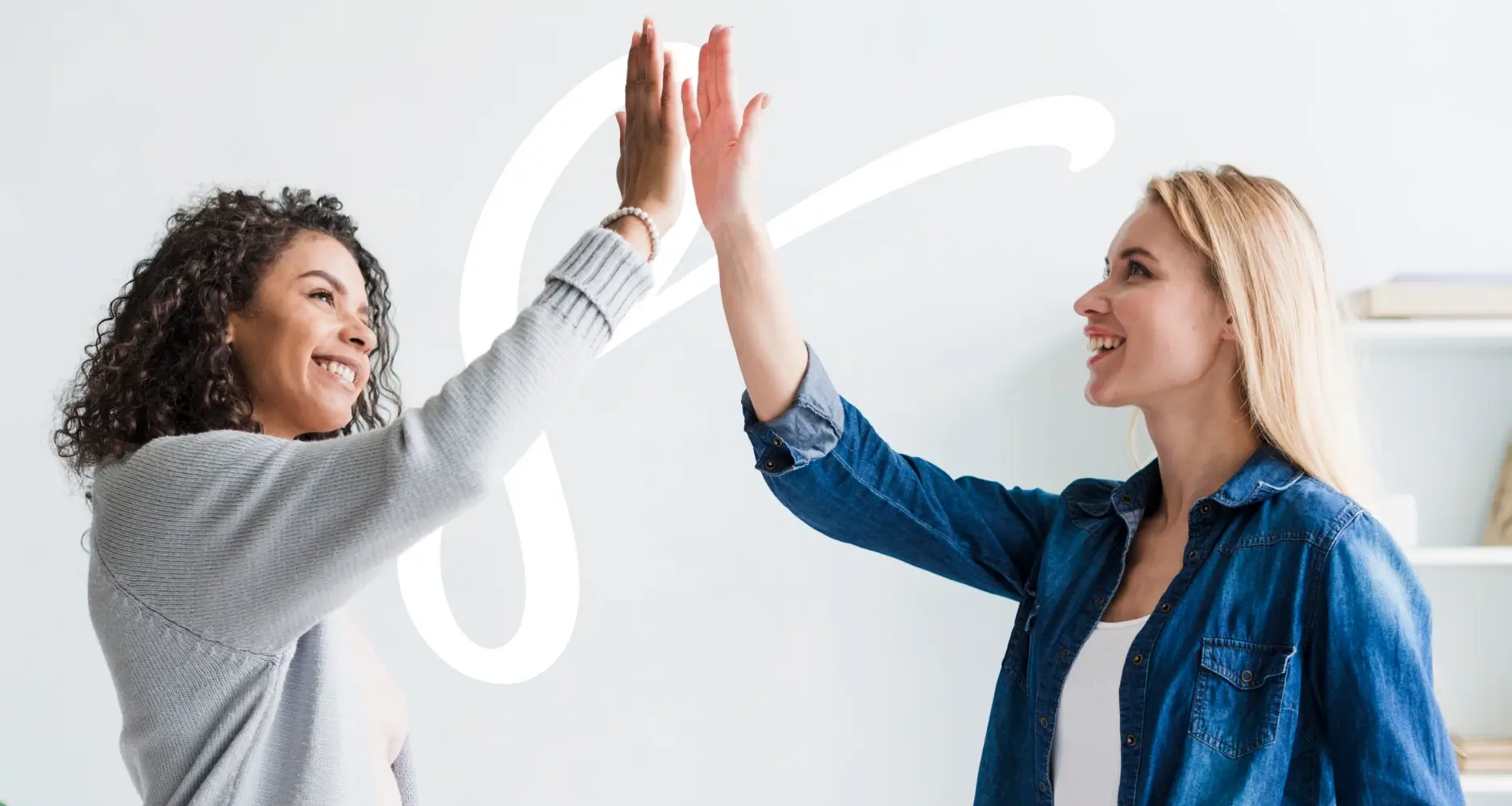
- Basic knowledge of maritime operations or maritime industry environment.
- Familiarity with general management or quality management principles is an advantage.
- Interest in regulatory compliance and safety management.
- No advanced technical expertise is required; suitable for beginners and intermediate professionals.
Training objectives
- Understand the role and requirements of IMO standards
- Identify the main maritime regulations
- Integrate IMO standards into a management system
- Master auditing and compliance practices
- Prepare for regulatory changes and updates
329Training program
Introduction to IMO Standards
- History of the International Maritime Organization (IMO): creation, mission, and global role.
- Objectives of IMO standards: maritime safety, environmental protection, and operational quality.
- Evolution of standards adapting to modern challenges (technology, environment, safety).
- Impact of IMO standards on the global maritime sector.
Overview of Key IMO Standards
- ISO 9001: Quality management principles applicable to maritime operations.
- ISM Code (International Safety Management): safety management requirements onboard and ashore.
- SOLAS (Safety of Life at Sea): rules for ship and passenger safety.
- MARPOL (Marine Pollution): conventions to prevent marine pollution from ships.
- Other relevant complementary standards as needed.
Compliance Requirements and Processes
- Detailed requirements of each standard covered.
- Identification of necessary documents, procedures, and controls.
- Defining roles and responsibilities within the organization.
- Control processes, reporting, and managing non-conformities.
Integrating IMO Standards into the Company
- Methodology for integration into existing management systems (e.g., ISO 9001).
- Adapting operational procedures to meet IMO standards.
- Raising awareness and training staff.
- Change management and maintaining daily compliance.
Practical Case Studies
- Presentation of real successful implementation cases.
- Analysis of challenges encountered and solutions applied.
- Discussion on economic, human, and environmental impacts.
- Group exercise: developing an action plan.
Internal Audits and Monitoring Standards
- Introduction to internal audits: purpose, methods, and tools.
- Preparing and conducting IMO compliance audits.
- Analyzing results and implementing improvement plans.
- Continuous monitoring of IMO standards updates.
- Strategic adaptation of the company according to regulatory changes.
Risk Analysis – FMEA Method
★★★★★
- QST-91
- 2 Days (14 Hours)
Description
This training introduces you to the FMEA method (Failure Modes and Effects Analysis), a powerful tool to identify, evaluate, and manage risks in industrial, quality, or safety processes. Through a practical and structured approach, you will learn how to detect potential failure modes, analyze their impacts, calculate their criticality, and plan effective corrective actions. This method will help improve the reliability, safety, and overall performance of your systems.
Who is this training for ?
For whom- Quality, safety, maintenance, and production managers.
- Engineers and technicians in industry, services, or risk management.
- Project managers aiming to integrate proactive risk management.
- Anyone involved in risk analysis, prevention, and control within their organization.
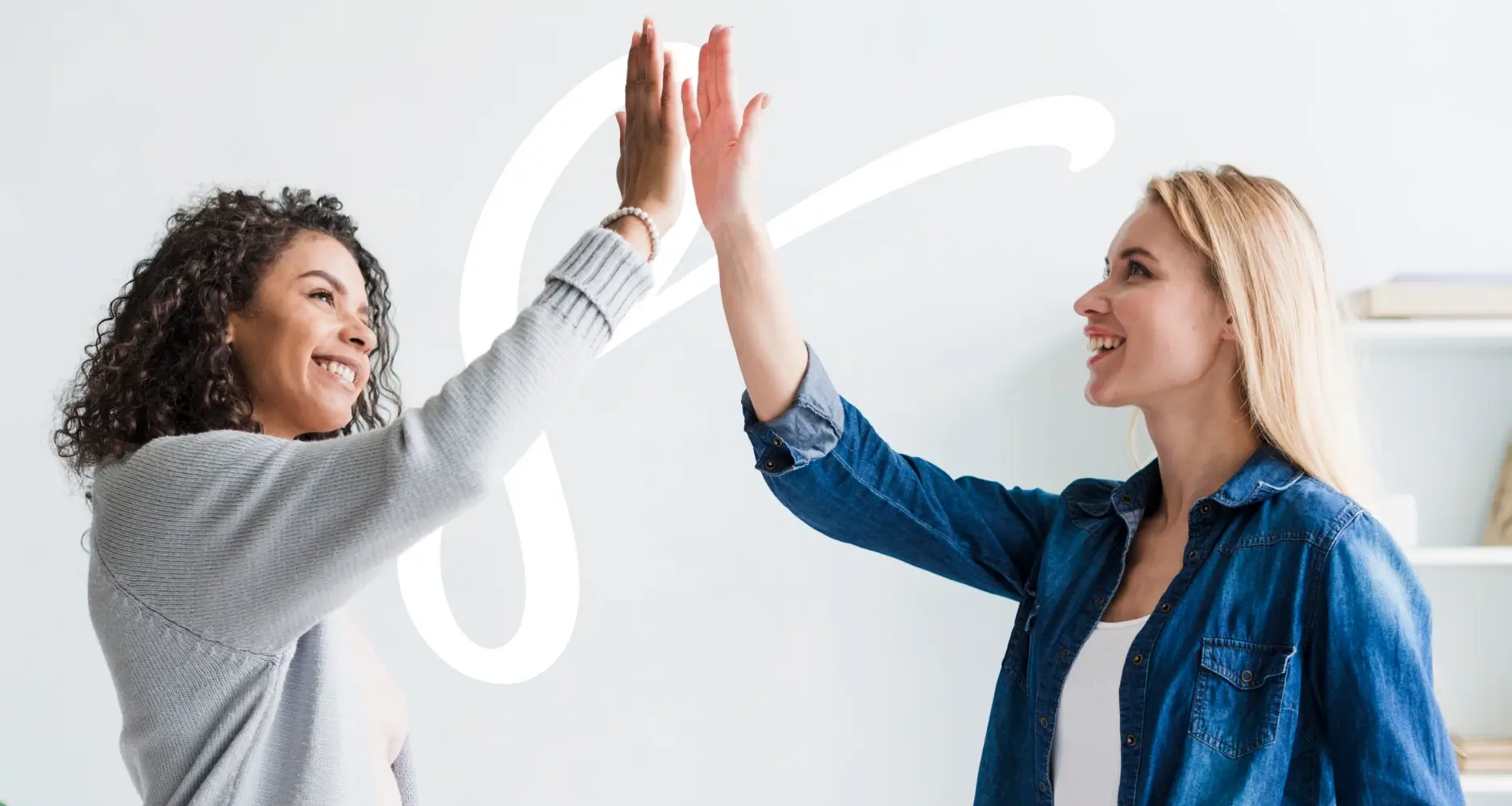
- Basic knowledge of risk management or quality management.
- Elementary understanding of industrial processes or systems to be analyzed.
- Practical experience in a technical or operational environment is a plus but not mandatory.
Training objectives
- Understand the fundamental principles and importance of the FMEA method in risk management
- Learn how to identify and classify potential failure modes within a process or system
- Master the calculation of risk criticality by assessing severity, occurrence, and detectability
- Develop and plan effective corrective and preventive actions to mitigate identified risks
332Training program
Introduction to the FMEA Method
- History and context of FMEA (Failure Modes and Effects Analysis).
- Key concepts: failure mode, effect, cause, criticality.
- Application areas (industry, quality, safety, maintenance).
- Advantages and limitations of the method.
- Overview of a typical FMEA study process
Identification of Failure Modes
- Identification techniques: brainstorming, documentation review, feedback, audits.
- Categorizing failure modes (mechanical, human, software-related, etc.).
- Practical examples and case studies
- Complementary tools (cause trees, diagrams).
- Documenting and formalizing failure modes in the FMEA worksheet.
Analysis of the Effects of Failures
- Defining direct and indirect effects of failures.
- Impact on production (downtime, performance loss).
- Consequences on product/service quality.
- Impact on safety and environment.
- Real-life examples and major effects analysis.
Calculating and Evaluating Criticality
- Explanation of the indices: Severity (S), Occurrence (O), Detection (D).
- Criticality score calculation (RPN = S × O × D).
- Scoring scales and classification criteria.
- Result analysis and identification of high-priority risks.
- Practical exercises on calculation and interpretation.
Planning Corrective and Preventive Actions
- Types of actions: corrective, preventive, continuous improvement.
- Prioritizing actions based on risk level.
- Monitoring and evaluating implemented measures.
- Importance of documentation and communication.
- Case study: creating an action plan based on an FMEA analysis.